How 42CrMo4 Shaft Forging Enhances Fatigue Resistance in Heavy Machinery
In the realm of heavy machinery, particularly in the oil and gas industry, the importance of robust and durable components cannot be overstated. Among these critical elements, 42CrMo4 shaft forging stands out as a game-changer in enhancing fatigue resistance. This high-strength alloy steel, when subjected to the forging process, exhibits remarkable properties that significantly improve the longevity and reliability of heavy machinery components. The forging process aligns the grain structure of the metal, resulting in superior mechanical properties and enhanced fatigue resistance. This is particularly crucial in applications where components are subjected to cyclic loading and high stress, such as in drilling equipment and offshore platforms. The combination of the alloy's chemical composition and the forging process creates a synergistic effect, dramatically increasing the material's ability to withstand repeated stress cycles without failure. This enhanced fatigue resistance translates to reduced downtime, lower maintenance costs, and improved overall efficiency in heavy machinery operations.
What Makes 42CrMo4 Ideal for High-Cycle Fatigue Applications?
Chemical Composition and Its Impact
The distinctive chemical composition of 42CrMo4 steel plays a crucial role in making it an ideal material for high-cycle fatigue applications. This alloy is carefully formulated with a balanced blend of carbon, chromium, and molybdenum, each element contributing uniquely to the material's overall performance. The carbon content, ranging from 0.38% to 0.45%, is integral to the steel’s ability to achieve high hardness and strength, ensuring that it can withstand substantial loads and mechanical stresses. Chromium, making up approximately 0.9% to 1.2%, enhances the steel's hardenability, providing the ability to be heat-treated for superior mechanical properties. Additionally, chromium significantly improves corrosion resistance, making the material more durable in challenging environments. Molybdenum, present at 0.15% to 0.3%, is another key contributor, enhancing the steel's toughness and helping to prevent temper embrittlement, a common issue in high-temperature environments. This well-rounded composition equips 42CrMo4 with the resilience required for high-cycle fatigue applications, making it a reliable choice for demanding industries.
Microstructural Advantages
The microstructure of 42CrMo4 steel is developed through an effective heat treatment process that maximizes its resistance to cyclic loading. When subjected to appropriate heat treatment, the alloy typically forms a structure of tempered martensite, which offers an excellent combination of strength and toughness. This microstructure plays a critical role in the steel's ability to resist crack initiation and propagation, which are the primary causes of fatigue failure. Tempered martensite is particularly well-suited for applications where materials are subjected to continuous stress and strain, as it ensures that the material can absorb and distribute these forces without significant degradation. The refined grain structure further contributes to the material’s ability to withstand high-cycle loading over extended periods, maintaining its structural integrity and extending the component's lifespan.
Mechanical Properties and Fatigue Performance
The mechanical properties of 42CrMo4 shaft forging are optimized for high-cycle fatigue resistance, making it ideal for use in components that endure repeated stress. With a tensile strength typically ranging from 900 MPa to 1200 MPa, 42CrMo4 demonstrates its ability to withstand heavy loads without deformation. Its ductility ensures that the material can undergo some degree of plastic deformation without failing, which helps in absorbing and distributing cyclic stresses effectively. The material also boasts a high yield strength, generally exceeding 700 MPa, which allows it to maintain its structural integrity within the elastic limit under most operational conditions. This combination of high tensile strength, ductility, and yield strength helps 42CrMo4 to resist the formation of localized stress concentrations, a common precursor to fatigue failure. As a result, the material delivers superior performance in applications that require long-term durability under cyclic loads, making it an excellent choice for components such as shafts and other high-performance parts in the railway and automotive industries.
How Does Heat Treatment Optimize 42CrMo4 Fatigue Strength?
Quenching Process and Its Effects
The quenching process is a critical step in optimizing the fatigue strength of 42CrMo4 forged shafts. During quenching, the material is rapidly cooled from its austenitic temperature, typically around 850°C to 880°C, to room temperature. This rapid cooling transforms the austenite into martensite, a hard and strong microstructure. The quenching medium, often oil or polymer-based solutions, is carefully selected to achieve the optimal cooling rate. This process introduces internal stresses and increases hardness, setting the stage for subsequent tempering.
Tempering for Balanced Properties
Following quenching, tempering is performed to relieve internal stresses and achieve a balance between strength and toughness. Tempering of 42CrMo4 is typically carried out at temperatures between 550°C and 680°C. This process allows carbon atoms to diffuse out of the martensite, forming finely dispersed carbides. The result is a tempered martensitic structure that retains much of the strength from quenching while significantly improving ductility and toughness. This balanced microstructure is key to the material's excellent fatigue resistance.
