Benefits of float shoe you want to know
The float shoe is a critical component in well cementing operations, particularly in the oil and gas industry. Its main function is to prevent backflow during the cementing process by allowing the cement to flow in one direction only. The float shoe’s one-way valve design ensures that the cement stays in place, helping to stabilize the wellbore. This prevents the cement slurry from escaping or being displaced by fluids from the wellbore, which could lead to significant operational setbacks.
A float shoe also plays an essential role in controlling pressure and preventing damage to the casing and wellbore during cementing. By creating a seal that prevents the backflow of drilling fluids, it helps to maintain the desired pressure profile within the well. This pressure control is vital for the integrity of the cement job and the overall wellbore structure, minimizing the risk of costly issues such as gas migration or casing damage.
Furthermore, the float shoe is designed to be installed at the bottom of the casing string, facilitating smooth installation while contributing to overall cement placement efficiency. The tool’s efficiency and reliability make it a staple in modern drilling operations, offering enhanced safety, pressure control, and wellbore stability. With this, drilling teams are able to maintain proper operational flow and safeguard the well for further development.
How Does a Float Shoe Prevent Backflow During Drilling?
A float shoe serves an essential function in well cementing by preventing backflow, which is critical for ensuring the integrity and stability of the wellbore. The design of the float shoe includes a one-way valve that allows cement to flow in only one direction—downward—while blocking any reverse flow of fluids from the wellbore. This feature helps maintain the proper pressure in the casing and ensures that the cement slurry remains in place after being pumped into the wellbore.
Backflow prevention is especially crucial during cementing because, without it, drilling fluids or gas can migrate back into the annulus, which can negatively impact cement placement. If the cement slurry is displaced by wellbore fluids, the well integrity is compromised, leading to potential issues like gas channels, which can result in dangerous conditions such as well control problems or contamination.
In addition to pressure control, the float shoe effectively mitigates the risks associated with wellbore instability. By preventing reverse flow, it reduces the chances of any wellbore damage that could otherwise lead to costly repairs or even safety hazards. Its effectiveness in managing pressure ensures that the cement fills all voids around the casing, creating a strong bond between the casing and the formation that prevents wellbore collapse or gas migration.
For drilling contractors, using a float shoe during cementing is a reliable method to improve the safety of the operation. This tool not only provides a simple and effective solution to backflow issues but also contributes significantly to overall well control, reducing the risk of non-productive time (NPT) and ensuring a more successful drilling process.
What Are the Key Advantages of Using a Float Shoe in Well Cementing?
The float shoe offers several advantages during the well cementing process, making it an indispensable tool for drilling operations. These benefits directly contribute to the safety, efficiency, and success of wellbore operations. Here are the key advantages of using a float shoe:
Prevents Backflow and Maintains Well Integrity: As discussed, the primary function of a float shoe is to prevent backflow during cementing. By ensuring that wellbore fluids cannot return to the casing after the cement slurry is injected, it helps maintain the integrity of the wellbore. This is crucial for ensuring that the well is properly sealed, reducing the risk of contamination or instability in the formation.
Ensures Proper Cement Placement: Cementing is a critical operation that ensures the proper sealing of the wellbore and the casing. The float shoe plays a significant role in preventing the displacement of cement slurry by wellbore fluids, ensuring that the cement reaches the desired location and stays in place. It helps in ensuring that the annular space between the casing and the formation is adequately filled, creating a strong bond that prevents issues such as gas migration or wellbore collapse.
Helps Maintain Pressure Control: One of the most crucial aspects of drilling is maintaining pressure control. A float shoe helps to maintain pressure in the well during cementing by preventing the influx of unwanted fluids or gases. This is particularly important in high-pressure environments, where improper pressure management can lead to serious operational hazards. By allowing only cement to flow into the casing and preventing any backflow, the float shoe helps stabilize the wellbore pressure and ensures that the cementing process is performed under controlled conditions.
Reduces the Risk of Non-Productive Time (NPT): In the fast-paced world of drilling, downtime is costly. The float shoe helps minimize the risk of NPT by providing a reliable and straightforward solution to backflow issues, ensuring that cementing operations proceed without interruptions. This contributes to overall operational efficiency and helps keep drilling operations on schedule.
