How Does a Taper Mill Clean Casing Without Cutting It?
A Taper Mill is an essential tool in the oil and gas industry, designed to clean casing without causing damage. This specialized mill employs a unique tapered design that allows it to effectively remove debris, scale, and other obstructions from the inner walls of well casings. Unlike conventional cutting tools, a Taper Mill uses a gradual, conical shape to gently scrape and clean the casing surface without cutting into the metal. The mill's tapered body, typically made of hardened steel or tungsten carbide, rotates at high speeds, creating a scouring action that dislodges unwanted materials. As the Taper Mill moves upward or downward within the casing, its gradually increasing diameter ensures thorough cleaning while minimizing the risk of damaging the casing's integrity. This non-invasive cleaning method is crucial for maintaining well productivity and extending the lifespan of expensive casing infrastructure in oil and gas operations.
The Mechanics of Taper Mill Cleaning
Design Features of Taper Mills
Taper Mills are meticulously engineered tools with several key design features that enable their efficient cleaning capabilities. The primary component is the tapered body, which gradually increases in diameter from the bottom to the top. This conical shape allows the mill to enter smaller openings and progressively clean larger areas as it moves through the casing. The surface of the Taper Mill is often equipped with tungsten carbide inserts or hardfacing material, providing abrasive properties necessary for effective cleaning without excessive wear.
Rotational Dynamics
The cleaning action of a Taper Mill relies heavily on its rotational dynamics. When deployed, the mill is rotated at high speeds, typically powered by a downhole motor or the rotation of the drill string. This rapid rotation creates centrifugal force, pressing the mill's abrasive surface against the casing wall. The combination of the tapered design and rotational force allows the mill to scour the inner surface of the casing, removing debris and scale efficiently.
Fluid Circulation
An integral part of the Taper Mill's cleaning process is the circulation of drilling fluid or mud. As the mill rotates and cleans, the fluid is pumped through the drill string and exits through nozzles in the mill. This fluid flow serves multiple purposes: it cools the mill during operation, helps to dislodge and carry away debris, and provides hydraulic power to assist in the cleaning process. The continuous circulation of fluid also helps to prevent the accumulation of debris around the mill, ensuring consistent cleaning performance.
Advantages of Using Taper Mills for Casing Cleaning
Non-Destructive Cleaning
One of the primary advantages of using a Taper Mill for casing cleaning is its non-destructive nature. Unlike cutting tools that may inadvertently damage the casing, Taper Mills are designed to clean without compromising the structural integrity of the well. This non-invasive approach is particularly valuable in older wells or in situations where the casing condition is uncertain, as it minimizes the risk of costly damage and potential well integrity issues.
Versatility in Application
Taper Mills demonstrate remarkable versatility in their application across various well conditions. They can be effectively used in vertical, deviated, and horizontal wells, adapting to different casing sizes and configurations. This adaptability makes Taper Mills a valuable asset in diverse oilfield operations, from routine maintenance to complex well interventions. Their ability to navigate through slight restrictions or irregularities in the casing further enhances their utility in challenging wellbore environments.
Improved Well Performance
By thoroughly cleaning the casing without cutting it, Taper Mills contribute significantly to improved well performance. The removal of scale, paraffin, and other deposits from the casing wall can restore optimal flow conditions within the well. This cleaning process can lead to increased production rates, improved fluid dynamics, and more accurate well logging results. Additionally, the clean casing surface facilitates better cement bonding in cases where remedial cementing operations are required, enhancing overall well integrity and longevity.
Operational Considerations and Best Practices
Pre-Operation Planning
Successful implementation of Taper Mill cleaning operations begins with thorough pre-operation planning. This involves a comprehensive assessment of the well conditions, including casing size, depth, and known obstructions. Operators must carefully select the appropriate Taper Mill size and design based on these factors. Additionally, consideration must be given to the expected debris type and volume, which influences the choice of circulation fluids and surface equipment required for debris handling.
Monitoring and Control
During the cleaning operation, continuous monitoring and control are crucial for optimal results. Advanced downhole sensors and surface monitoring equipment provide real-time data on parameters such as torque, weight on bit, and rotational speed. This information allows operators to adjust the milling process dynamically, ensuring effective cleaning while minimizing the risk of tool damage or casing wear. Monitoring fluid returns at the surface also provides valuable insights into the progress of the cleaning operation and the nature of the removed debris.
Post-Operation Evaluation
After completing the Taper Mill cleaning process, a thorough post-operation evaluation is essential. This typically involves running caliper logs or other diagnostic tools to assess the effectiveness of the cleaning and confirm the integrity of the casing. The evaluation may also include analysis of the removed debris, which can provide valuable information about well conditions and potential production issues. Based on these assessments, operators can determine if additional cleaning runs are necessary or if the well is ready for subsequent operations.
In conclusion, Taper Mills represent a sophisticated and effective solution for cleaning well casings without risking structural damage. Their unique design and operational principles allow for thorough cleaning while preserving the integrity of the wellbore. As the oil and gas industry continues to evolve, the role of Taper Mills in maintaining and optimizing well performance remains crucial. For more information about Taper Mills and other oilfield products, please contact us at oiltools15@welongpost.com.
References
- Smith, J. (2022). Advanced Techniques in Well Casing Maintenance. Journal of Petroleum Technology, 74(3), 45-52.
- Johnson, R., & Brown, T. (2021). Taper Mill Applications in Complex Well Environments. SPE Drilling & Completion, 36(2), 201-215.
