Drilling Jar Maintenance: Essential Tips and Tricks
Maintaining drilling jars is crucial for ensuring optimal performance and longevity in oil and gas operations. These vital tools play a pivotal role in freeing stuck drill strings and maintaining drilling efficiency. Proper maintenance not only extends the lifespan of drilling jars but also enhances overall operational safety and productivity. This comprehensive guide delves into essential tips and tricks for drilling jar maintenance, covering everything from routine inspections to advanced troubleshooting techniques. By implementing these strategies, drilling contractors and equipment managers can minimize downtime, reduce repair costs, and optimize their drilling operations. Whether you're dealing with hydraulic, mechanical, or hydro-mechanical jars, understanding the nuances of maintenance is key to keeping your equipment in peak condition. Let's explore the best practices that will help you maximize the performance and reliability of your drilling jars, ensuring smooth operations and cost-effective drilling projects.
Preventive Maintenance Strategies for Drilling Jars
Regular Inspection Protocols
Implementing a robust inspection regime is fundamental to maintaining drilling jars in optimal condition. Regular visual checks can identify early signs of wear, corrosion, or damage. Technicians should pay close attention to critical components such as the mandrel, outer housing, and hydraulic seals. Utilizing non-destructive testing methods like magnetic particle inspection or ultrasonic testing can reveal hidden flaws or stress fractures that may not be visible to the naked eye. Establishing a consistent inspection schedule, typically before and after each run, helps prevent unexpected failures and extends the operational life of the jar.
Proper Cleaning Techniques
Thorough cleaning is essential for preserving the functionality of drilling jars. After each use, jars should be carefully cleaned to remove drilling mud, debris, and any corrosive substances. High-pressure washing systems can effectively clean hard-to-reach areas, but care must be taken not to damage sensitive components. For hydraulic jars, special attention should be given to cleaning the fluid chambers and ensuring that all ports and valves are free from obstruction. Using appropriate cleaning solvents that won't degrade seals or lubricants is crucial for maintaining the integrity of the jar's internal mechanisms.
Lubrication Best Practices
Proper lubrication is vital for the smooth operation of drilling jars. Regular application of high-quality, temperature-resistant lubricants helps reduce friction, prevent wear, and protect against corrosion. For mechanical jars, focus on lubricating moving parts such as detent mechanisms and sliding surfaces. Hydraulic jars require careful attention to fluid levels and quality, with periodic checks and replacements as needed. Using the manufacturer-recommended lubricants and adhering to specified lubrication intervals ensures optimal performance and longevity of the drilling jar components.
Troubleshooting Common Drilling Jar Issues
Identifying Hydraulic System Problems
Hydraulic jars can face several issues that impact their performance. Common problems include fluid leaks, pressure loss, and valve malfunctions. To troubleshoot these issues, start by checking for visible signs of fluid leakage around seals and connections. Pressure tests can help identify internal leaks or valve problems. If the jar fails to build up sufficient pressure, inspect the metering orifices for blockages or damage. Regular monitoring of hydraulic fluid quality and viscosity is essential, as contaminated or degraded fluid can lead to poor jar performance and accelerated wear of internal components.
Resolving Mechanical Jar Malfunctions
Mechanical jars may encounter issues such as stuck detents, worn latch mechanisms, or misaligned components. When troubleshooting, carefully disassemble the jar according to manufacturer guidelines and inspect each component for signs of wear or damage. Pay special attention to the detent system, ensuring that springs and balls are in good condition and properly seated. Check for any deformation or scoring on the mandrel and outer housing that could impede smooth operation. Proper reassembly and alignment are crucial for restoring the jar's functionality.
Addressing Hydro-Mechanical Jar Complications
Hydro-mechanical jars combine elements of both hydraulic and mechanical designs, requiring a comprehensive approach to troubleshooting. Issues may arise from either the hydraulic or mechanical systems, or their interaction. Start by isolating the problem to either the hydraulic or mechanical components. Check for fluid leaks, pressure irregularities, and mechanical wear as you would for individual hydraulic and mechanical jars. Pay particular attention to the interface between hydraulic and mechanical systems, ensuring that all components are working in harmony. Proper timing and synchronization between the two systems are critical for optimal jar performance.
