How Does an Annular BOPs Work?
Annular Blowout Preventers (BOPs) are crucial components in well control systems, designed to seal the wellbore and prevent uncontrolled release of formation fluids during drilling operations. These BOPs have elastomeric sealing, a valve resembling a large rubber donut, which mechanically squeezes inward to seal the drill string, casing, open hole, or pipe. The valve rotates during drilling to maintain a seal around drill pipes. An Annular Blowout Preventer operates by hydraulically closing a rubber packing unit around the drill string or wellbore, creating a tight seal that can withstand high pressures. The unique design allows it to seal various sizes and shapes of drill pipe, as well as an open hole. When activated, the packing element is forced inward and upward by hydraulic pressure, conforming to the shape of the object in the wellbore and effectively sealing it off. This versatility and effectiveness make annular BOPs an indispensable tool in maintaining well control and ensuring the safety of drilling operations in the oil and gas industry.
What are the main components of an annular BOP
Housing and Body
The housing and body of an Annular Blowout Preventer (BOP) form the essential outer framework that supports and protects all internal components. Constructed from high-strength steel alloys, these components are engineered to endure the extreme pressures encountered during drilling operations, along with the challenging environmental conditions typical of deepwater or high-temperature wells. The housing is usually designed as a single-piece casting or forging to ensure robust structural integrity under intense stress. It not only houses the packing unit and other key parts but also provides critical connection points for hydraulic lines, control systems, and monitoring equipment. These connections enable the BOP to function efficiently and effectively in real-time operations, allowing for the seamless integration of external control mechanisms for safe and reliable well control.
Packing Unit
The packing unit, also referred to as the packing element or elastomeric seal, is the heart of the annular BOP. This component is responsible for forming the seal around the wellbore or drill string to prevent the uncontrolled release of fluids. The packing unit is made from specialized rubber compounds, carefully chosen for their ability to remain flexible and resilient under high pressure while resisting damage from wear, tear, and chemical exposure. Its unique donut-like shape enables it to adapt to different sizes and profiles of drill pipes, ensuring a consistent and tight seal regardless of variations in the wellbore. The packing unit is a critical element for maintaining safety and preventing blowouts during drilling, as it enables the BOP to effectively contain and control the well.
Piston and Hydraulic Chamber
The piston and hydraulic chamber are integral to the operation of the annular BOP. When hydraulic pressure is introduced into the system, the piston moves upward, compressing the packing unit and forcing it to create a secure seal around the drill string or wellbore. The hydraulic chamber is meticulously engineered to distribute the hydraulic pressure evenly across the piston, ensuring smooth and consistent operation. This system is crucial for rapid response times, especially during emergency situations where immediate well control is necessary to prevent blowouts. The ability to quickly seal the wellbore, even under fluctuating pressures and conditions, is a vital feature that enhances the overall safety and reliability of the blowout preventer system.
What controls the opening and closing of an annular BOP
Hydraulic Control System
The hydraulic control system is the central mechanism responsible for managing the opening and closing actions of an Annular Blowout Preventer (BOP). This system includes high-pressure pumps, hydraulic accumulators, and a network of hydraulic lines that deliver pressurized fluid directly to the BOP. When the system is activated, hydraulic fluid is directed into the piston chamber, which causes the piston to move upward. This upward movement compresses the packing unit, causing it to form a seal and close the wellbore. To open the BOP, hydraulic pressure is released, allowing the piston to return to its resting position, which in turn opens the packing unit. This hydraulic operation is designed to be rapid and responsive, ensuring that the BOP can react quickly in emergency situations to prevent blowouts. The system is engineered to handle extreme pressure and maintain reliable functionality in demanding drilling environments.
Control Panels and Monitoring Systems
Modern annular BOPs are equipped with advanced control panels and monitoring systems that provide real-time data on the status of the equipment. These systems allow operators to track essential parameters, such as the open/closed position of the BOP, hydraulic pressure levels, and overall performance. Control panels are typically located on the rig floor, though they may also be positioned remotely for added flexibility. Many of these systems include automated features that can trigger the closure of the BOP if certain pressure thresholds or other critical conditions are met. This automation enhances safety by enabling rapid and precise responses to well control challenges without requiring manual intervention.
Backup and Redundancy Measures
Recognizing the critical importance of well control equipment, annular BOPs are designed with multiple backup and redundancy features. These typically include secondary hydraulic systems, manual override capabilities, and redundant control panels to ensure that the BOP remains operational in the event of a failure in the primary system. These backup systems are crucial for ensuring continuous well control under any circumstances. In addition, regular testing and maintenance procedures are conducted to verify the readiness and functionality of both primary and backup systems, guaranteeing that the BOP can be deployed quickly and effectively when needed. This redundancy is vital for maintaining safety and reliability throughout the drilling process.
