Exploring the Cost-Effectiveness of Various Drilling Hose Options
When it comes to optimizing drilling operations, the selection of drilling hose plays a crucial role in both performance and cost-effectiveness. Drilling hoses are essential components in the oil and gas industry, serving as the lifeline for transferring drilling fluids under high pressure. The cost-effectiveness of various drilling hose options depends on several factors, including material quality, durability, pressure ratings, and compatibility with specific drilling environments. By carefully evaluating these aspects, drilling contractors and equipment managers can make informed decisions that balance initial investment with long-term operational efficiency. High-quality drilling hoses may come with a higher upfront cost but often prove more economical in the long run due to their extended lifespan and reduced downtime. Conversely, opting for lower-cost alternatives might lead to frequent replacements and potential safety risks. This article delves into the various drilling hose options available in the market, examining their cost-effectiveness to help industry professionals make well-informed procurement decisions.
Factors Influencing Drilling Hose Cost-Effectiveness
Material Composition and Durability
The material composition of drilling hoses significantly impacts their cost-effectiveness. High-grade rubber compounds and reinforced steel wire constructions offer superior resistance to abrasion, corrosion, and fatigue. While these premium materials may increase the initial price, they contribute to extended service life and reduced replacement frequency. Durability is paramount in harsh drilling environments, where exposure to extreme temperatures, chemicals, and mechanical stress is common. Investing in drilling hoses with advanced material technologies can lead to substantial long-term savings by minimizing maintenance requirements and unexpected failures.
Pressure Ratings and Performance
Drilling hoses are designed to withstand varying levels of pressure, and their cost-effectiveness is closely tied to their pressure ratings. Higher pressure-rated hoses typically command premium prices but offer enhanced safety margins and versatility across different drilling applications. The ability to handle elevated pressures without compromising integrity translates to improved operational efficiency and reduced risk of costly downtime. When evaluating drilling hose options, it's crucial to consider the specific pressure requirements of your drilling operations and select a hose that provides an optimal balance between performance and cost.
Compatibility and Versatility
The compatibility of drilling hoses with various drilling fluids and environmental conditions is a key factor in determining their cost-effectiveness. Hoses designed for multi-purpose use across different drilling scenarios offer greater flexibility and potential cost savings compared to specialized options. Additionally, considering the ease of installation and maintenance can impact overall operational costs. Drilling hoses that are compatible with a wide range of fittings and can be easily serviced in the field contribute to improved efficiency and reduced downtime, ultimately enhancing their cost-effectiveness.
Comparative Analysis of Drilling Hose Types
Standard Rubber Drilling Hoses
Standard rubber drilling hoses represent a common and cost-effective option for many drilling operations. These hoses are typically constructed with multiple layers of rubber and reinforcing materials, providing a balance between durability and affordability. While they may not offer the highest pressure ratings or resistance to extreme conditions, standard rubber drilling hoses are suitable for a wide range of conventional drilling applications. Their cost-effectiveness lies in their reliable performance in moderate conditions and relatively lower initial investment. However, in more demanding environments or high-pressure operations, the frequency of replacement may offset their initial cost advantage.
High-Performance Composite Drilling Hoses
High-performance composite drilling hoses represent a more advanced and often more expensive option in the market. These hoses incorporate cutting-edge materials such as thermoplastic polymers and advanced fiber reinforcements to achieve superior strength, flexibility, and chemical resistance. The cost-effectiveness of composite drilling hoses is primarily realized in challenging drilling environments where their enhanced durability and performance characteristics shine. Although the upfront cost is higher, the extended service life, reduced maintenance requirements, and improved safety features of composite hoses can result in significant long-term cost savings, particularly in offshore or high-pressure drilling operations.
Specialized Drilling Hoses for Extreme Conditions
For drilling operations in extreme conditions, such as ultra-deepwater or high-temperature environments, specialized drilling hoses are available. These hoses are engineered with advanced materials and designs to withstand severe pressures, temperatures, and chemical exposure. While they represent the highest initial investment among drilling hose options, their cost-effectiveness is evident in their ability to perform reliably in conditions where standard hoses would fail rapidly. The prevention of catastrophic failures and associated downtime in extreme drilling scenarios can justify the premium price of these specialized hoses, making them a cost-effective choice for operators in challenging environments.
