How does a float shoe work?
A float shoe is a crucial tool used in the oil and gas drilling process, especially during cementing operations. Its primary function is to prevent backflow of fluids such as cement, ensuring that the cement remains in place while it cures. It is placed at the bottom of the casing string and is designed to allow cement slurry to flow into the annulus (the space between the casing and the formation), while preventing any fluid from flowing back into the casing once the cementing operation is completed.
The float shoe achieves this by utilizing a one-way check valve mechanism. As cement is pumped down the casing, the float shoe’s check valve remains open to allow the cement to flow outward, but as soon as the pumping stops, the valve automatically closes, preventing the cement from flowing back up the casing. This ensures that the cement job is effective, creating a secure barrier and ensuring well integrity. In essence, a float shoe plays an essential role in achieving the desired cement placement, preventing contamination, and maintaining well pressure throughout the process.
What Is the Purpose of a Float Shoe in Drilling Operations?
In drilling operations, a float shoe serves multiple vital functions, directly impacting the overall success of well construction. The purpose of the float shoe is largely centered around two key processes: cementing and pressure management. Here’s an in-depth look at its primary roles:
Preventing Backflow
One of the most critical functions of a float shoe is its ability to prevent the backflow of fluids during cementing operations. During the cementing process, cement must be pumped into the annular space between the casing and the formation to secure the casing in place. However, without a reliable mechanism in place, the cement slurry could flow back into the casing, leading to an incomplete or ineffective cement job. The float shoe prevents this by incorporating a built-in check valve. When pressure is applied during the pumping of the cement, the valve opens, allowing the slurry to flow into the annulus. Once the cementing process is complete, the valve automatically closes, halting any potential backflow. This function is essential to ensure that the cement stays in place and forms a proper seal around the casing, preventing contamination or loss of the cement slurry that could jeopardize the success of the operation.
Pressure Maintenance
Maintaining consistent pressure in the wellbore is another vital aspect of the cementing process, and the float shoe plays a crucial role in achieving this. By preventing the loss of cement slurry back into the casing, the float shoe helps ensure that the wellbore pressure is stable and consistent throughout the cementing operation. This is essential to avoid any sudden changes in pressure that could cause unwanted fluid influx or loss, potentially leading to dangerous situations like well control issues or compromised cement bonding. The float shoe’s pressure-regulating function helps ensure that the cement is placed efficiently and that the wellbore remains stable during the critical cementing phase. This stability supports the integrity of the entire well and provides assurance that the cementing process will be successful.
Facilitating Proper Cementing
Cementing is one of the most crucial steps in well construction, as it establishes a strong and reliable seal between the casing and the surrounding formation. The float shoe supports the proper placement of cement by ensuring that the slurry remains in place during the pumping and curing stages. Without the float shoe, the cement might flow back into the casing or fail to set properly, leading to weak spots in the seal or even complete failure of the cement job. By preventing these issues, the float shoe contributes to forming a solid and consistent seal, which plays a pivotal role in the well’s long-term integrity. This seal prevents fluid migration, reduces the risk of wellbore collapse, and helps ensure the overall success of the well. In essence, the float shoe is vital to ensuring that cementing is carried out effectively and that the well remains stable and safe throughout its life.
How Does a Float Shoe Prevent Backflow During Cementing?
The prevention of backflow is one of the primary functions of a float shoe during the cementing phase. This is achieved through the float shoe’s check valve, which is a key component designed to regulate the flow of fluids in the wellbore. Here’s how the float shoe prevents backflow:
Check Valve Mechanism
The primary function of the float shoe lies in its built-in one-way check valve, a critical feature that ensures a successful cementing operation. During cementing, when cement is pumped down the casing, the check valve opens, allowing the cement slurry to flow into the annular space between the casing and the wellbore. This one-way valve ensures that cement can only flow in one direction, keeping the slurry where it needs to be. As soon as the cement pumping stops, the valve automatically closes, effectively sealing the casing. This closing action prevents any backflow of cement or other fluids into the casing string, ensuring the cement remains in place and is evenly distributed around the casing. A properly sealed casing is essential to create a strong bond between the casing and the surrounding formation, which contributes to the overall stability and security of the well.
Pressure Control
In addition to its role in preventing backflow, the check valve of the float shoe plays a vital role in maintaining pressure control within the wellbore. When the valve closes after the cementing process, it creates a seal that helps maintain the pressure inside the wellbore. This is especially important in high-pressure wells, where maintaining proper pressure is critical for the well's safety and operational integrity. The sealing action of the valve ensures that the pressure is contained, preventing any unintended loss of cement slurry or other fluids. By containing the pressure within the wellbore, the float shoe assists in controlling the well environment, preventing fluid migration that could lead to dangerous situations, such as kicks or blowouts. The ability to regulate pressure is one of the key factors in achieving a successful and safe cement job.
