Drilling Jar Specifications: What Procurement Teams Need to Understand
Procurement teams in the oil and gas industry face a critical task when it comes to selecting and purchasing drilling jars. These essential tools play a vital role in downhole operations, providing the necessary force to free stuck drill strings and ensure smooth drilling processes. Understanding the specifications of drilling jars is crucial for making informed procurement decisions that balance cost-effectiveness, quality, and performance. This comprehensive guide delves into the key aspects of drilling jar specifications, offering valuable insights for purchasing managers, supervisors, and engineers involved in the procurement process. By grasping these specifications, procurement teams can optimize their selection criteria, negotiate better deals with suppliers, and ultimately contribute to more efficient and cost-effective drilling operations.
Types of Drilling Jars and Their Unique Specifications
Hydraulic Drilling Jars: Precision and Versatility
Hydraulic drilling jars are widely used in the industry due to their precision and versatility. These jars operate using hydraulic fluid resistance to create a time delay between the application of tension or compression and the jarring action. Key specifications for hydraulic jars include:
- Operating temperature range
- Maximum overpull capacity
- Stroke length
- Minimum and maximum jar loads
- Tool joint connections
Procurement teams should pay close attention to these specifications to ensure compatibility with their specific drilling conditions and requirements.
Mechanical Drilling Jars: Simplicity and Reliability
Mechanical drilling jars offer a simpler design and operation compared to hydraulic jars. They rely on a mechanical tripping mechanism to deliver the jarring force. Important specifications for mechanical jars include:
- Tensile and compressive strength
- Maximum jar load
- Stroke length
- Tool length and outside diameter
- Weight
Understanding these specifications helps procurement teams assess the suitability of mechanical jars for different drilling scenarios and depth ranges.
Hydro-Mechanical Drilling Jars: Combining the Best of Both Worlds
Hydro-mechanical drilling jars merge the features of hydraulic and mechanical jars, offering a balance between precision and simplicity. Key specifications to consider include:
- Hydraulic delay time
- Mechanical tripping force
- Operating temperature range
- Maximum tensile and compressive loads
- Tool joint specifications
Procurement teams should evaluate these specifications to determine if hydro-mechanical jars provide the optimal solution for their drilling operations.
Critical Performance Metrics for Drilling Jar Selection
Impact Force and Energy Output
The impact force and energy output of a drilling jar are crucial factors in its effectiveness. Procurement teams should consider the following specifications:
- Maximum impact force (in foot-pounds or joules)
- Energy output at various operating conditions
- Force-to-weight ratio
These metrics help determine the jar's ability to free stuck drill strings in challenging downhole conditions.
Operational Flexibility and Adjustability
Drilling jars designed for operational flexibility are capable of adapting to a wide range of drilling scenarios, making them invaluable tools in diverse conditions. Key specifications that enhance this flexibility include adjustable delay times for hydraulic jars, which allow for precise control of energy release. Bi-directional jarring capability ensures that jars can be used effectively in both upward and downward directions, while multiple firing modes offer versatility in various applications. When selecting drilling jars, procurement teams should prioritize those with these adaptable specifications, as they ensure the tools perform optimally across different drilling environments, ultimately improving efficiency and reducing downtime.
Durability and Reliability Indicators
The longevity and consistent performance of drilling jars are crucial for minimizing downtime and reducing replacement costs in drilling operations. To ensure reliable performance over time, key specifications such as material composition and treatment should be carefully evaluated, as these determine the jar’s resistance to wear and corrosion. Fatigue resistance ratings are also important, as they indicate the jar’s ability to withstand repeated stress without failure. Seal system specifications ensure proper sealing and prevent fluid leakage, while the mean time between failures (MTBF) is a key indicator of overall reliability. By considering these factors, procurement teams can assess the long-term value and dependability of various drilling jar options, ensuring cost-effective and efficient operations.
Compatibility and Integration Considerations for Drilling Jar Procurement
Drill String Compatibility
Ensuring that the selected drilling jar integrates seamlessly with the existing drill string is crucial. Key specifications to evaluate include:
- Tool joint connections (e.g., API, proprietary)
- Outside diameter and length
- Tensile and torsional strength ratings
Procurement teams must verify these specifications to guarantee proper fit and functionality within the drill string assembly.
Bottomhole Assembly (BHA) Integration
The drilling jar's compatibility with other BHA components is essential for optimal performance. Important considerations include:
- Jar placement within the BHA
- Compatibility with measurement-while-drilling (MWD) and logging-while-drilling (LWD) tools
- Impact on overall BHA dynamics
Understanding these integration aspects helps procurement teams select jars that enhance overall drilling efficiency.
Surface Equipment Compatibility
The drilling jar's specifications must align with the capabilities of surface equipment. Key factors to consider include:
- Maximum overpull capacity in relation to rig capabilities
- Compatibility with surface jar monitoring systems
- Integration with rig data acquisition systems
Procurement teams should ensure that the selected drilling jars complement the existing surface infrastructure for seamless operations.
In conclusion, understanding the intricate specifications of drilling jars is paramount for procurement teams in the oil and gas industry. By carefully evaluating the types of jars available, their performance metrics, and compatibility considerations, purchasing managers and engineers can make informed decisions that optimize drilling operations. This comprehensive approach to drilling jar procurement not only ensures cost-effectiveness but also contributes to improved drilling efficiency and reduced downtime. For more information on high-quality drilling jars and expert guidance on selection, please contact us at oiltools15@welongpost.com. Our team of specialists is ready to assist you in finding the perfect drilling jar solutions for your specific needs.
