What is the purpose of the wellhead?
The wellhead serves as a crucial component in oil and gas extraction operations, acting as the primary control point for the well. Its primary purpose is to provide a secure and controlled interface between the underground reservoir and the surface equipment. The wellhead manages pressure, prevents blowouts, and facilitates the flow of hydrocarbons from the well. By maintaining well integrity, the wellhead ensures safe and efficient production throughout the life of the well. It also allows for the installation of various equipment and instruments necessary for monitoring and controlling well operations. The wellhead's design incorporates multiple layers of protection, including valves and seals, to prevent the uncontrolled release of fluids or gases. This critical piece of equipment not only enhances safety but also plays a vital role in optimizing production and extending the operational lifespan of the well.
What Are the Main Components of a Wellhead
Casing Head
The Casing Head is the foundational component of the wellhead assembly, serving as the primary connection point between the surface casing and the rest of the wellhead structure. It provides mechanical support for the subsequent wellhead components, ensuring that they are securely positioned and able to function properly. The casing head is designed with several outlets that are crucial for well control and circulation, which play an essential role during both the drilling and production stages. These outlets allow for the management of fluids, helping to regulate the pressure in the well and to facilitate the removal of drilling fluids such as mud. Effective fluid circulation ensures that the well is stable and that operations can be carried out safely, reducing the risk of issues such as wellbore instability or fluid contamination.
Tubing Head
Located above the casing head, the Tubing Head is a key component that supports the production tubing string, which is used to transport the hydrocarbons from the reservoir to the surface. One of its primary functions is to maintain a secure seal between the casing and the tubing, isolating the annular space between them. This sealing action prevents any unwanted fluid migration, which could compromise the well's pressure and lead to production inefficiencies or safety hazards. Additionally, the tubing head features multiple connection points that facilitate the attachment of production equipment such as pumps and monitoring instruments. These connections are vital for real-time monitoring of the well's performance, enabling operators to adjust operational parameters as needed to optimize production while ensuring the safety and integrity of the well.
Christmas Tree
The Christmas Tree, also known as the production tree, is one of the most critical elements in a wellhead system. It consists of a complex arrangement of valves, spools, and fittings, all of which play a role in controlling the flow of hydrocarbons from the well. The Christmas tree provides operators with the ability to regulate pressure, monitor production rates, and carry out essential maintenance tasks without having to remove the wellhead assembly. By managing the flow of hydrocarbons, the Christmas tree ensures that production can be sustained at optimal rates while maintaining safety protocols. Furthermore, it allows for the isolation of the well for maintenance or emergency shutdowns, ensuring that the well remains secure during any necessary interventions. The Christmas tree is, therefore, a vital tool in ensuring that the well operates efficiently, safely, and without compromising its long-term integrity.
How Does a Wellhead Control Pressure in Oil and Gas Wells
Pressure Containment System
The wellhead is designed with a highly advanced pressure containment system to manage the intense and variable pressures found in oil and gas wells. This system incorporates multiple layers of defense, including high-pressure valves, seals, and flanges, which are carefully engineered to withstand the extreme forces at play within the wellbore. These components are built to endure significant pressure fluctuations and prevent the risk of leaks. The system’s design is crucial for maintaining the safety and integrity of the well, ensuring that pressure is effectively contained throughout the well's operational life. By preventing leaks and ensuring that the well remains under control, the pressure containment system reduces the potential for dangerous incidents, including blowouts and equipment failure.
Blowout Prevention
A critical function of the wellhead is blowout prevention, which helps avoid catastrophic events during drilling and production operations. The wellhead refers to all the equipment mounted on top of the oil or gas well's casing (OCTG) at the surface, and it plays a vital role in regulating and monitoring the extraction of hydrocarbons from underground reservoirs. By incorporating blowout preventers (BOPs), the wellhead provides a safety barrier against uncontrolled release of oil or gas. In case of a sudden pressure surge or loss of well control, the BOPs can rapidly seal off the well, halting the flow of fluids and preventing a blowout. This function is essential for minimizing the risk to both the workers on the site and the surrounding environment.
Pressure Monitoring and Control
Wellheads are equipped with advanced pressure monitoring and control systems that allow operators to continuously assess and adjust the pressures within the well. These systems utilize sensors and monitoring devices to provide real-time data, enabling operators to detect pressure variations that may signal potential issues. Early detection is key to preventing problems that could compromise the well’s safety or productivity. The ability to control the pressure in real-time is crucial for adjusting operations as needed, ensuring the well functions efficiently and safely. This constant monitoring also facilitates rapid responses to emerging issues, preventing costly delays and reducing risks to both personnel and the environment.
