What is the difference between a float collar and a float shoe?
A float collar and a float shoe are both essential tools in wellbore construction and cementing operations, but they serve distinct roles. The key difference lies in their placement within the casing string and their specific functions.
The float shoe is typically installed at the bottom of the casing string, designed to allow cement to flow into the annular space between the casing and the surrounding formation. It also prevents backflow during the cementing process. The float shoe is equipped with a check valve, which allows the cement slurry to flow out but automatically seals the casing once the pumping pressure is stopped, preventing any cement from flowing back into the casing.
On the other hand, a float collar is installed just above the float shoe, usually at the top of the casing string. Its primary role is to aid in the control of cement placement, ensuring the cement remains in place until it has set. Similar to the float shoe, the float collar has a check valve, but it is designed to provide additional control over the pressure during the cementing operation, particularly in deeper wells or wells with high-pressure environments.
In summary, while both tools prevent fluid backflow and help in the cementing process, the float shoe is positioned at the bottom to initiate the cement flow, while the float collar works further up the casing string to support pressure control and cement placement.
What Are the Main Functions of a Float Collar and a Float Shoe?
The float collar and float shoe are complementary tools that serve specific functions in cementing and pressure management during drilling operations. Both of these tools are essential for ensuring the wellbore integrity and cement job success.
Cementing Process Assistance
The float collar and float shoe are integral components in the cementing process, playing a critical role in the controlled placement of cement in the wellbore. When cement is pumped into the well, it must flow into the annulus, the space between the casing and the formation. The float shoe initiates this process by allowing the cement slurry to flow out of the casing while also preventing any backflow once the pumping stops. This is essential because, without such a mechanism, the cement would not stay in place and could result in an incomplete seal. The float collar, positioned further up in the casing string, helps to continue this controlled cement placement. It prevents the cement from migrating or flowing back, ensuring it remains in the desired location. The combination of these two tools guarantees that the cement is properly placed, providing a solid foundation for well integrity and long-term stability.
Preventing Backflow and Fluid Migration
A primary concern during the cementing process is preventing backflow, which could undermine the well's structural integrity. The check valve inside the float shoe plays a pivotal role in preventing backflow by automatically sealing off the casing once the pumping pressure ceases. This ensures that the cement stays in the annular space and does not return to the wellbore, maintaining the placement and bond. The float collar extends this function by preventing any cement or other fluids from moving once they are placed, while also managing the pressure inside the casing string. The float collar’s ability to control fluid migration is particularly valuable in deep or high-pressure wells, where the risk of fluid displacement is greater. By effectively containing the cement slurry, both the float collar and float shoe contribute significantly to preserving well integrity and ensuring the cement bond remains intact.
Pressure Control During Cementing
Another essential function of both the float collar and float shoe is managing pressure during the cementing process. When cement is pumped into the wellbore, it generates a significant amount of pressure. The float shoe helps to control this pressure, preventing any fluid from leaking or escaping from the casing while the cement slurry is being placed. Once the pumping ceases, the check valve in the float shoe ensures the pressure is maintained in the correct direction, preventing unwanted fluid migration. The float collar continues this pressure control further up the casing string, ensuring that pressure remains consistent throughout the cementing operation. In deeper wells, where pressure fluctuations can be more pronounced, the float collar’s ability to stabilize pressure is vital for maintaining the integrity of the well. Together, the float collar and float shoe ensure that the cementing process is conducted under optimal pressure conditions, which is crucial for the success and safety of the well over its lifespan.
How Does a Float Shoe Work in Well Cementing Compared to a Float Collar?
The float shoe and float collar both play pivotal roles in the cementing process, but they differ significantly in their placement and specific functions during cementing operations.
Float Shoe Cementing Function
The float shoe is a vital component of the casing string, located at the very bottom, just above the drill bit. Its primary purpose during the cementing process is to facilitate the proper placement of cement into the annular space between the casing and the wellbore. The float shoe has a one-way check valve that opens when the cement slurry is pumped, allowing it to flow outward and fill the annulus. This mechanism ensures that the cement slurry reaches the required depth in the well. Once the pumping stops, the check valve automatically closes, preventing the cement from flowing back into the casing. This prevents any unwanted movement of the cement slurry, ensuring that the cement remains in place and forms a solid bond between the casing and the formation. In essence, the float shoe is responsible for initiating the cement flow and preventing backflow, a critical function in ensuring a successful cement job and well integrity.
