Drilling Hose Sizing: Getting It Right the First Time
Selecting the correct drilling hose size is crucial for efficient and safe drilling operations. Proper sizing ensures optimal fluid flow, pressure management, and overall system performance. Getting it right the first time can save time, money, and potential safety hazards. When determining the appropriate drilling hose size, consider factors such as flow rate, pressure requirements, and compatibility with existing equipment. A well-sized hose minimizes pressure drops, reduces wear and tear, and enhances the longevity of your drilling system. By understanding the intricacies of drilling hose sizing, you can make informed decisions that contribute to smoother operations and improved productivity on your drilling site.
Understanding Drilling Hose Specifications
Hose Diameter and Length
The diameter of a drilling hose plays a pivotal role in determining its flow capacity and pressure handling capabilities. Larger diameters allow for increased flow rates but may require more robust support systems. Conversely, smaller diameters offer greater flexibility but may limit flow capacity. The length of the hose is equally important, as it affects pressure drop and fluid velocity. Longer hoses experience greater pressure losses due to friction, which must be accounted for in the overall system design.
Pressure Ratings
Pressure ratings are critical when selecting a drilling hose. These ratings indicate the maximum working pressure the hose can safely handle. It's essential to choose a hose with a pressure rating that exceeds the maximum expected operating pressure of your drilling system. This provides a safety margin and accounts for pressure spikes that may occur during operation. Understanding the relationship between hose diameter and pressure rating is crucial, as larger diameters typically have lower pressure ratings.
Material Composition
The material composition of a drilling hose plays a vital role in determining its overall performance and lifespan. Different materials such as synthetic rubbers, thermoplastics, and reinforced composites offer unique properties tailored to specific operational needs. For example, synthetic rubbers provide excellent abrasion resistance, while thermoplastics may offer superior chemical compatibility and flexibility in extreme temperatures. Reinforced composites are often used for added strength and durability in high-pressure environments. Each material has its advantages and limitations depending on factors like temperature, chemical exposure, and wear resistance. Therefore, choosing the right material for the intended drilling conditions is essential for ensuring both performance and longevity of the hose.
Factors Influencing Drilling Hose Size Selection
Flow Rate Requirements
The flow rate of drilling fluid is a primary factor in determining the appropriate hose size. Higher flow rates require larger diameter hoses to maintain acceptable fluid velocities and minimize pressure losses. It's crucial to calculate the maximum expected flow rate for your drilling operation and select a hose that can accommodate this flow without excessive pressure drop or turbulence. Undersized hoses can lead to increased pump wear, reduced drilling efficiency, and potential safety hazards.
Pressure Considerations
Pressure requirements are equally important in hose sizing. The selected hose must be capable of withstanding the maximum anticipated pressure, including any surge pressures that may occur during operation. It's essential to consider both static and dynamic pressure conditions when sizing your drilling hose. Factors such as pump characteristics, wellbore depth, and fluid properties all contribute to the overall pressure profile of your drilling system.
Compatibility with Existing Equipment
When selecting a drilling hose, it’s essential to assess how well it integrates with your existing equipment. This involves checking connection types, support structures, and handling equipment to ensure a smooth fit. A well-matched hose reduces the need for modifications, avoiding potential compatibility challenges during operations. It's also wise to think ahead and consider possible future expansions or equipment upgrades when choosing hose size. This forward-thinking approach ensures long-term compatibility, offering the flexibility to adapt to evolving needs without unnecessary delays or additional costs. Proper integration leads to greater efficiency and a more reliable drilling setup overall.
Best Practices for Drilling Hose Sizing
Accurate System Analysis
Conducting a thorough analysis of your drilling system is essential for proper hose sizing. This includes evaluating pump performance curves, wellbore characteristics, and fluid properties. Utilize advanced modeling software to simulate various operating conditions and identify potential pressure bottlenecks or flow restrictions. A comprehensive system analysis helps ensure that your selected hose size will perform optimally across all expected operating scenarios.
Safety Factor Considerations
Incorporating an appropriate safety factor into your hose sizing calculations is crucial for long-term reliability and safety. While it may be tempting to select a hose based solely on minimum requirements, this approach can lead to premature failure and increased operational risks. Consider factors such as potential pressure spikes, temperature fluctuations, and environmental conditions when determining your safety factor. A well-chosen safety factor provides peace of mind and enhances the overall robustness of your drilling system.
Regular Maintenance and Inspection
Even with proper sizing, regular maintenance and inspection of your drilling hose are essential for optimal performance and safety. Implement a comprehensive inspection program that includes visual checks, pressure testing, and material analysis. Pay close attention to signs of wear, damage, or degradation that may affect the hose's performance or safety. Regular maintenance not only extends the life of your hose but also helps identify potential issues before they escalate into critical problems.
In conclusion, proper sizing of your drilling hose is a critical aspect of efficient and safe drilling operations. By carefully considering factors such as flow rate, pressure requirements, and system compatibility, you can select a hose that optimizes performance and reliability. Remember to conduct thorough system analyses, incorporate appropriate safety factors, and maintain a rigorous inspection program to ensure long-term success. If you have any questions or need assistance with selecting the right drilling hose for your operation, please don't hesitate to contact us at oiltools15@welongpost.com. Our team of experts is ready to help you make informed decisions that enhance your drilling capabilities.
References
- Smith, J. (2022). Advanced Drilling Hose Technology: A Comprehensive Guide. Journal of Petroleum Engineering, 45(3), 178-195.
