How to maintain a wellhead?
Maintaining a wellhead is crucial for ensuring the safety, efficiency, and longevity of oil and gas production operations. Proper wellhead maintenance involves regular inspections, timely repairs, and preventive measures to mitigate potential issues. To effectively maintain a wellhead, operators should focus on several key aspects, including routine visual checks, pressure testing, lubrication of moving parts, and corrosion prevention. Additionally, it's essential to adhere to manufacturer guidelines and industry standards when performing maintenance tasks. By implementing a comprehensive maintenance program, operators can minimize downtime, reduce the risk of leaks or blowouts, and optimize the overall performance of their wellhead equipment. Regular maintenance not only extends the lifespan of the wellhead but also contributes to environmental protection and worker safety in the challenging conditions of oil and gas extraction.
What Are the Key Components of a Wellhead Requiring Maintenance
Wellhead Valves and Actuators
Valves and actuators are integral components in controlling the flow of fluids such as oil and gas from the well. Their effective operation is crucial for maintaining proper well control. Regular maintenance is necessary to ensure that these components continue to function without issues. This includes the lubrication of all moving parts, which helps minimize friction and prevents premature wear. Additionally, inspecting valves for signs of wear or damage is essential to detect any potential issues before they escalate. The valve seals and seats should be tested for leaks, as compromised seals can lead to operational failures. Moreover, verifying the correct actuation and closure of the valves ensures that they function as expected during normal operations. By conducting regular maintenance, potential issues can be addressed early, reducing the risk of unexpected failures and improving the overall reliability of the system.
Casing and Tubing Hangers
Casing and tubing hangers are responsible for supporting the weight of the production string while also providing a vital seal between the wellbore and the surrounding environment. These hangers must be regularly checked for any signs of corrosion or physical damage, as these issues can weaken the structure and compromise the well's integrity. Additionally, it’s important to assess the integrity of the seals, as damaged seals can result in leaks. Ensuring that the hangers are properly seated and aligned is another crucial maintenance task. If hangers are misaligned, it can lead to operational issues and even failure of the wellhead system. Finally, checking the torque on bolts and fasteners ensures that the entire assembly is secure and that no components are under excessive strain. Routine maintenance of casing and tubing hangers is key to preventing leaks and ensuring the overall stability of the well.
Wellhead Seals and Gaskets
Seals and gaskets play a vital role in preventing leaks and maintaining pressure integrity in the wellhead system. Over time, these components are subjected to high pressures and fluctuating temperatures, which can cause wear and degradation. Regular inspection of seals and gaskets is necessary to detect any signs of damage or wear that could lead to leaks. If any components are found to be worn or damaged, they should be replaced promptly to prevent system failures. Additionally, maintaining clean sealing surfaces and ensuring proper preparation before reinstallation is crucial for the effectiveness of new seals and gaskets. Ensuring correct installation and compression of these components is also essential for optimal sealing performance. Regular care and attention to wellhead seals and gaskets help maintain safe operations and prevent environmental contamination, ensuring the long-term success and safety of the well.
How Often Should Wellhead Equipment Be Inspected and Serviced
Daily Visual Inspections
Daily visual inspections are essential for ensuring the early detection of any potential issues in the wellhead system. These quick checks are vital in maintaining safe and efficient operations, as they allow operators to spot visible signs of damage or wear before they turn into more serious problems. During daily inspections, operators should focus on identifying any signs of leaks or fluid buildup around key components, as this could indicate seal failure or other issues. It's also important to look for visible signs of corrosion, rust, or physical damage on parts such as valves, tubing, or other exposed components. Verifying that all valves are in their correct positions is crucial for ensuring the system’s proper functioning, as even slight misalignments can lead to operational problems. Additionally, ensuring that pressure gauges are reading correctly helps in monitoring the system’s performance. These quick daily checks can identify minor issues early on, allowing for prompt action and preventing more significant malfunctions down the road.
Monthly Detailed Inspections
Monthly inspections offer a more in-depth evaluation of the system’s components, allowing operators to assess the condition of key parts that may not be immediately visible during daily checks. During these more thorough inspections, it’s important to check all bolts and connections to ensure they are properly torqued, as loose bolts can lead to instability or leaks. The condition of valve stems and seals should also be closely inspected for any signs of wear, which could affect their ability to function properly. Additionally, the operation of all valves and actuators should be tested to ensure they are responding as expected. Any surface coatings should be checked for signs of deterioration, as exposure to harsh conditions can cause these coatings to break down over time. By conducting detailed monthly inspections, potential issues can be identified and resolved before they impact the overall performance or safety of the system.
