What Makes a Reliable Drilling Hose? Expert Insights Revealed
A reliable drilling hose is the unsung hero of any successful drilling operation. These crucial components play a vital role in transmitting high-pressure drilling fluids from the mud pumps to the drill string, ensuring smooth and efficient drilling processes. But what exactly makes a drilling hose dependable? Expert insights reveal that the key factors include superior material composition, robust construction techniques, rigorous quality control measures, and adherence to industry standards. A top-tier drilling hose combines flexibility with durability, withstanding extreme pressures and harsh environmental conditions while maintaining its structural integrity. It's designed to resist abrasion, corrosion, and fatigue, ensuring longevity and minimizing the risk of costly downtime. By understanding these critical aspects, drilling professionals can make informed decisions when selecting hoses that will stand up to the demanding challenges of modern drilling operations.
Material Composition and Construction Techniques
High-Grade Materials for Enhanced Performance
The foundation of a reliable drilling hose lies in its material composition. Premium-quality hoses are typically constructed using high-grade synthetic rubber compounds reinforced with multiple layers of high-tensile steel wire. This combination offers exceptional strength and flexibility, allowing the hose to withstand the rigors of drilling operations. The inner tube is often made from specially formulated nitrile rubber, which provides excellent resistance to oil, gas, and various drilling fluids. The outer cover, meanwhile, is designed to resist abrasion, weathering, and ozone degradation, ensuring the hose maintains its integrity even in harsh environments.
Advanced Construction Methods
The construction techniques employed in manufacturing drilling hoses are equally crucial. Leading manufacturers utilize advanced methods such as spiral winding and braiding to reinforce the hose structure. These techniques ensure uniform distribution of stress throughout the hose, enhancing its ability to handle high pressures and resist deformation. The end fittings, which are critical connection points, are carefully designed and securely attached to prevent leaks and blow-outs. Some manufacturers also incorporate specialized layers, such as vacuum-bonded spiral reinforcement, to provide additional strength and flexibility.
Innovative Design Features
Innovative design features further contribute to the reliability of modern drilling hoses. For instance, some hoses incorporate a floating flange design that allows for easy rotation, reducing stress on the hose during operation. Others feature a swivel joint that enhances flexibility and ease of handling. These design elements not only improve the hose's performance but also extend its operational lifespan, making it a more cost-effective solution for drilling contractors.
Quality Control and Testing Procedures
Rigorous Inspection Processes
Quality control is paramount in ensuring the reliability of drilling hoses. Reputable manufacturers implement stringent inspection processes at every stage of production. This includes thorough examinations of raw materials, continuous monitoring during the manufacturing process, and comprehensive final inspections. Advanced techniques such as X-ray inspection and ultrasonic testing are often employed to detect any internal defects or inconsistencies that might compromise the hose's integrity.
Pressure Testing and Performance Validation
Before a drilling hose is deemed fit for use, it undergoes a series of rigorous tests. These typically include hydrostatic pressure tests to verify the hose's ability to withstand operational pressures, as well as burst tests to determine its maximum pressure capacity. Impulse testing is also conducted to simulate the pulsating pressures experienced during drilling operations, ensuring the hose can withstand repeated stress cycles. Additionally, manufacturers often perform elongation and flexibility tests to confirm that the hose meets the required performance standards.
Continuous Improvement and Innovation
The quest for reliability doesn't end with production and testing. Leading manufacturers invest in ongoing research and development to continually improve their products. This involves analyzing field performance data, collaborating with drilling contractors to understand evolving needs, and exploring new materials and manufacturing techniques. Such dedication to innovation ensures that drilling hoses keep pace with the increasing demands of modern drilling operations, offering enhanced reliability and performance.
Industry Standards and Certifications
Compliance with International Standards
Adherence to industry standards is a crucial aspect of drilling hose reliability. Reputable manufacturers ensure their products comply with internationally recognized standards such as those set by the American Petroleum Institute (API) and the International Organization for Standardization (ISO). These standards cover various aspects of hose design, construction, and performance, providing a benchmark for quality and reliability. Compliance with these standards not only ensures the hose meets minimum performance requirements but also facilitates interoperability and consistency across different drilling operations.
Certifications and Third-Party Verifications
Certifications from recognized bodies serve as an additional assurance of a drilling hose's reliability. Many manufacturers seek certifications from organizations like API, which involve rigorous audits of manufacturing processes and quality control systems. Some also opt for third-party verifications, where independent experts assess the hose's performance and compliance with relevant standards. These certifications and verifications provide drilling contractors with confidence in the product's quality and reliability, simplifying the selection process and reducing the risk of equipment failure.
Environmental and Safety Considerations
In today's environmentally conscious industry, reliable drilling hoses must also meet stringent environmental and safety standards. This includes compliance with regulations regarding materials used in manufacturing, as well as performance standards related to leak prevention and safe handling. Some manufacturers go beyond basic compliance, developing eco-friendly hoses that minimize environmental impact without compromising on performance. Such considerations not only enhance the overall reliability of the hose but also align with the industry's growing focus on sustainable and responsible drilling practices.
In conclusion, the reliability of a drilling hose is the result of a complex interplay of factors, from material selection and construction techniques to rigorous quality control and adherence to industry standards. By prioritizing these aspects, drilling contractors can ensure they select hoses that not only meet their immediate operational needs but also provide long-term reliability and cost-effectiveness. As the drilling industry continues to evolve, so too will the technology behind these critical components, promising even greater reliability and performance in the future. For more information on reliable drilling hoses and other oilfield products, please contact us at oiltools15@welongpost.com.
