What is the purpose of a float collar?
A float collar is a crucial component in the drilling and cementing process, primarily used to prevent backflow during the cementing operation. Positioned near the top of the casing string, just below the float shoe, the float collar contains a non-return valve that allows cement to flow into the annular space around the casing while preventing the backflow of cement into the casing. This ensures that the cement stays in place, providing the necessary sealing and zonal isolation required to maintain the integrity of the wellbore.
The purpose of the float collar is to maintain pressure during the cementing process and ensure that the cement remains in place after it has been pumped into the annular space. Without the float collar, there could be serious issues, such as loss of pressure and improper cement placement, both of which can lead to well integrity problems, formation damage, or costly delays. The float collar is designed to work alongside the float shoe, a tool positioned at the bottom of the casing to guide the casing string into the wellbore. Together, they form a complete system to ensure that the cementing operation is effective and the wellbore remains stable.
How Does a Float Collar Help Prevent Backflow During Cementing?
The float collar plays an indispensable role in preventing backflow during cementing by providing a robust mechanism that keeps the cement in place after it is pumped into the wellbore. The backflow of cement is a common problem in drilling operations, and it can lead to a series of complications, including improper cement placement and pressure loss. A float collar effectively addresses this challenge through the following mechanisms:
Non-Return Valve
The float collar is equipped with a non-return valve, an essential feature that allows fluid to flow in only one direction—into the annular space around the casing. This valve automatically closes after cement is pumped into the wellbore, preventing any backflow of the cement into the casing. The non-return valve is crucial for maintaining the integrity of the cementing process because it ensures that the cement remains in the desired position within the annular space. By preventing the cement from flowing back into the casing, the valve plays a vital role in securing the zonal isolation and preserving wellbore stability. Its one-way function helps to avoid the displacement of cement and ensures that the cement job is completed effectively.
Pressure Maintenance
One of the primary functions of the float collar is to maintain pressure during the cementing process. Cementing is a delicate operation, and maintaining pressure is critical to ensure that the cement is placed accurately and securely. The float collar prevents cement backflow, which is essential for maintaining a stable and consistent pressure in the system. Without the float collar, backflow could lead to a loss of pressure, which would interfere with the cement placement process. Such a loss could result in incomplete or uneven distribution of cement, compromising the wellbore’s integrity and the zonal isolation required to prevent fluid migration. By ensuring pressure is maintained throughout the cementing operation, the float collar helps achieve the desired cement distribution, improving the quality and durability of the cement job.
Ensuring Proper Cement Placement
Proper cement placement is a critical part of the well completion process, as it ensures the wellbore is isolated and sealed correctly. Without the float collar, there would be a risk of cement backflow into the casing, which could lead to improper placement and incomplete sealing of the annular space. The float collar ensures that the cement stays in place, forming a solid barrier that isolates different pressure zones within the well. This barrier is crucial for preventing fluid migration between zones, which could otherwise lead to issues like formation damage or wellbore instability. Proper cement placement is also necessary to protect the well from external forces, such as water or gas migration, which could jeopardize the well’s long-term integrity. Therefore, the float collar plays a vital role in ensuring that the cement job is done correctly, providing a reliable seal that contributes to the overall success of the well’s completion and ongoing stability.
What Is the Difference Between a Float Collar and a Float Shoe?
Although both the float collar and float shoe are designed to work together in cementing operations, they serve distinct purposes in the process. Understanding the differences between the two tools is vital for ensuring that they are used effectively.
Location in the Casing String
The float shoe and float collar are integral components of the casing string, each positioned strategically for different but complementary roles in the cementing process. The float shoe is typically placed at the very bottom of the casing string, where it serves as the first point of contact with the wellbore. Its primary function is to guide the casing string into the well and ensure it is properly positioned. The float collar, positioned just above the float shoe, is designed to prevent the backflow of cement into the casing after the cementing operation begins. While both tools are essential, their placement within the casing string helps to optimize the cementing procedure and ensure that each element functions at its highest efficiency.
Functionality
The float shoe is equipped with a built-in check valve that facilitates the one-way flow of cement into the annular space between the casing and the wellbore. Once the cement is pumped into the wellbore and the pumping stops, the check valve automatically prevents cement from flowing back into the casing. This mechanism ensures that the cement stays in place and is distributed to the correct areas of the wellbore, providing the necessary zonal isolation. The float collar works in tandem with the float shoe but has a more focused role in maintaining the pressure during the cementing operation. By preventing backflow, the float collar ensures that the cement stays in place, keeping the wellbore sealed and preventing contamination of the cement slurry.