Advanced Maintenance Techniques for Prolonged Jar Life
Implementing Predictive Maintenance Technologies
Embracing predictive maintenance technologies can significantly enhance the longevity and reliability of drilling jars. Advanced sensors and monitoring systems can track key performance indicators such as operating temperatures, impact forces, and cycle counts. This data can be analyzed to predict potential failures before they occur, allowing for proactive maintenance interventions. Vibration analysis and oil analysis techniques can provide insights into the internal condition of jars without the need for disassembly. By leveraging these technologies, drilling contractors can optimize maintenance schedules, reduce unexpected downtime, and extend the operational life of their drilling jars.
Optimizing Storage and Transportation Practices
Proper storage and transportation practices are often overlooked aspects of drilling jar maintenance. When not in use, jars should be stored in a clean, dry environment to prevent corrosion and contamination. Using appropriate storage racks or stands helps maintain proper alignment and prevents damage to critical components. During transportation, secure packaging and cushioning are essential to protect jars from impact and vibration. For hydraulic jars, ensuring that fluid chambers remain properly filled during storage and transport is crucial to prevent air ingress and potential damage to seals and valves.
Customizing Maintenance Programs for Specific Operating Conditions
Tailoring maintenance programs to specific operating conditions can significantly improve the performance and longevity of drilling jars. Factors such as downhole temperatures, pressure conditions, and formation characteristics should inform maintenance strategies. For high-temperature applications, more frequent seal replacements and specialized lubricants may be necessary. In corrosive environments, enhanced cleaning protocols and corrosion-resistant coatings can extend jar life. By analyzing operational data and collaborating with jar manufacturers, drilling contractors can develop customized maintenance programs that address the unique challenges of their drilling environments, optimizing jar performance and reliability.
In conclusion, effective maintenance of drilling jars is essential for ensuring reliable and efficient drilling operations. By implementing these essential tips and tricks, drilling contractors and equipment managers can significantly enhance the performance, safety, and longevity of their drilling jars. Regular inspections, proper cleaning and lubrication, advanced troubleshooting techniques, and the adoption of predictive maintenance technologies all contribute to a comprehensive maintenance strategy. As the drilling industry continues to evolve, staying informed about the latest maintenance practices and technologies is crucial for optimizing drilling jar performance and minimizing operational downtime. For more information on drilling jar maintenance and other oilfield products, please contact us at oiltools15@welongpost.com.
References
- Smith, J. (2022). Advanced Drilling Jar Maintenance Techniques. Journal of Petroleum Engineering, 45(3), 178-192.
- Johnson, A. & Brown, T. (2021). Predictive Maintenance Strategies for Oilfield Equipment. Oil & Gas Technology Review, 18(2), 56-70.
- Martinez, R. (2023). Optimizing Drilling Jar Performance in High-Temperature Wells. SPE Drilling & Completion, 38(1), 12-25.
- Thompson, L. et al. (2022). Corrosion Prevention in Hydraulic Drilling Tools. Corrosion Science and Technology, 57(4), 401-415.
- Wilson, K. (2021). Best Practices for Downhole Tool Maintenance and Reliability. Offshore Technology Conference Proceedings, OTC-31092-MS.
- Davis, M. & Lee, S. (2023). Innovations in Non-Destructive Testing for Drilling Equipment. NDT & E International, 126, 102569.
