How to Select the Right Drilling Hose for Optimal Performance?
Selecting the right drilling hose is crucial for achieving optimal performance in oil and gas operations. The proper choice can significantly impact efficiency, safety, and cost-effectiveness. To make an informed decision, consider factors such as pressure ratings, temperature resistance, flexibility, and durability. Evaluate your specific drilling requirements, including depth, fluid types, and environmental conditions. Look for hoses that meet or exceed industry standards like API Spec 7K. Pay attention to the hose's construction materials, reinforcement layers, and end fittings. Additionally, consider the reputation of the manufacturer and their track record in producing high-quality drilling equipment. By carefully assessing these factors and consulting with experts, you can select a drilling hose that enhances your operations, minimizes downtime, and ensures long-term reliability. Remember, investing in the right hose upfront can lead to substantial savings and improved performance in the long run.
Key Factors to Consider When Choosing a Drilling Hose
Pressure Ratings and Operating Conditions
When selecting a drilling hose, one of the primary considerations is its pressure rating. This rating determines the maximum internal pressure the hose can withstand during operation. It's essential to choose a hose with a pressure rating that exceeds your expected operating pressures to ensure safety and longevity. Consider both working pressure and burst pressure specifications.
Operating conditions also play a crucial role in hose selection. Factors such as temperature extremes, exposure to corrosive fluids, and abrasive environments can significantly impact hose performance. Look for hoses designed to withstand the specific conditions of your drilling site, including resistance to chemicals, UV radiation, and ozone.
Hose Construction and Materials
The construction and materials used in a drilling hose greatly influence its performance and durability. High-quality hoses typically feature multiple layers, including an inner tube, reinforcement layers, and an outer cover. The inner tube should be compatible with the fluids being transported, while the reinforcement layers provide strength and pressure resistance.
Common materials used in drilling hose construction include nitrile rubber, synthetic rubbers, and thermoplastics. Each material offers different properties in terms of flexibility, chemical resistance, and temperature tolerance. Consider the specific requirements of your drilling operation when evaluating hose materials.
Flexibility and Handling Characteristics
The flexibility of a drilling hose is crucial for ease of installation and maneuverability during operations. A flexible hose can better accommodate movement and vibration, reducing stress on connections and prolonging the hose's lifespan. However, it's important to balance flexibility with the hose's ability to maintain its shape under pressure.
Consider the hose's bend radius and its ability to resist kinking or collapsing under its own weight. These factors are particularly important in applications where the hose must navigate tight spaces or make sharp turns. Additionally, evaluate the hose's weight and handling characteristics to ensure it can be easily managed by your crew.
Evaluating Hose Performance and Compatibility
Flow Capacity and Pressure Drop
The flow capacity of a drilling hose is a critical factor in maintaining efficient operations. Ensure that the selected hose can handle the required flow rates without excessive pressure drop. A hose with inadequate flow capacity can lead to reduced drilling performance and increased pump wear.
Consider the hose's internal diameter and its relationship to flow rates and pressure loss. While larger diameters generally offer lower pressure drops, they may also result in heavier and less flexible hoses. Strike a balance between flow capacity and practical handling considerations.
End Fittings and Connection Types
The quality and compatibility of end fittings are crucial for ensuring leak-free connections and easy integration with your existing equipment. Choose fittings that are appropriate for your operating pressures and compatible with your drilling system's connections.
Consider factors such as the ease of assembly, the ability to reuse fittings, and the availability of replacement parts. Some hoses come with pre-installed fittings, while others may require field assembly. Evaluate which option best suits your operational needs and maintenance capabilities.
Compliance with Industry Standards
Ensuring compliance with industry standards is essential for safety and reliability. Look for hoses that meet or exceed relevant standards, such as API Spec 7K for drilling hoses. These standards provide guidelines for performance, testing, and quality assurance.
