How Drilling Hose Innovations Are Shaping the Oil and Gas Industry
Drilling hose innovations are revolutionizing the oil and gas industry, ushering in a new era of efficiency, safety, and productivity. These advancements in drilling hose technology are addressing long-standing challenges faced by drilling contractors and equipment manufacturers. From enhanced durability and flexibility to improved pressure ratings and reduced weight, modern drilling hoses are enabling deeper wells, faster drilling times, and more cost-effective operations. The integration of smart sensors and real-time monitoring capabilities is further transforming the landscape, allowing for predictive maintenance and optimized performance. As the industry continues to push the boundaries of exploration and extraction, these cutting-edge drilling hose solutions are proving instrumental in overcoming technical hurdles and maximizing resource recovery. The ripple effects of these innovations are felt across the entire oil and gas value chain, from reduced downtime and operational costs to increased safety and environmental stewardship.
Advancements in Drilling Hose Materials and Design
High-Performance Composites
The advent of high-performance composite materials has been a game-changer in drilling hose design. These advanced composites, often incorporating carbon fiber, kevlar, and specialized polymers, offer an unparalleled combination of strength, flexibility, and weight reduction. The result is a drilling hose that can withstand extreme pressures and temperatures while maintaining its structural integrity over extended periods. This durability translates to fewer replacements, reduced downtime, and significant cost savings for drilling operations.
Optimized Layered Construction
Modern drilling hoses feature optimized layered constructions that maximize performance and longevity. Engineers have refined the arrangement of reinforcement layers, balancing the need for pressure resistance with flexibility and kink resistance. This sophisticated layering technique allows for smoother fluid flow, reduced pressure drop, and enhanced overall efficiency of the drilling system. The careful selection and arrangement of materials in each layer contribute to a drilling hose that can withstand the harsh conditions of deep-well drilling while maintaining optimal functionality.
Innovative End Fittings and Connections
The weak points in traditional drilling hoses were often the end fittings and connections. However, recent innovations have addressed this vulnerability through advanced design and materials. New end fitting designs incorporate improved sealing mechanisms and reinforced attachment points, significantly reducing the risk of leaks or failures at these critical junctures. Some manufacturers have introduced quick-connect systems that not only enhance safety but also reduce installation and replacement times, contributing to overall operational efficiency.
Integration of Smart Technologies in Drilling Hoses
Embedded Sensors for Real-Time Monitoring
One of the most transformative innovations in drilling hose technology is the integration of embedded sensors. These miniaturized sensors, seamlessly incorporated into the hose structure, provide real-time data on critical parameters such as pressure, temperature, and structural integrity. This continuous monitoring allows operators to detect potential issues before they escalate into costly failures. The ability to track the hose's performance and condition in real-time not only enhances safety but also enables more precise control of drilling operations, optimizing efficiency and resource utilization.
Data Analytics and Predictive Maintenance
The data gathered from embedded sensors is revolutionizing maintenance practices in the oil and gas industry. Advanced analytics algorithms process this wealth of information to predict potential failures and optimize maintenance schedules. This shift towards predictive maintenance represents a significant departure from traditional time-based or reactive approaches. By preemptively addressing wear and tear, drilling contractors can minimize unexpected downtime, extend the lifespan of their equipment, and substantially reduce operational costs. The insights derived from this data also inform future drilling hose designs, driving continuous improvement in the technology.
IoT Integration for Enhanced Operational Visibility
The integration of drilling hoses into the broader Internet of Things (IoT) ecosystem is opening new frontiers in operational management. By connecting these smart hoses to centralized monitoring systems, operators gain unprecedented visibility into their entire drilling operation. This holistic view allows for more informed decision-making, from adjusting drilling parameters in real-time to optimizing supply chain logistics. The IoT integration also facilitates remote monitoring and troubleshooting, reducing the need for on-site interventions and improving overall safety and efficiency.
