Learn What an Annular Blowout Preventer
An Annular Blowout Preventer (ABP) is a critical safety device used in the oil and gas industry to prevent uncontrolled releases of formation fluids during drilling operations. This essential component of well control equipment plays a vital role in maintaining safety, protecting the environment, and preserving valuable resources. ABPs are designed to seal the wellbore quickly and effectively, containing pressure and preventing potential blowouts that could lead to catastrophic consequences. Understanding the function, operation, and advantages of annular blowout preventers is crucial for anyone involved in drilling operations, from rig operators to purchasing managers. In this comprehensive guide, we'll explore the intricacies of ABPs, their working principles, and the benefits they offer to the oil and gas industry.
What is an Annular Blowout Preventer
Definition and Purpose
An annular blowout preventer is a large valve designed to seal, control, and monitor oil and gas wells. These BOPs have elastomeric sealing, a valve resembling a large rubber donut, which mechanically squeezes inward to seal the drill string, casing, open hole, or pipe. This unique design allows for versatile and efficient well control, making ABPs an indispensable tool in modern drilling operations. ABPs are crucial components of a Blowout Preventer (BOP) stack, which is a collection of safety devices installed at the wellhead to manage and control pressure.
Components and Construction
The main components of an ABP include:
- Housing: The outer shell that contains and supports the internal components
- Piston: A hydraulically actuated component that applies force to the packing unit
- Packing unit: An elastomeric element that forms the seal around the drill pipe or wellbore
- Operating system: Hydraulic controls that activate and deactivate the ABP
The unique design of the packing unit, often referred to as a "donut" due to its shape, allows it to conform to various sizes and shapes of drill pipe, ensuring a reliable seal under diverse conditions.
Types and Sizes
ABPs come in various sizes and pressure ratings to accommodate different wellbore diameters and operating conditions. Common sizes range from 7-1/16" to 21-1/4" bore, with working pressures typically between 2,000 and 20,000 psi. The choice of ABP depends on factors such as well depth, expected formation pressures, and drilling program requirements.
How an Annular Blowout Preventer Works
Activation Mechanism
The activation mechanism of an Annular Blowout Preventer (ABP) is a critical function in ensuring effective well control during drilling operations. When activated, hydraulic pressure is directed to a piston within the system. This hydraulic force moves the piston, which, in turn, compresses the packing unit inside the BOP. The compression of the packing unit causes it to expand inward, where it forms a tight and reliable seal around the drill pipe, casing, or even an open hole. This sealing action occurs very quickly, often within seconds, allowing for a rapid response in situations where well control is needed, such as during a kick or blowout event. The speed and efficiency of this mechanism are crucial in preventing the uncontrolled release of gas or fluids from the wellbore, thus protecting the safety of the rig, personnel, and surrounding environment.
Sealing Process
One of the standout features of the ABP is its elastomeric packing unit, which is designed for exceptional flexibility and adaptability. This packing unit can conform to a wide range of shapes and sizes, whether it is around a drill pipe, casing, or even an open hole. This versatility ensures that the ABP can maintain an effective seal in diverse well conditions. The elastomeric material used in the packing unit provides the necessary flexibility to adapt to slight variations in the shape or size of the object it is sealing. Moreover, the packing unit is engineered to maintain a tight seal even if the drill pipe is in motion, such as during rotation or axial movement. This capability allows the ABP to offer continuous protection throughout the drilling process, without needing to stop or pause operations. The ability to create a reliable seal, regardless of pipe movement, is crucial for maintaining well control and preventing blowouts during drilling.
Integration with BOP Stack
Annular Blowout Preventers (ABPs) are typically installed at the top of the BOP stack, positioned above the ram-type preventers. This placement allows the ABP to serve as the primary method for controlling the well in many scenarios. The ram-type preventers, positioned below, are used as secondary or backup systems, designed to handle more severe or emergency situations where the ABP alone may not suffice. The integration of ABPs within the overall blowout preventer stack creates a multi-layered approach to well control, ensuring both redundancy and reliability. This design allows for greater flexibility in responding to different wellbore conditions, with the ABP providing a fast-acting primary response and the ram preventers offering additional protection when needed. The combined system enhances the safety of the drilling operation, offering multiple lines of defense against potential blowouts and kick events.