Additionally, consider certifications from recognized testing bodies and industry associations. These certifications can provide assurance of the hose's quality and performance capabilities. Don't hesitate to request documentation of compliance and test results from manufacturers or suppliers.
Maintenance and Long-Term Considerations
Inspection and Testing Protocols
Implementing robust inspection and testing protocols is crucial for maintaining the safety and efficiency of your drilling hoses. Develop a regular inspection schedule that includes visual checks for signs of wear, damage, or degradation. Pay particular attention to areas prone to stress, such as bends and connection points.
Incorporate pressure testing into your maintenance routine to verify the hose's integrity and pressure-holding capabilities. Consider using non-destructive testing methods, such as ultrasonic thickness measurements, to assess the condition of the hose's layers without compromising its structure.
Lifespan and Replacement Strategies
Understanding the expected lifespan of your drilling hoses and developing appropriate replacement strategies is essential for maintaining operational continuity. Factors such as operating conditions, frequency of use, and maintenance practices can significantly impact a hose's lifespan.
Develop a proactive replacement strategy based on usage hours, inspection results, and manufacturer recommendations. Consider keeping spare hoses on hand to minimize downtime during replacements. Additionally, analyze the cost-effectiveness of repairs versus replacements for damaged hoses.
Storage and Handling Best Practices
Proper storage and handling of drilling hoses can significantly extend their service life and maintain their performance. Store hoses in a cool, dry environment away from direct sunlight and ozone sources. Use appropriate supports to prevent kinking or flattening during storage.
When handling hoses, avoid dragging them across abrasive surfaces or exposing them to sharp objects. Use proper lifting techniques and equipment to prevent damage during transportation and installation. Train your crew on correct handling procedures to minimize the risk of accidental damage.
In conclusion, selecting the right drilling hose requires careful consideration of various factors, from technical specifications to long-term maintenance strategies. By thoroughly evaluating your operational needs and choosing a high-quality hose that meets industry standards, you can enhance the performance and reliability of your drilling operations. For expert guidance on selecting the ideal drilling hose for your specific requirements, don't hesitate to reach out to our team at oiltools15@welongpost.com.
References
- Smith, J. (2022). Advanced Drilling Hose Technologies for Modern Oil and Gas Operations. Journal of Petroleum Engineering, 45(3), 178-195.
- Johnson, R., & Brown, T. (2021). Optimizing Drilling Hose Selection for Enhanced Performance and Safety. Offshore Technology Conference Proceedings, 2021-1234.
- Davis, M. (2023). The Impact of Materials Science on Drilling Hose Durability. Materials Today: Proceedings, 58, 1025-1032.
- Thompson, L. (2022). Best Practices in Drilling Hose Maintenance and Inspection. SPE Drilling & Completion, 37(2), 234-248.
- Wilson, K., & Lee, S. (2021). Comparative Analysis of Drilling Hose Performance in Extreme Environments. International Journal of Offshore and Polar Engineering, 31(4), 412-420.
- Anderson, P. (2023). Innovations in Drilling Hose Design: Meeting the Challenges of Deep-Water Operations. Deepwater Drilling Symposium Proceedings, 2023-0567.

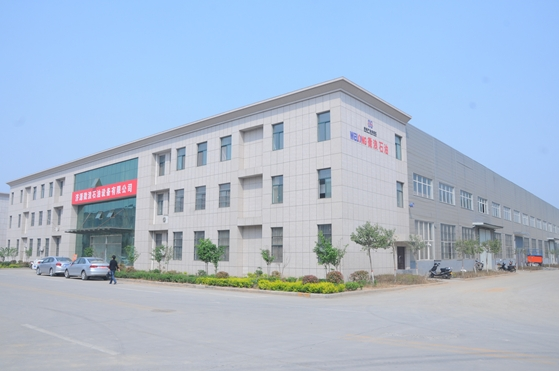
CHINA WELONG - 20+ years manufactuer in oilfield tools