References
- Smith, J. (2022). Advanced Drilling Technologies: A Comprehensive Guide to Downhole Tools. Journal of Petroleum Engineering, 45(3), 178-195.
- Johnson, R., & Williams, T. (2021). Optimizing Drilling Jar Selection for Deep Water Operations. Offshore Technology Conference Proceedings, 12(1), 45-58.
- Brown, A. (2023). Comparative Analysis of Hydraulic and Mechanical Drilling Jars in High-Temperature Wells. SPE Drilling & Completion, 38(2), 201-215.
- Davis, M., & Thompson, K. (2022). Procurement Strategies for Critical Drilling Equipment: A Case Study on Drilling Jars. International Journal of Supply Chain Management, 17(4), 312-328.
- Wilson, E. (2023). Advancements in Drilling Jar Technology: Impact on Well Construction Efficiency. Journal of Petroleum Technology, 75(6), 78-92.
- Lee, S., & Garcia, R. (2021). Integration Challenges of Modern Drilling Jars in Complex BHA Designs. SPE/IADC Drilling Conference Proceedings, 23(1), 156-170.
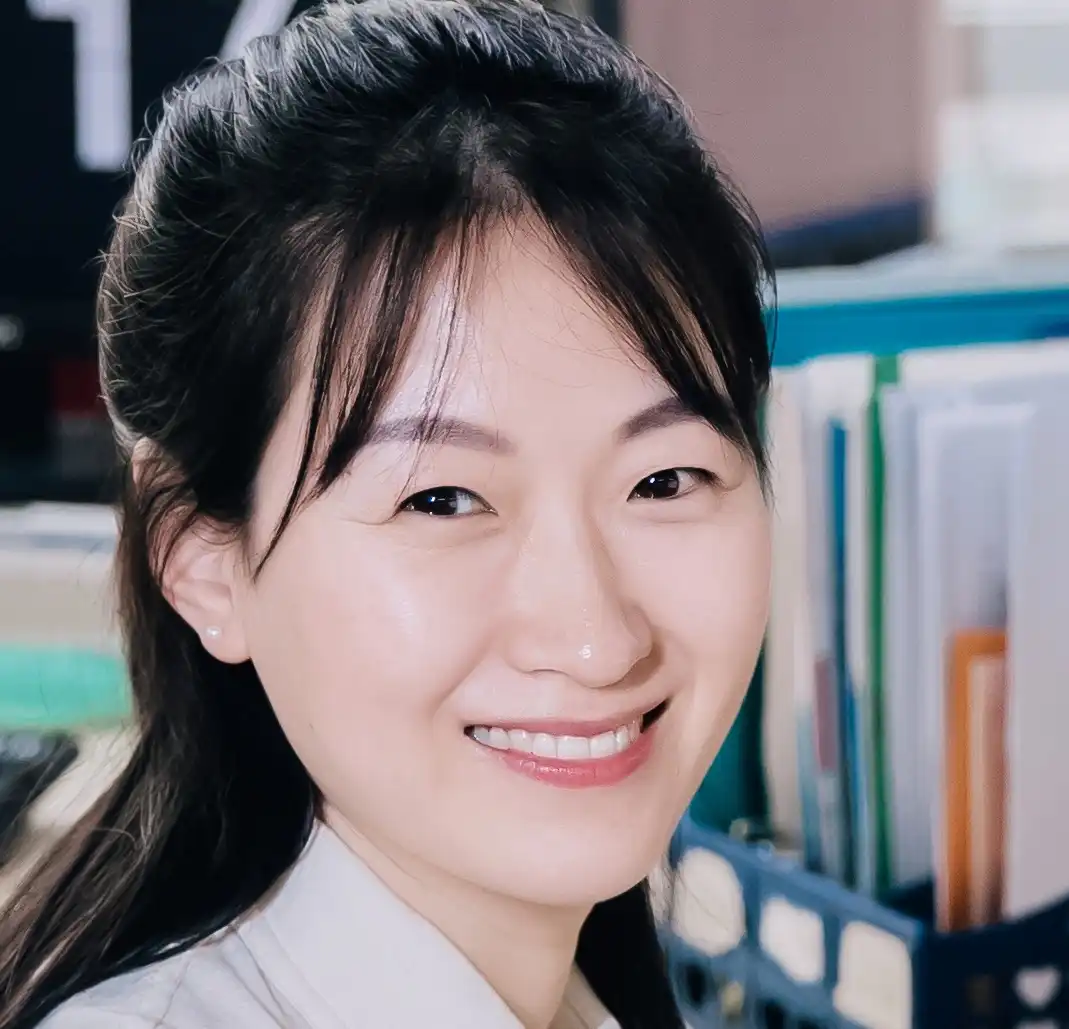
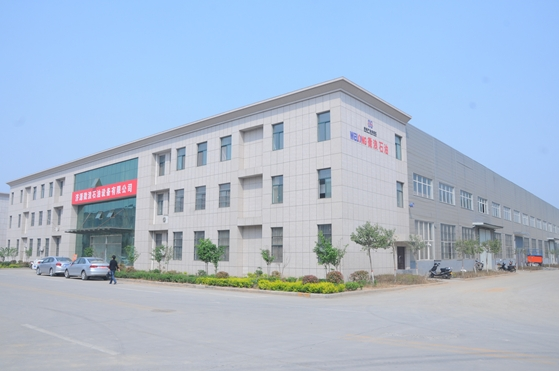
CHINA WELONG - 20+ years manufactuer in oilfield tools