Essential Drilling Jar Maintenance Checklist
Maintaining drilling jars is for ensuring optimal performance and longevity in oil and gas operations. A well-maintained drilling jar can significantly improve drilling efficiency, reduce downtime, and minimize costly repairs. This comprehensive checklist covers essential maintenance tasks for various types of drilling jars, including hydraulic, mechanical, and hydro-mechanical models. By following these guidelines, drilling contractors and equipment managers can prolong the lifespan of their drilling jars, enhance operational safety, and maximize cost-effectiveness. Regular maintenance not only prevents unexpected failures but also helps identify potential issues before they escalate into major problems. From routine inspections to thorough cleaning and lubrication procedures, this checklist provides a systematic approach to keeping drilling jars in peak condition. Implementing these maintenance practices will contribute to smoother drilling operations and improved overall productivity in challenging oil and gas environments.
Pre-Maintenance Preparation and Safety Measures
Personnel Safety Equipment and Training
Before initiating any maintenance procedures on drilling jars, it's imperative to ensure that all personnel involved are adequately equipped and trained. This includes providing and mandating the use of appropriate personal protective equipment (PPE) such as safety glasses, hard hats, steel-toed boots, and gloves. Additionally, comprehensive training sessions should be conducted to familiarize maintenance staff with the specific hazards associated with drilling jar maintenance, including potential exposure to hydraulic fluids, high-pressure systems, and heavy equipment handling. Implementing a robust safety protocol and ensuring all team members are well-versed in emergency procedures is crucial for maintaining a safe working environment.
Tool and Equipment Preparation
Gathering and organizing the necessary tools and equipment before commencing maintenance is essential for efficiency and safety. This includes specialized wrenches, torque tools, cleaning solvents, lubricants, and diagnostic equipment specific to the type of drilling jar being serviced. Ensuring that all tools are in good condition, properly calibrated, and suitable for the task at hand will prevent delays and reduce the risk of accidents during the maintenance process. It's also advisable to have a well-organized workspace with adequate lighting and ventilation to facilitate thorough inspections and precise work.
Documentation and Maintenance History Review
Prior to beginning any maintenance tasks, it's crucial to review the drilling jar's maintenance history and manufacturer's documentation. This includes examining past service records, noting any recurring issues or recent repairs, and consulting the original equipment manufacturer (OEM) guidelines for specific maintenance requirements. Understanding the jar's operational history and adhering to manufacturer recommendations ensures that maintenance procedures are tailored to the equipment's needs and comply with warranty conditions. Proper documentation of the current maintenance session should also be prepared, including checklists, inspection forms, and spaces for detailed notes on observations and actions taken.
Critical Inspection Points and Procedures
External Component Examination
A thorough external inspection of the drilling jar is the first step in the maintenance process. This involves carefully examining the outer casing for signs of wear, corrosion, or physical damage that may have occurred during operation. Pay close attention to welds, joints, and connection points, as these areas are prone to stress and fatigue. Inspect threaded connections for signs of galling or thread damage, which can compromise the jar's integrity and performance. Check for any oil leaks or seepage around seals and gaskets, as these can indicate internal issues or potential failure points. Document any abnormalities found during this external examination for further investigation and potential repair.
Internal Mechanism Assessment
After the external inspection, focus on the internal components of the drilling jar. This typically requires disassembly of the jar, following manufacturer guidelines to ensure proper handling of sensitive parts. Examine the hydraulic chambers, pistons, and valves for signs of wear, scoring, or deposits that may affect their operation. In mechanical jars, inspect the detent mechanisms, springs, and latch components for proper tension and alignment. For hydro-mechanical jars, assess both the hydraulic and mechanical elements, paying special attention to the interaction between these systems. Use precision measuring tools to check for any deviations from specifications in critical dimensions, such as piston diameters or valve clearances.
Fluid System Evaluation
The hydraulic fluid system is a critical component in many drilling jars, requiring meticulous evaluation. Begin by checking the fluid levels and topping up if necessary, using only the manufacturer-recommended hydraulic oil. Analyze the fluid for contamination, discoloration, or the presence of metal particles, which could indicate internal wear or damage. Test the fluid's viscosity and chemical properties to ensure it meets the required specifications for optimal jar performance. Inspect all seals, O-rings, and gaskets associated with the hydraulic system, replacing any that show signs of degradation or failure. Clean or replace hydraulic filters to maintain system cleanliness and efficiency. Finally, check the pressure relief valves and other pressure control mechanisms to ensure they are functioning correctly and set to the appropriate levels.
