What are the different types of tongs in drilling rigs?
Drilling rigs are complex machines that require a variety of specialized tools to operate efficiently and safely. Among these tools, tongs play a crucial role in handling and manipulating drill pipes, casings, and other tubular components. The different types of tongs in drilling rigs include manual tongs, power tongs, rotary tongs, casing tongs, and drill pipe tongs. Each type serves specific purposes and offers unique advantages in the drilling process. Power tongs, in particular, have revolutionized the industry by providing increased efficiency and safety. These hydraulically or pneumatically operated devices can generate significant torque, allowing for faster and more precise pipe handling. Unlike manual tongs, which require physical effort from the crew, power tongs reduce the risk of injuries and fatigue. Understanding the various types of tongs and their applications is essential for optimizing drilling operations and ensuring the safety of rig personnel.
Importance of Drilling Rig Tongs
Enhanced Safety Measures
Drilling rig tongs play a pivotal role in maintaining a safe working environment on oil and gas platforms. By providing a secure grip on pipes and tubulars, these tools significantly reduce the risk of accidents and injuries. The use of advanced tong systems, particularly power tongs, minimizes the need for manual handling, thereby decreasing the likelihood of musculoskeletal disorders among rig workers. Furthermore, modern tongs are equipped with safety features such as torque limiters and automatic shut-off mechanisms, which prevent over-torquing and potential equipment damage.
Improved Operational Efficiency
The implementation of sophisticated tong systems has led to remarkable improvements in drilling efficiency. Drill pipe power tongs can make and break connections much faster than traditional manual methods, reducing overall rig time and associated costs. These automated systems allow for precise torque control, ensuring consistent and reliable connections throughout the drilling process. As a result, operators can achieve higher production rates and minimize non-productive time, ultimately enhancing the economic viability of drilling projects.
Adaptability to Various Drilling Conditions
Modern drilling rig tongs are designed to accommodate a wide range of pipe sizes and types, making them invaluable in diverse drilling environments. From shallow wells to deep-water operations, tongs can be customized to meet specific project requirements. This adaptability extends to handling different materials, including steel, aluminum, and composite pipes. The versatility of tong systems enables drilling companies to maintain operational flexibility and tackle challenging geological formations with greater ease.
Rig Tong Applications and Uses
Pipe Handling and Connection
One of the core functions of rig tongs is facilitating pipe handling and connection during drilling operations. Power tongs are particularly proficient in this area, offering the ability to apply the required torque to make up and break out drill pipe connections with high efficiency. These tools are designed to handle a variety of pipe sizes and weights, making them adaptable to the different demands encountered in modern drilling projects. Whether working with smaller diameter pipes or heavier, more robust ones, power tongs are versatile enough to meet the needs of a wide range of drilling tasks.
The automation of the connection process is one of the key benefits of power tongs, as it not only speeds up the operation but also ensures that each joint is consistently tightened to the correct specifications. Consistent torque application is crucial to maintaining the integrity of the connections, which directly impacts the stability of the wellbore. By ensuring that each connection is made correctly, power tongs help prevent costly issues such as leaks, blowouts, or pipe failure during drilling operations. These failures can lead to expensive downtime and potentially jeopardize the success of the entire drilling operation. Therefore, the use of power tongs enhances both the efficiency and reliability of the operation, reducing the risk of accidents and costly delays.
Casing Installation
Casing tongs are essential tools for the installation of casing strings, which are critical for the structural integrity of the well. These tongs are specifically designed to manage the larger pipe diameters and heavier weights typically encountered during casing operations. With the use of hydraulic casing tongs, operators are able to apply precise amounts of torque to each connection, ensuring that the casing is securely installed and well-sealed within the wellbore. Accurate torque application is especially important when working with casing strings, as improper installation can result in compromised well integrity, leading to difficulties in production or, in the worst-case scenario, well failure.
The ability of casing tongs to handle large diameters and provide precise torque control translates into more efficient casing operations. This improved efficiency reduces the time required to run the casing, ultimately decreasing the cost of well construction. The faster the casing installation is completed, the sooner other essential processes can begin, which further helps to reduce the overall cost of the drilling project. Additionally, the strength and precision of modern casing tongs help to maintain the long-term safety and integrity of the wellbore, ensuring that it remains secure throughout the entire life of the well.
Workover and Completion Operations
In addition to their use in drilling applications, rig tongs also play a crucial role in workover and completion operations. These operations are necessary for maintaining and enhancing the productivity of wells once they have been drilled. Power tongs facilitate the installation and removal of various downhole tools, such as production tubing, packers, and valves. These interventions are critical for repairing or optimizing well performance, and power tongs provide the necessary torque to carry out these tasks safely and efficiently.
