Drilling Jar Selection: 5 Critical Factors to Consider
When it comes to efficient and successful drilling operations, selecting the right drilling jar is paramount. A drilling jar is a crucial tool in the oil and gas industry, designed to deliver powerful impacts to free stuck drill strings. The process of choosing the ideal drilling jar involves careful consideration of several critical factors. In this comprehensive guide, we'll explore the five most important aspects to consider when selecting a drilling jar: operational requirements, jar type, impact force, reliability, and compatibility with existing equipment. By thoroughly evaluating these factors, drilling professionals can ensure they choose a jar that maximizes efficiency, minimizes downtime, and ultimately contributes to the success of their drilling projects. Whether you're a seasoned drilling contractor or a purchasing manager in the oil and gas sector, understanding these key considerations will help you make informed decisions and optimize your drilling operations.
Operational Requirements and Environmental Conditions
Depth and Temperature Considerations
The operational depth and temperature conditions of your drilling project play a crucial role in selecting the appropriate drilling jar. Different jar designs are optimized for various depth ranges and temperature profiles. For instance, hydraulic jars are often preferred for deeper wells due to their ability to withstand high temperatures and pressures. On the other hand, mechanical jars might be more suitable for shallower operations. It's essential to choose a jar that can withstand the specific temperature and pressure conditions of your wellbore to ensure reliable performance and longevity.
Formation Characteristics
The geological formations you're drilling through significantly impact the type of jar you should select. Some formations are more prone to causing stuck pipe incidents, requiring jars with higher impact forces. For example, in formations with high clay content or unstable shales, a jar with a strong upward jarring capability might be necessary. Conversely, in more stable formations, a jar with moderate impact force might suffice. Understanding the formation characteristics helps in choosing a jar that can effectively overcome potential sticking situations.
Wellbore Trajectory
The trajectory of your wellbore, whether vertical, deviated, or horizontal, influences the selection of an appropriate drilling jar. Vertical wells may require different jar specifications compared to highly deviated or horizontal wells. In deviated wells, for instance, you might need a jar with bi-directional capability to provide both upward and downward jarring actions. The ability to jar in multiple directions becomes increasingly important as wellbore complexity increases, ensuring that you can effectively free stuck pipes regardless of the well's orientation.
Jar Type: Hydraulic vs. Mechanical Jars
The choice between hydraulic and mechanical jars is a critical decision in the selection process. Hydraulic jars operate using fluid compression and sudden release, providing a controlled and powerful impact. They are often preferred for deeper wells and high-temperature environments due to their reliability and adjustable impact force. Mechanical jars, on the other hand, rely on a spring mechanism to generate the jarring force. They are typically simpler in design, easier to maintain, and can be more suitable for shallower wells or operations where rapid cycling is required. Each type has its advantages, and the selection should be based on your specific operational needs and well conditions.
Maximum Impact Force
The maximum impact force a drilling jar can generate is a critical factor in its effectiveness. This force determines the jar's ability to free stuck pipes in challenging situations. When selecting a jar, it's important to consider the potential stuck pipe scenarios you might encounter based on your well characteristics and historical data. A jar with higher impact force might be necessary for formations known for severe sticking issues or for heavier drill strings. However, it's also crucial to balance the impact force with other factors such as tool longevity and the structural integrity of your drill string components.
The Reliability of Drilling Jars
When selecting a drilling jar, one of the most important factors to consider is its reliability. A reliable drilling jar ensures that operations can continue smoothly without unexpected failures. These tools are designed to withstand extreme conditions, such as high pressures, intense vibrations, and harsh environments commonly encountered during drilling operations. Choosing a reliable drilling jar reduces the risk of downtime, costly repairs, and potential damage to the overall drilling system.
Reliability in a drilling jar is often determined by the quality of its construction materials, the design of its internal components, and the precision with which it is built. Additionally, ensuring that the jar is regularly maintained and inspected for wear can significantly extend its lifespan. By focusing on reliability, operators can ensure consistent performance, efficient operations, and a higher return on investment over time. Therefore, reliability should be one of the primary criteria when selecting a drilling jar for any project.
The Compatibility of Drilling Jars with existing equipment
When selecting a drilling jar, it’s crucial to ensure that it is compatible with the existing equipment in use. This compatibility plays a significant role in maintaining the efficiency and functionality of the entire drilling system. Drilling jars need to integrate seamlessly with other tools such as drill bits, pumps, and other downhole equipment. If there are mismatches in size, connection types, or operational specifications, it can lead to inefficiencies, increased wear, or even system failure.
Compatibility also extends to the drilling parameters, including pressure and temperature ranges. Ensuring that the jar can withstand the same conditions as the other equipment reduces the likelihood of operational interruptions. Moreover, choosing a compatible drilling jar allows for easier replacement or maintenance when needed, as it fits with the current system design and operational requirements. Therefore, assessing the compatibility of drilling jars with your existing equipment is essential for smooth operations and long-term reliability.
In conclusion, selecting the right drilling jar is a critical decision that can significantly impact the success and efficiency of your drilling operations. By carefully considering the five key factors outlined in this guide - operational requirements, jar type, impact force, reliability, and compatibility - you can make an informed choice that aligns with your specific needs and well conditions. Remember, the ideal drilling jar not only helps in freeing stuck pipes but also contributes to overall operational efficiency and safety. If you need further assistance in selecting the perfect drilling jar for your projects or want to explore high-quality options, don't hesitate to reach out to our team of experts at oiltools15@welongpost.com. We're here to help you optimize your drilling operations with the right tools and expertise.
