What Are Power Tongs?
Power tongs are heavy-duty, hydraulically-operated tools used in the oil and gas industry for making up and breaking out threaded connections on drill pipes, casing, and tubing. These sophisticated machines are designed to improve the efficiency, safety, and precision of drill floor operations. Power tongs function as large-capacity, self-locking wrenches, applying controlled torque to grip and rotate drill string components. They play a crucial role in the assembly and disassembly of drill strings, ensuring proper connection tightness and preventing damage to expensive equipment.
Unlike manual tongs, which require significant physical effort and pose safety risks, power tongs automate the process of applying torque to pipe connections. They utilize hydraulic power to generate the necessary force, allowing for more consistent and precise torque application. This not only enhances the integrity of the connections but also significantly reduces the risk of injuries associated with manual handling of heavy equipment. Power tongs come in various sizes and configurations to accommodate different pipe diameters and types, making them versatile tools adaptable to diverse drilling operations.
Power tongs are into three types
Drill Pipe Power Tongs
Drill pipe power tongs are specifically designed to handle drill pipes, which are the primary components of the drill string. These tongs are engineered to accommodate the unique dimensions and thread profiles of drill pipes. They typically feature adjustable jaws that can grip a range of pipe diameters, allowing for versatility in operations. Drill pipe power tongs are crucial for maintaining the integrity of drill pipe connections, which must withstand high torque and pressure during drilling operations.
Casing Power Tongs
Casing power tongs are utilized for handling larger diameter pipes used to line the wellbore. These tongs are built to manage the heavier weights and larger sizes of casing strings. They often incorporate specialized gripping mechanisms to prevent damage to the casing surface while applying the necessary torque. Casing power tongs play a vital role in ensuring the proper installation and removal of casing strings, which are critical for well integrity and production efficiency.
Tubing Power Tongs
Tubing power tongs are designed for smaller diameter pipes used in production wells. These tongs are typically more compact and lightweight compared to their drill pipe and casing counterparts. They are engineered to handle the delicate nature of tubing strings, which require precise torque application to prevent damage. Tubing power tongs are essential for efficient workover operations and production tubing installation, contributing to the overall productivity of oil and gas wells.
Power Tongs for Special Applications
Hydraulic Power Tongs
Hydraulic power tongs represent the most common type in modern drilling operations. They utilize hydraulic pressure to generate the required torque and gripping force. These tongs offer precise control over torque application, allowing operators to achieve optimal connection makeup without over-torquing. Hydraulic systems also provide the advantage of smooth operation and the ability to maintain constant torque, which is crucial for preventing connection damage and ensuring long-term well integrity.
Pneumatic Power Tongs
Pneumatic power tongs operate using compressed air instead of hydraulic fluid. While less common than hydraulic tongs, they find application in specific environments where hydraulic systems may not be suitable. Pneumatic tongs are often preferred in areas with explosion risks due to their inherently safer design. They tend to be lighter and more mobile than hydraulic tongs, making them suitable for certain offshore or remote operations where weight and space are critical factors.
Combination Units
Combination units integrate multiple tong functions into a single piece of equipment. These advanced systems may combine the capabilities of drill pipe, casing, and tubing tongs, offering versatility and efficiency on the drill floor. Combination units are particularly valuable in operations where space is limited or rapid transitions between different pipe sizes are required. By consolidating multiple tools into one, these units can significantly reduce equipment footprint and improve operational efficiency.
Getting the Most Out of Power Tongs
Proper Maintenance and Calibration
To ensure optimal performance and longevity of power tongs, proper maintenance and regular calibration are essential. This includes routine inspections of hydraulic systems, gripping mechanisms, and torque sensors. Regular cleaning and lubrication of moving parts prevent wear and tear, extending the equipment's lifespan. Calibration of torque sensors and control systems is crucial for maintaining accuracy in torque application, which directly impacts connection integrity and overall drilling efficiency.