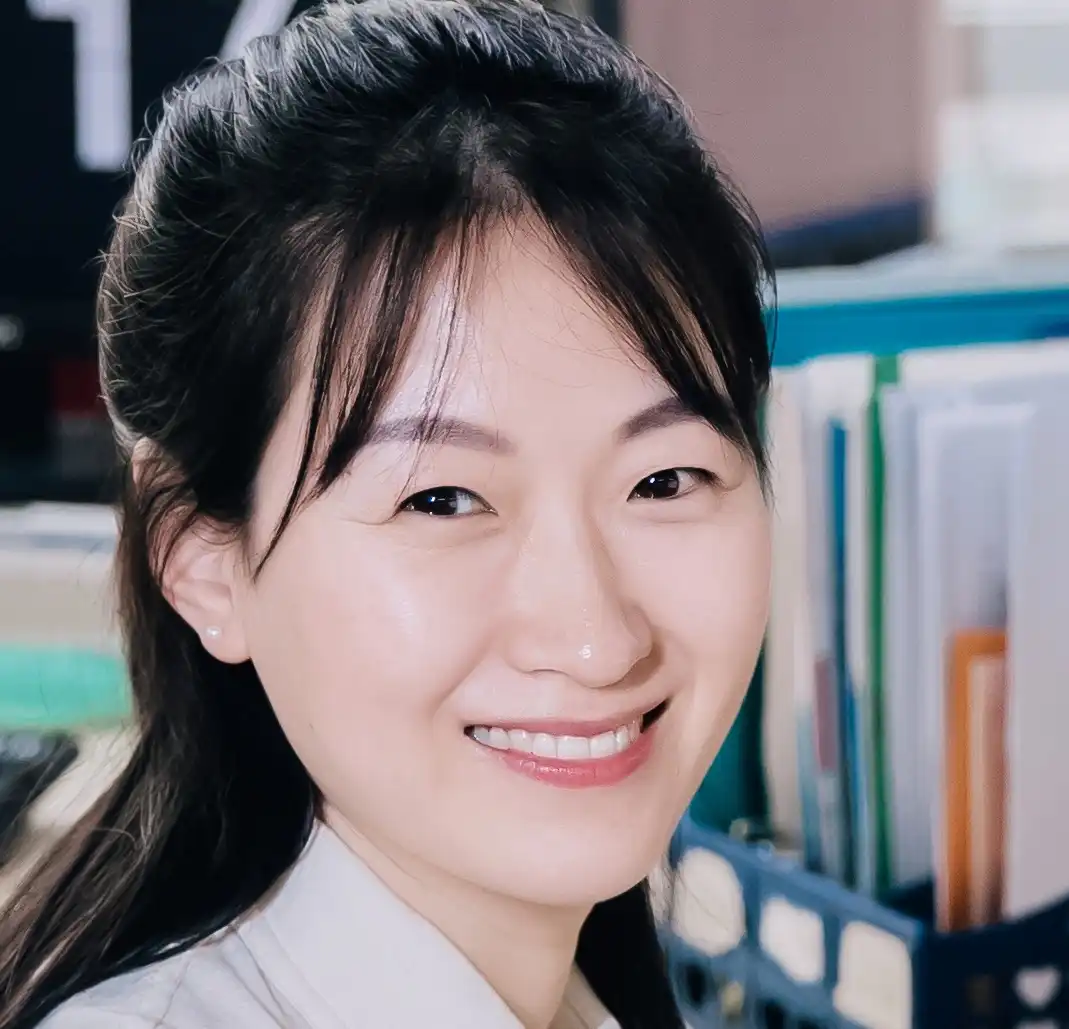
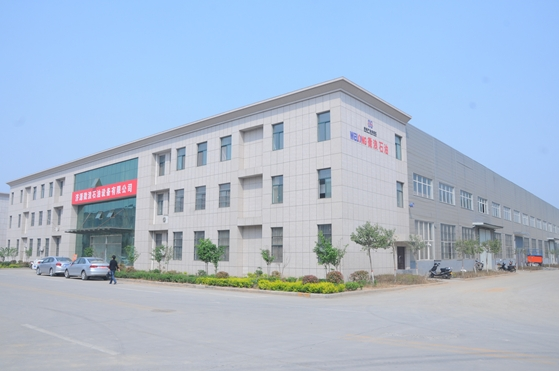
CHINA WELONG - 20+ years manufactuer in oilfield tools