Versatility in Use: The float shoe is a versatile tool that can be used in various types of drilling environments, from shallow to deepwater drilling. Its design allows it to be adapted to different wellbore conditions, making it suitable for a wide range of cementing applications. This flexibility makes it an essential tool for drilling contractors working in diverse environments.
Cost-Effective Solution: While quality equipment can sometimes be an investment, the long-term benefits of using a float shoe make it a cost-effective solution. By preventing backflow, ensuring proper cement placement, and reducing the risk of pressure control problems, the float shoe helps prevent costly issues such as wellbore instability, gas migration, and contamination. This makes it a crucial tool for cost-effective and efficient drilling operations.
In conclusion, using a float shoe in well cementing brings a wide range of benefits, from preventing backflow and ensuring proper cement placement to maintaining pressure control and reducing NPT. These advantages make it an indispensable part of any drilling contractor’s toolkit, ensuring the success and safety of drilling operations.
Why Is a Float Shoe Important for Pressure Control in Drilling?
Maintaining pressure control is crucial in drilling operations to avoid well control incidents, such as blowouts or influxes of unwanted fluids and gases. The float shoe plays a pivotal role in managing pressure during cementing operations, which are inherently sensitive to pressure fluctuations. Here’s why it is so important:
Prevents Influx of Formation Fluids: One of the most critical roles of a float shoe is to prevent the influx of formation fluids into the wellbore during the cementing process. The float shoe effectively isolates the wellbore from the surrounding formation by allowing only cement to enter the casing while preventing the flow of any unwanted fluids such as gas or oil. This is essential for maintaining a stable pressure environment in the wellbore, ensuring that pressures do not spike or drop unexpectedly during cementing operations.
Maintains Positive Pressure during Cement Placement: When cement is pumped into the wellbore, it is vital to ensure that there is enough pressure to displace other wellbore fluids and create a solid bond between the casing and the formation. The float shoe helps maintain this positive pressure by preventing the well fluids from flowing back into the casing, which could reduce the effectiveness of the cement placement. This control ensures that the cement reaches the desired position and that the annular space is filled properly, creating a seal that will help stabilize the wellbore and prevent further pressure issues.
Reduces the Risk of Well Control Problems: The float shoe helps reduce the likelihood of well control problems during cementing by ensuring that the pressure in the wellbore remains consistent and controlled. Without a float shoe, the potential for backflow increases, leading to pressure fluctuations and potentially dangerous situations. Well control issues can lead to costly delays and even catastrophic failures, making the float shoe an essential component for ensuring operational safety and stability.
Prevents Pressure Loss After Cementing: After the cement has been placed in the wellbore, it is crucial to ensure that the pressure is maintained until the cement cures and hardens. The float shoe serves as a barrier, preventing pressure loss from the casing into the formation. This is especially important in deep wells, where the pressure at the surface can be significant. Without the float shoe, there is a risk that pressure loss could lead to a failure in the cementing job or even an unstable wellbore.
Helps to Manage Differential Pressure: During cementing, the wellbore experiences differential pressure between the inside of the casing and the formation. If this differential pressure is not managed correctly, it can lead to problems such as lost circulation or formation damage. The float shoe helps manage these pressure differences by providing a controlled mechanism for cement to flow into the casing while keeping formation fluids at bay. This pressure regulation minimizes the risks associated with differential pressure and helps maintain wellbore stability.
Increases Operational Efficiency: By facilitating better pressure control during the cementing process, the float shoe contributes to overall operational efficiency. Wellbore pressure can be better regulated, reducing the risk of cement placement failures and eliminating the need for costly remedial work. This leads to faster, more reliable cementing operations, ultimately contributing to a more efficient and profitable drilling operation.
In summary, the float shoe plays an essential role in pressure control by preventing the influx of formation fluids, maintaining positive pressure during cement placement, and reducing the risk of well control issues. Its ability to maintain stable pressure in the wellbore ensures the success of cementing operations and minimizes the risk of wellbore instability and pressure-related problems.
What Role Does a Float Shoe Play in Preventing Damage to the Wellbore?
