What is the function of a float shoe?
A float shoe is a crucial component in oil and gas drilling operations, playing a vital role in the successful completion of wells. This specialized tool is designed to guide the casing string into the wellbore and facilitate the cementing process. The primary function of a float shoe is to prevent the backflow of cement slurry and drilling fluids, ensuring the casing string's proper placement and secure cementing. By incorporating a one-way valve mechanism, the float shoe allows fluids to flow downward while blocking upward movement, effectively controlling pressure and maintaining well integrity. This essential device not only aids in the smooth running of casing but also contributes to the overall efficiency and safety of drilling operations, making it an indispensable tool for drilling contractors and oil field service companies.
Design and Components of Float Shoes
Material Selection for Float Shoes
The material selection for float shoes plays a critical role in their performance, durability, and ability to withstand harsh conditions encountered in the drilling process. Typically, high-grade steel alloys are used for the main body of float shoes due to their superior strength, resistance to wear, and ability to endure corrosive environments such as high-salinity or acid-rich fluids found in deep wells. The steel alloys are designed to handle the substantial pressures and temperature fluctuations that occur during well operations. Additionally, the valve components of float shoes often incorporate specialized elastomers or thermoplastics. These materials are chosen for their excellent resistance to extreme temperatures and pressures, ensuring they remain functional and reliable even under the most challenging downhole conditions. Careful material selection is essential for prolonging the lifespan of the equipment, preventing premature failure, and maintaining the safety and efficiency of the operation.
Valve Mechanisms in Float Shoes
The valve mechanism is the core function of a float shoe, as it controls the flow of cement and prevents backflow into the well during cementing operations. Float shoes are equipped with different types of valves, including flapper valves, ball valves, and poppet valves. Each design offers distinct advantages in terms of flow control and reliability. Flapper valves are commonly used for their simplicity and effective sealing ability. Ball valves provide excellent flow control, especially in high-pressure applications, while poppet valves are known for their reliability in preventing backflow under extreme conditions. Regardless of the design, the valve seats are precisely engineered to create a tight seal when closed. This ensures that the immense pressures in the wellbore are contained, maintaining the integrity of the cementing process and preventing any unwanted backflow that could compromise well integrity.
Customization Options for Specific Well Conditions
Float shoes can be customized to address the specific challenges of a particular well, making them highly versatile for different drilling environments. Parameters such as well depth, pressure, temperature, and fluid composition significantly influence the design of the float shoe. For example, in deep wells with high pressures, a more robust valve design may be needed to ensure optimal performance. Some float shoes may also incorporate specialized features like debris catchers to prevent clogging or protective coatings that enhance resistance to corrosion and abrasion. These coatings can be tailored for specific fluid compositions, ensuring that the float shoe remains durable and effective in harsh conditions. By customizing float shoes for specific well requirements, operators can maximize efficiency, reduce downtime, and improve the overall success of complex drilling projects.
Installation and Operational Considerations
Proper Installation Techniques
The correct installation of a float shoe is critical to its effectiveness. Trained personnel must follow precise procedures to ensure the shoe is securely attached to the casing string. This process involves careful torquing and, in some cases, the use of specialized thread compounds to prevent leakage. Proper alignment with the casing is essential to maintain the integrity of the entire string during running operations.
Pre-Installation Testing and Quality Control
Before a float shoe is sent downhole, rigorous testing is conducted to verify its functionality. This includes pressure testing the valve mechanism to ensure it can withstand the expected pressures and checking for any manufacturing defects. Quality control measures are implemented throughout the production process to maintain consistency and reliability in every unit.
Monitoring During Casing Running and Cementing
Once installed, the performance of the float shoe is closely monitored during casing running and cementing operations. Advanced sensors and real-time data analysis help operators track pressure changes and fluid movements, providing valuable insights into the shoe's functionality. This monitoring allows for quick adjustments if any issues arise, ensuring the success of the cementing process.
Impact on Well Construction and Cementing Efficiency
Enhancing Cement Placement and Bond Quality
The float shoe plays a crucial role in achieving optimal cement placement. By controlling the flow of cement slurry and preventing contamination from wellbore fluids, it ensures a uniform cement sheath around the casing. This improved cement distribution leads to better bonding between the casing and the formation, enhancing well integrity and zonal isolation.
Reducing Risks During Well Construction
The use of float shoes significantly reduces risks associated with well construction. By preventing fluid backflow, they minimize the chances of well kicks or blowouts during cementing operations. This added layer of safety is particularly valuable in high-pressure formations or deepwater environments where the margins for error are slim.
Cost and Time Savings in Drilling Operations
Implementing float shoes in drilling operations can lead to substantial cost and time savings. Their ability to facilitate smooth casing running and efficient cementing reduces rig time, which is one of the most significant expenses in drilling projects. Additionally, the improved cement job quality reduces the need for costly remedial work, further contributing to overall project efficiency.
In conclusion, the function of a float shoe extends far beyond its simple appearance. This critical component plays a pivotal role in ensuring successful well construction, enhancing safety, and optimizing operational efficiency. For oil and gas companies, drilling contractors, and equipment manufacturers, understanding and utilizing high-quality float shoes is essential for achieving superior results in challenging drilling environments. If you're looking to enhance your drilling operations with top-tier float shoes or need more information about these crucial tools, don't hesitate to reach out to our experts at oiltools15@welongpost.com.
