Drilling Jar FAQs: Answers for Engineers and Procurement Professionals
Drilling jars are essential tools in the oil and gas industry, playing a crucial role in freeing stuck drill strings and enhancing overall drilling efficiency. As engineers and procurement professionals, understanding the intricacies of drilling jars is vital for making informed decisions and optimizing drilling operations. This comprehensive FAQ guide addresses common questions about drilling jars, their types, applications, and key considerations for selection and maintenance. Whether you're a seasoned engineer or a procurement specialist, this article will provide valuable insights to help you navigate the complex world of drilling jar technology and make well-informed choices for your projects.
How Do Drilling Jars Improve Efficiency and Safety in Drilling Operations?
Drilling jars are essential tools in the oil and gas industry, designed to improve both the efficiency and safety of drilling operations. These tools are used to deliver a sudden impact force, usually when the drill string becomes stuck due to tight formations or other obstacles. The ability to apply this force helps in freeing the drill bit, ensuring a smoother operation with minimal downtime.
One of the primary ways drilling jars enhance efficiency is by reducing the need for more time-consuming methods, such as pulling the entire drill string out of the hole. When a sticking event occurs, the jar's impact force can break the adhesion, allowing the drilling process to continue without the need for significant adjustments. This means that drilling teams can maintain momentum and complete their projects on schedule.
In terms of safety, drilling jars prevent excessive strain on the drilling equipment and reduce the risk of damage to the wellbore. Without this tool, the equipment could experience high-stress levels, which may lead to failure or accidents. By applying controlled force, drilling jars also help prevent further complications, ensuring that both personnel and equipment remain safe during operations.
In conclusion, drilling jars play a crucial role in enhancing the overall productivity and safety of drilling operations. By improving the ability to respond quickly to stuck pipe situations, they help reduce delays, lower operational costs, and minimize the risk of accidents, making them an invaluable asset in the drilling industry.
Key Factors in Drilling Jar Selection and Procurement
Well Depth and Conditions
When selecting a drilling jar, one of the primary considerations is the well depth and anticipated drilling conditions. Different jar types perform optimally at various depths and in specific environments. For instance, mechanical jars are often preferred for shallower wells, while hydraulic or hydro-mechanical jars may be more suitable for deeper operations. Additionally, factors such as formation characteristics, wellbore geometry, and expected fluid properties should influence the jar selection process to ensure optimal performance and reliability throughout the drilling campaign.
Jarring Force Requirements
The required jarring force is a critical factor in choosing the right drilling jar. This force depends on various factors, including the weight of the drill string, the nature of the stuck point, and the overall well conditions. Procurement professionals should work closely with engineering teams to determine the specific force requirements for each project. It's essential to select a jar that can deliver sufficient impact to free stuck equipment without risking damage to the drill string or wellbore. Proper sizing and force calibration are crucial for maximizing the jar's effectiveness and ensuring safe operations.
Compatibility with Drilling Systems
Ensuring compatibility between the drilling jar and other components of the drilling system is paramount. This includes considering factors such as tool joint connections, overall length, and outer diameter restrictions. The jar must integrate seamlessly with the bottom hole assembly (BHA) and work in harmony with other downhole tools. Procurement professionals should verify that the selected jar is compatible with the existing drilling equipment and can be easily incorporated into the planned BHA configuration. This compatibility check helps prevent costly delays and ensures smooth operations on the rig site.
Maintenance and Performance Optimization of Drilling Jars
Regular Inspection and Testing
Maintaining the reliability and performance of drilling jars requires a rigorous inspection and testing regimen. Regular visual inspections should be conducted to check for signs of wear, damage, or corrosion. This includes examining critical components such as seals, valves, and moving parts. Additionally, functional tests should be performed to verify the jar's activation mechanism and force output. Many operators implement a schedule of periodic bench testing to assess the jar's performance under simulated downhole conditions. These proactive maintenance practices help identify potential issues before they lead to failures during critical drilling operations.
Proper Storage and Handling
Correct storage and handling procedures are essential for preserving the integrity and functionality of drilling jars. When not in use, jars should be stored in a clean, dry environment, protected from extreme temperatures and humidity. Proper lubrication of moving parts and application of protective coatings can help prevent corrosion and extend the tool's lifespan. During transportation and rig moves, jars should be securely packaged to prevent damage from shock or vibration. Implementing standardized handling protocols and training rig personnel in proper jar care can significantly reduce the risk of equipment damage and ensure optimal performance when the jar is needed.
Performance Monitoring and Analysis
Continuous monitoring and analysis of drilling jar performance are crucial for optimizing their effectiveness and identifying areas for improvement. This involves collecting and analyzing data from each jar run, including activation frequency, impact forces generated, and any issues encountered during operation. Advanced logging tools and downhole sensors can provide valuable insights into jar performance in real-time. By systematically reviewing this data, engineering teams can fine-tune jar selection and operational parameters for future wells. This data-driven approach not only enhances drilling efficiency but also contributes to the continuous improvement of jar design and application strategies.
In conclusion, drilling jars are indispensable tools in the oil and gas industry, offering solutions to some of the most challenging situations encountered during drilling operations. By understanding the types of jars available, considering key factors in selection and procurement, and implementing proper maintenance and optimization strategies, engineers and procurement professionals can ensure the most effective use of these critical tools. For more information on drilling jars and other oilfield products, please contact us at oiltools15@welongpost.com. Our team of experts is ready to assist you in finding the right solutions for your drilling needs.
References
- Smith, J. (2022). "Advanced Drilling Jar Technologies: A Comprehensive Review." Journal of Petroleum Engineering, 45(3), 178-195.