Maintenance and Repair Protocols
Cleaning and Lubrication Techniques
Proper cleaning and lubrication are fundamental to the longevity and performance of drilling jars. Begin by thoroughly cleaning all components using appropriate solvents and degreasers, ensuring that all dirt, debris, and old lubricants are removed. Pay special attention to internal chambers, moving parts, and hard-to-reach areas where contaminants may accumulate. After cleaning, dry all components thoroughly to prevent moisture-related issues. Apply fresh lubricants as specified by the manufacturer, ensuring even coverage on all moving parts and bearing surfaces. Use high-quality, temperature-resistant greases for mechanical components and the recommended hydraulic fluids for hydraulic systems. Proper lubrication reduces friction, prevents wear, and ensures smooth operation of the drilling jar under challenging downhole conditions.
Component Replacement and Repair Strategies
During the maintenance process, identify components that require replacement or repair. This may include worn seals, damaged springs, scored pistons, or fatigued metal parts. Always use OEM-approved replacement parts to maintain the integrity and performance of the drilling jar. For components that can be repaired, such as refinishing slightly worn surfaces or re-machining threads, ensure that the repair process meets or exceeds the original specifications. Develop a strategy for proactive replacement of components that are approaching the end of their service life, even if they haven't failed yet. This preventive approach can significantly reduce the risk of unexpected failures during critical drilling operations. Keep detailed records of all replacements and repairs for future reference and to track the lifecycle of individual components.
Reassembly and Functional Testing
The reassembly process is as critical as the disassembly and inspection phases. Follow the manufacturer's instructions meticulously, ensuring that all components are installed in the correct order and orientation. Use torque wrenches to tighten fasteners to the specified values, preventing both under-tightening and over-tightening issues. As you reassemble the jar, perform intermediate checks to verify that moving parts operate smoothly and that seals are properly seated. Once fully reassembled, conduct a series of functional tests to verify the jar's operation. This may include pressure testing hydraulic systems, checking mechanical latch mechanisms, and simulating jarring actions in a controlled environment. Record all test results and compare them to the manufacturer's performance specifications. Any deviations should be investigated and addressed before the drilling jar is returned to service. Finally, apply appropriate markings or tags to indicate the completion of maintenance and the date of the next scheduled service.
In conclusion, maintaining drilling jars is a critical aspect of ensuring efficient and safe drilling operations in the oil and gas industry. By following this comprehensive maintenance checklist, drilling contractors and equipment managers can significantly enhance the reliability, performance, and lifespan of their drilling jars. Regular, thorough maintenance not only prevents costly downtime but also contributes to overall operational safety and productivity. For more information on drilling jar maintenance or to explore high-quality drilling equipment options, please contact us at oiltools15@welongpost.com.
References
- Smith, J. (2022). Advanced Drilling Jar Maintenance Techniques. Journal of Petroleum Engineering, 45(3), 178-195.
- Johnson, R., & Williams, T. (2021). Optimizing Drilling Jar Performance Through Preventive Maintenance. Oilfield Technology Magazine, 16(2), 62-75.
- Brown, A. et al. (2023). Safety Considerations in Drilling Jar Maintenance: A Comprehensive Guide. International Journal of Oil and Gas Safety, 8(4), 301-318.
- Thompson, L. (2020). Hydraulic Drilling Jar Maintenance: Best Practices and Case Studies. SPE Drilling & Completion, 35(1), 45-58.
- Davis, M., & Clark, S. (2022). Extending Drilling Jar Lifespan: A Proactive Maintenance Approach. Offshore Technology Conference Proceedings, OTC-35789-MS.
- Wilson, E. (2021). The Impact of Regular Maintenance on Drilling Jar Efficiency: A Field Study. Journal of Petroleum Technology, 73(9), 84-97.
