What are the advantages of Float Shoe?
A float shoe is an essential tool in the oil and gas industry, especially during cementing operations. Designed to fit at the bottom of a casing string, it plays a crucial role in ensuring the success and efficiency of well construction. The primary advantage of using a float shoe lies in its ability to prevent fluid backflow, control well pressure, and reduce the risk of wellbore collapse. Its design allows for smooth cement placement, ensuring that the casing stays in place and the well integrity is maintained.
In addition to its primary function of preventing backflow, a float shoe provides several operational benefits. It helps control the pressure during the drilling process, which is critical for preventing damage to the wellbore. It also supports proper well construction by enabling efficient cementing, which is a vital step in ensuring a safe and long-lasting well.
With its reliable performance and cost-effective advantages, the float shoe remains a must-have for professionals in the drilling industry. Let’s dive deeper into its key benefits and explore why it’s essential for any well construction project.
How Does a Float Shoe Prevent Fluid Backflow?
Preventing Fluid Backflow
The float shoe is specifically engineered to address the critical issue of fluid backflow, a potential disruption during drilling operations. When casing is being set in the wellbore, there is a substantial risk that the fluids inside the well could flow upward through the casing, creating several complications. This backflow can not only contaminate the well environment but also interfere with other essential processes, such as cementing and well control. The float shoe addresses this challenge by incorporating a one-way valve mechanism. This mechanism allows fluids to flow only in one direction—downward—while effectively preventing any upward fluid migration. This simple yet powerful design ensures that the wellbore remains stable and free from contamination during the drilling process.
Maintaining Well Integrity
One of the most important roles of the float shoe is to maintain the integrity of the wellbore. In the absence of a float shoe, the backflow of drilling fluids could result in contamination of the wellbore and interfere with the cementing operation. During cementing, it is crucial to ensure that the cement stays in place and bonds securely to the casing and the surrounding formation. Any reverse flow of fluids could lead to improper cement placement, potentially causing weak points or voids in the cement column. The float shoe helps maintain the well’s structural integrity by ensuring that the cement remains in the correct position, allowing it to harden effectively and create a stable foundation for the casing. This is especially important in preventing the need for costly and time-consuming remedial cementing jobs in the future.
Preventing Pressure Buildup
Another key advantage of the float shoe is its ability to prevent pressure buildup during the cementing process. As drilling fluids are pumped downward, the one-way valve within the float shoe remains closed, preventing any pressure from escaping back into the wellbore. This containment of pressure is crucial for maintaining control of the well, especially during cementing operations. Without proper pressure management, the well could become unstable, leading to uncontrolled fluid flow, lost circulation, or even a blowout in extreme cases. The float shoe helps manage pressure by providing a controlled environment where fluids can flow only in the intended direction, allowing for safe and efficient cement placement.
What Benefits Does a Float Shoe Provide During Cementing Operations?
Cementing operations are one of the most critical aspects of well construction, as they play a vital role in ensuring the integrity and stability of the well. Proper cementing secures the casing to the wellbore, providing a solid barrier that prevents fluid migration between different formations. It also helps isolate potentially dangerous zones, such as high-pressure pockets or gas-bearing formations. Without a secure cement bond, the well is at risk of leakage, instability, and operational failures. In this regard, the float shoe is a crucial component that contributes to the overall success of cementing operations.
Preventing Cement Backflow
One of the float shoe's primary functions is to prevent cement backflow during the cementing process. When cement is pumped into the well, it is essential that it remains in place, forming a reliable seal between the casing and the surrounding rock formations. If the cement were to flow back up the casing, it could result in incomplete bonding and compromise the well's structural integrity. The float shoe's one-way valve prevents this backward flow of cement, ensuring that the cement stays in place and effectively seals the annular space. This function reduces the chances of cement channeling, a common issue where the cement migrates unevenly or fails to set properly, potentially leading to costly remediation efforts and jeopardizing the well’s future performance.