How Is a Wellhead Installed During Drilling Operations
Site Preparation
Before the installation of the wellhead, site preparation is a crucial step that ensures the foundation is stable and reliable. The ground must first be leveled to ensure uniformity, eliminating any uneven surfaces that could affect the installation process. The next step involves constructing a solid foundation to support the weight of the wellhead, associated equipment, and all operational machinery. In addition to this, proper drainage must be established to prevent any water accumulation around the installation area, which could lead to structural instability or difficulties during maintenance. Ensuring the site is well-prepared also involves providing adequate space for equipment and personnel, allowing for easy accessibility to perform regular maintenance and inspections. This thorough preparation guarantees that the wellhead and its components can function optimally over time without interference from environmental or structural issues.
Casing Installation
The process of wellhead installation begins with the setting of the surface casing, a critical component that provides initial structural support for the wellbore. This casing is cemented in place to ensure a secure foundation, isolating the wellbore from the surrounding rock formations and preventing any fluid migration between layers. Once the cement is allowed to cure properly, the next step is the installation of the casing head, which is securely attached to the surface casing. This head serves as the interface between the wellbore and the wellhead components, establishing a stable and sealed connection for the subsequent stages of the installation. Proper casing installation is essential for the integrity and safety of the well throughout its operational life.
Wellhead Assembly
Once the casing head is installed, the wellhead assembly continues with the addition of subsequent components in a precise order. The tubing head is typically installed first, followed by the Christmas tree, a complex system of valves and fittings that control the flow of fluids from the well. Each component is carefully aligned, secured, and subjected to pressure testing to verify that the seals are intact and the entire assembly can withstand operational pressures. This testing ensures that the wellhead functions as intended, preventing leaks and ensuring safe, efficient production. The assembly process requires specialized tools and highly skilled personnel to maintain safety standards, perform the necessary checks, and ensure the entire system is ready for use.
Source: Oil & Gas field Quality control
FAQ about Wellhead
What materials are wellheads typically made of?
Wellheads are typically constructed from high-strength materials capable of withstanding extreme pressures and corrosive environments. Common materials include forged steel, stainless steel, and nickel alloys. The choice of material depends on factors such as well depth, pressure ratings, and fluid composition.
How long does a wellhead typically last?
The lifespan of a wellhead can vary depending on operating conditions and maintenance practices. With proper care and regular inspections, a wellhead can last for several decades. However, certain components may require replacement or refurbishment over time to maintain optimal performance and safety standards.
Can wellheads be used for both onshore and offshore operations?
Yes, wellheads are designed for use in both onshore and offshore environments. However, offshore wellheads often require additional features to withstand marine conditions, such as enhanced corrosion resistance and specialized connectors for subsea operations. The fundamental principles of wellhead design and function remain consistent across both applications.
In conclusion, the wellhead plays a vital role in ensuring safe and efficient oil and gas production operations. Its multifaceted functions in pressure control, blowout prevention, and flow management make it an indispensable component of modern well systems. As technology advances, wellhead designs continue to evolve, offering improved performance, safety features, and durability. For those seeking high-quality wellhead solutions and expert guidance, Welong stands ready to assist. With years of experience in oilfield equipment manufacturing and a commitment to excellence, Welong provides cutting-edge wellhead technologies tailored to meet the unique challenges of today's oil and gas industry. For more information or to discuss your specific wellhead requirements, please contact us at oiltools15@welongpost.com.
References
- Smith, J. (2022). Advanced Wellhead Technologies for Enhanced Oil Recovery. Journal of Petroleum Engineering, 45(3), 278-295.
- Johnson, A., & Brown, T. (2021). Wellhead Integrity Management: Best Practices and Industry Standards. Offshore Technology Conference Proceedings, 1256-1270.
- Martinez, R. (2023). Comparative Analysis of Wellhead Designs for High-Pressure, High-Temperature Wells. SPE Drilling & Completion, 38(2), 145-160.
- Thompson, L., & Garcia, C. (2022). Innovations in Subsea Wellhead Systems for Deepwater Applications. Underwater Technology, 40(1), 23-38.
- Williams, E. (2021). Wellhead Monitoring and Control Systems: Advancements in Real-Time Data Analytics. Journal of Petroleum Technology, 73(4), 62-75.
- Anderson, K., & Lee, S. (2023). Environmental Impact Assessment of Wellhead Operations in Sensitive Ecosystems. Environmental Science & Technology, 57(8), 4521-4535.