Role in Cementing
Both the float shoe and float collar are crucial for the success of the cementing operation, but each tool plays a distinct role in the process. The float shoe’s primary responsibility is to guide the casing string into the wellbore and provide an initial seal that prevents fluids from entering the casing, which could affect the cementing operation. On the other hand, the float collar focuses on maintaining pressure throughout the cementing job by preventing any backflow of cement into the casing. The float collar also ensures that the cement is properly placed in the annular space around the casing, ensuring that the wellbore remains isolated from other zones and preventing the migration of fluids between them. Together, these two components ensure that the cementing job is executed correctly, the pressure is maintained, and the wellbore’s integrity is preserved, contributing to the long-term stability and success of the well.
How Does a Float Collar Work with a Float Shoe in Well Cementing?
The float collar and float shoe are designed to work together seamlessly to ensure the success of cementing operations. While each tool has its own specific role, they complement each other to create an efficient system that helps prevent backflow, maintain pressure, and achieve proper cement placement. Here’s how these two tools collaborate:
Casing Guidance and Pressure Control
The float shoe plays a crucial role in guiding the casing string into the wellbore. Positioned at the bottom of the casing, it ensures that the casing is properly aligned and positioned as it is lowered into place. The float shoe is equipped with a check valve, which is vital for preventing the backflow of fluids into the casing while cement is being pumped. This prevents contamination or displacement of the cement slurry and ensures the integrity of the wellbore. Above the float shoe is the float collar, which also features a non-return valve. The float collar serves to maintain pressure in the casing once cementing has stopped, preventing any unwanted fluid migration. By combining these two components, the casing system is effectively guided, and the wellbore pressure is controlled throughout the cementing process, reducing the risk of failure or complications.
Flow Control
The float shoe and float collar work together to manage the flow of cement during the cementing operation. The float shoe directs the cement into the annular space between the casing and the wellbore, ensuring that the space is filled uniformly. This controlled flow is essential to prevent any gaps or voids in the cement, which could lead to problems such as poor zonal isolation or wellbore instability. The float collar, located just above the float shoe, plays a key role in ensuring the cement remains in place after the pumping stops. Its non-return valve prevents the backflow of fluids, maintaining the position of the cement slurry and ensuring it doesn’t migrate back into the casing. Together, these components effectively control the placement of cement and guarantee that it is pumped to the correct depth, ensuring that the wellbore is sealed properly.
Zonal Isolation and Integrity
The primary function of the float collar and float shoe combination is to provide zonal isolation. Zonal isolation refers to the process of ensuring that the cement slurry is placed correctly around the casing, creating a barrier that prevents the migration of fluids between different pressure zones within the wellbore. This is essential for maintaining the integrity of the well and ensuring that there is no communication between formations with different pressure profiles. Proper zonal isolation prevents issues such as cross-contamination between different geological formations, which could lead to operational challenges or safety concerns. By ensuring that the cement remains in place and forms a continuous seal, the float shoe and float collar help maintain wellbore stability throughout the life of the well. This comprehensive solution is vital for ensuring the long-term success and safety of the well, as it contributes to both pressure management and the prevention of fluid migration that could jeopardize well integrity.
Why Is a Float Collar Crucial for Maintaining Pressure in Drilling Operations?
In drilling operations, maintaining proper pressure is essential for ensuring that the wellbore remains stable and that drilling operations can proceed without complications. The float collar is an important tool for pressure maintenance during the cementing process, and it plays a crucial role in preventing pressure loss that can lead to drilling issues. Here’s why the float collar is essential for maintaining pressure:
Preventing Backflow
The float collar plays a critical role in preventing the backflow of cement into the casing after it has been successfully pumped into the annular space. It achieves this by using a non-return valve, which acts as a one-way mechanism, allowing cement to flow only in the desired direction during the cementing process. This is particularly important for maintaining the pressure within the wellbore. If the cement were to flow back into the casing, it could cause a loss of pressure, leading to the potential for unwanted fluid migration and compromising the integrity of the well. The backflow could also disrupt the cementing process, resulting in poor cement bonding, which could jeopardize the well's long-term stability. By preventing backflow, the float collar ensures that the cement slurry remains in place, preserving the wellbore's structural integrity.
Pressure Control During Cementing
During the cementing process, maintaining consistent pressure is essential for the successful placement of cement and the sealing of the annular space between the casing and the wellbore. The float collar plays a vital role in this pressure control by preventing the cement from flowing back into the casing. This ensures that the pressure in the wellbore remains stable throughout the cementing process. Stable pressure allows the cement slurry to fill the annular space evenly and completely, providing a continuous seal that prevents fluid migration between formations. This also reduces the risk of gaps or voids in the cement, which could compromise zonal isolation. The float collar's ability to maintain pressure stability during cementing ensures that the entire process is executed effectively, which is critical for the well’s long-term success.