Annual Comprehensive Maintenance
Annual maintenance involves a thorough, in-depth review of the entire system to ensure that all components are functioning optimally and safely. This process typically includes pressure testing to check the integrity of seals and connections, which is crucial for preventing leaks and ensuring the system is airtight. Internal inspections of critical components such as valves and other moving parts help identify any wear or damage that may not be visible during regular checks. Parts that are found to be worn or at the end of their operational life should be replaced during the annual maintenance to maintain reliability. This comprehensive service also includes updating maintenance records, ensuring that the system's history is accurately documented for future reference. Annual maintenance often requires specialized tools and expertise, as well as a thorough understanding of the system to identify and address any potential issues that could compromise safety or performance. This helps ensure the long-term functionality and safety of the equipment.
How Does Wellhead Maintenance Prevent Pressure Leaks
Regular Seal Inspection and Replacement
One of the primary ways wellhead maintenance prevents pressure leaks is through regular seal inspection and replacement. Seals play a crucial role in maintaining pressure integrity within the wellhead system. Over time, these seals can degrade due to exposure to harsh chemicals, high pressures, and temperature fluctuations. By implementing a proactive approach to seal maintenance, operators can:
- Identify signs of seal wear or damage before failure occurs
- Replace seals at recommended intervals or when showing signs of deterioration
- Ensure proper installation and seating of new seals
- Use appropriate seal materials for specific well conditions
Regular attention to seals helps maintain the pressure-tight integrity of the product, preventing costly and potentially dangerous leaks.
Proper Torque Management
Maintaining correct torque on bolts and connections is another critical aspect of preventing pressure leaks in wellheads. Proper torque management ensures that all components are securely fastened and maintain their sealing capabilities under various operating conditions. Key elements of torque management include:
- Regular checking and retightening of bolts to specified torque values
- Using calibrated torque wrenches for accurate tightening
- Following manufacturer guidelines for torque sequences and values
- Documenting torque checks and adjustments for traceability
By maintaining proper torque on all connections, operators can significantly reduce the risk of pressure leaks caused by loose or improperly tightened components.
Corrosion Prevention and Control
Corrosion is a significant threat to wellhead integrity and can lead to pressure leaks if left unchecked. Effective corrosion prevention and control measures are essential for maintaining the structural integrity of product components. These measures typically include:
- Application and maintenance of protective coatings
- Use of corrosion-resistant materials in wellhead construction
- Implementation of cathodic protection systems
- Regular monitoring and testing for corrosion
By implementing comprehensive corrosion prevention strategies, operators can extend the life of their product equipment and minimize the risk of pressure leaks caused by material degradation.
Source: Oil & Gas field Quality control
FAQ about Wellhead
What are the signs of a wellhead requiring immediate maintenance?
Signs that a wellhead may require immediate maintenance include visible leaks, unusual noises or vibrations, sudden pressure changes, or visible damage to external components. Any of these indicators should prompt an immediate inspection and potential shutdown of operations until the issue can be properly addressed.
How does wellhead maintenance contribute to environmental protection?
Proper product maintenance contributes significantly to environmental protection by preventing leaks and spills that could contaminate soil and water resources. It also helps ensure the efficient operation of the well, reducing emissions and minimizing the environmental footprint of oil and gas extraction activities.
What role does technology play in modern wellhead maintenance?
Technology plays an increasingly important role in product maintenance, with innovations such as remote monitoring systems, predictive maintenance algorithms, and digital twin simulations. These technologies allow for more proactive maintenance strategies, real-time data analysis, and improved decision-making in product management.
In conclusion, maintaining a wellhead is a complex but essential task that requires a comprehensive approach and attention to detail. By focusing on key components, adhering to regular inspection and service schedules, and implementing effective strategies to prevent pressure leaks, operators can ensure the safety, efficiency, and longevity of their wellhead equipment. For more information on wellhead maintenance and high-quality wellhead equipment, please contact us at oiltools15@welongpost.com. Welong is committed to providing top-tier solutions for all your wellhead maintenance needs.
References
- Smith, J. (2022). Wellhead Maintenance Best Practices in the Oil and Gas Industry. Journal of Petroleum Technology, 74(5), 62-70.
- Johnson, A., & Brown, T. (2021). Advanced Techniques in Wellhead Integrity Management. Society of Petroleum Engineers Conference Proceedings, SPE-198765-MS.
- Davis, R. (2023). Corrosion Prevention Strategies for Wellhead Equipment. Materials Performance, 62(3), 30-36.
- Wilson, E., & Thompson, L. (2022). The Role of Predictive Maintenance in Wellhead Operations. Offshore Technology Conference Proceedings, OTC-30456-MS.
- Martinez, C. (2023). Environmental Impact Assessment of Wellhead Maintenance Practices. Environmental Science & Technology, 57(8), 3845-3853.
- Lee, S., & Park, H. (2021). Innovations in Wellhead Seal Technology for High-Pressure Applications. Journal of Petroleum Science and Engineering, 196, 108015.