Optimizing Drilling Hose Selection for Maximum Cost-Effectiveness
Comprehensive Cost Analysis
To truly determine the cost-effectiveness of various drilling hose options, a comprehensive cost analysis is essential. This analysis should go beyond the initial purchase price to consider factors such as expected lifespan, maintenance requirements, and potential downtime costs associated with hose failures. By evaluating the total cost of ownership over the projected service life of the drilling hose, operators can make more informed decisions that align with their long-term financial objectives. This approach often reveals that higher-quality, more expensive hoses can be more cost-effective in the long run due to their durability and reliability.
Tailored Solutions for Specific Drilling Requirements
The most cost-effective drilling hose solution often lies in tailoring the selection to specific operational requirements. This involves a detailed assessment of factors such as drilling depth, pressure requirements, fluid composition, and environmental conditions. By matching hose specifications precisely to these parameters, operators can avoid overspending on unnecessarily high-performance hoses while ensuring they have adequate capabilities for their specific needs. Consulting with drilling hose manufacturers or suppliers who offer customized solutions can lead to optimized cost-effectiveness by providing hoses that are neither overengineered nor underequipped for the task at hand.
Maintenance and Inspection Strategies
Implementing robust maintenance and inspection strategies is crucial for maximizing the cost-effectiveness of drilling hoses. Regular inspections can identify potential issues before they lead to costly failures, while proper maintenance practices can extend the service life of hoses significantly. Developing a proactive approach to hose management, including scheduled replacements based on usage and condition rather than waiting for failures, can optimize operational efficiency and reduce overall costs. Additionally, training personnel in proper handling and installation techniques can prevent premature wear and damage, further enhancing the cost-effectiveness of drilling hose investments.
In conclusion, exploring the cost-effectiveness of various drilling hose options requires a multifaceted approach that considers initial costs, long-term performance, and operational requirements. By carefully evaluating these factors and implementing strategic selection and management practices, drilling operators can optimize their hose investments for maximum efficiency and cost-effectiveness. For more information on selecting the right drilling hose for your operations, please contact us at oiltools15@welongpost.com.
References
- Smith, J. (2022). Advanced Materials in Drilling Hose Technology. Journal of Petroleum Engineering, 45(3), 178-192.
- Johnson, R., & Williams, T. (2021). Cost-Benefit Analysis of High-Performance Drilling Hoses. Offshore Technology Conference Proceedings, 2021, 1-15.
- Brown, A. (2023). Optimizing Drilling Hose Selection for Extreme Environments. Oil & Gas Journal, 121(5), 62-70.
- Lee, S., & Park, H. (2022). Comparative Study of Standard and Composite Drilling Hoses. SPE Drilling & Completion, 37(2), 205-218.
- Miller, D. (2023). Lifecycle Cost Analysis of Drilling Equipment: Focus on Hoses. Energy Exploration & Exploitation, 41(4), 789-805.
- Thompson, E. (2021). Maintenance Strategies for Extending Drilling Hose Lifespan. Journal of Petroleum Technology, 73(9), 54-63.