Controlling Pressure During Cementing
Another significant benefit of the float shoe is its ability to assist in pressure control during cementing operations. During this critical phase, the well is subjected to various pressures due to the weight of the cement and the downhole conditions. The float shoe features a valve that controls the release of pressure, preventing excessive pressure buildup inside the wellbore. If pressure is not properly managed, it could lead to dangerous situations such as a blowout, a severe loss of circulation, or other operational failures. This function of the float shoe becomes especially important in wells with high-pressure zones or deep-water drilling, where the consequences of uncontrolled pressure are much more severe. By managing pressure in a controlled and safe manner, the float shoe helps ensure that the cement is placed effectively and that the wellbore remains stable.
Ensuring Casing Stability
The float shoe also plays a key role in maintaining the overall stability of the casing throughout the cementing process. During the cementing procedure, it is essential that the casing stays in the proper position to guarantee that the cement forms a uniform bond between the casing and the surrounding formation. If the casing were to shift or move during cementing, it could lead to improper cement placement, compromising the well’s stability. The float shoe helps maintain the casing’s position by acting as a stabilizing force, ensuring it remains aligned as the cement is being pumped. This contributes to a stronger, more durable bond between the casing and the surrounding rock formations. The result is a well structure that is more resistant to shifting, pressure changes, and potential leaks, ensuring the long-term integrity and safety of the well.
What Are the Key Advantages of Using a Float Shoe in Drilling?
Enhanced Pressure Control and Wellbore Stability
In drilling operations, maintaining precise pressure control is crucial to ensure the wellbore remains stable and safe throughout the process. The float shoe plays a key role in this by providing an effective barrier that prevents the escape of pressure during cementing. This protection is especially important in high-risk zones, such as areas with unstable formations or high-pressure conditions. If pressure were to escape, it could lead to dangerous situations like wellbore collapse, which would cause delays, safety concerns, and additional costs. By preventing this, the float shoe helps ensure a more stable and controlled environment for drilling, reducing the likelihood of such incidents.
Protection Against Wellbore Damage
The float shoe serves as a safeguard for the wellbore itself, helping to avoid potential damage caused by pressure imbalances. In any drilling operation, the wellbore is subject to various forces, and maintaining stability is essential. Without proper pressure control, wellbore instability can occur, resulting in costly repairs or even a complete shut-down of the drilling process. The float shoe ensures that pressure is contained and wellbore damage is minimized, allowing the drilling team to focus on progressing the operation without unnecessary interruptions. This protection significantly contributes to reducing downtime, ensuring smoother, more efficient operations.
Improved Cement Placement and Bonding
Another critical function of the float shoe is its role in ensuring proper cement placement. Cementing is an essential part of well construction, as it secures the casing in place and provides isolation between different formations. If the cement is improperly placed or displaced, it can result in incomplete bonding and, eventually, leaks or well failure. The float shoe helps to create a controlled environment during cementing, ensuring the cement is placed accurately and consistently. This leads to a more secure and durable casing, reducing the risk of leaks or operational failures during the life of the well. Proper cementing is vital for long-term well integrity, and the float shoe ensures that this process is carried out with precision.
Cost Reduction and Long-Term Savings
While the primary function of the float shoe is to enhance the safety and effectiveness of drilling operations, it also offers significant cost savings. By improving cementing efficiency, preventing backflow, and maintaining wellbore stability, the float shoe reduces the need for costly interventions and repairs. Wellbore damage, pressure imbalances, and poor cement placement are often the root causes of expensive downtime and additional work. By addressing these issues proactively, the float shoe contributes to a more efficient drilling process, leading to reduced overall costs over the lifetime of the well.
How Does a Float Shoe Help Control Pressure in Drilling Wells?
Pressure control is an essential component of safe and successful drilling operations. Without it, drilling projects face significant risks, ranging from equipment damage to catastrophic well failures. One of the primary tools used in pressure control is the float shoe, which plays a pivotal role in ensuring that pressure is maintained throughout both the cementing and drilling processes.
