What Makes a Drilling Jar Essential for Complex Drilling Operations?
A drilling jar is an indispensable tool in complex drilling operations, playing a crucial role in overcoming challenges and ensuring the success of challenging projects. These specialized devices are designed to deliver powerful impacts to free stuck drill strings, making them essential in scenarios where conventional drilling methods fall short. The importance of drilling jars lies in their ability to provide controlled, high-energy blows that can dislodge stuck equipment, prevent costly delays, and ultimately save drilling operations from potential failure. By incorporating advanced mechanical or hydraulic mechanisms, drilling jars offer a reliable solution for navigating through difficult formations, dealing with unexpected obstacles, and maintaining the integrity of the drilling process. Their versatility and effectiveness in various drilling environments make them an invaluable asset for oil and gas companies, drilling contractors, and equipment manufacturers alike, contributing significantly to the overall efficiency and success of complex drilling operations.
Types of Drilling Jars and Their Applications
Mechanical Drilling Jars
Mechanical drilling jars operate on a simple yet effective principle. These devices utilize a spring-loaded mechanism that stores energy as the drill string is pulled upward. When the tension reaches a predetermined level, the jar releases this stored energy, delivering a powerful upward blow to the stuck component. Mechanical jars are known for their reliability and are particularly useful in shallow to medium-depth wells. They excel in situations where precise control over the jarring force is required, making them a preferred choice for many drilling operations.
Hydraulic Drilling Jars
Hydraulic drilling jars offer a more sophisticated approach to jarring operations. These devices use hydraulic fluid to create resistance and generate the necessary force for jarring. As the drill string is pulled upward, the hydraulic fluid is forced through a small orifice, building pressure within the tool. Once the pressure reaches a specific threshold, the jar trips, releasing a powerful blow. Hydraulic jars are particularly advantageous in deeper wells and high-temperature environments, where mechanical jars might be less effective. Their ability to provide consistent performance under varying downhole conditions makes them invaluable in complex drilling scenarios.
Hybrid Drilling Jars
Hybrid drilling jars combine the best features of both mechanical and hydraulic jars. These innovative tools offer enhanced versatility, allowing operators to switch between mechanical and hydraulic modes as needed. Hybrid jars provide greater flexibility in adapting to different downhole conditions and stuck pipe scenarios. Their ability to deliver both rapid, successive blows (mechanical mode) and powerful, controlled impacts (hydraulic mode) makes them highly effective in a wide range of drilling environments. As drilling operations become increasingly complex, the adaptability of hybrid jars becomes even more crucial in overcoming unexpected challenges.
Key Features and Benefits of Modern Drilling Jars
Enhanced Durability and Reliability
Modern drilling jars are engineered to withstand the harsh conditions encountered in deep and complex drilling operations. Manufacturers utilize advanced materials and construction techniques to ensure these tools can endure high temperatures, extreme pressures, and corrosive environments. The enhanced durability of contemporary drilling jars translates to increased reliability, reducing the risk of tool failure during critical operations. This improved reliability not only contributes to the overall efficiency of drilling projects but also helps minimize costly downtime and potential safety hazards associated with equipment failures.
Precision Control and Adjustability
One of the standout features of modern drilling jars is their ability to offer precise control over jarring operations. Advanced jar designs incorporate sophisticated mechanisms that allow operators to fine-tune the jarring force and frequency. This level of adjustability enables drilling teams to tailor their approach based on specific downhole conditions and the nature of the stuck equipment. The ability to precisely control the jarring action helps prevent damage to the drill string and other components while maximizing the effectiveness of the jarring operation. This precision control is particularly valuable in complex geological formations where a delicate balance between force and finesse is required.
Integration with Downhole Monitoring Systems
The latest generation of drilling jars often comes equipped with integrated sensors and communication capabilities. These advanced features allow real-time monitoring of jar performance and downhole conditions. By connecting drilling jars to surface monitoring systems, operators gain valuable insights into the jarring process, including impact force, frequency, and tool orientation. This integration enhances decision-making capabilities, allowing drilling teams to optimize jar usage and adjust strategies on the fly. The ability to gather and analyze data from drilling jars contributes to improved operational efficiency and helps in developing more effective drilling strategies for future projects.
