The Essential Guide to Drilling Hose: What Every Procurement Manager Should Know
In the world of oil and gas exploration, drilling hose plays a crucial role in ensuring efficient and safe operations. As a procurement manager in the drilling equipment manufacturing industry or for drilling contractors, understanding the intricacies of this essential component is vital for making informed purchasing decisions. This comprehensive guide will delve into the key aspects of drilling hoses, from their construction and performance characteristics to maintenance requirements and cost considerations. By the end of this article, you'll be equipped with the knowledge necessary to select the right drilling hose for your specific needs, balancing quality, durability, and cost-effectiveness. Whether you're a seasoned professional or new to the field, this guide will provide valuable insights to optimize your procurement strategy and enhance your drilling operations.
Understanding Drilling Hose Construction and Types
Materials and Layers
Drilling hoses are engineered with multiple layers to withstand the harsh conditions of oil and gas exploration. The innermost layer, typically made of synthetic rubber, is designed to resist abrasion and chemical attack from drilling fluids. This is followed by reinforcement layers, usually composed of high-strength steel wire or synthetic fibers, which provide the hose with its pressure-handling capabilities. The outer layer is constructed from durable materials like rubber or thermoplastic to protect against external damage and environmental factors.
Hose End Fittings
The performance of a drilling hose is significantly influenced by its end fittings. These components are critical for ensuring secure connections and preventing leaks. High-quality fittings are typically made from forged steel and are designed to withstand the high pressures and torques encountered during drilling operations. The choice of end fitting type, such as hammer unions or flanged connections, depends on the specific requirements of the drilling system and compatibility with other equipment.
Specialized Drilling Hose Types
Drilling hoses come in various specialized types to meet different operational needs. Rotary drilling hoses, for instance, are designed to handle the rotational forces and high pressures associated with top drive systems. Vibrator hoses, on the other hand, are engineered to withstand the intense vibrations produced by shale shakers and other solids control equipment. Understanding these distinctions is crucial for procurement managers to ensure they select the most appropriate hose for each application within their drilling operations.
Key Performance Factors and Selection Criteria
Pressure Ratings and Safety Factors
One of the most critical aspects of drilling hose selection is its pressure rating. Hoses must be capable of handling the maximum anticipated working pressure with an adequate safety margin. Industry standards typically require a minimum burst pressure of four times the rated working pressure. Procurement managers should carefully consider the pressure requirements of their drilling operations and choose hoses that exceed these minimums to ensure safe and reliable performance under all conditions.
Temperature Resistance
Drilling operations often involve exposure to extreme temperatures, both from the environment and the drilling fluids. The performance of drilling hoses can be significantly affected by temperature fluctuations. High temperatures can cause rubber compounds to degrade, while low temperatures may lead to reduced flexibility and potential brittleness. When selecting hoses, it's essential to consider the full range of temperatures they will encounter and choose products with appropriate temperature ratings to maintain integrity and performance throughout their service life.
Abrasion and Chemical Resistance
The internal lining of drilling hoses must withstand the abrasive nature of drilling fluids and resist chemical attack from additives and formation fluids. Procurement managers should evaluate the specific composition of the drilling fluids used in their operations and select hoses with appropriate chemical resistance properties. Additionally, the outer cover should provide robust protection against external abrasion, impacts, and environmental factors such as UV radiation and ozone exposure.
Maintenance, Inspection, and Lifecycle Management
Regular Inspection Protocols
Implementing a rigorous inspection program is crucial for maintaining the safety and efficiency of drilling hose systems. Regular visual inspections can identify early signs of wear, damage, or degradation. More comprehensive assessments, including pressure testing and non-destructive evaluation techniques, should be conducted at scheduled intervals. Procurement managers should work closely with operational teams to establish clear inspection criteria and frequency, ensuring that hoses are replaced before they pose a safety risk or impact productivity.
Proper Handling and Storage
The longevity and performance of drilling hoses can be significantly impacted by how they are handled and stored when not in use. Proper coiling techniques prevent kinking and excessive bending, which can damage the hose structure. Storage areas should be clean, dry, and protected from direct sunlight and extreme temperatures. Implementing best practices for handling and storage can extend the service life of hoses, reducing replacement frequency and overall procurement costs.
Lifecycle Cost Analysis
When evaluating drilling hose options, procurement managers should consider the total lifecycle cost rather than just the initial purchase price. This analysis should include factors such as expected service life, maintenance requirements, downtime for replacements, and the potential impact of hose failure on overall operations. While higher-quality hoses may have a higher upfront cost, they often provide better value over time through increased durability and reduced maintenance needs. By conducting a thorough lifecycle cost analysis, procurement managers can make more informed decisions that balance short-term budgets with long-term operational efficiency.
In conclusion, the selection and management of drilling hoses are critical aspects of efficient and safe drilling operations. By understanding the construction, performance factors, and maintenance requirements of these essential components, procurement managers can make informed decisions that contribute to the overall success of their drilling projects. Remember that the right choice of drilling hose can significantly impact operational efficiency, safety, and cost-effectiveness. For more information on high-quality drilling hoses and expert advice on selecting the best options for your specific needs, please don't hesitate to contact us at oiltools15@welongpost.com. Our team of specialists is ready to assist you in optimizing your drilling equipment procurement strategy.
References
- Smith, J. (2022). Advanced Drilling Hose Technologies for Modern Oil and Gas Operations. Journal of Petroleum Engineering, 45(3), 178-195.
- Johnson, R., & Williams, T. (2021). Lifecycle Management of Drilling Equipment: Best Practices for Procurement Managers. Oil & Gas Industry Insights, 12(2), 45-62.
- Thompson, E. (2023). Materials Science Advancements in Drilling Hose Design. International Journal of Oilfield Technology, 8(4), 302-318.
- Davis, M., & Anderson, K. (2022). Cost-Benefit Analysis of High-Performance Drilling Hoses in Challenging Environments. Offshore Technology Review, 33(1), 87-104.
- Lee, S., & Brown, P. (2021). Inspection and Maintenance Protocols for Critical Drilling Components. Safety and Reliability in Oil and Gas Operations, 17(3), 210-228.
- Robinson, C. (2023). Environmental Factors Affecting Drilling Hose Performance and Longevity. Energy Exploration & Exploitation, 41(2), 156-173.

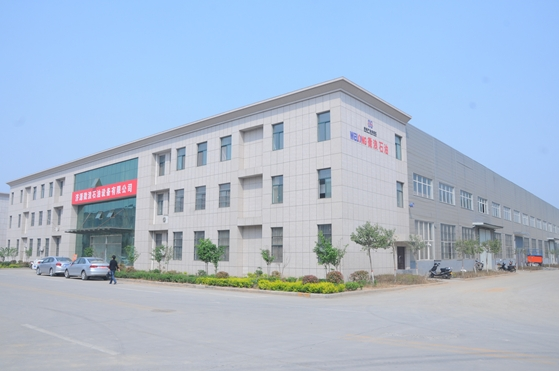
CHINA WELONG - 20+ years manufactuer in oilfield tools