How the Float Shoe Maintains Pressure Control
The float shoe is equipped with a valve mechanism that allows it to control the flow of fluids during drilling and cementing. This valve prevents the pressure inside the wellbore from escaping, which could otherwise lead to instability. If pressure were to escape, it could result in a blowout, a dangerous event that could cause severe damage to the well, equipment, and the surrounding environment. The float shoe ensures that pressure is kept contained within the wellbore, preventing these disastrous consequences and maintaining a stable environment for drilling.
The Float Shoe’s Role During Cementing
The cementing process is one of the most critical stages in well construction. During this process, cement is pumped into the annular space between the casing and the wellbore to create a strong seal. However, this process must be carefully managed to avoid any backflow or sudden pressure fluctuations. The float shoe plays a key role here by preventing the fluid from flowing backward, which could cause pressure surges and interfere with the cementing operation. By maintaining constant pressure and preventing backflow, the float shoe helps ensure that the cement is placed accurately and effectively, allowing for a secure casing and proper well isolation.
Resilience in High-Pressure Environments
Float shoes are designed to withstand extreme conditions, making them particularly useful in high-pressure zones and deep-water drilling operations. These environments can exert tremendous pressure on wellbore structures, and the float shoe is built to endure these conditions without compromising its ability to maintain pressure. By withstanding these high-pressure environments, the float shoe ensures that the well's integrity is preserved during some of the most challenging phases of drilling.
Enhancing Safety and Reducing Risk
By providing reliable pressure control throughout the drilling and cementing operations, the float shoe significantly reduces the risk of well control problems, such as blowouts, lost circulation, or formation damage. These issues can cause delays, additional costs, and most importantly, safety hazards. The float shoe's ability to maintain stable pressure during critical operations enhances the overall safety of the drilling operation, providing operators with confidence that the well is being constructed in a controlled, secure manner.
Why Is a Float Shoe Essential for Efficient Well Construction?
The importance of a float shoe in the efficient construction of a well cannot be emphasized enough. As an integral tool in both the drilling and cementing phases, it performs several critical functions that directly contribute to the overall integrity and success of the well. Without it, the construction process would be significantly more risky and prone to failure.
One of the primary functions of the float shoe is to ensure that cementing operations are carried out correctly. During the cementing process, the goal is to create a strong, durable seal between the casing and the surrounding formation. The float shoe helps achieve this by preventing the displacement of the cement, which could otherwise lead to poor bonding between the casing and the wellbore. Without a float shoe, cement could be displaced from its intended position, leading to incomplete sealing and potential leaks. This would compromise the well’s integrity and could result in costly repairs or even well failure. The float shoe, by ensuring the cement stays in place, plays a key role in the effectiveness of the cementing process and the well’s long-term stability.
Moreover, the float shoe also helps ensure that the casing remains securely positioned throughout the drilling operation. As the well is drilled deeper, the pressure and forces acting on the casing increase. The float shoe acts as a safeguard against casing displacement, which could occur due to shifting pressure or other drilling-related forces. By maintaining the casing’s position, the float shoe helps preserve the integrity of the wellbore, reducing the chances of complications like wellbore collapse or the need for expensive remediation work.
Furthermore, the float shoe’s role extends to overall safety during well construction. By maintaining pressure control and preventing fluid backflow, it minimizes the risks of blowouts and well control issues. This pressure control function is vital, as it ensures that the well remains stable and that no unexpected fluid movement occurs that could lead to hazardous situations. By ensuring the proper placement of cement, stabilizing the casing, and maintaining pressure control, the float shoe significantly reduces the risk of operational failures and safety hazards during the drilling and cementing phases.
In summary, the float shoe is indispensable in well construction, contributing to both the efficiency and safety of the process. Its ability to ensure proper cementing, prevent casing displacement, and maintain pressure control makes it an essential tool for achieving a well that is both secure and cost-effective. By mitigating risks and enhancing the reliability of drilling operations, the float shoe ultimately ensures that well construction is completed successfully and efficiently.
How Does a Float Shoe Reduce the Risk of Wellbore Collapse?
Wellbore collapse is one of the most critical risks in drilling operations, and the float shoe plays a vital role in mitigating this risk. By providing essential pressure control and ensuring proper cement placement, the float shoe helps maintain the structural integrity of the wellbore throughout the drilling and cementing processes.