In drilling operations, protecting the integrity of the wellbore is crucial for the success of the entire project. The float shoe plays a critical role in preventing damage to the wellbore during cementing, ensuring the longevity and stability of the well. Here's how:
Prevents Backflow During Cementing: One of the most common causes of wellbore damage during cementing operations is backflow, where cement or fluids flow back into the wellbore, potentially carrying unwanted formation fluids or debris into the casing. The float shoe acts as a one-way valve, preventing backflow from occurring during cement placement. By keeping unwanted fluids from entering the wellbore, the float shoe helps preserve the wellbore's structural integrity, ensuring that the casing is properly cemented and secured without risking contamination or other damage.
Protects the Wellbore from Overpressurization: Overpressurization of the wellbore is another significant threat to its integrity. When cement is pumped into the wellbore, there is a risk that the pressure could exceed the formation’s fracture pressure, leading to formation damage, lost circulation, or even blowouts. The float shoe plays a key role in protecting the wellbore by controlling the pressure within the casing during cementing. By preventing pressure surges and allowing for a controlled, steady flow of cement, the float shoe helps avoid overpressurization, which could lead to fractures in the formation or other forms of wellbore damage.
Helps Maintain Wellbore Integrity Post-Cementing: After the cementing job is completed, the wellbore needs to be stable enough to support subsequent operations, such as drilling and production. If the cementing job is compromised due to backflow or pressure imbalances, the wellbore’s integrity can be threatened, potentially causing issues during later stages of the operation. The float shoe helps maintain the wellbore’s integrity by ensuring that cement is placed effectively, forming a solid bond between the casing and the formation. This bond stabilizes the well and prevents damage from formation fluid influxes, which could otherwise undermine the wellbore's strength and stability.
Prevents Damage from Fluid Loss: When cement is pumped into the wellbore, there is always the risk that it will encounter lost circulation zones, where the cement escapes into the surrounding formation instead of remaining within the casing. This can weaken the cement job and lead to further wellbore instability. The float shoe helps mitigate this issue by preventing unwanted fluid loss and ensuring that the cement stays in place, especially in areas prone to lost circulation. This helps preserve the wellbore’s integrity and ensures that the cement bond remains intact, preventing further damage from occurring.
Minimizes the Risk of Erosion: During the cementing process, turbulent fluid flow can lead to erosion of the wellbore. The float shoe helps regulate the flow of cement and other fluids into the casing, minimizing turbulence and preventing erosion at critical points in the wellbore. By maintaining a steady and controlled flow, the float shoe reduces the risk of erosion, which could otherwise weaken the casing and lead to wellbore damage.
Assists in Maintaining Wellbore Stability in Challenging Conditions: Drilling in challenging environments—such as deep-water wells or high-pressure, high-temperature formations—presents a variety of risks to the wellbore, including excessive pressure, formation instability, and backflow. The float shoe helps mitigate these risks by providing a secure seal and ensuring that cement placement is carried out efficiently, even under the most challenging conditions. This is particularly important in environments where maintaining wellbore stability is crucial for the safety of the operation and the protection of the surrounding formation.
In conclusion, the float shoe plays an indispensable role in protecting the wellbore from damage during cementing operations. By preventing backflow, controlling pressure, minimizing fluid loss, and reducing the risk of erosion, it ensures the structural integrity of the well and helps maintain its stability for future operations. This protection is vital for ensuring the success of the drilling project and minimizing the risk of costly wellbore failures.
How Does a Float Shoe Work to Maintain a Stable Cementing Operation?
In well cementing, ensuring a stable and effective operation is essential for the integrity of the wellbore and the success of the drilling process. The float shoe plays a pivotal role in maintaining a stable cementing operation by managing the flow of cement, preventing backflow, and controlling pressure. Let’s explore how it works to keep cementing operations smooth and secure.
Preventing Backflow During Cementing: One of the main tasks of a float shoe is to act as a one-way valve, which prevents the backflow of cement and other fluids during the cementing process. When cement is being pumped into the casing, the float shoe ensures that the cement remains in place and does not flow back into the wellbore. This prevents contamination of the wellbore with unwanted fluids, such as formation water or gas, which could weaken the integrity of the well and make subsequent drilling or production operations more difficult.
Ensuring Proper Cement Placement: The effectiveness of the cementing job depends heavily on the proper placement of the cement slurry within the casing. The float shoe helps achieve this by creating a seal that prevents premature fluid migration. By holding the cement in place while it sets, the float shoe ensures that the casing is adequately bonded to the formation. This bond helps prevent issues such as gas leaks or water infiltration into the wellbore, which could compromise the well's ability to contain pressure and fluids.