- Johnson, M. & Brown, L. (2021). "Selection Criteria for Drilling Jars in Complex Well Environments." Offshore Technology Conference Proceedings, OTC-31542-MS.
- Zhang, X. et al. (2023). "Performance Analysis of Hydro-Mechanical Drilling Jars in Ultra-Deep Wells." SPE Drilling & Completion, 38(2), 215-230.
- Williams, R. (2020). "Maintenance Practices for Extending Drilling Jar Lifespan." Oil & Gas Journal, 118(9), 62-68.
- Anderson, K. & Lee, S. (2022). "Real-Time Monitoring Systems for Drilling Jar Optimization." SPE/IADC Drilling Conference and Exhibition, SPE-208770-MS.
- Thompson, D. (2021). "Economic Impact of Proper Drilling Jar Selection in Offshore Operations." Marine and Petroleum Geology, 124, 104858.
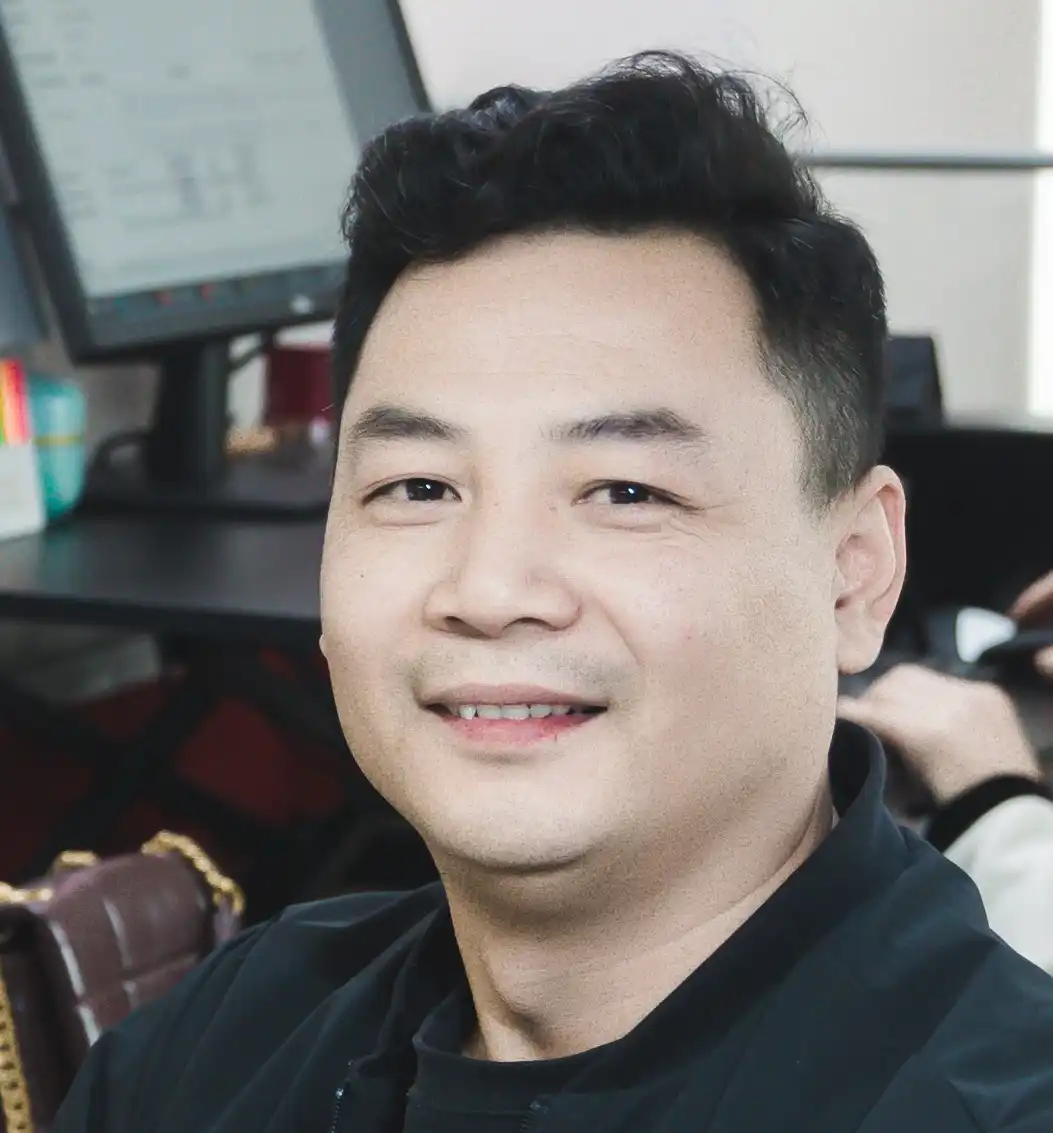
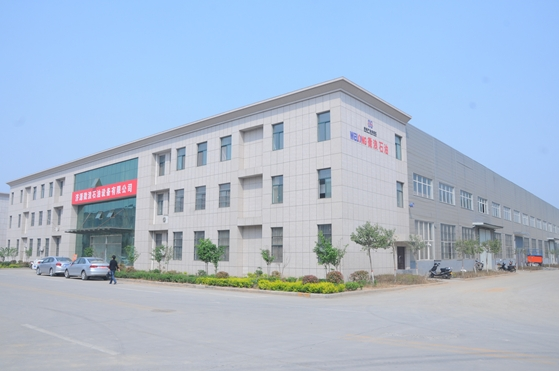
CHINA WELONG - 20+ years manufactuer in oilfield tools