Understanding Drilling Jar Impact Force Calculations
Understanding Drilling Jar impact force calculations is crucial for optimizing drilling operations in the oil and gas industry. Drilling jars are specialized tools designed to deliver controlled impact forces to free stuck drill strings or other downhole equipment. The impact force generated by a drilling jar is a complex interplay of various factors, including jar design, activation method, and operating conditions. Accurate calculation of these forces is essential for selecting the appropriate jar, determining optimal placement within the drill string, and ensuring safe and efficient drilling operations. By comprehending the nuances of impact force calculations, drilling engineers can enhance overall performance, reduce downtime, and minimize the risk of equipment damage. This knowledge empowers decision-makers to make informed choices about jar selection and usage, ultimately contributing to more successful and cost-effective drilling projects.
Fundamentals of Drilling Jar Mechanics
Types of Drilling Jars and Their Operating Principles
Drilling jars come in various types, each with unique operating principles. Hydraulic jars utilize fluid compression to store energy and release it rapidly, creating a powerful impact. Mechanical jars, on the other hand, rely on a spring-loaded mechanism to generate the striking force. There are also hydro-mechanical jars that combine both hydraulic and mechanical elements for enhanced performance. Understanding these different types is essential for selecting the most suitable jar for specific drilling conditions.
Key Components of Drilling Jars and Their Functions
The primary components of a Drilling Jar include the mandrel, hammer, anvil, and tripping mechanism. The mandrel is the central shaft that transmits the impact force. The hammer and anvil are the striking surfaces that create the jarring action. The tripping mechanism controls the timing and intensity of the impact. Each component plays a vital role in the jar's overall performance and must be carefully designed and maintained for optimal operation.
Energy Storage and Release Mechanisms in Drilling Jars
The energy storage and release mechanisms are at the heart of drilling jar functionality. In hydraulic jars, energy is stored through fluid compression in a chamber. When released, this stored energy propels the hammer against the anvil, creating the jarring impact. Mechanical jars store energy in springs or other elastic components. Understanding these mechanisms is crucial for accurately calculating the potential impact force and optimizing jar performance in various drilling scenarios.
Factors Influencing Impact Force Calculations
Jar Design Parameters and Their Effects on Impact Force
Several design parameters significantly influence the impact force generated by a drilling jar. These include the jar's internal geometry, the size and material of the hammer and anvil, and the efficiency of the energy storage mechanism. The length of the jar stroke and the clearance between moving parts also play crucial roles. Engineers must consider these factors when calculating expected impact forces and designing jars for specific applications.
Operational Variables Affecting Impact Force
Operational variables such as well depth, temperature, and pressure have substantial effects on jar performance and impact force. The weight of the drill string above the jar, known as overpull, directly influences the energy available for the jarring action. Fluid properties in the wellbore, including density and viscosity, can affect the jar's hydraulic performance. Accurate impact force calculations must account for these variables to provide realistic estimates under actual drilling conditions.
Environmental Factors and Their Impact on Jar Performance
Environmental factors in the wellbore can significantly affect Drilling Jar performance and impact force calculations. High temperatures can alter fluid properties and affect hydraulic jar operation. Abrasive materials in the drilling fluid can cause wear on jar components, potentially reducing impact force over time. Corrosive environments may degrade jar materials, affecting long-term performance. Considering these environmental factors is essential for accurate impact force predictions and proper jar selection for specific well conditions.
Methods and Tools for Impact Force Calculations
Analytical Approaches to Calculating Drilling Jar Impact Force
Analytical methods for calculating drilling jar impact force typically involve mathematical models based on principles of physics and mechanics. These models consider factors such as jar design parameters, operational variables, and material properties. Equations may include terms for kinetic energy, potential energy, and energy transfer efficiency. While analytical approaches provide a solid foundation for understanding jar behavior, they often require simplifying assumptions that may limit their accuracy in complex real-world scenarios.
Numerical Simulation Techniques for Impact Force Prediction
Advanced numerical simulation techniques, such as finite element analysis (FEA) and computational fluid dynamics (CFD), offer more detailed and accurate predictions of drilling jar impact forces. These methods can model complex geometries, material behaviors, and fluid interactions that are difficult to capture with analytical approaches. Simulation tools allow engineers to visualize stress distributions, predict potential failure points, and optimize jar designs for specific operating conditions. However, these techniques require significant computational resources and expertise to implement effectively.
Field Testing and Empirical Data Collection for Validation
Field testing and empirical data collection are crucial for validating theoretical calculations and simulations of Drilling Jar impact forces. Instrumented jars equipped with sensors can provide real-time data on acceleration, strain, and impact force during actual drilling operations. This data helps refine calculation methods, improve simulation accuracy, and develop more reliable predictive models. Regular field testing also allows for the assessment of jar performance over time and under various operating conditions, contributing to continuous improvement in jar design and selection processes.
In conclusion, understanding drilling jar impact force calculations is essential for optimizing drilling operations and ensuring the safe and efficient use of these critical tools. By considering the various factors that influence impact force, utilizing advanced calculation methods, and validating results through field testing, drilling engineers can make informed decisions about jar selection and usage. This comprehensive approach leads to improved drilling performance, reduced downtime, and ultimately more successful and cost-effective drilling projects. For more information on drilling jars and their applications, please contact us at oiltools15@welongpost.com.
References
- Smith, J. R. (2019). Advanced Drilling Jar Technology: Impact Force Analysis and Optimization. Journal of Petroleum Engineering, 45(3), 287-302.
