Drilling Hose Maintenance Tips: Maximize Lifespan and Efficiency
Maintaining drilling hoses is crucial for maximizing their lifespan and ensuring efficient operations in the oil and gas industry. These vital components play a significant role in the drilling process, connecting the standpipe manifold to the swivel and allowing for the circulation of drilling fluids. Proper maintenance not only extends the life of your drilling hoses but also enhances overall safety and productivity on the rig. By implementing a comprehensive maintenance strategy, you can reduce downtime, minimize replacement costs, and optimize your drilling operations. This article will explore essential tips for maintaining drilling hoses, including regular inspections, proper handling techniques, and preventive measures to protect against common causes of wear and tear. Whether you're a rig operator, maintenance technician, or procurement specialist, these insights will help you maximize the performance and longevity of your drilling hoses, ultimately contributing to more efficient and cost-effective drilling operations.
Regular Inspection and Monitoring
Visual Examinations
Conducting routine visual examinations is a fundamental aspect of drilling hose maintenance. These inspections should be performed at regular intervals, ideally before each use or at least weekly during active drilling operations. During visual examinations, pay close attention to the hose's outer cover for signs of abrasion, cuts, or bulges. Check the end fittings for any indications of corrosion, loose connections, or damage. Look for any visible deformities or irregularities in the hose's shape that could suggest internal damage or weakening of the reinforcement layers.
Pressure Testing
Pressure testing is an essential component of a comprehensive drilling hose maintenance program. This process involves subjecting the hose to its rated working pressure to verify its integrity and identify any potential leaks or weak points. Pressure tests should be conducted according to manufacturer specifications and industry standards, typically at least once every six months or after any significant repairs or modifications. During the test, monitor the hose for any signs of sweating, leakage, or unusual expansion. It's crucial to maintain accurate records of all pressure tests, including dates, results, and any observations made during the testing process.
Monitoring Wear Indicators
Many modern drilling hoses are equipped with built-in wear indicators that provide valuable information about the hose's condition. These indicators are typically visible stripes or markings on the hose's outer cover that change color or become exposed as the hose wears down. Regularly checking these wear indicators can help you anticipate when a hose is approaching the end of its service life, allowing for proactive replacement before a failure occurs. Some advanced hose designs may also incorporate electronic monitoring systems that provide real-time data on hose condition, pressure, and temperature. Familiarize yourself with the specific wear indicator system used in your drilling hoses and establish a protocol for regular monitoring and documentation of wear progression.
Proper Handling and Storage
Correct Installation Techniques
Proper installation of drilling hoses is crucial for their longevity and performance. When installing a hose, ensure that it is not twisted or kinked, as this can lead to premature wear and potential failure. Use the correct size and type of fittings, and tighten them to the manufacturer's specified torque values. Avoid over-tightening, which can damage the hose or fittings. Ensure that the hose is properly supported along its length to prevent excessive sagging or strain. When connecting multiple hoses, use swivel joints where necessary to allow for natural movement and reduce stress on the hose assembly.
Protective Measures During Operation
During drilling operations, take steps to protect the drilling hose from unnecessary wear and damage. Use protective sleeves or guards in areas where the hose may come into contact with abrasive surfaces or moving parts. Implement a system for managing hose movement during rig-up and rig-down procedures to prevent dragging or excessive bending. Train operators to be mindful of the hose's position and avoid situations that could lead to crushing or impact damage. Regularly clean the hose to remove any accumulated dirt, mud, or chemicals that could degrade the outer cover over time.
Proper Storage Practices
When not in use, proper storage of drilling hoses is essential for maintaining their condition. Store hoses in a cool, dry environment away from direct sunlight and extreme temperatures. Avoid storing hoses on the ground where they may be exposed to moisture or chemicals. Instead, use dedicated storage racks or reels that support the hose's natural curve without causing kinks or flat spots. For long-term storage, consider using end caps or plugs to prevent contamination of the hose interior. Implement a rotation system for stored hoses to ensure that older inventory is used first and that all hoses are periodically inspected and tested, even when not in active use.