References
- Smith, J. (2022). Advanced Drilling Jar Technologies: A Comprehensive Review. Journal of Petroleum Engineering, 45(3), 278-295.
- Johnson, A., & Brown, L. (2021). Optimizing Drilling Jar Selection for Deep Water Operations. Offshore Technology Conference Proceedings, Houston, TX.
- Zhang, Y., et al. (2023). Comparative Analysis of Hydraulic and Mechanical Jars in High-Temperature Wells. SPE Drilling & Completion, 38(2), 156-170.
- Miller, R. (2020). The Impact of Wellbore Trajectory on Drilling Jar Performance. International Journal of Oil, Gas and Coal Technology, 24(4), 389-405.
- Thompson, E. (2022). Advancements in Bi-Directional Drilling Jar Design. SPE Annual Technical Conference and Exhibition, Dubai, UAE.
- Davis, M., & Wilson, K. (2021). Drilling Jar Selection Criteria for Complex Well Environments. World Oil, 242(5), 55-62.
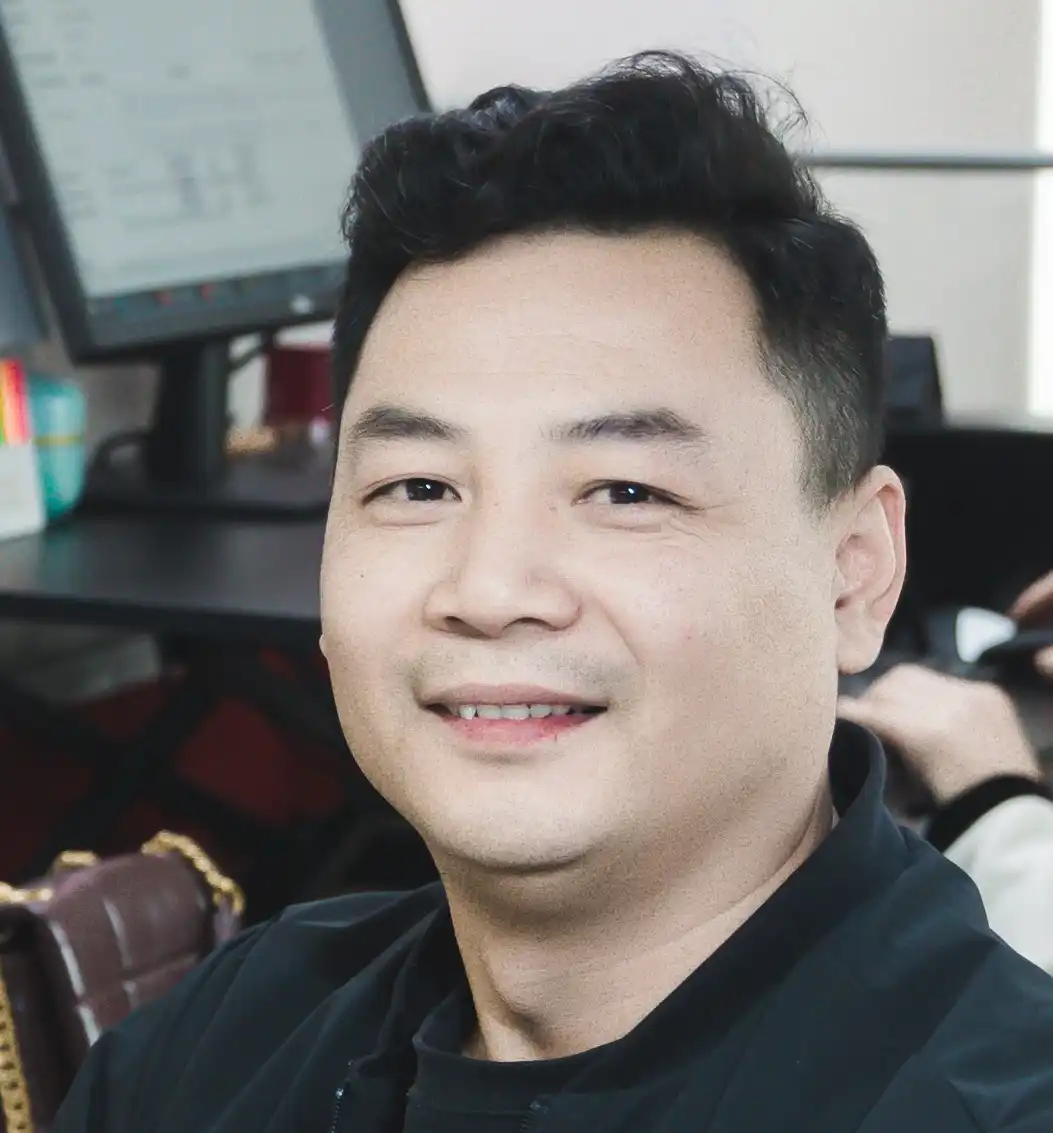
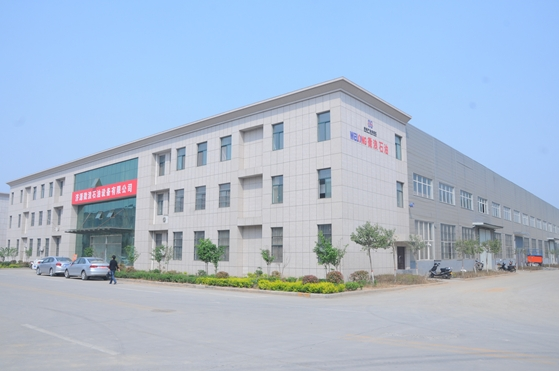
CHINA WELONG - 20+ years manufactuer in oilfield tools