Float Collar Cementing Function
Sitting just above the float shoe, the float collar plays a complementary role during the cementing process. While the float shoe initiates the cement flow, the float collar is responsible for supporting the pressure control within the casing string. Its primary function is to help regulate the pressure inside the casing after the cement has been pumped into the well. By doing so, the float collar ensures that the cement remains in place and doesn’t migrate, especially in deeper or higher-pressure wells where fluid migration is a greater risk. Like the float shoe, the float collar also contains a check valve, which prevents any backflow of fluid or cement. However, the float collar's main role is not to initiate the cement flow, but rather to work in tandem with the float shoe to ensure that pressure is managed and that the cement is securely placed throughout the casing string. It’s particularly important in helping to control the overall cementing environment, ensuring that pressure fluctuations do not affect the wellbore stability.
Key Differences in Cementing Operations
The main difference between the float shoe and the float collar lies in their placement and their specific functions within the cementing process. The float shoe is located at the very bottom of the casing string, where it plays a crucial role in starting the flow of cement into the annulus and preventing backflow once the cementing operation is completed. It is the first point of contact for the cement slurry and has a direct impact on how the cement is placed at the lowest part of the wellbore. On the other hand, the float collar is installed further up in the casing string and works to regulate pressure during the cementing process. While both tools have check valves to prevent fluid backflow, the float collar’s primary function is to provide additional support for managing pressure and ensuring that the cement stays in place higher up the well. Together, the float shoe and float collar function cohesively to guarantee an effective cement job, with the float shoe responsible for initiating the cement flow and the float collar supporting pressure management and cement placement further along the casing string. Both tools are essential for a successful cementing operation, ensuring that the well remains secure and stable.
How Do Float Shoes and Float Collars Prevent Backflow in Drilling?
Backflow prevention is one of the most critical functions of both the float shoe and float collar during drilling operations, especially during cementing. Both tools are designed to prevent the reversal of fluid flow once cement is pumped into the wellbore, ensuring the cement stays in place and forms a strong, continuous seal.
Float Shoe Check Valve
The float shoe’s check valve is the primary mechanism that prevents backflow. During the cementing process, the check valve remains open to allow cement to flow from the casing into the annular space between the casing and the formation. Once the cementing pump stops, the pressure in the casing decreases, causing the check valve to automatically close, preventing any backflow of cement or other fluids into the casing. This ensures that the cement remains in the annular space, where it can cure and form a proper bond with the formation.
Float Collar Check Valve
Similarly, the float collar has a check valve that performs a comparable function to that of the float shoe. Positioned higher in the casing string, the float collar ensures that the cement slurry stays in place by preventing backflow after the cementing operation. The check valve in the float collar adds an extra layer of security in the cementing process by further controlling the fluid flow and preventing the cement from flowing back into the casing after it has been placed.
Enhanced Backflow Prevention in Combination
When used together, the float shoe and float collar provide a robust system for preventing backflow during cementing. The float shoe initiates cement placement, while the float collar manages pressure and prevents fluid migration further up the casing string. The combination of these two tools ensures that the cement remains in place without being displaced or contaminated, which is vital for ensuring the long-term integrity of the well.
By preventing backflow, both tools contribute significantly to the effectiveness of the cementing operation, ensuring that the cement forms a solid seal and maintains wellbore stability.
What Are the Key Design Differences Between a Float Shoe and a Float Collar?
While both the float shoe and float collar serve similar functions in the cementing process, there are notable design differences between the two tools. These differences are based on their placement within the casing string and their specific roles in pressure management and cement flow control.
Position in the Casing String
The most obvious design difference is their placement in the casing string. The float shoe is positioned at the bottom of the casing, directly above the drill bit, while the float collar is located above the float shoe in the casing string. This placement determines their primary functions during cementing. The float shoe initiates the cement flow and prevents backflow, while the float collar helps manage pressure and supports cement placement further up the casing string.
Check Valve Design and Function
Both tools are equipped with check valves, but the design and function of the valves differ slightly. The float shoe’s check valve is typically designed to be activated by the pumping pressure of the cement slurry, allowing it to open and close automatically. The float collar’s check valve is often designed to maintain a more consistent seal to help manage pressure during and after the cementing process. The float collar’s valve ensures that pressure is maintained in the casing string, contributing to cement stability and wellbore integrity.
Structural Differences for Pressure Management
The float collar is often designed with more robust pressure management features than the float shoe. This includes additional seals and valves that allow it to better manage the pressure during cementing, particularly in deep or high-pressure wells. The float collar's design ensures that once the cement is placed, it remains in place while also managing any pressure fluctuations that could occur in the wellbore.
In summary, the float shoe and float collar are designed to complement each other, with the float shoe focused on initiating the cement flow and preventing backflow, while the float collar helps with pressure control and supports cement placement further up the casing string.
Why Is a Float Shoe Typically Placed at the Bottom of the Well?
The float shoe is specifically designed to be placed at the bottom of the well for several important reasons:
Initial Cement Placement
The float shoe is installed at the bottom of the casing string because it is responsible for starting the cementing process. Once the casing is lowered into the well, the float shoe is the first component to come into contact with the cement slurry, allowing it to flow into the annular space between the casing and the formation. Its placement at the bottom ensures that the cement is placed properly from the bottom up.
