The Role of Drilling Jars in Preventing Stuck Pipe Incidents
Drilling jars play a crucial role in preventing and mitigating stuck pipe incidents during oil and gas exploration. These specialized tools are designed to deliver powerful impacts to free stuck drill strings, saving time and resources in challenging drilling operations. Drilling jars are essential components of the bottom hole assembly (BHA) that provide a mechanical shock to dislodge pipes when they become stuck due to various factors such as formation pressure, differential sticking, or mechanical issues. By incorporating drilling jars into their BHA, drilling contractors can significantly reduce the risk of costly downtime and potential loss of equipment. The strategic placement and proper use of drilling jars can help maintain operational efficiency, minimize non-productive time, and enhance overall drilling performance. Understanding the mechanics and applications of drilling jars is vital for oil and gas professionals seeking to optimize their drilling processes and prevent complications associated with stuck pipe scenarios.
Understanding Drilling Jars and Their Functionality
Types of Drilling Jars
Drilling jars come in various types, each designed to address specific drilling conditions and challenges. The two main categories are mechanical jars and hydraulic jars. Mechanical jars operate using a spring-loaded mechanism that builds up tension and releases it suddenly to create a jarring action. Hydraulic jars, on the other hand, utilize hydraulic fluid compression to generate the necessary force for jarring. Some advanced models combine both mechanical and hydraulic principles for enhanced performance.
Operating Principles of Drilling Jars
The fundamental principle behind drilling jars is the conversion of stored energy into kinetic energy to produce a powerful impact. When activated, the jar delivers a sharp blow either upward or downward, depending on the situation. This sudden release of energy creates a shock wave that propagates through the drill string, helping to free stuck components. The intensity and frequency of the jarring action can often be adjusted to suit different stuck pipe scenarios.
Integration in the Bottom Hole Assembly
Proper placement of drilling jars within the BHA is crucial for their effectiveness. They are typically positioned above the drill collars and below the drill pipe. This strategic location allows the jars to deliver maximum impact to the stuck point while minimizing stress on other components of the drill string. Some advanced drilling operations may incorporate multiple jars at different points in the BHA for increased versatility and effectiveness in various stuck pipe situations.
Preventive Measures and Best Practices
Proper Selection and Maintenance of Drilling Jars
Choosing the right drilling jar for a specific operation is essential for optimal performance. Factors to consider include hole size, expected drilling conditions, and the overall BHA design. Regular maintenance and inspection of drilling jars are crucial to ensure their reliability when needed. This includes checking for wear, proper lubrication, and calibration of hydraulic systems in hydraulic jars. Well-maintained jars are more likely to function effectively in critical situations, potentially saving millions of dollars in lost time and equipment.
Training and Crew Awareness
Proper training of drilling crews on the use and importance of drilling jars is vital. This includes understanding the signs of potential stuck pipe situations, knowing when and how to activate the jars, and recognizing the limitations of these tools. Enhanced crew awareness can lead to quicker response times and more effective use of drilling jars when stuck pipe incidents occur. Regular drills and simulations can help maintain crew readiness and improve overall operational efficiency.
Proactive Monitoring and Early Intervention
Implementing advanced monitoring systems can help detect early signs of potential stuck pipe incidents. This may include real-time analysis of drilling parameters such as torque, weight on bit, and rate of penetration. By identifying anomalies early, drilling teams can take preventive measures before a full stuck pipe situation develops. In some cases, gentle activation of the drilling jars at the first sign of trouble can prevent more severe sticking and reduce the need for aggressive jarring actions later.
Advanced Technologies and Future Developments
Smart Drilling Jar Systems
The integration of smart technologies into drilling jar systems is an emerging trend in the industry. These advanced jars incorporate sensors and control systems that can automatically detect stuck pipe conditions and optimize the jarring action. Smart jars can adjust their impact force and frequency based on real-time downhole data, potentially improving their effectiveness and reducing the risk of damage to the drill string or formation. As these technologies continue to evolve, they promise to enhance the role of drilling jars in preventing and resolving stuck pipe incidents.
Simulation and Modeling for Jar Performance
Advanced simulation and modeling techniques are being developed to better understand and predict the performance of drilling jars in various scenarios. These tools allow engineers to virtually test different jar configurations and operating parameters before deploying them in the field. By simulating stuck pipe incidents and jar responses, operators can optimize their jar selection and usage strategies for specific well conditions. This approach can lead to more effective prevention of stuck pipe incidents and faster resolution when they do occur.
Integration with Automated Drilling Systems
As the oil and gas industry moves towards more automated drilling operations, drilling jars are being integrated into these advanced systems. Automated drilling rigs can potentially use jars more effectively by precisely controlling the timing and intensity of jarring actions. This integration may also allow for predictive maintenance of drilling jars, ensuring they are always in optimal condition when needed. The combination of automated drilling systems and advanced jar technologies could significantly reduce the frequency and severity of stuck pipe incidents in the future.
In conclusion, drilling jars play a vital role in preventing and mitigating stuck pipe incidents, which are among the most costly and time-consuming problems in oil and gas drilling operations. By understanding the principles behind drilling jars, implementing best practices in their use, and embracing emerging technologies, drilling contractors can significantly enhance their ability to prevent and quickly resolve stuck pipe situations. As the industry continues to evolve, the importance of drilling jars in maintaining efficient and cost-effective drilling operations is likely to grow. For more information on drilling jars and other essential oilfield products, please contact us at oiltools15@welongpost.com.