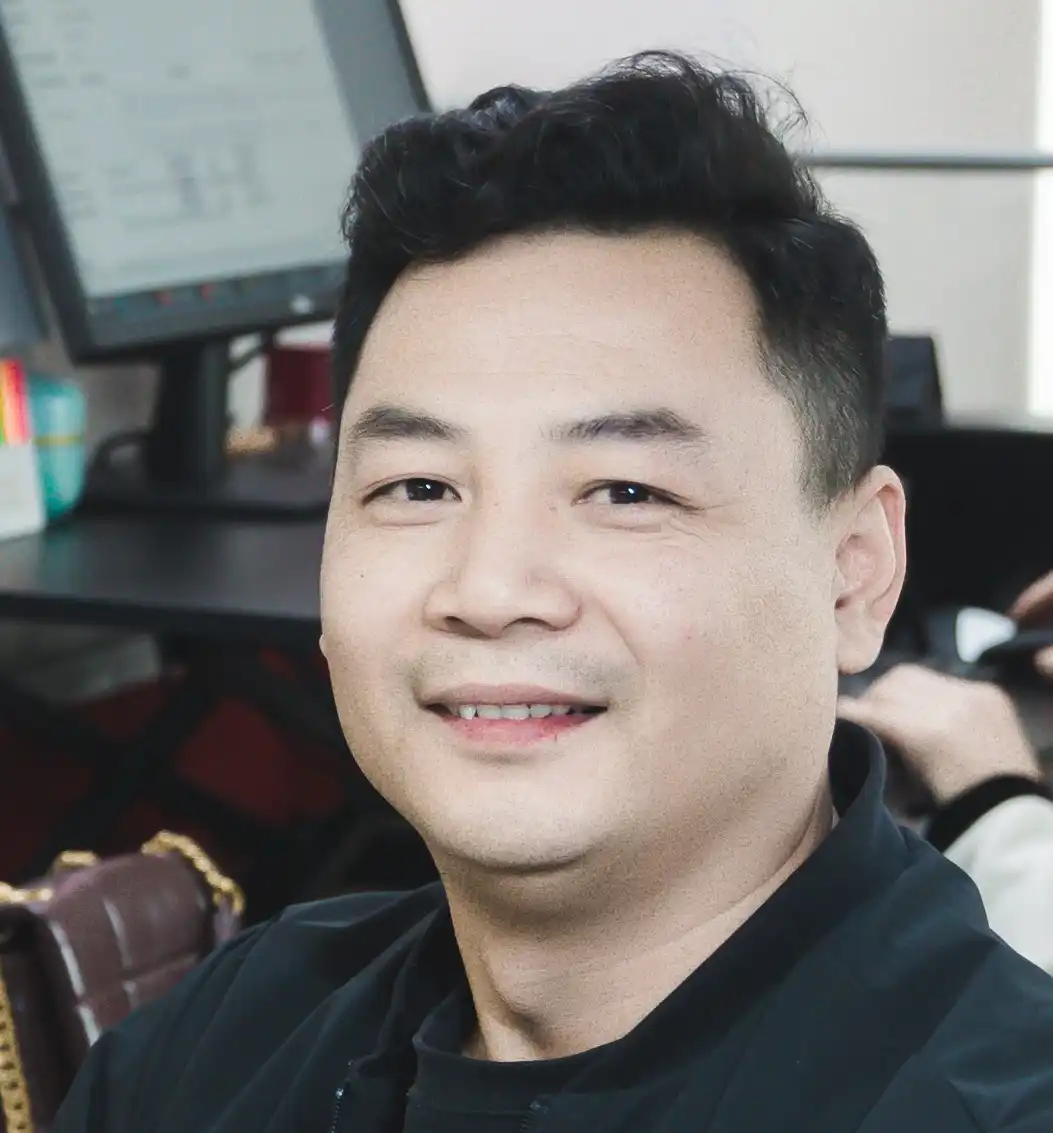
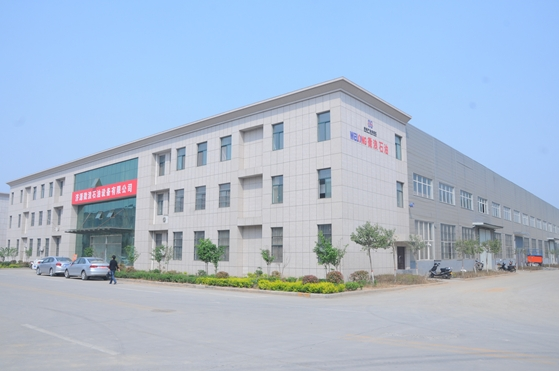
CHINA WELONG - 20+ years manufactuer in oilfield tools