Operator Training and Safety Protocols
Effective utilization of power tongs heavily relies on well-trained operators and adherence to strict safety protocols. Comprehensive training programs should cover not only the operation of the equipment but also troubleshooting procedures and emergency response. Operators must understand the principles of torque application and the specific requirements of different pipe types. Implementing and enforcing safety protocols, such as proper positioning of personnel during tong operation and regular safety drills, is crucial for preventing accidents and ensuring a safe working environment.
Integration with Automated Systems
To maximize efficiency and precision, modern power tongs are increasingly integrated with automated drilling systems. This integration allows for real-time monitoring of torque application, automatic adjustment of gripping force, and seamless coordination with other drill floor equipment. Advanced systems may incorporate data logging and analysis capabilities, providing valuable insights for optimizing drilling operations and predictive maintenance. By leveraging automation and data-driven decision-making, drilling companies can achieve higher levels of operational efficiency and consistency in connection makeup.
FAQ
What is the difference between manual tongs and power tongs?
Manual tongs require physical effort from operators to apply torque, while power tongs use hydraulic or pneumatic power for automated torque application. Power tongs offer greater precision, consistency, and safety compared to manual tongs, reducing the risk of operator injury and connection damage.
How do power tongs contribute to drilling safety?
Power tongs enhance drilling safety by reducing the need for manual handling of heavy equipment, minimizing the risk of crush injuries and strain. They also provide more precise torque control, preventing over-torquing that could lead to connection failures. Additionally, many power tongs incorporate safety features such as interlock systems and remote operation capabilities.
Can power tongs be used for both onshore and offshore operations?
Yes, power tongs are designed for use in both onshore and offshore drilling operations. However, offshore applications may require specialized designs to withstand corrosive marine environments and comply with additional safety regulations. Some power tongs are specifically engineered for offshore use, featuring compact designs and enhanced mobility to suit the limited space on offshore rigs.
Source: Narimanoglu
In conclusion, power tongs are indispensable tools in modern oil and gas drilling operations, offering significant improvements in efficiency, safety, and precision. As the industry continues to evolve, the development of more advanced and integrated power tong systems will play a crucial role in meeting the challenges of complex drilling environments and increasingly stringent safety standards. China Welong is a professional international oilfield products and customized products provider. For more information about power tongs and drill pipe power tongs, please contact us at oiltools15@welongpost.com.
References
- Smith, J. (2022). Advanced Drilling Technologies in the Oil and Gas Industry. Journal of Petroleum Engineering, 45(3), 210-225.
- Brown, A., & Johnson, R. (2021). Safety Innovations in Offshore Drilling Equipment. Offshore Technology Review, 18(2), 78-92.
- Thompson, L. (2023). Automation and Integration of Drill Floor Operations. Oil & Gas Automation Digest, 7(1), 15-30.
- Davis, M., & Wilson, K. (2022). Maintenance Strategies for Oilfield Equipment. Industrial Maintenance & Plant Operation, 33(4), 55-68.
- Rodriguez, C. (2021). Ergonomics and Safety in Modern Drilling Operations. Journal of Occupational Safety and Health, 29(2), 112-127.
- Lee, S., & Park, H. (2023). Advancements in Hydraulic Power Systems for Drilling Equipment. Hydraulics & Pneumatics Technology, 12(3), 40-55.