Advantages of Annular Blowout Preventers
Versatility and Adaptability
One of the standout features of Annular Blowout Preventers (ABPs) is their remarkable versatility and adaptability. ABPs are designed to seal around a wide range of pipe sizes, including both large and small diameters. This capability significantly reduces the need for multiple ram-type preventers, each tailored to a specific pipe size. By eliminating the requirement for various preventers, the ABP simplifies the blowout preventer (BOP) stack design, leading to a more streamlined and cost-effective solution. In addition to accommodating different pipe sizes, ABPs have the unique ability to form a seal around irregular shapes or even in open hole conditions, where no pipe is present. This makes the ABP an invaluable tool in maintaining well control in a variety of situations, enhancing its operational flexibility. Whether the wellbore is empty or filled with a specific tool, the ABP ensures a reliable seal, providing continued safety and efficiency. This adaptability significantly increases the overall utility of the BOP system, as it can be employed in a broader range of drilling scenarios, thus reducing the need for additional equipment.
Quick Response Time
Another key advantage of ABPs is their ability to be activated quickly, typically within seconds, in response to a well control issue, such as a kick. This rapid activation is essential to preventing small well control problems from escalating into a full-blown blowout, which can have catastrophic consequences. The speed with which the ABP responds minimizes the risk of uncontrolled pressure surges, which could cause significant damage to both the well and the surrounding environment. The swift sealing action of the ABP also allows operators to regain control of the well faster, reducing the likelihood of operational downtime. In turn, this contributes to overall safety, protecting the crew, the rig, and the environment. The quick response of ABPs plays a crucial role in maintaining efficient and safe drilling operations, ensuring that any potential hazards are addressed before they can grow into more dangerous situations.
Reduced Wear and Maintenance
When compared to ram-type preventers, ABPs generally experience less wear and tear during normal operations. The elastomeric packing unit at the core of the ABP is designed to be resilient, capable of withstanding multiple actuations without significant degradation. This durability ensures that the ABP remains functional for longer periods, reducing the frequency of maintenance and part replacement. Less wear translates to lower operational costs, as there is less need for expensive repairs and component changes. Moreover, the reduced wear of ABPs increases the overall reliability of the system, as it minimizes the chances of malfunction during critical moments. The lower maintenance requirements also ensure that the BOP system remains in peak working condition, further enhancing the safety and efficiency of the drilling operation. Over time, this durability can result in significant cost savings for operators, as the ABP continues to perform at a high level without frequent servicing.
Source: 老白的频道 Lao Bai
FAQ about Annular Blowout Preventers
What is the lifespan of an Annular Blowout Preventer?
The lifespan of an ABP can vary depending on factors such as usage frequency, operating conditions, and maintenance practices. With proper care and regular inspections, an ABP can last for several years before requiring major overhaul or replacement. However, critical components like the packing unit may need more frequent replacement to ensure optimal performance.
How often should Annular Blowout Preventers be tested?
Testing frequency for ABPs is typically governed by industry standards and regulatory requirements. In general, ABPs should be function tested at least once per week and pressure tested every 14 days or as specified by local regulations. More frequent testing may be necessary in high-risk environments or during critical operations.
Can Annular Blowout Preventers be used in subsea applications?
Yes, ABPs are commonly used in subsea BOP stacks for offshore drilling operations. Subsea ABPs are designed to withstand the harsh marine environment and high pressures associated with deepwater drilling. These specialized ABPs often incorporate additional features such as ROV intervention capabilities and enhanced sealing mechanisms to ensure reliable performance in challenging subsea conditions.
In conclusion, Annular Blowout Preventers are indispensable components of modern well control systems, offering versatility, rapid response, and reliable protection against potential blowouts. Their unique design and capabilities make them a crucial element in maintaining safety and efficiency in drilling operations across the oil and gas industry. China Welong is a seasoned global integrated supply chain service provider that was founded in 2001. With durable products, we are able to establish a positive reputation through stringent quality control. For more information about ABPs and other well control equipment, please contact us at oiltools15@welongpost.com.
References
- Smith, J. (2022). Advanced Well Control Techniques in Modern Drilling Operations. Journal of Petroleum Engineering, 45(3), 178-195.
- Johnson, R. & Brown, T. (2021). Blowout Preventer Technology: Innovations and Best Practices. Offshore Technology Conference Proceedings, Houston, TX.
- Anderson, L. (2023). Comparative Analysis of Annular and Ram-Type Blowout Preventers. SPE Drilling & Completion, 38(2), 201-215.
- Williams, M. et al. (2020). Maintenance Strategies for Extending the Lifespan of Well Control Equipment. Journal of Petroleum Technology, 72(8), 62-75.
- Chen, Y. & Davis, K. (2022). Subsea BOP Systems: Design Considerations and Operational Challenges. Underwater Technology, 39(4), 145-160.
- Thompson, E. (2021). Risk Assessment and Management in Offshore Drilling Operations. Safety Science, 142, 105-120.