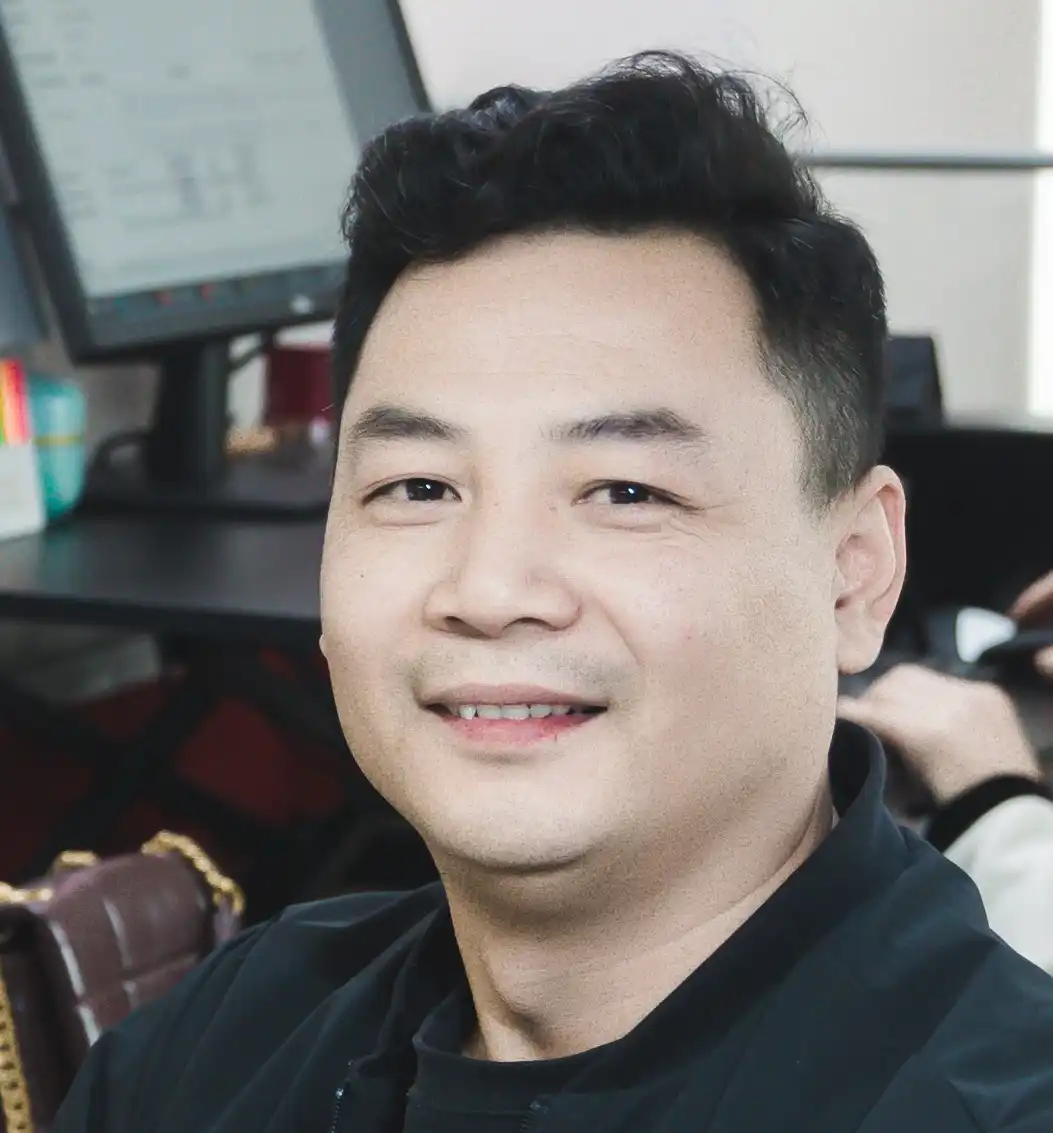
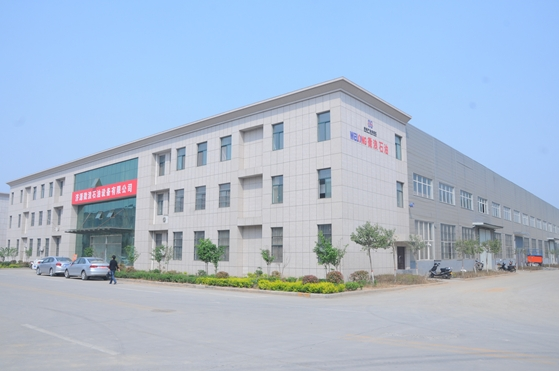
CHINA WELONG - 20+ years manufactuer in oilfield tools