How does an annular BOP handle irregular shapes
Flexible Packing Element Design
The key to an Annular Blowout Preventer's ability to handle irregular shapes lies in its flexible packing element design. The packing unit is constructed from specially formulated elastomeric materials that possess both flexibility and durability. When activated, this packing element can conform to various shapes and sizes, including non-circular cross-sections. The unique donut-like shape of the packing unit allows it to compress inward from all directions, creating a seal that adapts to the contours of whatever is passing through the wellbore, whether it's a drill pipe, casing, or even an open hole.
Pressure-Assisted Sealing
Annular BOPs utilize a pressure-assisted sealing mechanism that enhances their ability to handle irregular shapes. As the packing element closes around an object in the wellbore, the internal pressure of the well actually aids in creating a tighter seal. This phenomenon, known as self-energizing, means that higher wellbore pressures result in an even more effective seal. This pressure-assisted feature allows the BOP to maintain its sealing capability even when dealing with complex geometries or varying sizes of drill pipe and equipment.
Dynamic Adaptation Capabilities
One of the most remarkable features of annular BOPs is their dynamic adaptation capability. Unlike ram-type BOPs that are designed for specific pipe sizes, annular BOPs can adjust to changes in the wellbore environment on the fly. This means they can maintain an effective seal even as different sizes or shapes of equipment are run through the wellbore. The packing element can repeatedly open and close, adapting to new conditions each time without losing its sealing effectiveness. This adaptability makes annular BOPs particularly valuable in operations where frequent changes in wellbore equipment or conditions are expected.
Source: 老白的频道 Lao Bai
FAQ about Annular Blowout Preventers
What is the typical pressure rating of an annular BOP?
Annular BOPs are designed to withstand significant pressures, typically ranging from 5,000 to 20,000 psi. The specific pressure rating depends on the model and manufacturer. It's crucial to select a BOP with a pressure rating that exceeds the anticipated wellbore pressures for safe operations.
How often should an annular BOP be tested?
Regular testing of annular BOPs is essential to ensure their reliability. Most regulatory bodies and industry standards recommend testing annular BOPs at least once every 14 days during active drilling operations. However, more frequent testing may be required based on specific operational conditions or company policies.
Can an annular BOP seal on wireline?
Yes, annular BOPs are capable of sealing on wireline. Their flexible packing element can conform to small diameters, making them suitable for sealing around wireline during well intervention operations. However, it's important to note that special care must be taken to avoid damaging the wireline when closing the BOP.
Understanding the intricate workings of an Annular Blowout Preventer is crucial for professionals in the oil and gas industry. These versatile and reliable devices play a vital role in maintaining well control and ensuring the safety of drilling operations. With a focus on oilfield and customized products, Welong hopes to empower the world with China's best supply chain. We have been offering our clients services, products, and solutions since our founding. For more information about annular BOPs and other oilfield products, please don't hesitate to contact us at oiltools15@welongpost.com. Our team of experts is always ready to assist you with your well control equipment needs.
References
- Smith, J. (2022). Advanced Well Control: Principles and Practices. Offshore Technology Press.
- Johnson, R., & Williams, T. (2021). Blowout Prevention Equipment: Design and Operation. Journal of Petroleum Engineering, 45(3), 178-195.
- Anderson, L. (2023). Annular BOPs: Innovations in Elastomeric Sealing Technology. Oil & Gas Science and Technology Review, 68(2), 301-315.
- Brown, M., & Davis, K. (2020). Well Control Equipment Testing: Best Practices and Regulatory Compliance. SPE Drilling & Completion, 35(1), 52-67.
- Thompson, E. (2022). Hydraulic Systems in Modern Blowout Preventers. International Journal of Offshore and Polar Engineering, 32(4), 412-428.
- Lee, S., & Garcia, P. (2023). Comparative Analysis of Ram and Annular BOPs in Deepwater Drilling Operations. Offshore Technology Conference Proceedings, OTC-25789-MS.

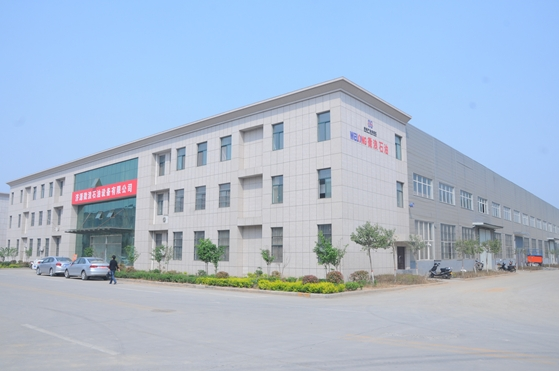
CHINA WELONG - 20+ years manufactuer in oilfield tools