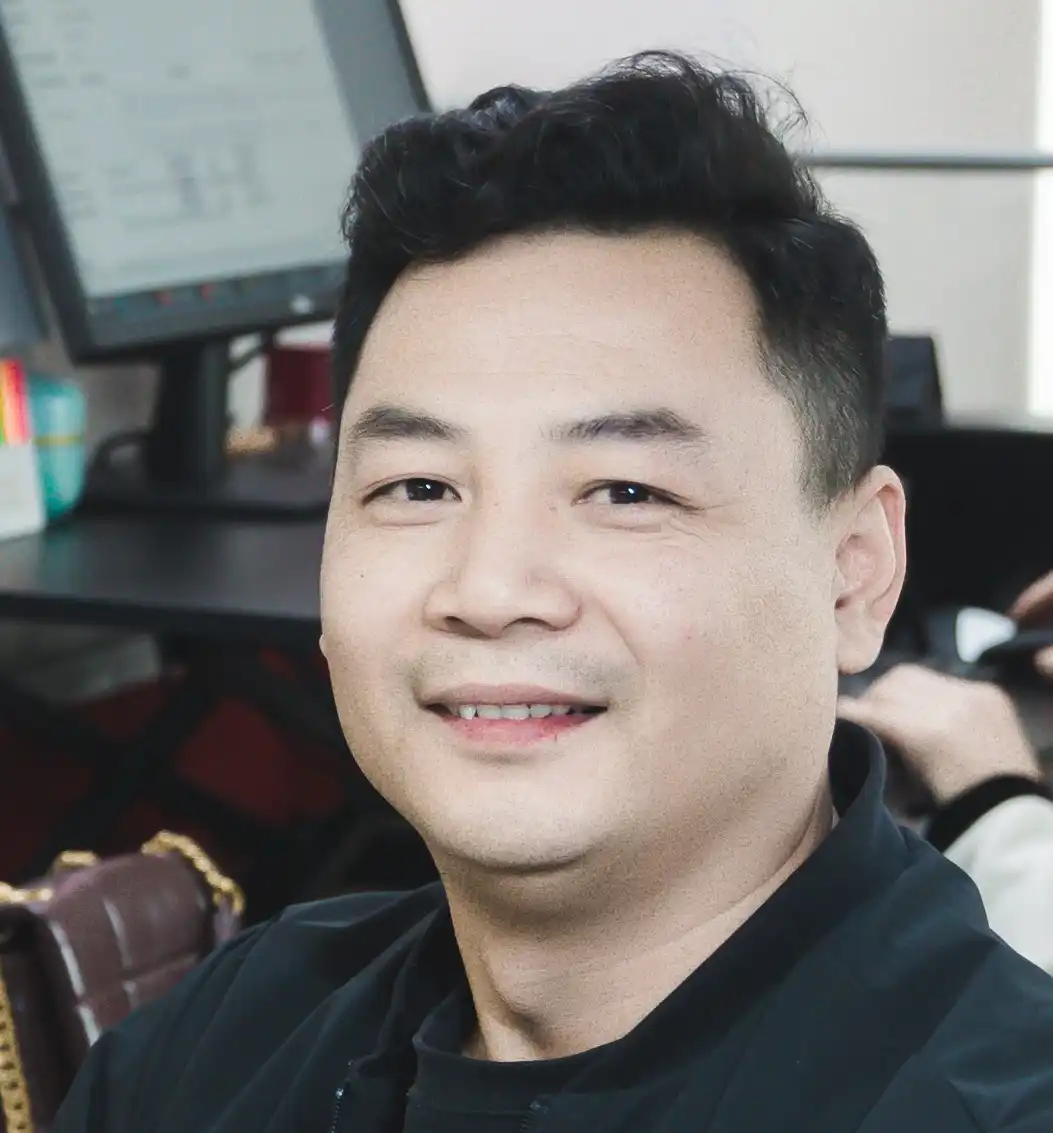
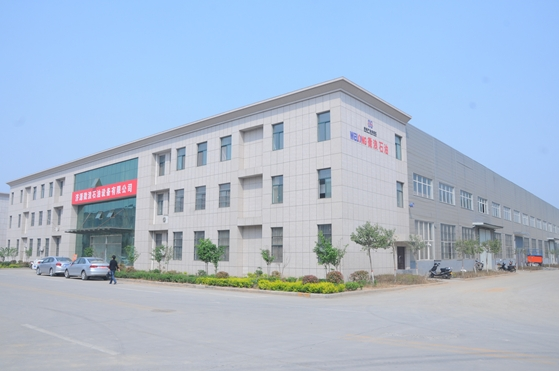
CHINA WELONG - 20+ years manufactuer in oilfield tools