Preventing Backflow During Cementing
The float shoe's primary role is to prevent backflow once the cement is pumped into the well. Positioned at the bottom of the casing string, the float shoe ensures that no cement or fluids flow back into the casing after the pump is turned off. Its check valve automatically closes once pumping stops, preventing any unwanted flow and keeping the cement in place.
Maintaining Wellbore Pressure
In addition to controlling backflow, the float shoe helps maintain pressure in the wellbore during the cementing process. Its strategic position at the bottom of the casing allows it to support pressure control, ensuring that the wellbore remains stable and that the cement job is successful.
In essence, the float shoe’s position at the bottom of the well ensures the cement flows correctly, remains in place, and prevents backflow, contributing significantly to well integrity and stability.
What Happens If a Float Shoe Is Not Used in a Drilling Operation?
The float shoe plays a vital role in ensuring the success of the cementing operation. If a float shoe is not used, several potential issues may arise:
Backflow of Cement
Without the presence of a float shoe, the risk of cement backflow significantly increases once the cementing pump is stopped. The float shoe is equipped with a one-way check valve that plays a vital role in preventing the cement slurry from flowing back into the casing. This valve ensures that, after the cement is pumped into the annular space, it stays in place without re-entering the casing, which would otherwise disrupt the cement job. If the cement flows back into the casing, it can create voids or gaps in the cement column, leading to poor zonal isolation. This is particularly critical when the goal is to form a solid bond between the casing and the surrounding formation to prevent fluid migration or gas leakage. By preventing cement backflow, the float shoe guarantees that the cement remains in place, allowing it to set properly and form the necessary seal.
Pressure Instability
The float shoe also plays a critical role in maintaining wellbore pressure during the cementing process. Without it, pressure fluctuations can occur once the cementing pump is stopped. These pressure variations can destabilize the wellbore environment, potentially causing problems such as gas influx, fluid migration, or even damage to the well integrity. If the pressure isn't properly controlled, it can lead to an incomplete cement job, where the cement does not fill the annular space as intended or fails to form an adequate bond with the formation. Such pressure instability can also increase the chances of issues like wellbore collapse or compromised cement seals, which are essential for the long-term stability of the well. The float shoe helps regulate the pressure, ensuring that the cement is placed effectively and that the well's structural integrity is maintained throughout the cementing operation.
Inaccurate Cement Placement
The float shoe helps ensure that cement is placed correctly and in the right quantity. Without it, there may be challenges in ensuring proper cement placement, which could result in incomplete cement jobs or ineffective sealing of the well.
In conclusion, not using a float shoe could lead to complications in wellbore stability, cementing success, and overall well integrity. The float shoe is a crucial component for ensuring the proper placement of cement and preventing backflow during drilling operations.
Conclusion
In conclusion, understanding the difference between a float collar and a float shoe is critical for ensuring the success of cementing operations. Both tools serve complementary roles in preventing backflow, managing pressure, and ensuring proper cement placement. The float shoe is typically placed at the bottom of the casing string, while the float collar is positioned further up to support pressure control and cement placement. Together, these tools contribute to the overall stability and integrity of the well.
When selecting a taper mill, it’s important to consider factors such as the well's depth, the type of materials you are working with, and the specific challenges you anticipate in the wellbore. China Welong offers a variety of taper mills designed to meet the demanding requirements of drilling operations. Our taper mills are engineered for durability and efficiency, providing you with the tools needed to handle tough drilling conditions. We prioritize reasonable cost control, timely delivery, and superior product quality. Our team is always available to assist you in selecting the right tools for your specific needs.
For more information on our high-quality float shoes and other oilfield products, feel free to reach out to us at oiltools15@welongpost.com.
References
1. Smith, M. E., & Howard, C. M. (2007). Cementing: An Overview of the Techniques and Applications. Journal of Petroleum Technology, 59(7), 68-75.
2. Dorman, S. T., & Shields, R. L. (2013). Casing and Cementing Operations for Drilling Engineers. Oil & Gas Journal, 111(12), 72-79.
3. Daum, R. P., & Montoya, F. A. (2009). Enhanced Cementing Techniques for Challenging Wells. SPE/IADC Drilling Conference, Society of Petroleum Engineers, 1-10.
4. Green, T. H., & Wilson, D. P. (2015). The Role of Float Equipment in Wellbore Integrity. SPE/IADC Wellbore Integrity Conference, Society of Petroleum Engineers, 21-30.
5. Thigpen, M. D., & Richardson, R. D. (2011). Optimizing Cementing Operations for Wellbore Integrity. SPE Journal of Energy Resources, 45(4), 283-290.
