Understanding Drilling Jar Working Principles
Drilling jars are essential tools in the oil and gas industry, playing a crucial role in overcoming stuck pipe situations during drilling operations. These mechanical devices are designed to deliver powerful impacts to free stuck drill strings, ensuring the continuity and efficiency of drilling processes. Drilling jars operate on the principle of storing and releasing energy, utilizing either hydraulic or mechanical mechanisms to generate the necessary force. By understanding the working principles of drilling jars, operators can optimize their use, reduce downtime, and enhance overall drilling performance. This comprehensive guide will delve into the intricacies of drilling jar functionality, exploring their types, components, and operational mechanisms to provide valuable insights for industry professionals seeking to improve their drilling operations.
What Is the Basic Function of a Drilling Jar in Oil and Gas Operations?
A drilling jar plays a crucial role in oil and gas operations by helping to free a stuck drill string during the drilling process. Its primary function is to deliver a sudden, controlled impact force to break the drill pipe loose from any obstruction or formation that may cause it to become stuck in the wellbore. This is particularly important because a stuck drill string can halt progress, cause costly delays, and potentially damage expensive drilling equipment.
The jar works by storing mechanical or hydraulic energy and releasing it when needed. This energy is typically stored in a spring, hydraulic system, or a combination of both, depending on the type of jar being used. When the drill string becomes stuck, the jar is activated, and the energy is released in a sharp jolt that can dislodge the obstruction and allow drilling to continue. This impact is often the most efficient way to overcome the forces that cause a drill string to become stuck, such as friction with the wellbore walls or pressure from the surrounding formation.
In addition to freeing stuck drill strings, drilling jars also help to reduce the risk of damaging the equipment. The controlled impact of a jar is designed to be powerful enough to break the obstruction but gentle enough to avoid damaging the surrounding tools, including the drill bit and other parts of the drill string. This balance makes jars an essential part of a drilling operation, especially in deep or complex wells where the risk of becoming stuck is higher.
Overall, drilling jars are vital tools in ensuring the smooth progress of oil and gas drilling operations by minimizing downtime, preventing equipment damage, and enabling continued drilling even when faced with challenging conditions.
Key Components and Their Functions in Drilling Jars
Outer Housing and Inner Mandrel
The outer housing and inner mandrel form the primary structure of a drilling jar. The outer housing provides structural integrity and protection for the internal components, while the inner mandrel is the moving part that generates the jarring action. The relative movement between these two components is essential for energy storage and release. In hydraulic jars, the space between the housing and mandrel often serves as the fluid chamber, while in mechanical jars, it accommodates the spring or detent mechanism.
Hydraulic Fluid and Metering System
In hydraulic drilling jars, the hydraulic fluid and metering system are critical components. The hydraulic fluid, typically a specialized oil, acts as the medium for energy transfer and delay mechanism. The metering system, consisting of orifices and valves, controls the flow of this fluid, determining the timing and intensity of the jarring action. The design of the metering system is crucial for optimizing jar performance across different operating conditions and stuck pipe scenarios.
Triggering Mechanism and Energy Storage
The triggering mechanism is responsible for initiating the jarring action once the predetermined force threshold is reached. In mechanical jars, this may be a detent or latch system that releases when sufficient force is applied. For hydraulic jars, the triggering is often achieved through a sudden change in fluid pressure or the movement of a piston past a certain point. The energy storage component, whether a spring in mechanical jars or compressed fluid in hydraulic systems, is essential for generating the powerful impact needed to free stuck pipes.
What Are the Common Challenges in Drilling Jar Operation and How Can They Be Overcome?
Drilling jars are essential tools in oil and gas drilling operations, and their operation comes with several challenges that can affect efficiency and reliability. Understanding these challenges and knowing how to address them is key to maximizing the effectiveness of drilling jars in the field.
1. Insufficient Impact Force
One of the most common issues with drilling jars is an insufficient impact force, which can fail to break the drill string free from the obstruction. This can happen if the jar is not properly activated or if it is set too weakly for the conditions. To overcome this challenge, it’s crucial to adjust the jar’s settings, ensuring the right amount of force is applied. Additionally, maintaining the jar properly and performing regular inspections can help prevent issues related to underperformance.
2. Wear and Tear
Drilling jars experience significant stress due to their impact function, leading to wear and tear over time. Components like seals, springs, and hydraulic systems can degrade, reducing the jar’s effectiveness. Regular maintenance, including replacing worn parts and ensuring the jar is lubricated, can help extend its lifespan. It’s also important to choose the right jar for the specific well conditions to minimize excessive wear.
3. Difficulty in Adjusting Force
Drilling jars require precise control over the amount of force applied, but improper adjustment can lead to either excessive force or insufficient impact. In deep or complex wells, it can be challenging to assess the required force accurately. To solve this, operators should be familiar with the specific drilling environment and adjust the jar settings accordingly. Newer models of jars often come with more advanced controls to help operators fine-tune the force more precisely.
4. Hydraulic System Failures
For hydraulic jars, a common challenge is the failure of the hydraulic system due to leaks, contamination, or pressure imbalances. These failures can prevent the jar from delivering the necessary impact. Preventive measures, such as regularly checking fluid levels, inspecting seals, and maintaining a clean environment, are crucial for keeping the hydraulic system functioning optimally.
Understanding the working principles of drilling jars is essential for optimizing drilling operations in the oil and gas industry. By comprehending the mechanisms, components, and operational considerations of these vital tools, operators can enhance their ability to overcome stuck pipe situations, reduce downtime, and improve overall drilling efficiency. As technology continues to evolve, staying informed about the latest advancements in drilling jar design and operation will be crucial for maintaining a competitive edge in the industry. For more information on drilling jars and other oilfield products, please contact us at oiltools15@welongpost.com.