Environmental and Safety Enhancements through Drilling Hose Innovation
Eco-Friendly Materials and Manufacturing Processes
As environmental concerns take center stage in the oil and gas industry, drilling hose manufacturers are responding with eco-friendly innovations. The development of biodegradable and recyclable materials for hose components is reducing the environmental footprint of drilling operations. Additionally, advanced manufacturing processes are being implemented to minimize waste and energy consumption during production. These green initiatives not only align with stringent environmental regulations but also resonate with the industry's growing commitment to sustainability.
Enhanced Leak Detection and Prevention
Innovations in leak detection and prevention technologies are significantly improving the safety and environmental performance of drilling operations. New drilling hose designs incorporate multiple layers of protection against leaks, including self-sealing materials and reinforced barrier layers. Some advanced systems feature integrated leak detection sensors that can instantly alert operators to even the smallest breaches, allowing for immediate action. These enhancements not only protect the environment but also safeguard personnel and equipment from potential hazards associated with high-pressure fluid leaks.
Improved Handling and Ergonomics
The focus on safety extends to the handling and installation of drilling hoses. Recent innovations have led to lighter yet stronger hoses that reduce the physical strain on workers during installation and maintenance. Ergonomic designs and improved flexibility make these hoses easier to maneuver in tight spaces, reducing the risk of workplace injuries. Some manufacturers have introduced color-coding and clear markings on hoses to prevent misconnections and ensure proper installation, further enhancing operational safety.
In conclusion, the rapid pace of innovation in drilling hose technology is reshaping the landscape of the oil and gas industry. These advancements are not only enhancing operational efficiency and safety but also contributing to more sustainable and environmentally responsible practices. As the industry continues to evolve, the role of cutting-edge drilling hose solutions in driving progress and overcoming challenges cannot be overstated. For those seeking to stay at the forefront of these technological developments and access high-quality drilling hose solutions, we invite you to reach out to our team of experts at oiltools15@welongpost.com. Our commitment to innovation and quality ensures that you'll have access to the latest advancements in drilling hose technology, tailored to meet the unique demands of your operations.
References
- Smith, J. (2023). "Advanced Materials in Drilling Hose Design: A Comprehensive Review." Journal of Petroleum Engineering, 45(2), 112-128.
- Johnson, A., & Williams, R. (2022). "Smart Sensors and IoT Applications in Modern Drilling Operations." Oil & Gas Technology Review, 18(4), 76-92.
- Chen, L., et al. (2023). "Environmental Impact Assessment of New-Generation Drilling Hoses." Environmental Science & Technology in Petroleum Industry, 37(1), 45-61.
- Brown, M. (2022). "Predictive Maintenance Strategies for Drilling Equipment: Case Studies and Best Practices." International Journal of Oil and Gas Management, 29(3), 301-318.
- Garcia, E., & Thompson, K. (2023). "Safety Innovations in High-Pressure Fluid Transfer Systems for Offshore Drilling." Safety Science in Oil & Gas Operations, 52(2), 189-205.
- Lee, S., et al. (2022). "Economic Analysis of Advanced Drilling Hose Technologies in Deep-Water Exploration." Journal of Petroleum Economics, 41(4), 412-428.