6. Williams, B. A., & Herring, P. E. (2010). Float Equipment Design and Application in Cementing Operations. SPE/IADC Drilling Conference, Society of Petroleum Engineers, 35-42.
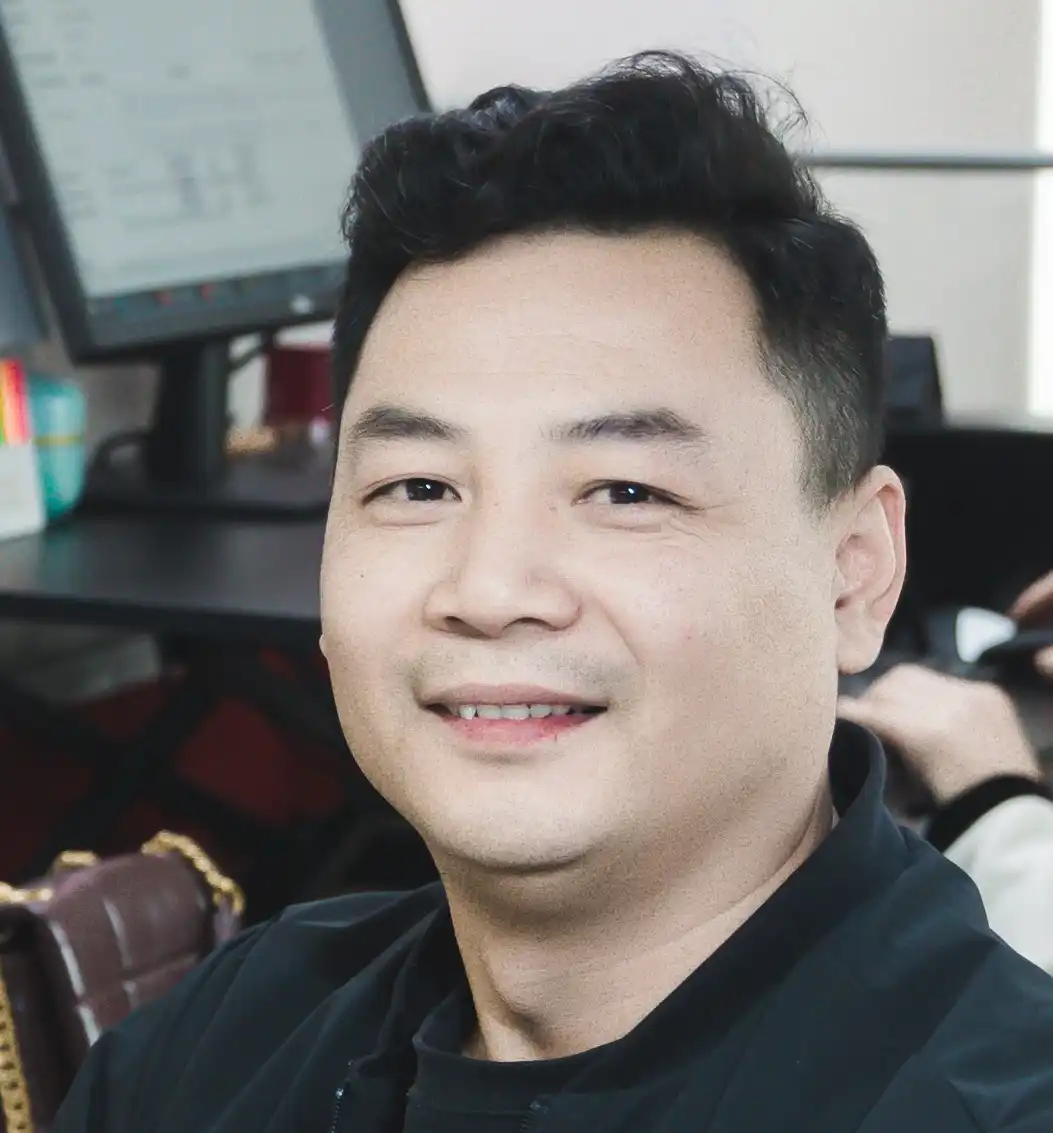
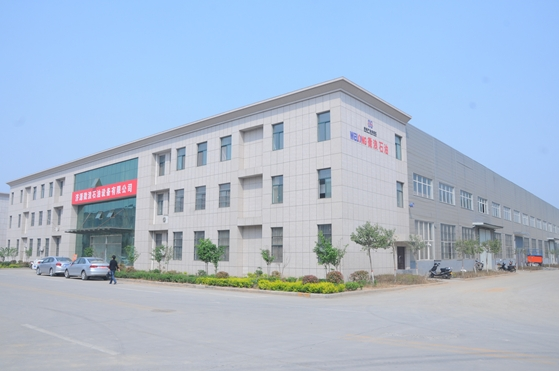
CHINA WELONG - 20+ years manufactuer in oilfield tools