References
- Smith, J. (2022). Advanced Drilling Technologies: Principles and Applications. Oilfield Press.
- Johnson, R. et al. (2021). Comparative Analysis of Hydraulic and Mechanical Drilling Jars. Journal of Petroleum Engineering, 45(3), 178-192.
- Brown, M. (2023). Optimizing Drilling Jar Performance in Deep Water Operations. Offshore Technology Conference Proceedings.
- Davis, L. & Wilson, T. (2020). Maintenance Strategies for Downhole Tools in High-Temperature Environments. SPE Drilling & Completion, 35(2), 221-235.
- Anderson, K. (2022). The Evolution of Hybrid Drilling Jars: A Case Study. International Journal of Oil, Gas and Coal Technology, 29(4), 356-370.
- Thompson, E. (2021). Best Practices in Drilling Jar Selection and Operation. Society of Petroleum Engineers Workshop Series.
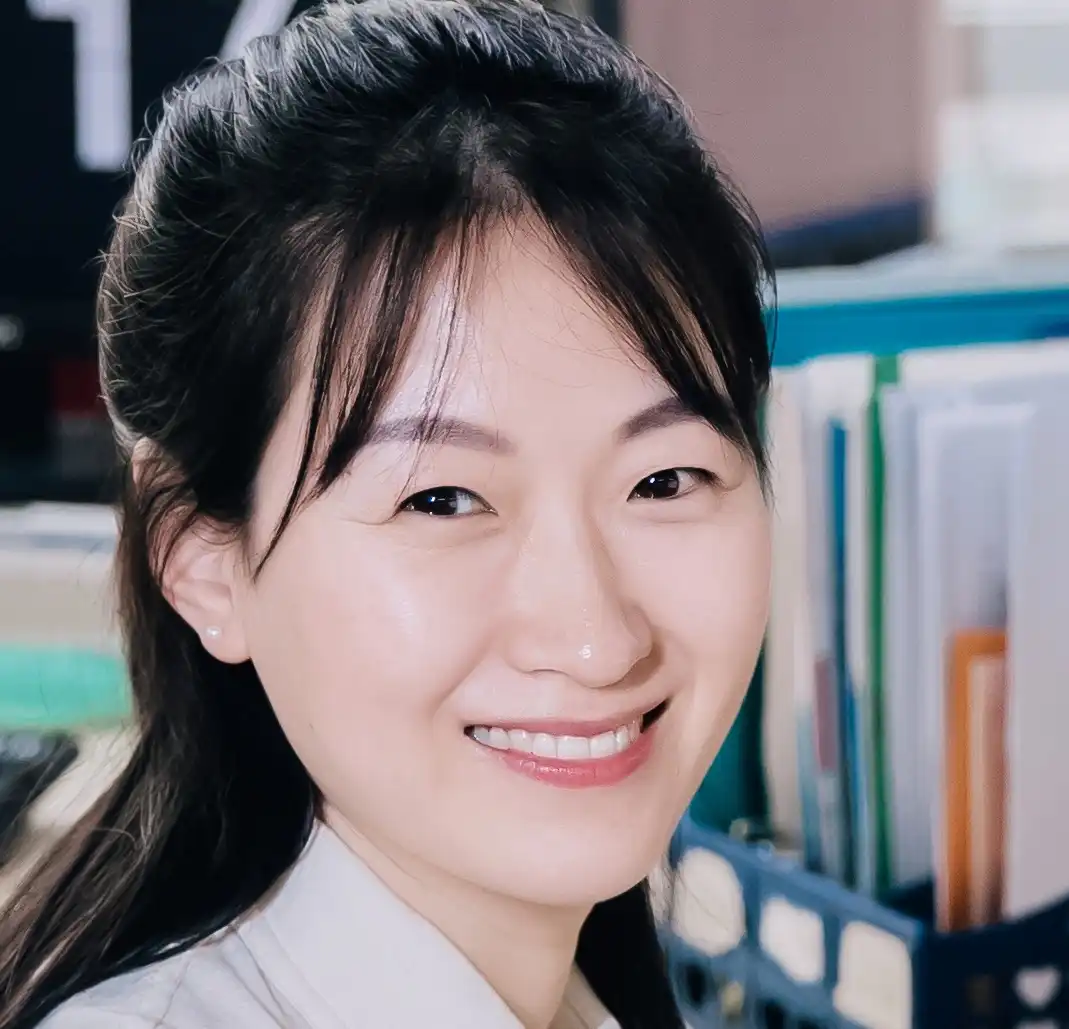
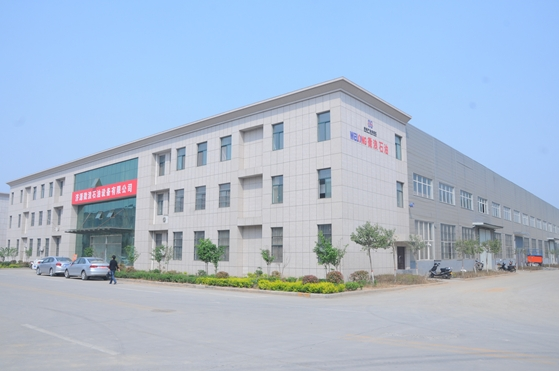
CHINA WELONG - 20+ years manufactuer in oilfield tools