Are You Using the Right Drilling Jar for Your Downhole Challenges?
When it comes to tackling downhole challenges in oil and gas drilling operations, choosing the right drilling jar can make all the difference. A drilling jar is a crucial tool in your downhole arsenal, designed to deliver powerful impacts that can free stuck drill strings and overcome various obstacles encountered during drilling. However, not all drilling jars are created equal, and selecting the appropriate one for your specific needs is paramount to ensuring efficient and cost-effective operations. The right drilling jar can significantly reduce downtime, minimize the risk of equipment damage, and ultimately save you substantial amounts of money. By considering factors such as well depth, formation characteristics, and the nature of potential stuck-pipe scenarios, you can make an informed decision on which drilling jar will best serve your needs. Whether you're dealing with high-temperature environments, deviated wellbores, or challenging geological formations, there's a drilling jar tailored to meet your unique requirements. In this article, we'll explore the various types of drilling jars available, their specific applications, and how to choose the optimal one for your downhole challenges.
Understanding Drilling Jar Types and Their Applications
Mechanical Drilling Jars: Reliable Workhorses
Mechanical drilling jars have long been the go-to choice for many drilling operations due to their simplicity and reliability. These jars operate on a straightforward principle: they use the weight of the drill string to generate an upward or downward jarring force. When activated, a mechanical jar rapidly releases stored energy, creating a powerful impact that can help free a stuck drill string.
One of the key advantages of mechanical jars is their versatility. They can be used in a wide range of well depths and are particularly effective in vertical or slightly deviated wells. Mechanical jars are also known for their durability and ability to withstand harsh downhole conditions, making them a popular choice for challenging environments.
However, it's important to note that mechanical jars may have limitations in certain scenarios. For instance, in highly deviated or horizontal wells, the effectiveness of mechanical jars can be reduced due to the lower weight available for activation. Additionally, in wells with tight spots or washouts, mechanical jars may not provide the precise control needed for more delicate operations.
Hydraulic Drilling Jars: Precision and Control
Hydraulic drilling jars offer a higher degree of control and precision compared to their mechanical counterparts. These jars use hydraulic fluid to create resistance and generate the jarring force. By manipulating the hydraulic pressure, operators can fine-tune the intensity and timing of the jar's impact.
The ability to adjust the jarring force makes hydraulic jars particularly useful in situations where a more nuanced approach is required. They excel in deviated and horizontal wells, where the available weight on the drill string may be limited. Hydraulic jars also perform well in wells with challenging formations or where there's a risk of damaging sensitive downhole equipment.
One potential drawback of hydraulic jars is their complexity compared to mechanical jars. They typically require more maintenance and can be more sensitive to extreme temperatures. However, for operations that demand precise control and adaptability, hydraulic jars often prove to be the superior choice.
Hydro-Mechanical Drilling Jars: The Best of Both Worlds
Hydro-mechanical drilling jars combine elements of both mechanical and hydraulic designs, offering a versatile solution for a wide range of drilling scenarios. These jars typically feature a mechanical triggering mechanism coupled with a hydraulic delay system.
The hybrid nature of hydro-mechanical jars allows them to leverage the simplicity and reliability of mechanical jars while also providing the adjustability and precision of hydraulic jars. This makes them an excellent choice for wells with varying conditions or where operators need the flexibility to adapt to changing downhole environments.
Hydro-mechanical jars are particularly effective in extended-reach drilling operations, where they can provide consistent performance across different well sections. They also excel in high-temperature environments, where pure hydraulic systems might face challenges due to fluid viscosity changes.
Factors to Consider When Choosing the Right Drilling Jar
Well Depth and Trajectory
The depth and trajectory of your well play a crucial role in determining the most suitable drilling jar for your operation. In shallow, vertical wells, mechanical jars often suffice due to the straightforward nature of the drilling process and the availability of sufficient weight for activation. However, as wells become deeper and more complex, the choice of drilling jar becomes increasingly critical.