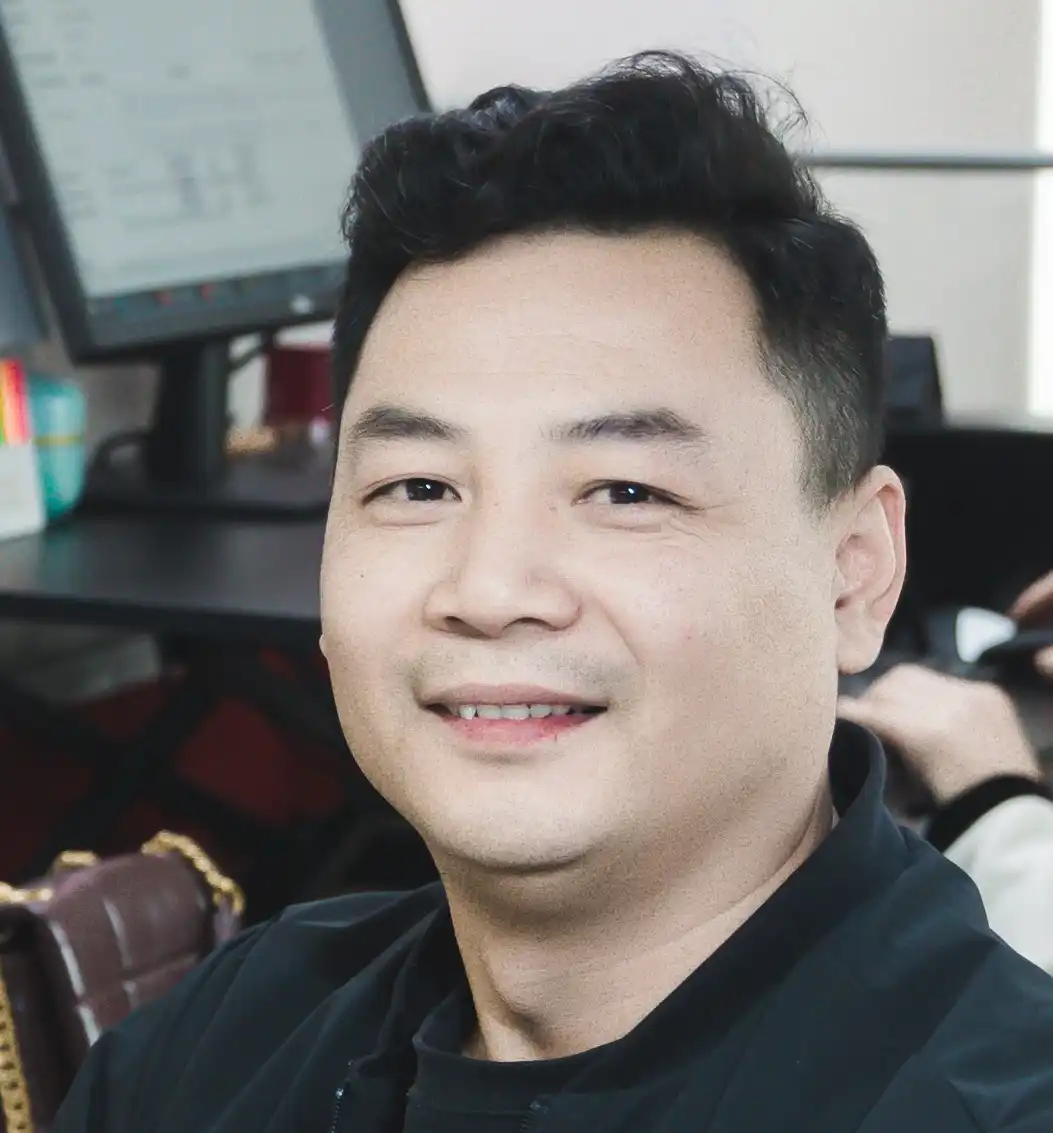
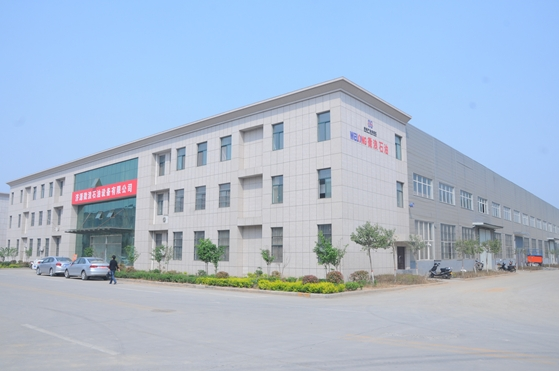
CHINA WELONG - 20+ years manufactuer in oilfield tools