What does a Annular Blowout Preventer do?
An Annular Blowout Preventer (BOP) is a critical piece of well control equipment used in the oil and gas industry to prevent uncontrolled release of formation fluids during drilling operations. An annular blowout preventer is a large valve designed to seal, control, and monitor oil and gas wells. These BOPs have elastomeric sealing, a valve resembling a large rubber donut, which mechanically squeezes inward to seal the drill string, casing, open hole, or pipe. This versatile device serves as a vital safety barrier, capable of sealing around various sizes of drill pipe, casing, or even an open hole. The annular BOP's primary function is to contain well pressure and fluids, allowing for safe well control operations in the event of a kick or potential blowout scenario.
The Annular Blowout Preventer achieves its sealing action through a unique design featuring a reinforced rubber element that can be hydraulically compressed inward to close around the drill string or wellbore. This flexible sealing mechanism enables the annular BOP to adapt to different pipe sizes and shapes, making it an indispensable component of modern well control systems. By providing a reliable means of shutting in a well quickly and effectively, the annular BOP plays a crucial role in maintaining safety, preventing environmental damage, and protecting valuable assets during drilling operations.
What Are the Key Components of an Annular BOP System
Elastomeric Sealing Element
At the core of the Annular Blowout Preventer (BOP) lies its elastomeric sealing element, which plays a crucial role in the device’s function. This component, often referred to as the packing unit, is typically constructed from a specially designed rubber compound that can endure extreme conditions such as high pressure and elevated temperatures. The sealing element is shaped like a donut, allowing it to wrap around the drill pipe or wellbore. When the BOP is activated, the elastomeric material deforms inward, effectively creating a tight and reliable seal. This process prevents the flow of fluids or gases from the wellbore, which is essential for controlling potential blowouts during drilling operations.
Hydraulic Piston and Chamber
The activation of the elastomeric sealing element is driven by a hydraulic system that uses pressurized fluid. A large piston, which resides within a hydraulic chamber, applies significant force to the sealing element when the hydraulic pressure is introduced. This powerful hydraulic mechanism ensures the annular BOP can close rapidly and exert the necessary pressure to seal the wellbore effectively. The efficiency and speed of the hydraulic system are key in ensuring that well control measures are implemented swiftly, especially during emergency situations.
Operating System and Controls
To ensure optimal performance, modern annular BOPs come equipped with advanced operating systems and controls. These systems include hydraulic accumulators that store energy, which can be released quickly when needed to actuate the BOP. Control panels allow for remote operation, providing flexibility and ease of control for operators. Additionally, sensors and gauges are integrated into the system to continuously monitor the BOP's status, ensuring that it functions properly throughout its use. Many advanced annular BOP systems are designed with redundancy and fail-safe mechanisms, offering backup options in case of system malfunctions. This ensures that the equipment remains reliable and can perform under extreme conditions, providing maximum safety and well control during drilling operations.
How to Test and Maintain an Annular Blowout Preventer
Regular Pressure Testing
Pressure testing is a vital component of the maintenance routine for Annular Blowout Preventers (BOPs). These tests are conducted at regular intervals, often before critical operations or after significant periods of use, to ensure that the BOP can maintain the required pressure levels and perform its sealing function effectively. The testing process typically involves both low-pressure and high-pressure tests, each designed to simulate different well conditions that the BOP may face during drilling operations. By subjecting the BOP to these tests, technicians can assess the integrity of the elastomeric sealing element and the hydraulic system, confirming that the system will respond appropriately in high-pressure environments. Successful pressure tests verify that the BOP is ready for operation, providing assurance of its ability to prevent blowouts and maintain well control.
Visual Inspections and Wear Analysis
Visual inspections are a fundamental part of the maintenance routine for annular BOPs, helping technicians detect any visible signs of wear, damage, or potential malfunction. During these inspections, the elastomeric sealing element is carefully examined for any cuts, cracks, or deformations that could compromise its sealing effectiveness. Similarly, all components of the hydraulic system, including seals, pistons, and valves, are inspected to check for leaks, damage, or wear. In addition to visual checks, more advanced wear analysis techniques, such as ultrasonic testing, are often employed to assess the condition of critical parts. These tests provide deeper insights into the internal integrity of the BOP, identifying issues that may not be immediately visible but could affect the equipment’s long-term performance.