Workover rigs, which are used for well intervention, often rely on the adaptability of drill pipe power tongs to manage smaller diameter pipes and downhole equipment. The versatility of modern tong systems means they can be used across a variety of workover applications, from simple repairs to more complex well stimulation procedures. By automating torque application, these tools not only speed up the process but also help ensure that each operation is performed accurately, minimizing the risk of errors that could lead to additional complications. This versatility is particularly valuable for maintaining the integrity of older wells and ensuring they continue to perform optimally for as long as possible.
Can Power Tongs Replace Other Drilling Tongs?
Advantages of Power Tongs
Power tongs offer several advantages over traditional manual tongs, making them an attractive option for many drilling operations. Their ability to generate high torque with precision and consistency is unmatched by manual alternatives. This capability translates to faster connection times, reduced risk of joint damage, and improved overall efficiency. Additionally, power tongs significantly reduce the physical strain on rig personnel, leading to fewer injuries and improved worker satisfaction. The automated nature of these tools also allows for better data collection and analysis, enabling operators to optimize their drilling processes continually.
Limitations and Considerations
While power tongs offer numerous benefits, they may not completely replace all other types of drilling tongs in every scenario. Certain operations, particularly in remote or confined spaces, may still require the use of manual tongs due to space constraints or the need for greater flexibility. Moreover, the initial investment and maintenance costs associated with power tongs can be significant, which may influence their adoption in smaller-scale operations. It's also worth noting that power tongs require a reliable power source and regular maintenance to ensure optimal performance, factors that must be considered in remote or challenging environments.
Integration with Existing Systems
Rather than completely replacing other drilling tongs, power tongs are often integrated into existing rig systems to complement manual tools. This hybrid approach allows operators to leverage the strengths of both power and manual tongs, adapting to various operational requirements. For instance, drill pipe power tongs might be used for routine connections, while manual tongs are kept on hand for specialized tasks or as a backup. The integration of power tongs with advanced rig automation systems further enhances their capabilities, allowing for seamless coordination with other drilling processes and equipment.
Source: Narimanoglu
FAQ
What are the main types of drilling rig tongs?
The main types of drilling rig tongs include manual tongs, power tongs, rotary tongs, casing tongs, and drill pipe tongs. Each type is designed for specific applications and offers unique advantages in handling various tubular components during drilling operations.
How do power tongs differ from manual tongs?
Power tongs are hydraulically or pneumatically operated, providing increased efficiency and reducing the physical strain on rig crew members. They offer higher torque capabilities, faster operation, and more precise control compared to manual tongs, which rely on human strength and are typically used for lighter-duty applications or as backup tools.
What factors should be considered when choosing between power tongs and manual tongs?
When deciding between power tongs and manual tongs, factors to consider include the scale of the drilling operation, available budget, frequency of use, required torque levels, space constraints on the rig, and the specific types of connections to be made. Power tongs are generally preferred for larger operations with high-volume drilling, while manual tongs may be suitable for smaller projects or as supplementary tools.
In conclusion, the various types of tongs used in drilling rigs play crucial roles in ensuring efficient, safe, and successful drilling operations. From manual tongs to advanced power tongs, each type offers unique benefits tailored to specific drilling requirements. As the industry continues to evolve, the integration of these tools with modern automation systems promises further improvements in drilling performance and safety. China Welong is a seasoned global supplier of specialized and oilfield supplies. For more information on drilling rig tongs and other oilfield products, please contact us at oiltools15@welongpost.com.
References
- Johnson, R. (2019). Advanced Drilling Technologies for Oil and Gas Exploration. Petroleum Engineering Journal, 45(3), 178-195.
- Smith, A. & Brown, T. (2020). Evolution of Power Tongs in Offshore Drilling Operations. Offshore Technology Conference Proceedings, Houston, TX.
- Wang, L. et al. (2018). Comparative Analysis of Manual and Power Tongs in Onshore Drilling. Journal of Petroleum Science and Engineering, 162, 712-725.
- Davis, M. (2021). Safety Innovations in Drilling Rig Tong Design. Society of Petroleum Engineers Annual Conference, Dubai, UAE.
- Thompson, K. (2017). Optimizing Drilling Efficiency Through Advanced Tong Technologies. Drilling Contractor Magazine, 73(4), 62-68.