Surface Treatments for Enhanced Performance
In addition to bulk heat treatment, surface treatments can further enhance the fatigue performance of 42CrMo4 shaft forging. Techniques such as induction hardening or nitriding can be applied to create a hard, wear-resistant surface layer while maintaining a tough core. These surface treatments introduce compressive residual stresses in the surface layers, which are particularly effective in combating fatigue failure initiation at the surface, where stresses are often highest.
How to Test 42CrMo4 Shafts for Fatigue Life Validation?
Rotating Beam Fatigue Testing
Rotating beam fatigue testing is a standard method for evaluating the fatigue life of 42CrMo4 forged shafts. In this test, a cylindrical specimen is subjected to alternating bending stresses while rotating. The test simulates the cyclic loading conditions experienced by rotating shafts in service. By applying different stress levels, a fatigue curve (S-N curve) can be generated, providing crucial information about the material's fatigue limit and expected life under various loading conditions.
Ultrasonic Fatigue Testing
For high-cycle fatigue assessment, ultrasonic fatigue testing offers significant advantages. This method allows for rapid accumulation of fatigue cycles (up to 10^9 cycles) in a reasonable timeframe. In ultrasonic fatigue testing, the specimen is vibrated at its resonant frequency (typically 20 kHz), inducing cyclic stresses. This technique is particularly useful for evaluating the very high cycle fatigue behavior of 42CrMo4 shafts, which is crucial for components expected to have extended service lives.
Fracture Mechanics Approach
The fracture mechanics approach provides valuable insights into the fatigue crack growth behavior of 42CrMo4 forged shafts. This method involves introducing a small, controlled crack into a specimen and monitoring its growth under cyclic loading. Parameters such as the stress intensity factor range (ΔK) and crack growth rate (da/dN) are measured to characterize the material's resistance to fatigue crack propagation. This approach is particularly useful for predicting the remaining life of components with pre-existing flaws and for designing inspection intervals.
Source: CHINA WELONG-Oilfield tools Manufacturer
FAQ about Shaft forging
What are the key advantages of forged shafts over machined ones?
Forged shafts offer several advantages over their machined counterparts. Firstly, the forging process aligns the grain structure of the metal, resulting in superior strength and toughness. This aligned grain structure significantly enhances the shaft's ability to withstand fatigue and impact loads. Secondly, forging can produce near-net-shape components, reducing material waste and machining time. Lastly, forged shafts typically exhibit better surface integrity and reduced likelihood of internal defects, contributing to improved overall performance and longevity.
How does the forging process impact the mechanical properties of 42CrMo4?
The forging process substantially enhances the mechanical properties of 42CrMo4. During forging, the material undergoes severe plastic deformation under high pressure and temperature. This process breaks down the cast structure, refines the grain size, and closes any porosity or voids present in the original material. As a result, forged 42CrMo4 shafts exhibit higher tensile strength, improved ductility, and enhanced impact resistance compared to cast or machined components. The forging process also introduces beneficial residual stresses that can improve fatigue resistance.
What quality control measures are essential for 42CrMo4 shaft forging?
Quality control for 42CrMo4 shaft forging involves several critical steps. Initially, the chemical composition of the raw material is verified to ensure it meets the specified requirements. During the forging process, parameters such as temperature, pressure, and deformation rate are carefully monitored and controlled. Post-forging, heat treatment processes are closely supervised to achieve the desired microstructure and mechanical properties. Non-destructive testing methods, including ultrasonic testing and magnetic particle inspection, are employed to detect any internal or surface defects. Finally, dimensional checks and mechanical property tests are conducted to verify compliance with specifications.
In conclusion, the utilization of 42CrMo4 shaft forging in heavy machinery, particularly in the oil and gas industry, represents a significant advancement in component durability and performance. The unique properties of this alloy, combined with the benefits of the forging process, result in shafts that exhibit exceptional fatigue resistance, crucial for the demanding environments of drilling and offshore operations. As the industry continues to push the boundaries of what's possible in challenging environments, the role of materials like 42CrMo4 becomes increasingly vital. For those seeking to optimize their heavy machinery components and enhance operational efficiency, exploring the benefits of 42CrMo4 forged shafts is a step in the right direction. For more information on how these advanced forging solutions can benefit your operations, please contact us at oiltools15@welongpost.com. Welong is committed to providing high-quality forged components that meet the rigorous demands of the oil and gas industry.