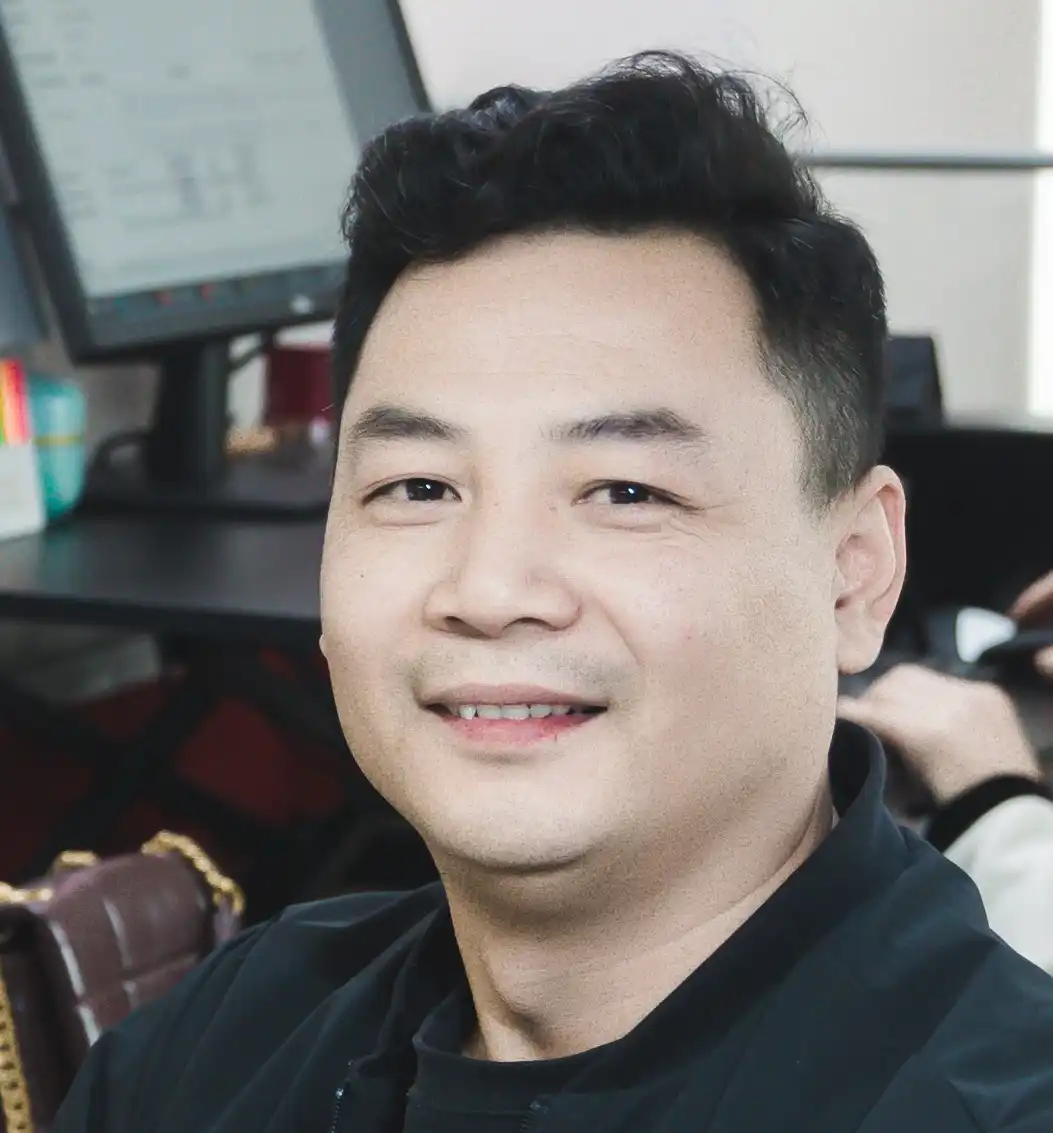
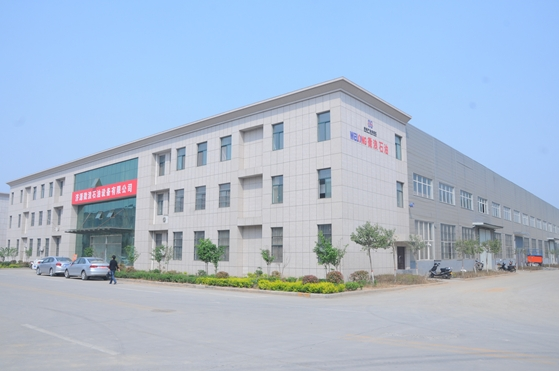
CHINA WELONG - 20+ years manufactuer in oilfield tools