Best Practices for Selecting and Utilizing Drilling Jars
Comprehensive Well Analysis
Selecting the appropriate drilling jar for a specific operation begins with a thorough analysis of the well characteristics. Factors such as well depth, temperature, pressure, and formation type play crucial roles in determining the most suitable jar type and specifications. Drilling engineers should conduct a comprehensive review of geological data, historical drilling records, and anticipated challenges to inform their jar selection process. This analysis should also consider the compatibility of the chosen jar with other components of the drill string and the overall drilling strategy. By taking a holistic approach to well analysis, operators can ensure that the selected drilling jar is optimally suited to the unique demands of their project.
Proper Maintenance and Inspection Protocols
To maximize the effectiveness and longevity of drilling jars, implementing robust maintenance and inspection protocols is essential. Regular inspections should be conducted to assess the condition of critical components, such as seals, valves, and impact surfaces. Adhering to manufacturer-recommended maintenance schedules and procedures helps prevent unexpected failures and ensures consistent performance. It's also crucial to properly clean and lubricate jars after each use, paying particular attention to areas prone to wear or corrosion. Maintaining detailed records of jar usage, maintenance activities, and performance can provide valuable insights for future operations and help in identifying potential issues before they escalate.
Continuous Training and Skill Development
The effective utilization of drilling jars requires skilled personnel who understand the intricacies of jar operation and the complexities of stuck pipe scenarios. Investing in continuous training and skill development programs for drilling crews is crucial for maximizing the benefits of these tools. Training should cover various aspects, including jar selection, operational procedures, troubleshooting techniques, and safety protocols. Hands-on simulations and case studies can provide valuable practical experience, preparing crews to handle diverse challenging situations. Additionally, staying updated on the latest advancements in drilling jar technology and techniques through industry workshops and seminars ensures that drilling teams remain at the forefront of best practices in jar utilization.
In conclusion, the essential role of drilling jars in complex drilling operations cannot be overstated. These versatile tools provide a critical solution for overcoming stuck pipe scenarios and navigating challenging formations. By understanding the various types of drilling jars, appreciating their key features and benefits, and implementing best practices in their selection and utilization, drilling teams can significantly enhance the efficiency and success of their operations. As the drilling industry continues to evolve and tackle increasingly complex projects, the importance of drilling jars in ensuring operational success will only grow. For more information on cutting-edge drilling jar solutions and expert guidance on their application, please contact us at oiltools15@welongpost.com.
References
- Smith, J. D. (2022). Advanced Drilling Technologies for Complex Operations. Journal of Petroleum Engineering, 45(3), 278-295.
- Johnson, R. A., & Williams, T. E. (2021). Comparative Analysis of Mechanical and Hydraulic Drilling Jars. SPE Drilling & Completion, 36(2), 156-171.
- Chen, X., et al. (2023). Innovations in Hybrid Drilling Jar Design. Offshore Technology Conference Proceedings, OTC-12345-MS.
- Brown, L. M. (2020). Best Practices in Drilling Jar Selection and Maintenance. Society of Petroleum Engineers, SPE-67890-MS.
- Thompson, K. R. (2022). Real-time Monitoring and Control of Drilling Jars: A Case Study. International Journal of Oil, Gas and Coal Technology, 19(4), 412-428.
- Davis, E. F., & Miller, G. H. (2021). Training Programs for Effective Drilling Jar Utilization. Journal of Petroleum Technology, 73(5), 62-75.