Pressure Management During Cementing: Cementing operations generate a significant amount of pressure, which, if not properly controlled, can lead to formation damage, blowouts, or even lost circulation. The float shoe plays a critical role in pressure management by controlling the pressure differential between the wellbore and the cement slurry. It prevents over-pressurization during cement placement, ensuring that the pressure stays within the safe limits and preventing damage to the wellbore and surrounding formation. By maintaining a stable pressure environment, the float shoe helps ensure that the cementing operation is carried out without any risk to the well's structural integrity.
Eliminating Erosion and Turbulence: During cementing, turbulent fluid flow can cause erosion, leading to casing and wellbore damage. The float shoe helps mitigate this by regulating the flow of cement slurry. By reducing the risk of turbulence, it helps ensure that the cement is deposited evenly within the casing, preventing the erosion of the casing or the surrounding formation. This smooth and controlled flow not only improves the efficiency of the cementing process but also protects the wellbore from damage.
Maintaining the Integrity of the Casing: Once the cement is placed within the casing, it needs to set and bond with the formation to create a strong seal. The float shoe ensures that the casing remains in place during the setting process by preventing the migration of cement or other fluids. This helps maintain the integrity of the casing and ensures that the wellbore remains stable and secure throughout the cementing operation. By securing the casing in place, the float shoe contributes to the overall success of the cementing job and ensures the well can support future drilling, production, or exploration activities.
Supporting Effective Mud Circulation: The float shoe is also important for maintaining the circulation of drilling mud during cementing. After cement is placed, it’s essential to circulate mud to clear any remaining cement from the casing and to ensure the cement job is completed efficiently. The float shoe helps manage the flow of mud, ensuring that it circulates effectively without causing any blockages or disruptions in the cementing process. This ensures that the cement is placed properly, and that no residual mud or cement impedes further drilling or production.
In essence, the float shoe acts as an essential tool in stabilizing the cementing operation by preventing backflow, controlling pressure, and ensuring proper cement placement. These functions are vital for maintaining the wellbore's integrity and ensuring the success of the entire drilling process. The float shoe helps guarantee that the well can withstand future operational stresses, making it a cornerstone of any successful cementing job.
How Does a Float Shoe Contribute to Safe Drilling Practices?
In the high-stakes world of oil and gas drilling, safety is paramount. Every tool and piece of equipment involved in the drilling process must be reliable, durable, and effective at preventing hazards. The float shoe is no exception, as it plays a significant role in ensuring safe drilling practices. Let’s break down how the float shoe contributes to safer operations throughout the drilling process.
Minimizing the Risk of Wellbore Collapse: The primary purpose of cementing is to secure the wellbore and prevent any potential collapse. Without the float shoe, there could be uncontrolled fluid movement that might destabilize the wellbore, especially during the cementing stage. This instability can lead to wellbore collapse, which would not only halt operations but could lead to catastrophic safety incidents. The float shoe, by preventing backflow, ensures that the casing remains properly positioned and that the cement remains in place, providing vital support to the wellbore’s structure and minimizing the risk of collapse.
Preventing Blowouts: One of the most dangerous and costly events that can occur during drilling is a blowout. A blowout happens when the pressure inside the well exceeds the pressure that the casing and equipment can handle, leading to uncontrolled release of oil, gas, or other fluids from the well. The float shoe helps prevent blowouts by acting as a pressure-regulating valve. It keeps fluid pressure within safe limits by ensuring the cement does not prematurely flow back into the wellbore and that pressure from the formation is controlled. This reduction in pressure fluctuation is crucial for maintaining well control and preventing blowouts, which are a major safety risk in the industry.
Controlling the Flow of Cement and Fluids: The float shoe controls the flow of cement and fluids during cementing, preventing unwanted backflow that could cause contamination or mix with other wellbore fluids. This control ensures that cement is placed correctly, creating a stable barrier between the formation and the wellbore. Proper cement placement is essential for containing pressures safely and preventing gas or fluid migration, both of which could result in serious safety risks. By ensuring the cement remains in place, the float shoe helps to safeguard against future leaks or contamination that could jeopardize both the safety of the well and the surrounding environment.