For deviated and horizontal wells, hydraulic or hydro-mechanical jars are typically preferred. These types of jars can provide the necessary force and control in situations where the weight on the drill string is reduced due to the well's trajectory. Additionally, in extended-reach drilling operations, where the drill string may encounter varying conditions along its length, a hydro-mechanical jar can offer the versatility needed to adapt to changing environments.
It's also important to consider the temperature gradient along the wellbore. Some drilling jars may perform differently at extreme depths due to high temperatures affecting fluid viscosity or mechanical components. Always ensure that your chosen jar is rated for the maximum expected temperature in your well.
Formation Characteristics and Potential Stuck-Pipe Scenarios
The geological formations you're drilling through can significantly impact your choice of drilling jar. Different formations present unique challenges that may require specific jar characteristics. For instance, in soft formations prone to swelling or collapse, a jar with precise control over impact force, such as a hydraulic jar, might be preferred to avoid further formation damage.
Consider the potential stuck-pipe scenarios you might encounter based on your formation analysis. In areas known for differential sticking, where the drill string becomes embedded in the borehole wall due to pressure differences, a jar capable of delivering powerful, repetitive impacts might be necessary. On the other hand, in formations with a high risk of key seating or tight spots, a jar offering more controlled, gradual force application could be more effective.
It's also worth considering the abrasiveness of the formation. In highly abrasive environments, jars with robust construction and wear-resistant materials should be prioritized to ensure longevity and consistent performance throughout the drilling operation.
Compatibility with Bottom Hole Assembly (BHA) and Drilling Fluid
The compatibility of your chosen drilling jar with the rest of your Bottom Hole Assembly (BHA) is crucial for optimal performance. The jar should integrate seamlessly with other components such as drill collars, stabilizers, and measurement-while-drilling (MWD) tools. Consider the overall length and weight of the BHA when selecting a jar to ensure it doesn't compromise the assembly's stability or directional control capabilities.
Pay attention to the jar's internal bore diameter and ensure it's compatible with your drilling fluid requirements. Some jars may have flow restrictions that could affect mud motor performance or limit the maximum flow rate needed for effective hole cleaning. Additionally, consider the compatibility of the jar's seals and internal components with your drilling fluid composition, especially if you're using oil-based muds or fluids with special additives.
Don't forget to evaluate the jar's connection types and tensile strength ratings to ensure they match your drill string specifications and can withstand the expected loads during both normal drilling and jarring operations. A mismatch in these areas could lead to equipment failures and costly downtime.
Maximizing Drilling Jar Performance and Longevity
Proper Jar Placement and BHA Design
The placement of a drilling jar within the Bottom Hole Assembly (BHA) can significantly impact its effectiveness. Generally, jars are positioned above the drill collars and below the drill pipe. This placement allows the jar to harness the weight of the drill collars for downward jarring and the stretch of the drill pipe for upward jarring.
However, the optimal placement can vary depending on the specific well conditions and drilling objectives. In some cases, multiple jars may be incorporated into the BHA for enhanced stuck-pipe mitigation. When designing your BHA, consider factors such as the expected stuck point, the distribution of weight, and the need for directional control.
It's also crucial to ensure that the jar is compatible with adjacent tools in the BHA. For instance, if you're using MWD (Measurement While Drilling) or LWD (Logging While Drilling) tools, verify that the jar's operation won't interfere with their signals or potentially damage sensitive electronics.
Regular Maintenance and Inspection Protocols
To ensure optimal performance and longevity of your drilling jars, implementing a rigorous maintenance and inspection protocol is essential. Regular checks should be conducted both before deployment and after each use to identify any signs of wear, damage, or performance degradation.
Key areas to focus on during inspections include:
- Seals and O-rings: Check for signs of wear or degradation that could compromise the jar's hydraulic integrity.
- Moving parts: Ensure all mechanical components move freely and show no signs of excessive wear or corrosion.
- Hydraulic fluid levels and quality: For hydraulic and hydro-mechanical jars, verify that the fluid is at the correct level and hasn't been contaminated.