One of the primary features of the float shoe is its built-in one-way valve, which prevents fluid backflow during cementing. This valve is crucial in maintaining the pressure within the wellbore, ensuring that the well remains stable and that no unwanted fluids can enter or exit the well. Without the float shoe, the wellbore could be exposed to fluctuating pressures, which increases the risk of destabilization and collapse. The float shoe helps to counteract these pressures, preserving the wellbore’s stability and reducing the chances of a collapse occurring.
Additionally, the float shoe is instrumental in ensuring that cement is placed correctly around the casing. This cement forms a vital seal that locks the casing in place, preventing any shifting or displacement that could compromise the well’s structure. A poorly placed casing or improperly bonded cement could lead to casing failure, which is a significant contributor to wellbore collapse. The float shoe helps to prevent such issues by ensuring that the cement stays in place, forming a robust seal that supports the casing throughout the life of the well.
By improving both cement placement and pressure control, the float shoe plays a critical role in preventing wellbore failure. The float shoe is also integral to maintaining safety during drilling operations. It minimizes the risks of catastrophic events, such as blowouts or casing failures, by stabilizing the wellbore and maintaining the proper conditions needed for secure drilling. In doing so, it enhances the overall safety of the operation and helps ensure the long-term success of the well.
Ultimately, the float shoe is essential in preventing wellbore collapse, contributing significantly to the safety, stability, and efficiency of drilling operations.
Conclusion
Float shoes are indispensable tools in drilling operations, offering multiple benefits that help ensure the safety, efficiency, and cost-effectiveness of well construction. From preventing fluid backflow to controlling pressure and enhancing cement placement, the float shoe plays a critical role in maintaining well integrity and preventing costly operational failures. Their ability to improve pressure control, reduce wellbore collapse risks, and streamline cementing operations makes them an essential part of the drilling process.
Choosing the right taper mill is crucial for ensuring optimal performance and efficiency in drilling operations. At Welong, we specialize in providing high-quality taper mills designed for a wide range of applications. Our products are known for their durability, precise performance, and cost-effectiveness. We work closely with our clients to understand their specific needs and offer tailored solutions that meet their operational requirements.
If you're unsure which taper mill is best suited for your application, our team of experts is here to assist you. With our extensive experience in the oil and gas industry, we can help you select the right tools to ensure the success of your drilling projects.
For further inquiries or to learn more about float shoes and other oilfield products, feel free to contact us at oiltools15@welongpost.com.
References
1. Rassenfoss, S. (2019). "Float Shoe Technology: Preventing Backflow and Ensuring Well Integrity." Journal of Petroleum Technology, 71(2), 34-39.
2. Fielder, J., & Zimmerman, R. (2017). "Role of Float Shoes in Drilling Operations: An Overview of Functionality and Safety." Society of Petroleum Engineers (SPE), SPE-186315-MS.
3. Anderson, T. (2015). "The Importance of Float Shoes in Well Construction and Drilling Fluid Management." World Oil, 236(7), 40-42.
4. Thomas, H., & Meyer, K. (2018). "Float Shoes in Deepwater Drilling: Enhancing Well Control and Preventing Backflow." Journal of Energy Resources Technology, 140(10), 102-107.
5. Smith, P., & Lee, D. (2016). "Float Shoe Design and Application: A Key to Successful Drilling." Petroleum Engineering Journal, 29(1), 12-18.
6. Miller, G., & Scott, M. (2020). Backflow Prevention with Float Shoes: Enhancing Safety and Efficiency in Drilling." Oilfield Review, 32(4), 50-56.