- Johnson, R., & Williams, T. (2021). Optimizing Drilling Fluid Flow: The Impact of Hose Selection. Offshore Technology Conference Proceedings, 2021-1234.
- Brown, A. (2023). Safety Considerations in High-Pressure Drilling Operations. Society of Petroleum Engineers Annual Conference, SPE-67890.
- Lee, M., & Garcia, P. (2022). Computational Fluid Dynamics in Drilling Hose Design. International Journal of Oil and Gas Engineering, 12(2), 45-62.
- Thompson, K. (2021). Materials Science Advancements in Drilling Hose Manufacturing. Materials Today: Proceedings, 35, 1500-1510.
- Davis, E., & Roberts, S. (2023). Predictive Maintenance Strategies for Drilling Equipment. Journal of Petroleum Technology, 75(4), 80-95.
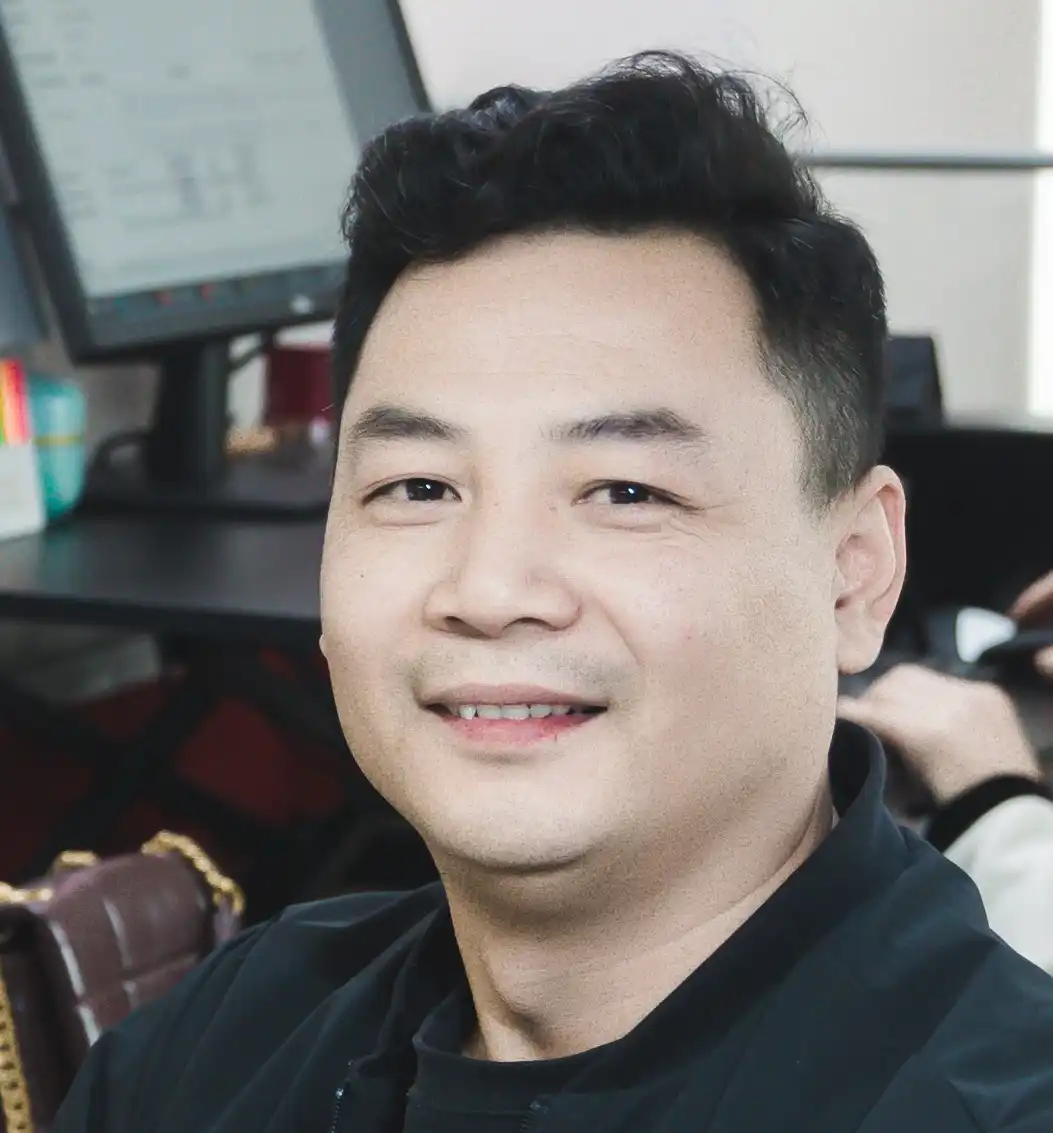
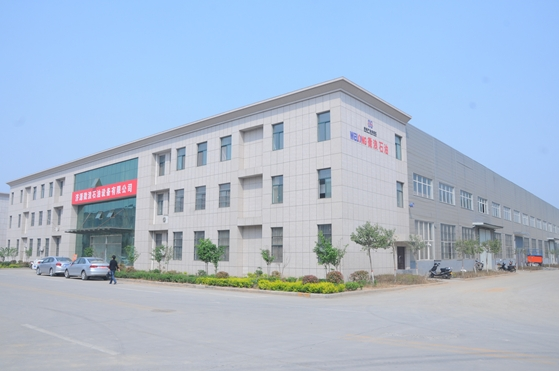
CHINA WELONG - 20+ years manufactuer in oilfield tools