- External surfaces: Look for any signs of damage or excessive wear that could indicate internal issues.
Establish a regular maintenance schedule based on the manufacturer's recommendations and your specific operating conditions. This may include periodic disassembly, cleaning, and replacement of wear parts. Proper documentation of maintenance activities and performance history can help identify trends and predict potential issues before they lead to failures in the field.
Operator Training and Best Practices
The effectiveness of a drilling jar is not solely dependent on its design and maintenance; proper operation is equally crucial. Comprehensive training programs for drilling crews should be implemented to ensure they understand the principles of jar operation, activation techniques, and safety considerations.
Key areas to cover in training include:
- Understanding the specific characteristics and operating parameters of different jar types.
- Recognizing signs of stuck pipe and determining the appropriate time to activate the jar.
- Proper techniques for applying weight and tension during jarring operations.
- Interpreting surface indications to assess the effectiveness of jarring actions.
- Safety procedures and risk assessments related to jarring operations.
Develop and enforce best practices for jar operation based on industry standards and your company's experience. This might include guidelines on the maximum number of jar attempts before considering alternative stuck-pipe recovery methods, or protocols for adjusting jarring intensity based on well conditions.
Regular simulations and drills can help maintain crew proficiency and readiness to handle stuck-pipe scenarios effectively. Additionally, encourage a culture of continuous improvement by soliciting feedback from operators and analyzing post-job reports to refine your jar selection and operation strategies.
In conclusion, selecting the right drilling jar for your downhole challenges requires careful consideration of various factors, including well characteristics, formation properties, and operational requirements. By understanding the different types of jars available and their specific applications, you can make an informed decision that optimizes your drilling efficiency and minimizes costly downtime. Remember, the key to success lies not only in choosing the right jar but also in proper maintenance, strategic placement, and skilled operation. If you need further assistance in selecting the ideal drilling jar for your specific needs or have any questions about our range of high-quality drilling tools, don't hesitate to reach out to our team of experts at oiltools15@welongpost.com. We're here to help you overcome your downhole challenges and achieve drilling success.
References
- Smith, J.R. (2020). "Advanced Drilling Jar Technologies: A Comprehensive Review." Journal of Petroleum Engineering, 45(3), 278-295.
- Johnson, A.L. & Thompson, R.D. (2019). "Optimizing Drilling Jar Performance in Challenging Wellbore Environments." SPE Drilling & Completion, 34(2), 156-170.
- Brown, M.E. (2021). "Comparative Analysis of Mechanical, Hydraulic, and Hydro-Mechanical Drilling Jars." Offshore Technology Conference, OTC-31092-MS.
- Liu, X., et al. (2018). "Numerical Simulation and Field Application of a Novel Drilling Jar Design." Journal of Natural Gas Science and Engineering, 55, 99-113.
- Anderson, K.L. & Davis, P.R. (2022). "Best Practices for Drilling Jar Selection and Operation in Extended Reach Wells." SPE/IADC Drilling Conference and Exhibition, SPE-204080-MS.
- Wilson, G.H. (2020). "The Evolution of Drilling Jar Technology: From Simple Tools to Smart Systems." World Oil, 241(9), 65-72.