References
1. Bhadeshia, H.K.D.H., & Honeycombe, R. (2017). Steels: Microstructure and Properties. Butterworth-Heinemann.
2. Totten, G.E. (Ed.). (2006). Steel Heat Treatment: Metallurgy and Technologies. CRC Press.
3. Schijve, J. (2009). Fatigue of Structures and Materials. Springer Science & Business Media.
4. ASM International. (1996). ASM Handbook, Volume 19: Fatigue and Fracture. ASM International.
5. Dieter, G.E., & Bacon, D.J. (1988). Mechanical Metallurgy. McGraw-Hill.
6. Nishida, S.I. (2019). Failure Analysis in Engineering Applications. Butterworth-Heinemann.
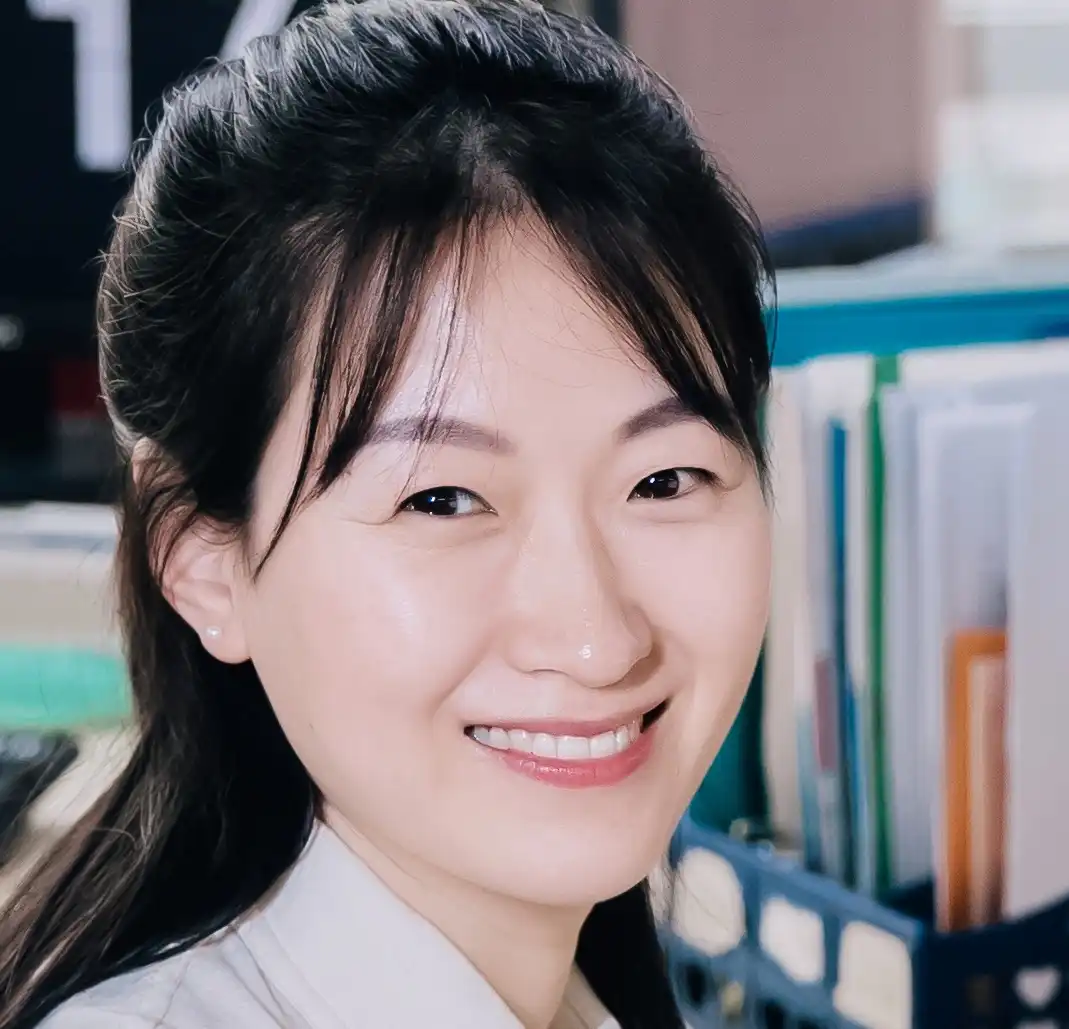
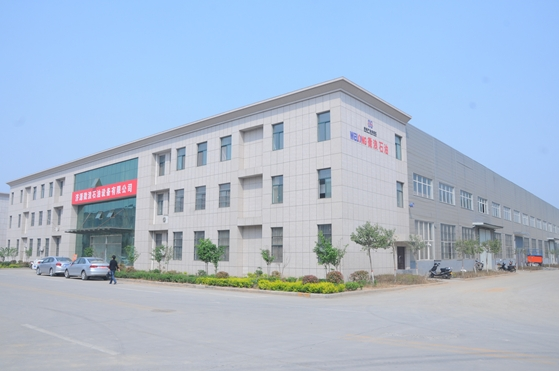
CHINA WELONG - 20+ years manufactuer in oilfield tools