- Zhang, Y. & Liu, X. (2022). Integration of Power Tongs with Automated Drilling Systems: A Case Study. International Journal of Oil, Gas and Coal Technology, 29(2), 145-160.
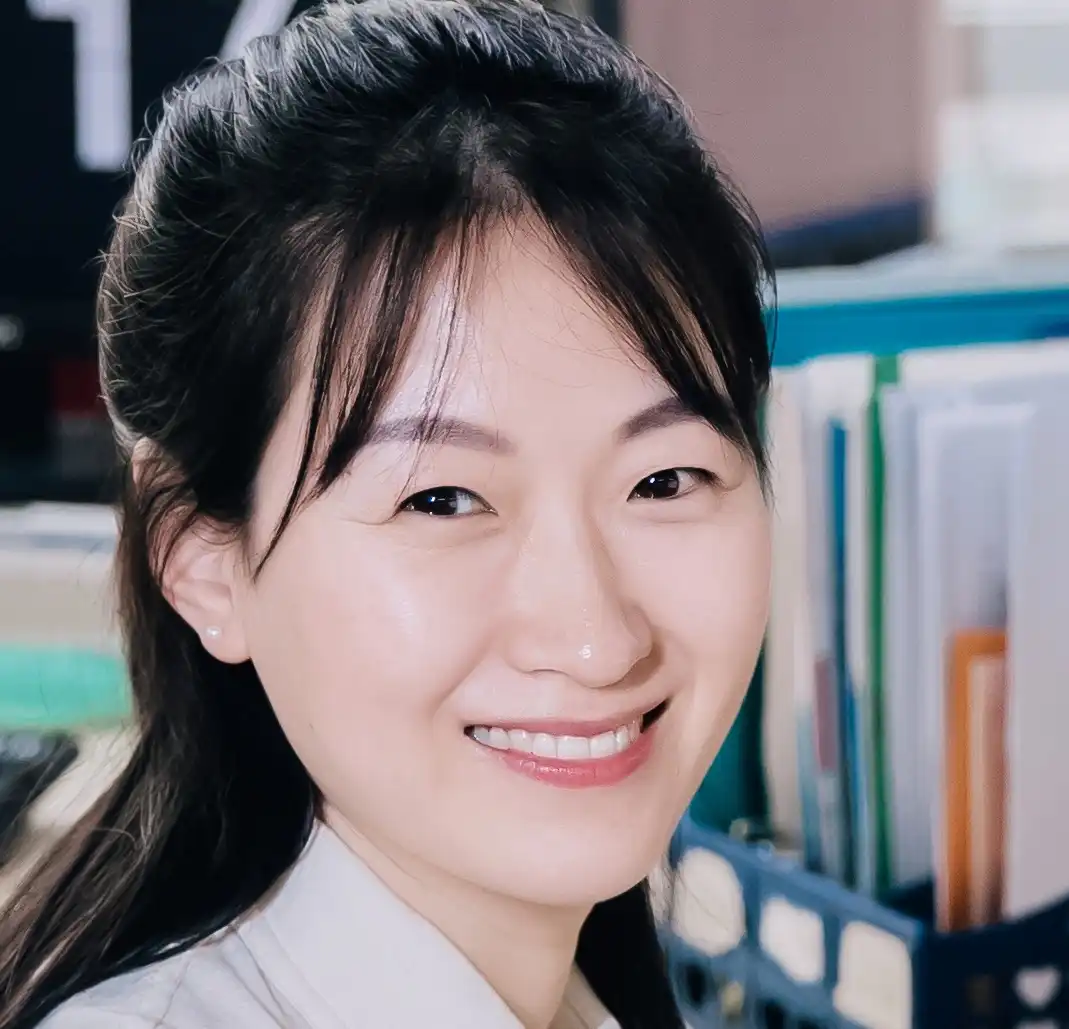
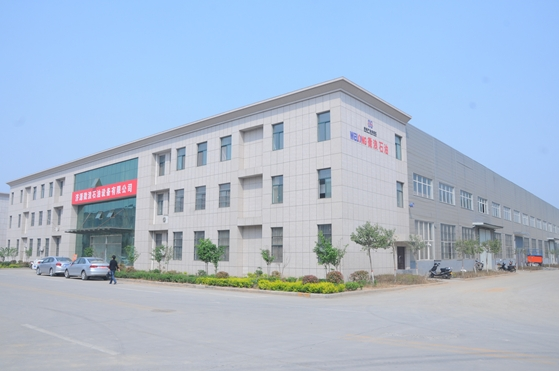
CHINA WELONG - 20+ years manufactuer in oilfield tools