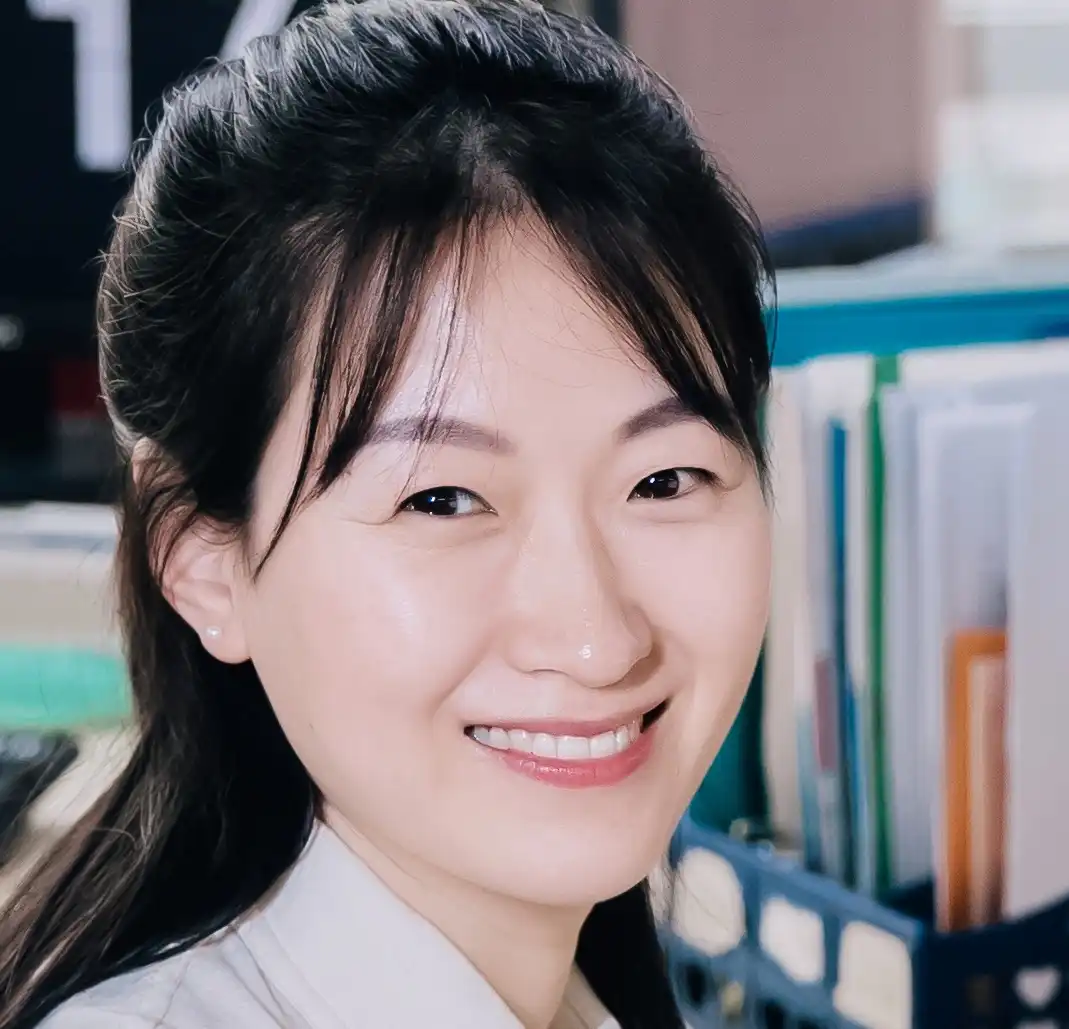
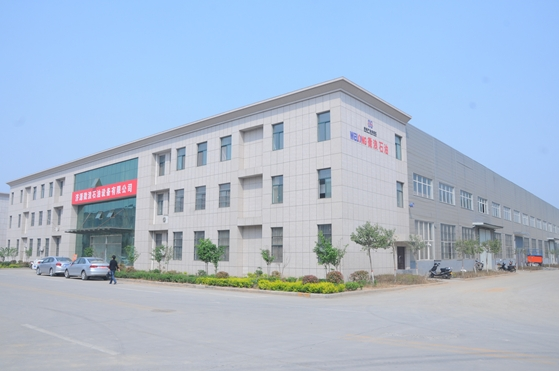
CHINA WELONG - 20+ years manufactuer in oilfield tools