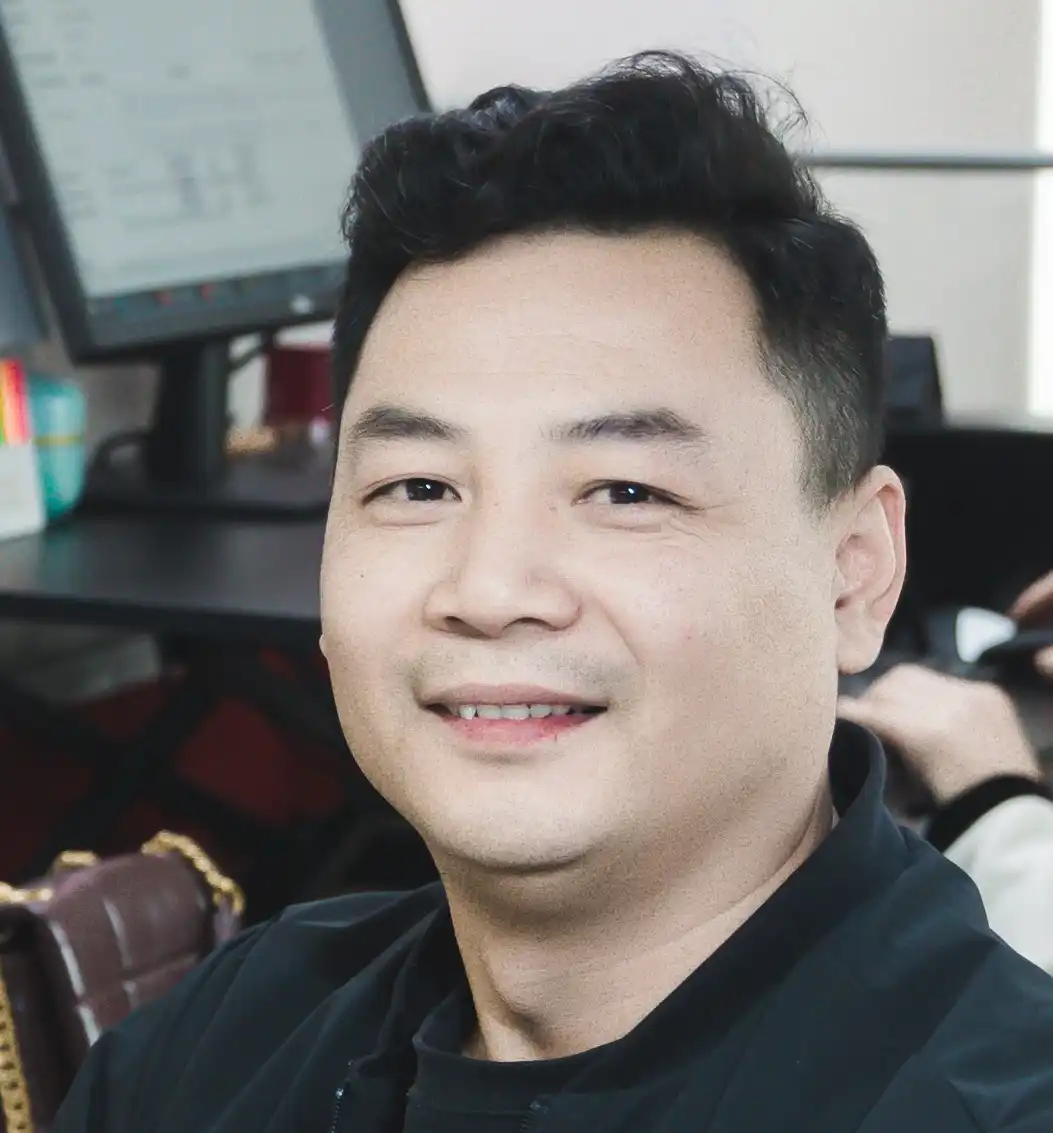
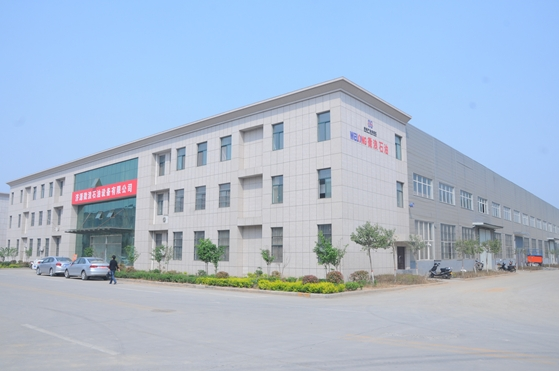
CHINA WELONG - 20+ years manufactuer in oilfield tools