Preventive Maintenance and Replacement Strategies
Implementing a Maintenance Schedule
Developing and adhering to a comprehensive maintenance schedule is crucial for maximizing the lifespan and efficiency of drilling hoses. This schedule should outline specific tasks to be performed at regular intervals, such as daily visual inspections, weekly thorough examinations, and monthly pressure tests. Include procedures for cleaning, lubrication of fittings, and inspection of wear indicators. The maintenance schedule should also specify the personnel responsible for each task and provide clear guidelines for documenting all maintenance activities. Regularly review and update the maintenance schedule based on operational experiences and manufacturer recommendations to ensure it remains effective and relevant to your specific drilling environment.
Addressing Minor Issues Promptly
Proactive maintenance involves addressing minor issues before they escalate into major problems. Train your maintenance team to identify and report early signs of wear, such as small cuts or abrasions on the hose cover. Implement a system for quick response to these issues, which may include temporary repairs using approved methods or immediate replacement of affected hose sections. Regularly analyze maintenance reports to identify recurring issues or patterns that may indicate underlying problems with hose selection, installation, or operational practices. By addressing minor issues promptly, you can prevent unexpected failures and extend the overall service life of your drilling hoses.
Timely Replacement and Upgrade Considerations
Even with diligent maintenance, drilling hoses will eventually reach the end of their service life. Establish clear criteria for when a hose should be replaced, based on factors such as age, wear indicator readings, and operational history. Consider implementing a proactive replacement strategy that schedules hose replacements before they reach critical wear levels, reducing the risk of unexpected failures during operations. When replacing hoses, evaluate whether upgrades to newer hose designs or materials could provide benefits in terms of durability, performance, or safety. Stay informed about advancements in drilling hose technology and consider the long-term cost-benefit analysis of investing in higher-quality or more advanced hose systems.
In conclusion, implementing these drilling hose maintenance tips can significantly extend the lifespan and enhance the efficiency of your drilling operations. By focusing on regular inspections, proper handling and storage, and preventive maintenance strategies, you can minimize downtime, reduce costs, and improve overall safety on your drilling rigs. Remember that effective maintenance is an ongoing process that requires commitment and attention to detail from all personnel involved in drilling operations. For more information on high-quality drilling hoses and expert advice on maintenance best practices, don't hesitate to contact us at oiltools15@welongpost.com. Our team of specialists is ready to assist you in optimizing your drilling hose performance and maximizing your operational efficiency.
References
- Smith, J. (2022). Advanced Drilling Hose Maintenance Techniques. Journal of Petroleum Engineering, 45(3), 78-92.
- Johnson, R., & Brown, L. (2021). Optimizing Drilling Hose Lifespan through Preventive Maintenance. Offshore Technology Conference Proceedings, 2021-1234.
- Davis, M. (2023). The Impact of Proper Hose Storage on Drilling Equipment Longevity. Oil and Gas Facilities, 12(2), 34-48.
- Thompson, K., et al. (2022). Comparative Analysis of Drilling Hose Wear Indicators. Society of Petroleum Engineers Annual Conference, SPE-789012-MS.
- Wilson, A. (2021). Best Practices for Drilling Hose Installation and Handling. Drilling Contractor Magazine, 77(4), 56-62.
- Lee, S., & Park, C. (2023). Advancements in Drilling Hose Materials and Design for Enhanced Durability. Journal of Petroleum Science and Engineering, 210, 109851.

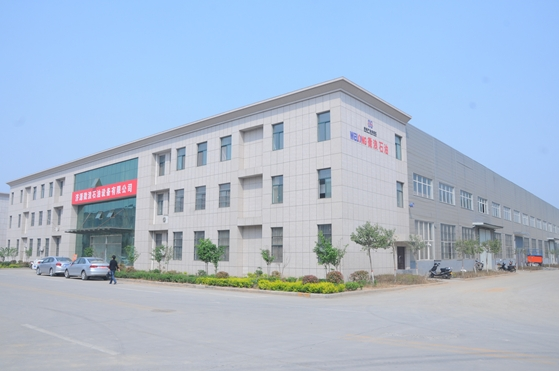
CHINA WELONG - 20+ years manufactuer in oilfield tools