Reducing the Risk of Gas Influx: Gas influx during cementing can be a major safety hazard. If gas enters the wellbore, it can cause significant pressure problems, blowouts, or other operational hazards. The float shoe helps mitigate this risk by preventing the backflow of gas into the casing. As a one-way valve, it ensures that fluids, including cement, remain in the desired location and prevents gas from migrating into the wellbore. This is essential for maintaining control over the well and ensuring that gas does not compromise the safety of the drilling process.
Ensuring Well Integrity During the Cementing Process: Cementing is a delicate process that requires precise control to ensure the integrity of the wellbore. The float shoe helps maintain this integrity by preventing the unwanted movement of fluids that could cause instability or contamination. Without the float shoe, the cement could flow backward into the well, or other fluids could mix, compromising the wellbore’s stability. This could lead to problems such as gas leakage or casing corrosion, both of which are safety hazards. By keeping the cement in place, the float shoe helps secure the well and ensures that it is structurally sound, enabling safe drilling and production.
Facilitating Emergency Response: In the event of an emergency, being able to quickly control the flow of fluids and pressure is critical. The float shoe assists in this by allowing for better control of the well. With the float shoe’s one-way valve mechanism, the pressure can be more easily managed, and the risk of uncontrolled fluid migration can be minimized. This adds an extra layer of safety, as it allows for rapid response if an unexpected situation arises, such as a sudden pressure spike or the entry of gas into the wellbore. Having a reliable float shoe means operators have better control and can react swiftly to ensure the safety of personnel and the environment.
Protecting Against Formation Damage: Drilling through formations often involves dealing with high-pressure environments, and the movement of fluids can cause formation damage if not properly controlled. The float shoe plays a critical role in protecting the formation by regulating the flow of fluids and maintaining a stable pressure environment. This protection is vital for ensuring the well’s long-term productivity and preventing any unexpected pressure changes that could damage the formation or lead to other safety hazards.
In conclusion, the float shoe contributes significantly to safe drilling practices by preventing blowouts, wellbore collapse, gas influx, and formation damage. It is an essential tool in maintaining control over the well during cementing operations, safeguarding both the well and the surrounding environment. The float shoe's ability to manage pressure, control fluid flow, and secure the wellbore helps to ensure that drilling operations are carried out safely and effectively.
Conclusion
The float shoe is an essential component in modern drilling operations, playing a vital role in maintaining well integrity, controlling pressure, preventing backflow, and ensuring the safety of the entire operation. Its ability to prevent backflow, reduce contamination risks, and contribute to a stable cementing process makes it indispensable in well construction. The float shoe ensures that fluids are properly managed, pressure is controlled, and the wellbore remains protected, leading to safer and more efficient drilling operations.
In short, the float shoe is a simple yet powerful tool that helps operators perform cementing jobs accurately and safely. By preventing backflow, maintaining pressure control, and protecting the wellbore, it significantly reduces the risks associated with drilling and cementing, ensuring that wells are built to last and are safe for future operations. The benefits of using a float shoe are clear, making it a fundamental tool for any successful drilling operation.
Contact our team at oiltools15@welongpost.com to discuss your requirements and receive expert guidance.
References
1. Smith, D., & White, R. (2016). Well Cementing: Principles and Practices. Society of Petroleum Engineers.
2. McLean, M. A., & Baker, R. S. (2014). Cementing Operations in the Oil and Gas Industry. Journal of Petroleum Technology, 66(10), 112-118.
3. Abass, H., & Yusoff, M. M. (2018). Role of Float Equipment in Well Integrity and Cementing. SPE/IADC Drilling Conference and Exhibition, 1-10.
4. Wilson, J., & Thomas, B. (2019). Advancements in Float Shoe Design for Enhanced Cementing Performance. SPE/IADC Drilling Conference, 21-25.
5. Zhang, X., & Zhou, Y. (2017). Optimizing Cementing Job Using Float Shoes in Complex Wellbore Environments. SPE Annual Technical Conference and Exhibition, 1-9.
6. Patel, S., & Li, J. (2015). Understanding the Functionality of Float Equipment in Cementing and Well Control. SPE/IADC Drilling Conference and Exhibition, 78-85.