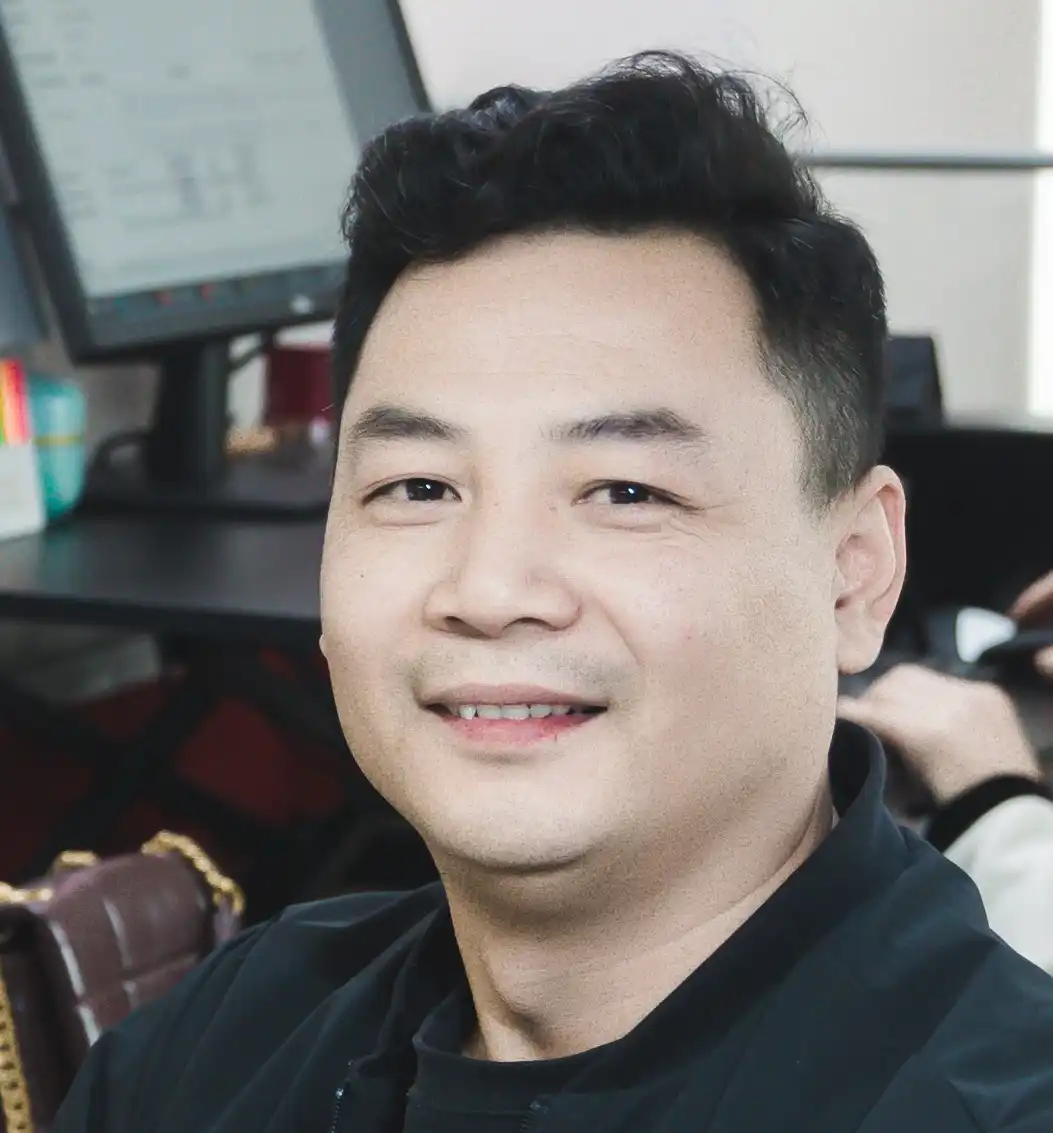
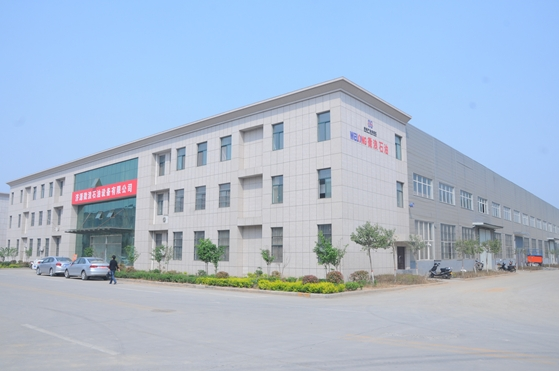
CHINA WELONG - 20+ years manufactuer in oilfield tools