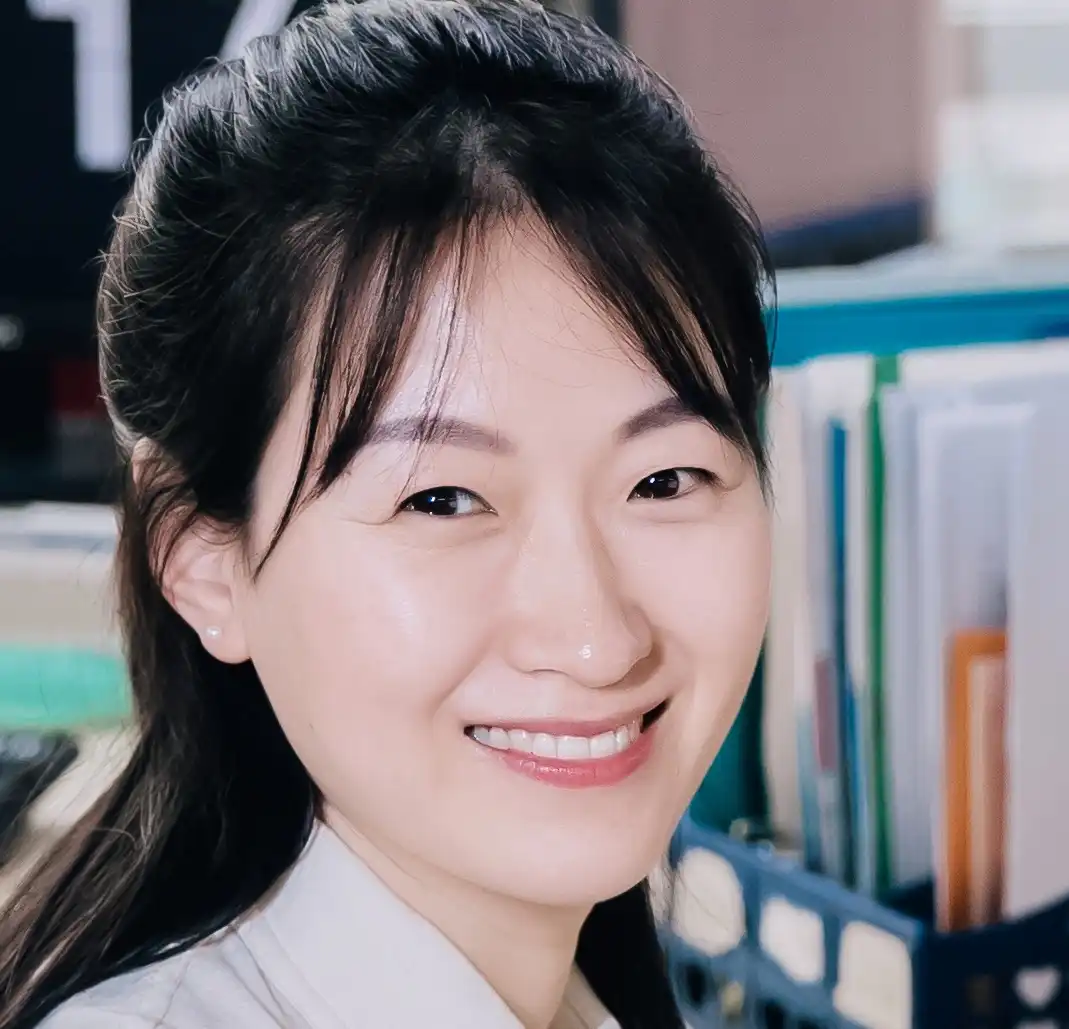
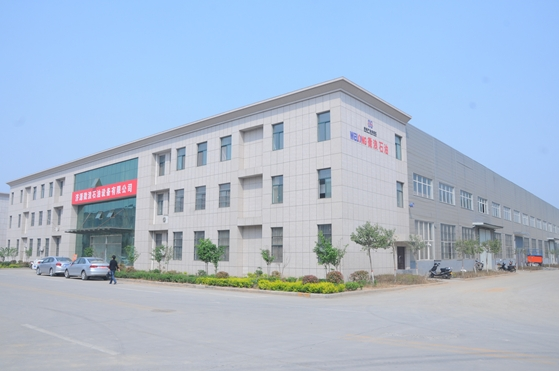
CHINA WELONG - 20+ years manufactuer in oilfield tools