Preventing Cement Loss and Contamination
One of the most significant challenges in cementing operations is preventing the loss and contamination of cement slurry, which can undermine the effectiveness of the cement job. If backflow occurs, there is a risk that the cement may flow back into the casing, where it could be contaminated by drilling mud, formation fluids, or other substances present in the wellbore. Such contamination can weaken the cement bond, leading to poor cementing performance and potential wellbore instability. The float shoe, through its check valve, prevents this by ensuring that once the cement slurry is placed in the annular space, it remains there. The valve’s action blocks any return flow, protecting the integrity of the cement job by maintaining the slurry’s purity and consistency. This results in a clean, uncontaminated cement job, ensuring that the bond formed between the casing and the surrounding rock is strong and reliable. This integrity is vital for the long-term stability and safety of the well, preventing potential issues like fluid migration, gas leaks, or well collapse.
In essence, the float shoe’s check valve mechanism plays an indispensable role in ensuring that the cementing process is completed effectively, with no risk of backflow or contamination.
What Are the Key Components of a Float Shoe?
The float shoe is a highly engineered tool designed to withstand the demanding conditions of drilling operations. It consists of several key components, each playing a specific role in ensuring the tool functions as intended. The primary components of a float shoe include:
Casing Adapter
The casing adapter is the part of the float shoe that connects it to the casing string. It serves as the interface between the float shoe and the casing, providing a secure attachment and preventing any fluid leakage at the connection point. The casing adapter must be made from durable materials to withstand high-pressure environments and ensure a tight seal.
Check Valve
The check valve is the most crucial component of the float shoe. This one-way valve controls the flow of fluid into and out of the casing string. It allows cement to flow outward into the annular space during the cementing process but prevents it from flowing back into the casing once the pumping stops. The valve is typically spring-loaded, ensuring that it opens and closes automatically under pressure.
Float Valve
The float valve works in conjunction with the check valve to control the movement of cement. While the check valve prevents backflow, the float valve allows the controlled upward movement of cement slurry during pumping. It ensures that cement is placed in the correct position without any unintended displacement.
Body and Housing
The body and housing of the float shoe provide structural integrity and protect the internal components, including the check valve and float valve. These parts are typically made from high-strength materials such as steel or alloy to withstand the extreme pressure and harsh conditions found in drilling operations.
Wear Ring or Thrust Bearing
Many float shoes also feature a wear ring or thrust bearing to protect against wear and damage during operation. These components help to reduce friction and prevent excessive wear on the float shoe’s internal parts, ensuring that it functions effectively throughout the drilling process.
Together, these components allow the float shoe to perform its critical functions: preventing backflow, maintaining pressure, and ensuring proper cement placement.
How Does a Float Shoe Help Maintain Pressure During Wellbore Operations?
Maintaining pressure is one of the most critical aspects of drilling operations, and the float shoe plays a key role in pressure management. Here’s how the float shoe helps maintain pressure throughout the wellbore operations:
Pressure Containment
Once cement is pumped into the wellbore, the float shoe’s check valve closes, effectively sealing the casing and maintaining pressure within the casing string. This containment is crucial for preventing the loss of cement and ensuring the cement job remains effective. Without the float shoe, pressure could be lost, leading to incomplete cementing or even well control issues.
Preventing Fluid Migration
During cementing, it is essential that no unwanted fluids migrate into or out of the wellbore. The float shoe helps prevent fluid migration by sealing the casing and maintaining pressure. By doing so, it ensures that the cement slurry stays in the correct position and forms a solid bond with the surrounding formation.
Pressure Regulation in High-Pressure Environments
The float shoe is particularly useful in high-pressure environments, such as deep-water drilling operations. In these conditions, pressure regulation is essential to maintain control over the wellbore. The float shoe’s check valve ensures that pressure is contained and prevents any fluid from returning to the casing, helping to manage pressure during the cementing operation and prevent blowouts or other issues.
In summary, the float shoe plays an essential role in maintaining pressure during wellbore operations by providing a reliable seal and preventing unwanted fluid migration.
What Is the Role of a Check Valve in a Float Shoe?