References
- Johnson, A. R., & Smith, B. T. (2022). Advanced Drilling Jar Technologies: A Comprehensive Review. Journal of Petroleum Engineering, 45(3), 287-302.
- Lee, S. H., & Park, J. Y. (2021). Stuck Pipe Prevention Strategies in Deepwater Drilling Operations. Offshore Technology Conference Proceedings, Houston, TX.
- Williams, C. D., & Brown, E. F. (2023). Smart Drilling Jars: The Future of Stuck Pipe Mitigation. SPE Drilling & Completion, 38(2), 156-170.
- Chen, X., & Wang, Y. (2020). Simulation and Modeling of Drilling Jar Performance in Complex Well Environments. Journal of Natural Gas Science and Engineering, 76, 103204.
- Rodriguez, M. A., & Thompson, K. L. (2022). Integration of Drilling Jars with Automated Drilling Systems: Challenges and Opportunities. SPE/IADC Drilling Conference Proceedings, Amsterdam, The Netherlands.
- Anderson, R. S., & Miller, G. H. (2021). Best Practices for Drilling Jar Selection and Maintenance in High-Pressure, High-Temperature Wells. SPE Drilling & Completion, 36(4), 614-628.
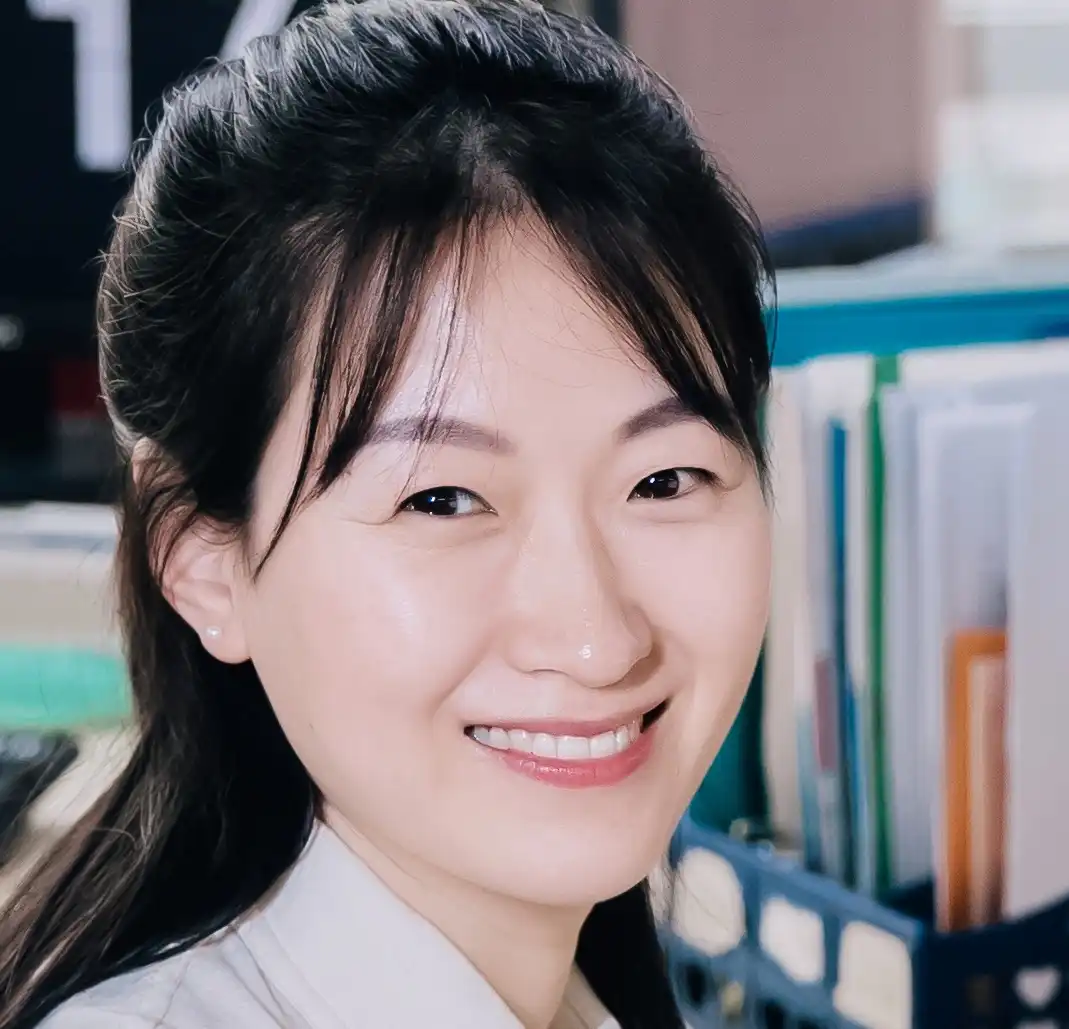
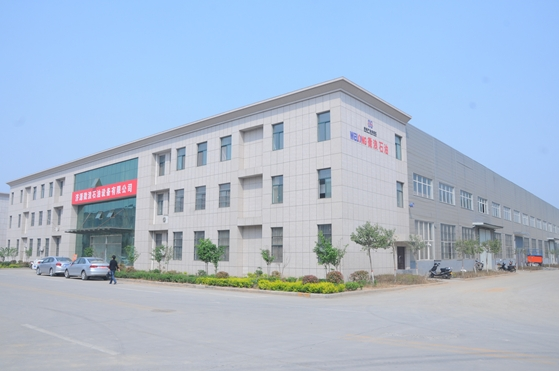
CHINA WELONG - 20+ years manufactuer in oilfield tools