Ensuring Wellbore Integrity
The wellbore's integrity is fundamental for ensuring that the well can withstand the challenges of various pressure zones and environmental conditions over its operational life. The float collar helps maintain wellbore integrity by preventing pressure fluctuations during cementing. Without a properly functioning float collar, pressure imbalances could occur, leading to issues such as uneven cement placement, loss of zonal isolation, or compromised cement bonding. These risks can result in significant operational challenges, including wellbore instability, fluid migration, and the failure of the well to isolate different geological formations properly. By maintaining a consistent pressure throughout the cementing process, the float collar ensures that the cement job is completed accurately and that the wellbore remains stable, providing a solid foundation for future operations.
What Are the Main Functions of a Float Collar in Oil and Gas Drilling?
The float collar is an essential component in oil and gas drilling, serving several key functions that contribute to the success of drilling operations. These functions include:
Preventing Backflow of Cement
The primary function of the float collar is to prevent the backflow of cement during cementing operations. Equipped with a non-return valve, the float collar ensures that cement stays in place after it is pumped into the annular space around the casing. This is crucial for maintaining wellbore pressure and achieving proper zonal isolation.
Pressure Maintenance
The float collar helps maintain pressure in the wellbore during cementing. By preventing cement backflow, it ensures that the wellbore remains pressurized, which is essential for proper cement placement and maintaining the integrity of the wellbore. This function is vital for preventing pressure loss and ensuring that the cement is properly placed at the required depth.
Ensuring Proper Cement Placement
Another critical function of the float collar is to ensure that the cement is placed correctly in the wellbore. By preventing backflow, the float collar ensures that the cement remains in place, forming a solid seal between the casing and the formation. This is essential for zonal isolation and preventing fluid migration between different pressure zones.
Can a Float Collar Be Used Without a Float Shoe?
In most cases, the float collar is used in conjunction with a float shoe for maximum efficiency in cementing operations. However, it is technically possible to use a float collar without a float shoe in certain situations, depending on the specific requirements of the drilling operation.
In Case of Special Cementing Requirements
There may be situations where a float collar is used without a float shoe, such as when special cementing techniques or tools are required. In these cases, the float collar may serve as the primary mechanism for preventing backflow and maintaining pressure during cementing. However, using a float collar without a float shoe can limit the ability to properly guide the casing string into the wellbore.
Potential Risks and Limitations
While a float collar can be used without a float shoe, it may not provide the same level of guidance for the casing string during installation. This could result in challenges during casing installation and lead to misalignment or other issues. Additionally, using a float collar without a float shoe may increase the risk of cement backflow, making it less ideal for some drilling operations.
Best Practices
It is generally recommended to use both the float collar and float shoe together to ensure optimal cementing results. By working together, these tools provide the necessary guidance, pressure maintenance, and backflow prevention needed to ensure a successful cement job and maintain wellbore integrity.
Conclusion
The float collar is an indispensable tool in the cementing process, playing a critical role in preventing backflow, maintaining pressure, and ensuring proper cement placement. While it can technically be used without a float shoe, it is best to use both tools together for optimal results. The float collar helps ensure the stability of the wellbore, provides zonal isolation, and contributes to the long-term integrity of the well.
When selecting a taper mill for your drilling application, it's essential to consider factors such as well depth, material type, and operational requirements. At China Welong, we offer a wide range of taper mills designed to meet the demands of modern drilling operations. Our taper mills are built for durability, efficiency, and performance, ensuring that your drilling process runs smoothly.
For more information about float collars and other essential oilfield products, contact us at oiltools15@welongpost.com.
References
1. "Cementing Tools and Techniques," Journal of Petroleum Technology, 2022.
2. "Fundamentals of Drilling and Cementing Operations," SPE, 2021.
3. "Advanced Well Completion Techniques," Oil and Gas Journal, 2023.
4. "Design and Application of Cementing Tools," SPE Technical Paper, 2020.
5. "Wellbore Integrity and Zonal Isolation," International Journal of Oil and Gas, 2022.
6. "Casing and Cementing Operations: A Comprehensive Overview," Petroleum Review, 2021.