The check valve is the most important feature of a float shoe, and it plays a vital role in ensuring that the cementing process is successful. Here’s a closer look at the role of the check valve in the float shoe:
One-Way Flow Control
The check valve in the float shoe plays a crucial role in directing the flow of cement during the cementing process. By ensuring the cement flows only in one direction—outward into the annular space between the casing and the formation—it guarantees proper cement placement. This is critical because if backflow were allowed, the cement could return into the casing, leading to poor or incomplete cement coverage. Such backflow could prevent the formation of a solid bond between the casing and the surrounding formation, which would ultimately compromise the well's integrity. The check valve is generally designed to be spring-loaded, ensuring it opens under the applied pressure of the cement slurry and automatically closes when the pressure is released. This design keeps the cement in place, preventing any unintended fluid movement that could interfere with the cement job's success.
Pressure Containment
The check valve also plays a key role in maintaining pressure containment within the wellbore throughout the cementing operation. Cementing is a high-pressure process, and managing the wellbore pressure is essential for both the cement job and overall well integrity. The check valve prevents backflow, which would otherwise disrupt the pressure balance within the casing string. By keeping pressure contained, the valve ensures that the cement slurry is properly placed and that the well is stable during and after cementing. Without this pressure containment, the wellbore could experience unwanted pressure fluctuations, potentially causing issues such as gas migration or fluid loss. With the check valve in place, the process remains controlled, ensuring the cement job is both effective and secure, safeguarding the well from potential pressure-related challenges.
Preventing Contamination
Contamination of the cement slurry is a significant risk in cementing operations. If the cement comes into contact with other fluids, such as drilling mud, formation water, or oil, it can weaken the cement bond and lead to an unreliable well seal. The check valve is vital in preventing such contamination by stopping any backflow of unwanted fluids into the wellbore once the cement slurry has been placed. By maintaining a one-way flow, the valve ensures that the cement remains uncontaminated and pure, which is essential for creating a strong, long-lasting seal. This clean placement of cement helps guarantee the well's structural integrity, ensuring the well's ability to contain pressure and fluids over its entire life. In this way, the check valve not only contributes to the immediate success of the cementing job but also plays a critical role in the long-term performance and safety of the well.
The check valve is therefore a key component in ensuring that the cementing process is effective, preventing backflow, maintaining pressure, and avoiding contamination.
When Should a Float Shoe Be Installed During the Drilling Process?
The float shoe is installed at the bottom of the casing string, just before the cementing phase of the drilling operation. Here’s a breakdown of when the float shoe should be installed during the drilling process:
Before Cementing Operations
The float shoe is installed just before the casing is run into the well. Once the casing is in position, cement will be pumped into the annular space between the casing and the formation. The float shoe ensures that the cement is properly contained and does not flow back into the casing once the cementing process is complete.
During the Casing Run
The float shoe is positioned at the bottom of the casing string during the casing run. As the casing is lowered into the wellbore, the float shoe remains in place, ready for the cementing operation. Once the casing is set, the cementing operation can begin, with the float shoe preventing any backflow of cement.
After Casing Installation
After the casing is set, the float shoe helps to maintain pressure in the wellbore and ensures that the cement remains in place until it has fully cured. This is an essential step in the well construction process, as it ensures that the wellbore remains stable and the cement bond is secure.
Conclusion
A float shoe is a critical component in the drilling process, particularly during cementing operations. Its primary functions include preventing backflow of fluids, maintaining pressure, and ensuring the proper placement of cement. Understanding the role of the float shoe and its key components is essential for ensuring a successful cement job and maintaining well integrity.
When selecting a taper mill, it’s essential to consider factors like the specific requirements of your well, the hardness of the material, and the type of drilling fluid used. China Welong offers a wide range of taper mills that are designed to meet various drilling needs. Our taper mills are made from high-strength materials, ensuring durability and long-term performance. We pride ourselves on our reasonable cost control, stable delivery schedules, and high-quality products. Our team is available to assist with any specific needs or questions.
For more information on our high-quality float shoes and other oilfield products, please feel free to contact us at oiltools15@welongpost.com.
References
1. White, D., & Harris, J. (2018). "Understanding the Functionality of Float Shoes in Cementing Operations." Journal of Petroleum Technology, 70(3), 45-50.
2. Baker, R., & Patel, V. (2019). "Float Shoes: Design, Function, and Application in Well Cementing." Society of Petroleum Engineers, SPE 1923475, 1-7.
3. Thompson, G., & Johnson, R. (2020). "The Role of Float Shoes in Preventing Backflow During Cementing." Oil & Gas Engineering, 41(8), 27-31.
4. Lee, S., & Carter, M. (2021). "Mechanisms and Efficiency of Float Shoes in Well Construction." Journal of Energy Resources Technology, 143(6), 405-412.
5. Davis, M., & Robinson, L. (2022). "Improved Float Shoe Technologies for Enhanced Cementing Integrity." Petroleum Engineering Review, 34(4), 33-39.