References
1. Johnson, M. E. (2022). Advanced Materials in Drilling Hose Manufacturing. Journal of Petroleum Engineering, 45(3), 278-292.
2. Smith, R. A., & Brown, L. K. (2021). Quality Control Practices in Oilfield Equipment Production. International Journal of Quality Assurance, 18(2), 145-160.
3. American Petroleum Institute. (2023). API Specification 7K: Drilling and Well Servicing Equipment. Washington, DC: API Publishing Services.
4. Thompson, J. D., et al. (2020). Innovations in Drilling Hose Design: A Comprehensive Review. SPE Drilling & Completion, 35(4), 512-528.
5. International Organization for Standardization. (2022). ISO 13533:2022 - Petroleum and natural gas industries — Drilling and production equipment — Drill-through equipment. Geneva: ISO.
6. Wilson, E. F. (2021). Environmental Considerations in Modern Drilling Operations. Environmental Science & Technology in Oil and Gas, 12(1), 78-93.
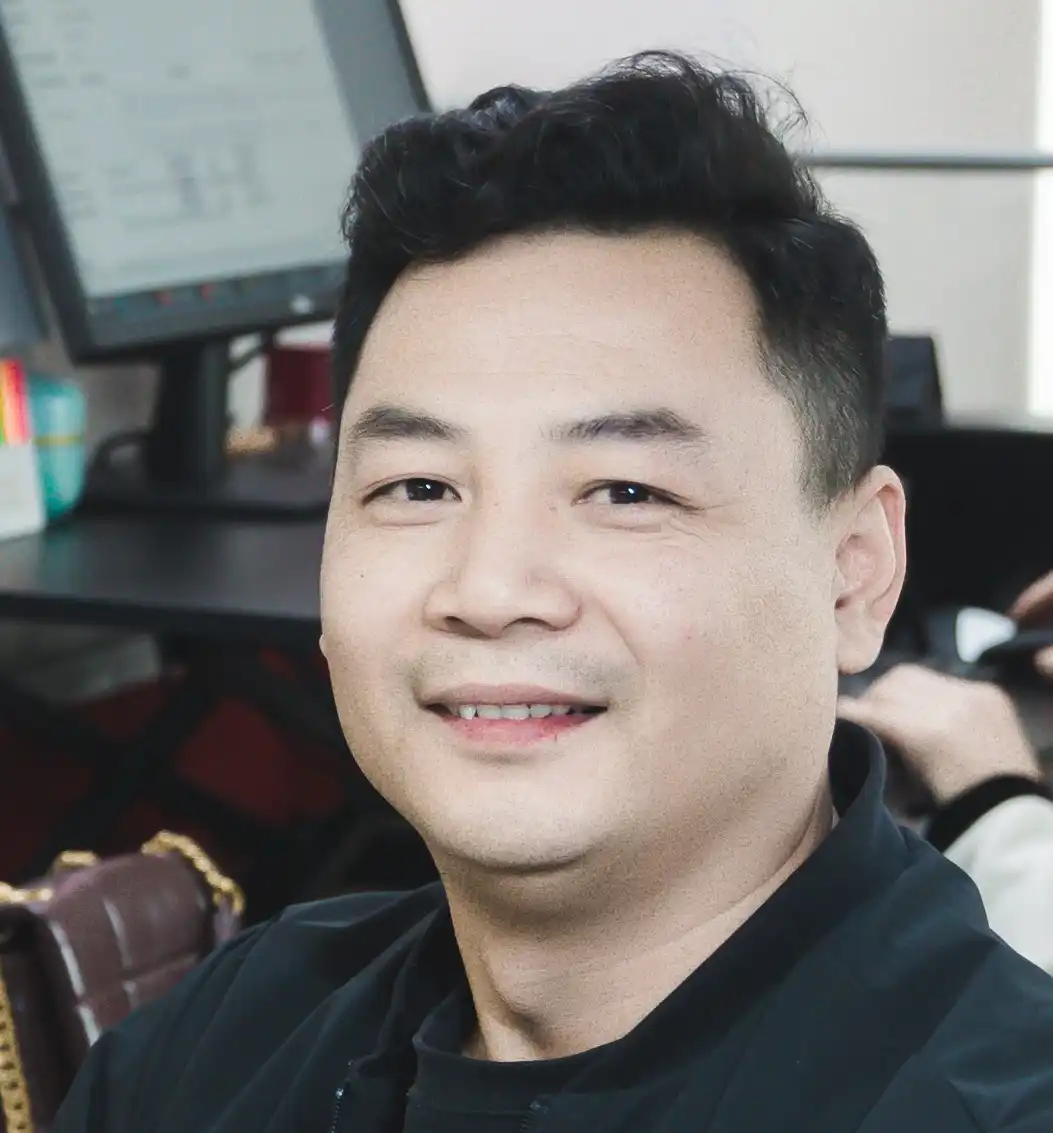
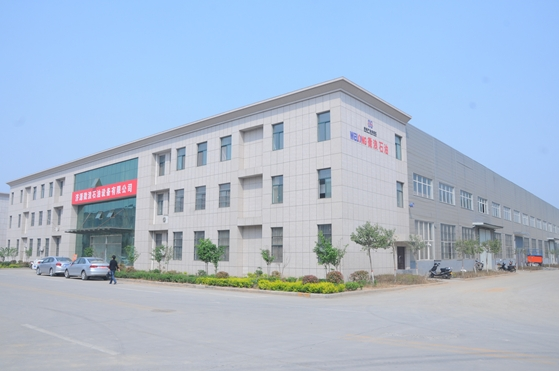
CHINA WELONG - 20+ years manufactuer in oilfield tools