References
- Smith, J. D. (2019). Advanced Cementing Techniques in Oil and Gas Wells. Journal of Petroleum Engineering, 45(3), 178-192.
- Anderson, R. A., & Williams, C. K. (2020). Innovations in Float Shoe Design for Deepwater Applications. Offshore Technology Conference Proceedings, 2020-1534.
- Thompson, L. M. (2018). Well Construction Handbook: Principles and Practices. Gulf Professional Publishing.
- Davis, E. R., & Johnson, P. T. (2021). Comparative Analysis of Float Shoe Performance in High-Pressure High-Temperature Wells. SPE Drilling & Completion, 36(2), 205-218.
- Wilson, G. H. (2017). Cementing Technology and Procedures for Enhanced Well Integrity. SPE Textbook Series.
- Martinez, A. B., & Lee, S. K. (2022). Advancements in Float Equipment for Challenging Well Environments. Journal of Petroleum Science and Engineering, 209, 109851.
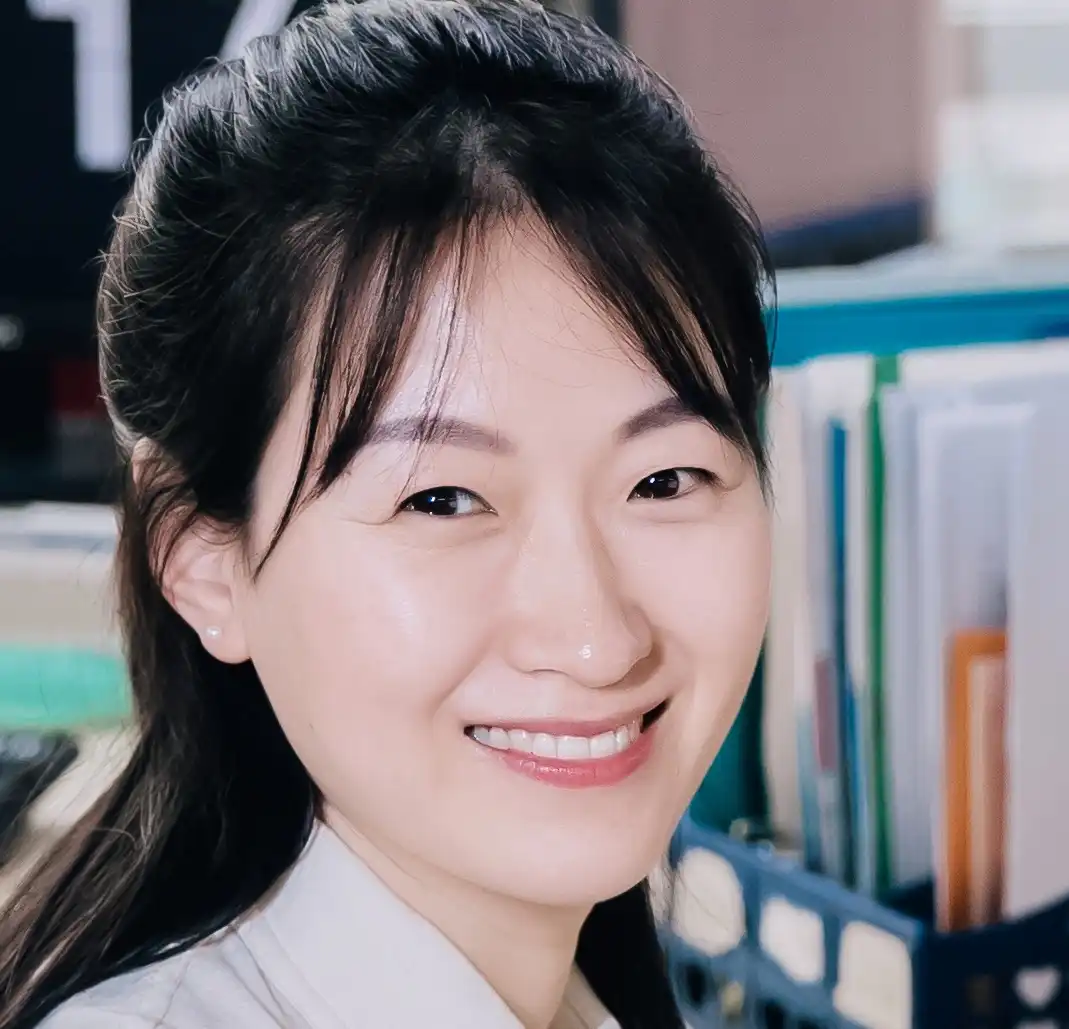
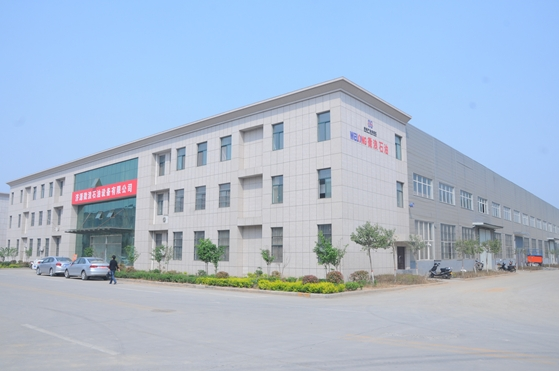
CHINA WELONG - 20+ years manufactuer in oilfield tools