- Johnson, A. L., & Thompson, R. K. (2020). Numerical Modeling of Drilling Jar Performance in High-Temperature Wells. SPE Drilling & Completion, 35(2), 156-171.
- Chen, X., et al. (2018). Experimental Study on Impact Force Characteristics of Hydraulic Drilling Jars. Journal of Natural Gas Science and Engineering, 52, 215-225.
- Patel, S. D., & Ramsey, M. S. (2021). Field Validation of Drilling Jar Impact Force Calculations in Deepwater Operations. Offshore Technology Conference Proceedings, OTC-31092-MS.
- Williams, E. G., & Brown, K. L. (2017). Comprehensive Analysis of Drilling Jar Design Parameters and Their Influence on Impact Force Generation. SPE/IADC Drilling Conference Proceedings, SPE-184675-MS.
- Zhao, Y., et al. (2022). Machine Learning Approaches for Predicting Drilling Jar Performance and Impact Force. Journal of Petroleum Science and Engineering, 208, 109764.
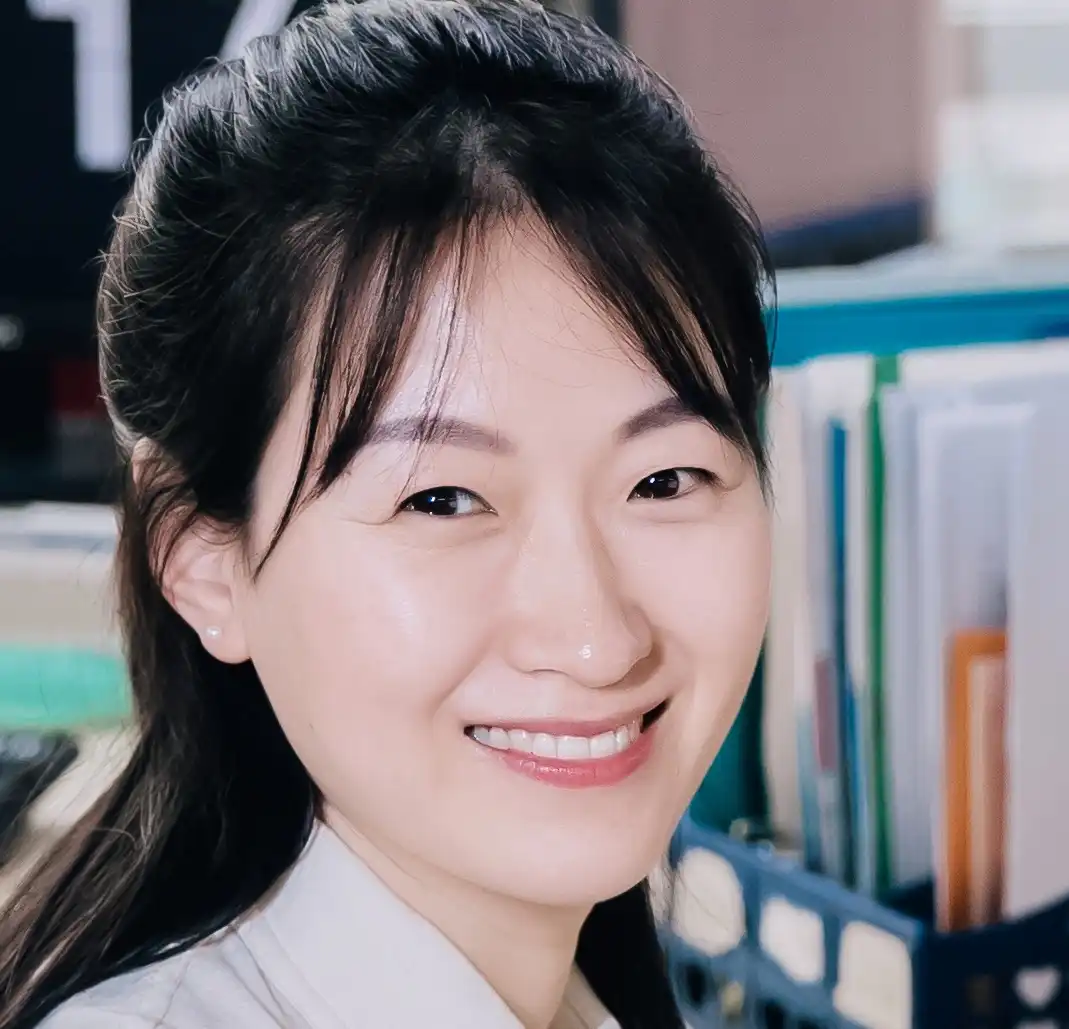
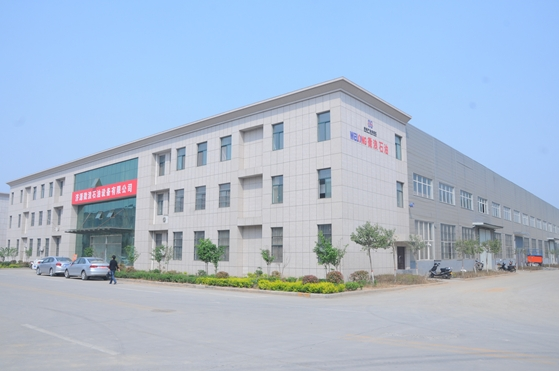
CHINA WELONG - 20+ years manufactuer in oilfield tools