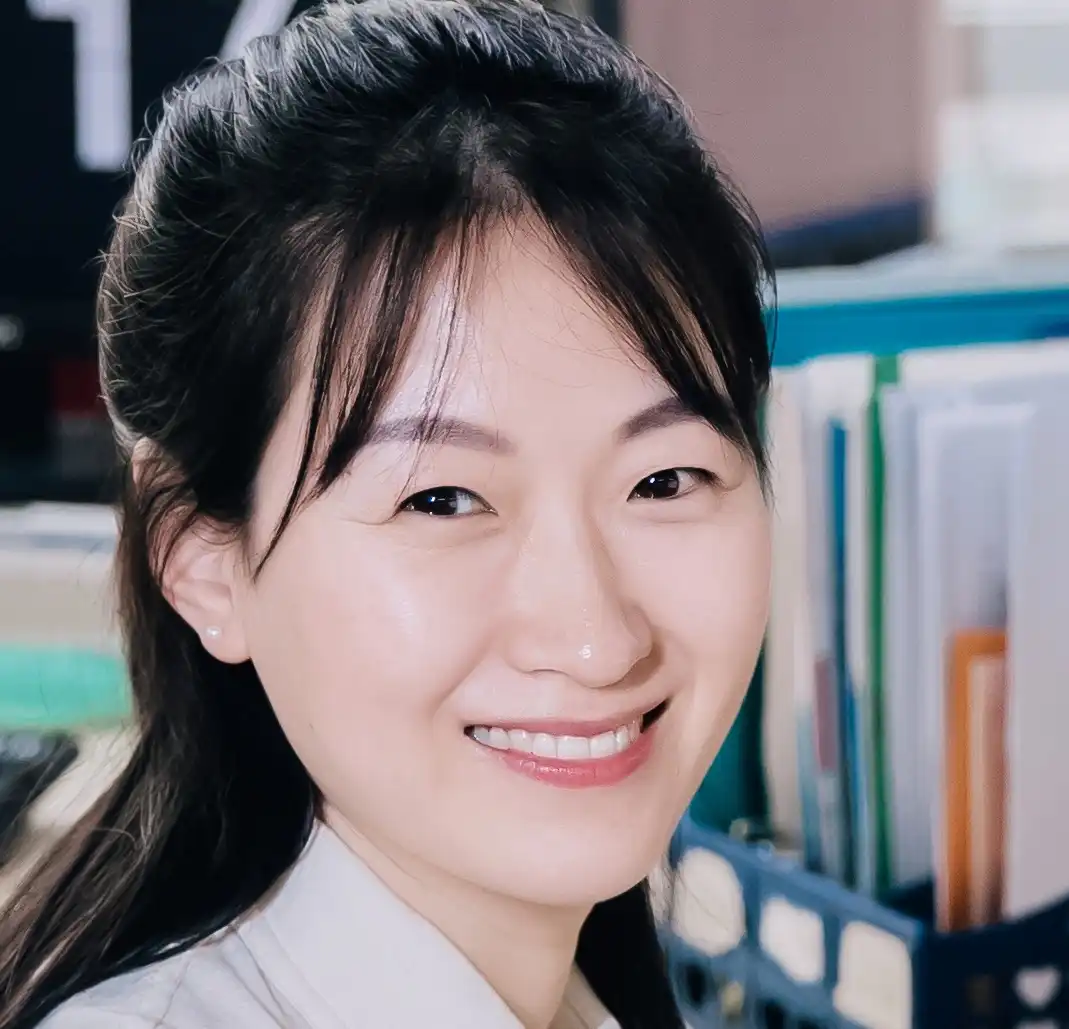
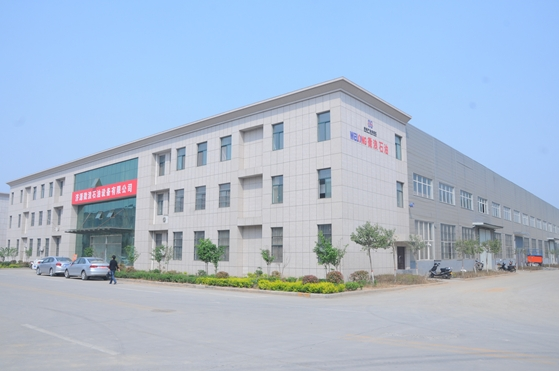
CHINA WELONG - 20+ years manufactuer in oilfield tools