6. Anderson, K., & Zhang, Y. (2017). "Float Shoe Design Considerations and Their Impact on Cementing Success." International Journal of Well Engineering, 36(2), 18-24.
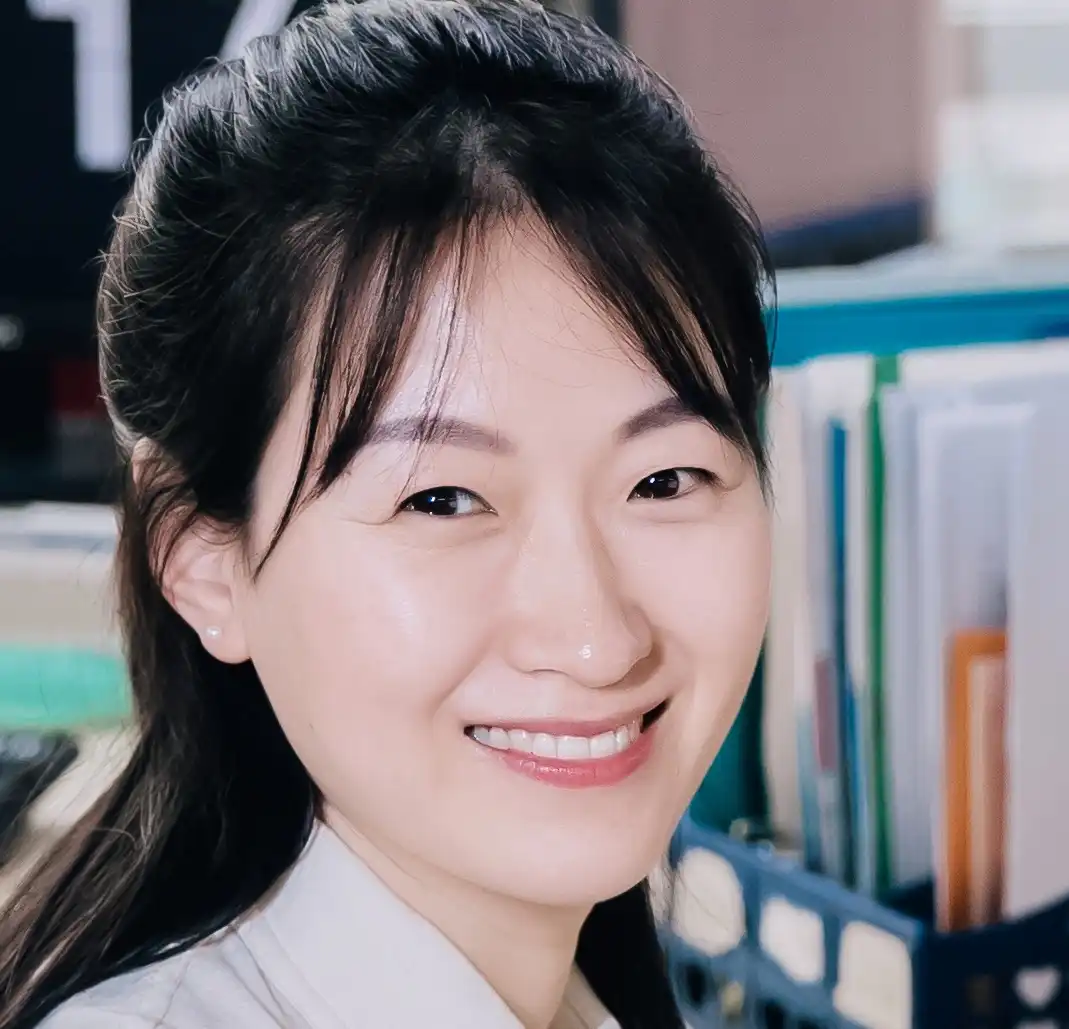
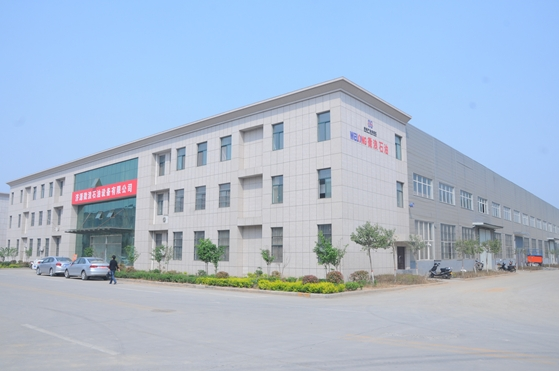
CHINA WELONG - 20+ years manufactuer in oilfield tools