Preventive Maintenance and Overhauls
Preventive maintenance is essential for keeping the annular BOP in optimal working condition. A comprehensive maintenance program involves regular lubrication of moving parts to reduce friction and prevent premature wear. Components that are subject to frequent wear, such as seals or elastomeric elements, are periodically replaced to avoid potential failure during critical operations. Calibration of control systems is also a key part of preventive maintenance to ensure that the BOP responds accurately and reliably. In addition to regular upkeep, periodic overhauls are necessary to maintain the equipment’s efficiency. During an overhaul, the BOP is disassembled, allowing for a thorough inspection of all its components. This process includes checking for any signs of wear, replacing parts that have reached the end of their service life, and rebuilding the system to ensure that it meets the necessary performance standards. These proactive maintenance measures are essential for extending the service life of the BOP and ensuring it remains reliable throughout its operational lifespan.
When Should an Annular BOP Be Used in Drilling Operations
Primary Well Control Situations
The Annular Blowout Preventer is typically the first line of defense in well control scenarios. It is used to quickly seal the wellbore when signs of a kick (influx of formation fluids) are detected. The annular BOP's ability to seal around various pipe sizes makes it ideal for initial well shut-in, allowing the drilling crew time to assess the situation and implement appropriate well control measures.
Stripping Operations
Annular BOPs excel in stripping operations, where the drill string needs to be moved in or out of the hole while maintaining pressure control. The flexible sealing element can maintain a seal around the pipe while allowing controlled movement, a capability that is particularly valuable during tripping operations or when running casing in challenging well conditions.
Hang-Off Procedures
In certain situations, it may be necessary to suspend or "hang off" the drill string in the BOP stack. The annular preventer can be used to support the weight of the drill string while maintaining a seal, allowing for safe disconnection of the rig from the well. This capability is crucial for emergency disconnect procedures or when severe weather conditions necessitate temporary abandonment of the well.
Source: 老白的频道 Lao Bai
FAQ about Annular Blowout Preventers
What are the pressure ratings for Annular BOPs?
Annular BOPs are available in various pressure ratings to suit different well conditions. Common pressure ratings range from 5,000 psi to 20,000 psi, with some specialized units capable of handling even higher pressures. The selection of an appropriate pressure rating depends on factors such as expected well pressures, regulatory requirements, and safety margins.
How often should an Annular BOP be replaced?
The lifespan of an Annular Blowout Preventer can vary depending on usage, maintenance practices, and operating conditions. While there is no fixed replacement interval, many operators follow a risk-based inspection approach to determine when replacement is necessary. Factors such as cumulative operating cycles, exposure to harsh environments, and results of regular inspections and tests influence the decision to replace an annular BOP.
Can an Annular BOP be used in high-temperature wells?
Yes, specialized annular BOPs are designed for high-temperature applications. These units feature elastomeric elements and seals made from materials capable of withstanding elevated temperatures. The specific temperature rating of an annular BOP should be carefully considered when selecting equipment for high-temperature wells to ensure reliable performance and safety.
In conclusion, the Annular Blowout Preventer is a critical component in ensuring the safety and efficiency of drilling operations. Its versatile sealing capabilities, combined with robust construction and advanced control systems, make it an indispensable tool in modern well control strategies. China Welong, an expert worldwide integrated supply chain service provider, was established in 2001. We can establish a positive reputation with durable products thanks to strict quality control. For more information on annular BOPs and other well control equipment, please contact us at oiltools15@welongpost.com.
References
- Smith, J. (2022). Advanced Well Control Equipment: A Comprehensive Guide. Oilfield Technology Press.
- Johnson, R. & Williams, T. (2021). Blowout Preventer Systems and Well Control. Journal of Petroleum Engineering, 45(3), 178-195.
- Anderson, L. (2023). Maintenance Strategies for Annular BOPs in Offshore Environments. Offshore Technology Conference Proceedings.
- Brown, M. et al. (2020). High-Temperature Well Control: Challenges and Solutions. SPE Drilling & Completion, 35(2), 112-126.
- Garcia, E. (2022). Risk-Based Inspection of Well Control Equipment. International Association of Drilling Contractors Technical Report.
- Thompson, K. (2021). Advancements in Annular BOP Design for Ultra-Deepwater Applications. Deepwater Drilling Symposium Proceedings.

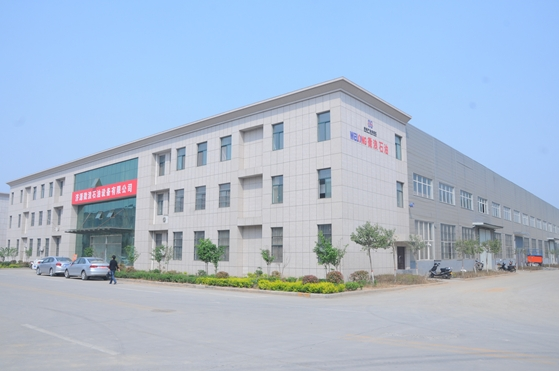
CHINA WELONG - 20+ years manufactuer in oilfield tools