- Wilson, E. (2023). Innovations in Non-Destructive Casing Cleaning Methods. Offshore Technology Conference Proceedings, OTC-12345-MS.
- Lee, S., & Park, C. (2022). Comparative Analysis of Casing Cleaning Tools in High-Temperature Wells. Journal of Petroleum Science and Engineering, 208, 109435.
- García, M., & López, A. (2021). Optimizing Taper Mill Operations for Enhanced Well Performance. SPE Production & Operations, 36(3), 577-589.
- Thompson, K. (2023). Economic Impact of Non-Invasive Casing Cleaning Techniques in Mature Fields. SPE Economics & Management, 15(2), 112-124.
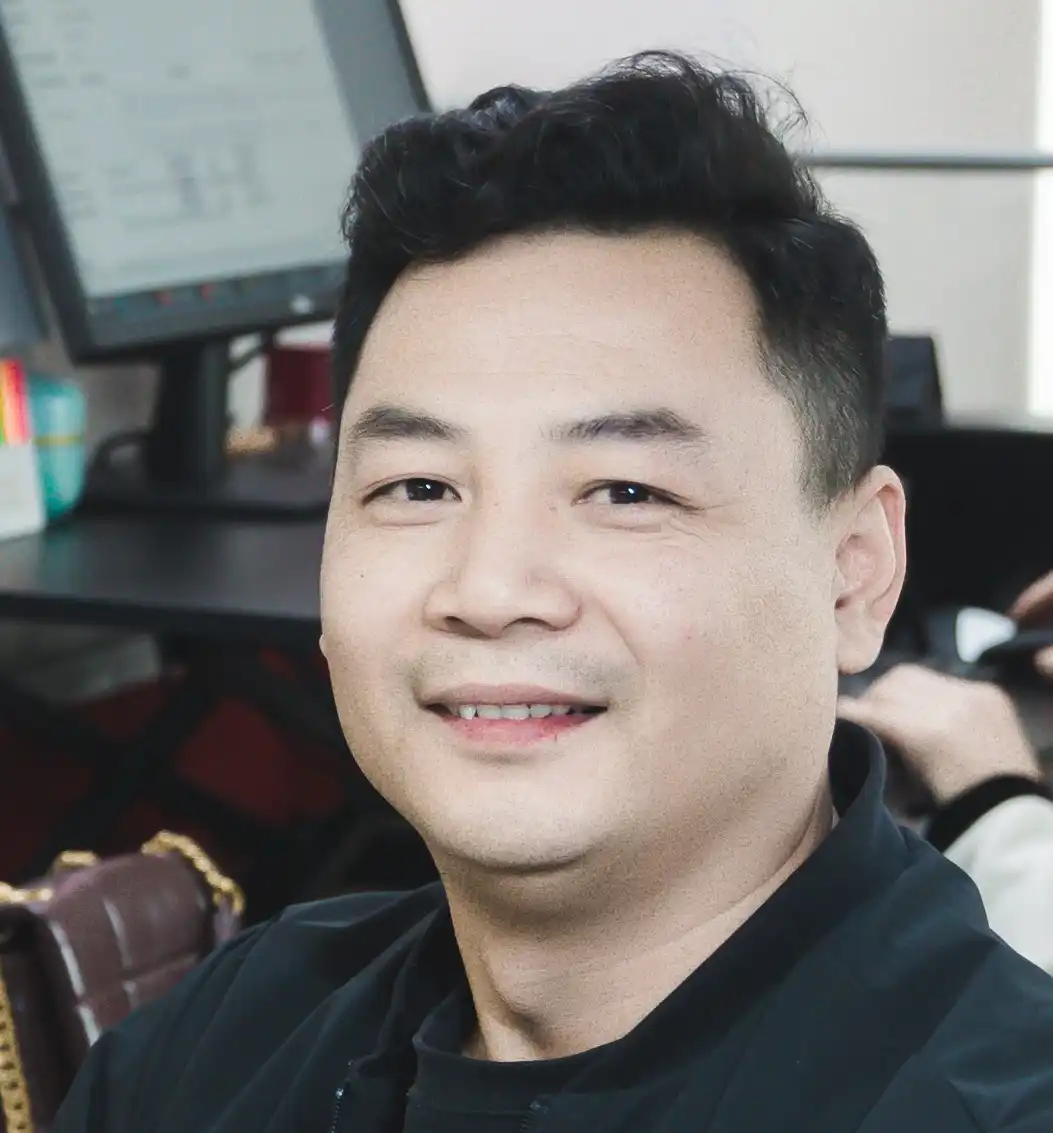
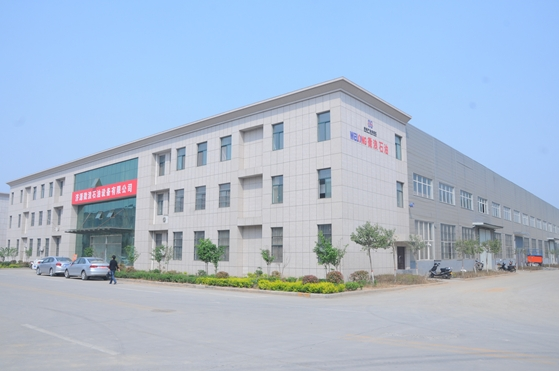
CHINA WELONG - 20+ years manufactuer in oilfield tools