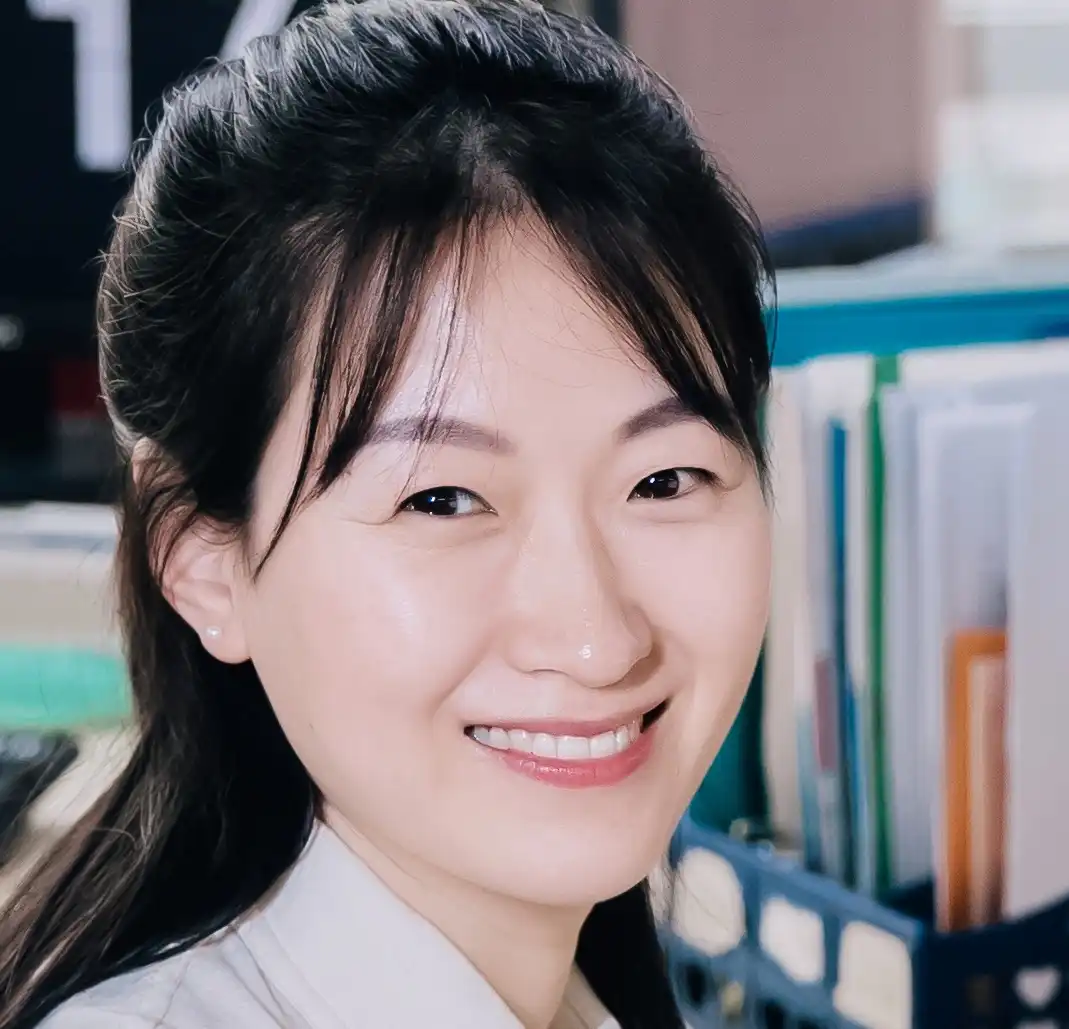
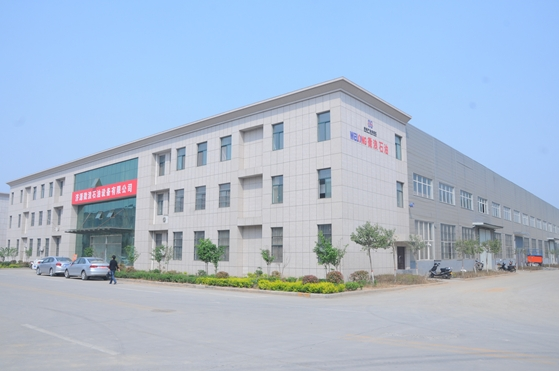
CHINA WELONG - 20+ years manufactuer in oilfield tools