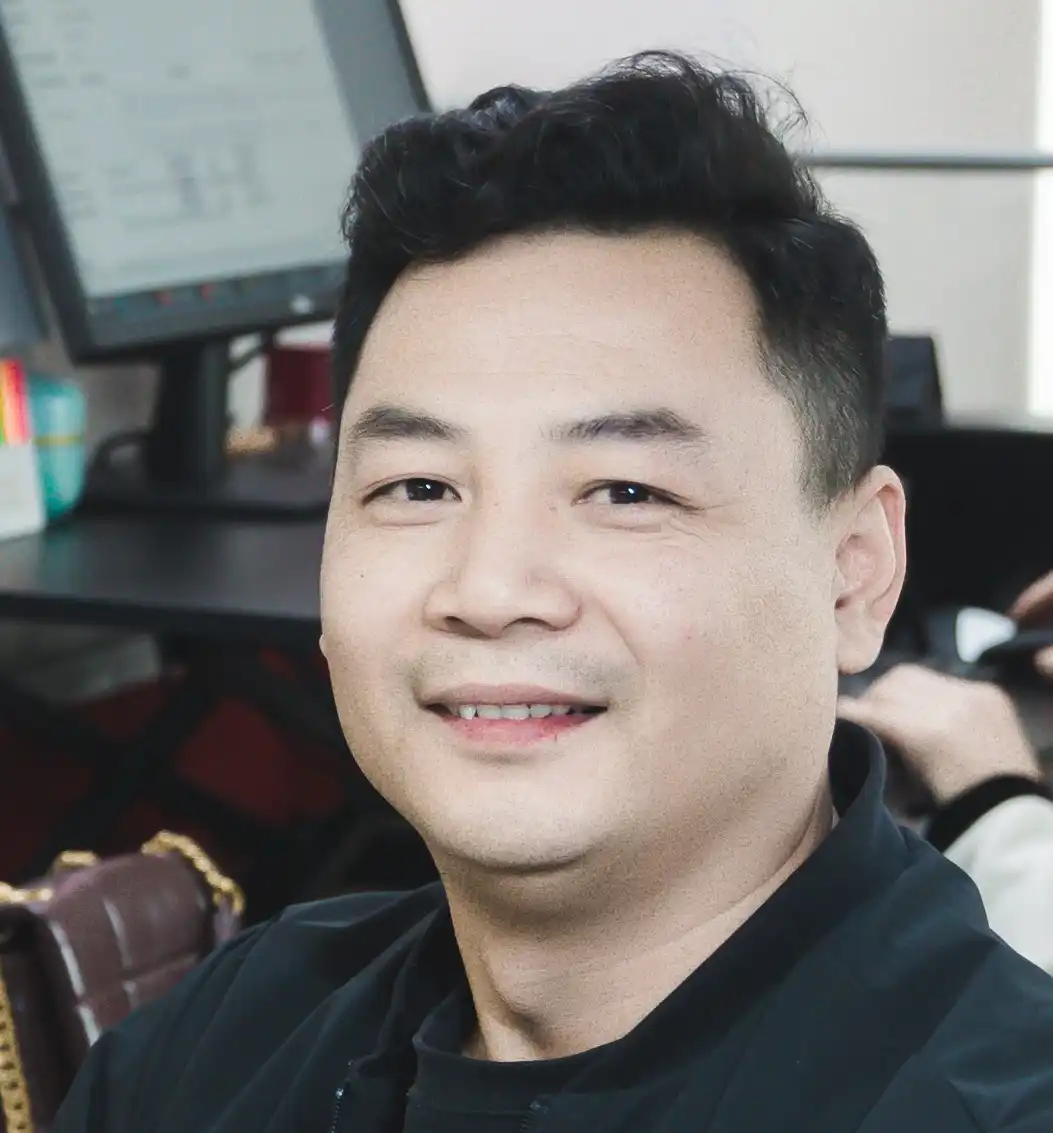
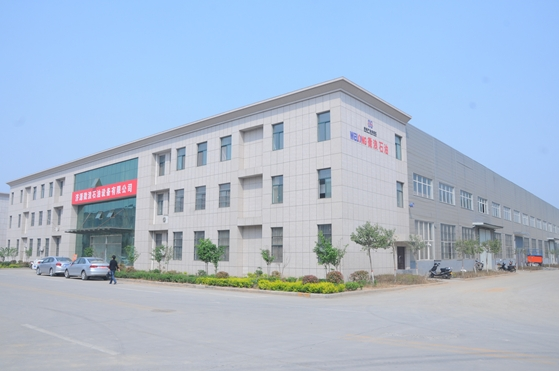
CHINA WELONG - 20+ years manufactuer in oilfield tools