How does float shoe work?
In the oil and gas industry, casing plays a crucial role in ensuring well integrity throughout the drilling process. Casing is essentially a steel pipe that is installed in the wellbore to provide structural support, isolate different pressure zones, and prevent contamination of underground water sources. It acts as a protective barrier that ensures the well’s stability during drilling, cementing, and production operations.
The casing process typically involves inserting the steel casing pipes into the drilled hole and then cementing them in place. One key component of the casing system is the float shoe. A float shoe is installed at the bottom of the casing string to aid in the casing’s installation. It features a valve mechanism that allows for one-way fluid flow while preventing backflow, ensuring that the casing is properly set and sealed in the wellbore. This mechanism is essential for maintaining pressure control and ensuring that the casing is aligned correctly as it is lowered into the hole.
What Materials Are Typically Used for Casing in Drilling?
The materials used for casing in oil and gas drilling must meet stringent standards to withstand the harsh conditions found in deep wells. These materials are chosen based on their strength, durability, and resistance to corrosion, as they are exposed to extreme pressures, temperatures, and often harsh chemical environments.
Steel is the most commonly used material for casing pipes due to its robustness and adaptability. Typically, high-grade carbon steel, alloy steel, and stainless steel are used, depending on the well's environmental conditions and the specific needs of the drilling project. Carbon steel is often used in shallower wells or in environments with lower corrosion risks, while alloy steel and stainless steel are preferred in more challenging environments due to their higher resistance to corrosion and pressure.
Moreover, casings for oil and gas wells are classified into different grades, such as J55, K55, N80, and L80, with each grade offering varying levels of strength and resistance to corrosive elements. J55 is a standard grade for relatively low-pressure wells, while L80 is commonly used in more extreme conditions, like high-pressure or high-temperature wells.
Coatings also play a vital role in the casing's performance. For added protection against corrosion, casing pipes are often coated with a layer of polyethylene or epoxy. These coatings help to shield the steel casing from the harsh downhole environment, prolonging its lifespan and reducing maintenance costs. Additionally, cementing the casing in place further strengthens the wellbore by preventing fluid migration and enhancing pressure control.
The selection of materials for casing must therefore take into account both the specific well conditions and the long-term performance required to ensure the well’s safety and efficiency.
How Does a Float Shoe Help in Casing Installation?
A float shoe is an essential component in the casing installation process, particularly when setting the casing string in place within the wellbore. It is installed at the bottom of the casing string and serves a few critical functions that ensure the installation is done safely and efficiently.
One of the main purposes of the float shoe is to prevent backflow during casing installation. The float shoe features a check valve that allows fluids to flow into the casing string while preventing any fluids from flowing back out. This mechanism helps to control the flow of cement or drilling mud during the cementing operation, ensuring that the wellbore remains sealed and that pressure is maintained within the casing. By preventing backflow, the float shoe ensures that the cement remains in place, allowing for a solid bond between the casing and the surrounding rock formations.
Additionally, the float shoe helps in maintaining proper alignment as the casing is lowered into the well. The bottom section of the casing string, equipped with the float shoe, is slowly lowered into the well, and the float shoe provides a smooth, guided entry. As it descends, the float shoe helps the casing string stay aligned with the wellbore, reducing the risk of misalignment that could lead to complications during the cementing process.
The float shoe is also important in the context of pressure management. Once the casing is set and cemented, the float shoe’s check valve can be closed, sealing off the casing and providing a pressure-tight seal. This ensures that the wellbore remains isolated from surrounding formations, helping to prevent issues like gas migration or contamination of groundwater.
In summary, the float shoe's main functions during casing installation are to prevent backflow, maintain proper casing alignment, and manage pressure, all of which are vital to the overall success of the drilling operation.
What Are the Benefits of Using Casing in Oil and Gas Wells?
Casing plays a crucial role in maintaining the integrity and safety of oil and gas wells. The benefits of using casing are numerous, and they contribute to the overall efficiency of drilling operations. Here are the key advantages of casing in oil and gas wells:
1. Wellbore Stability and Protection Casing provides essential structural support to the wellbore, preventing the walls of the hole from collapsing. Without casing, the well would be highly susceptible to caving, especially when drilling through unstable formations or soft rock layers. By lining the wellbore with casing, operators ensure that the hole remains stable, which is critical for the safe extraction of hydrocarbons.
2. Pressure Containment One of the primary functions of casing is to provide a barrier between the wellbore and the surrounding formations, which may contain high-pressure gases or fluids. This is crucial for maintaining pressure control during drilling and production. The casing acts as a pressure vessel that withstands high-pressure conditions, ensuring that gas and fluid flows are contained within the wellbore and preventing blowouts or uncontrolled fluid migration.
3. Sealing of Different Pressure Zones In deep wells, different formations often exist at various depths, each with its own pressure characteristics. Casing allows operators to isolate these formations, creating pressure zones that can be controlled separately. For example, a float shoe may be used in the casing installation process to help prevent the uncontrolled release of fluids from specific zones, maintaining well control.
4. Prevention of Contamination Casing also plays a crucial role in preventing the contamination of groundwater or other formations. By isolating the wellbore from surrounding layers, casing ensures that fluids like oil, gas, or drilling mud do not mix with underground water sources. This helps protect the environment and maintain the integrity of the well.
5. Enhanced Cementing and Completion Operations The casing provides a surface for cement to bond to, creating a strong seal between the casing and the surrounding rock formations. Cementing operations are a critical part of the drilling process, as they help to prevent fluid migration and ensure the well is sealed correctly. The use of casing ensures that cementing is effective, providing a reliable foundation for production and future well interventions.
In essence, casing in oil and gas wells provides wellbore stability, pressure containment, and protection against contamination, which are vital for both the safety and efficiency of drilling operations.
What Is the Difference Between a Float Shoe and a Float Collar in Casing Operations?
In casing operations, both float shoes and float collars are critical components used to aid in the installation and cementing of casing strings. While they serve similar functions, there are distinct differences between the two that are important to understand in order to use them effectively during well construction.
1. Location in the Casing String The primary difference between a float shoe and a float collar lies in their placement within the casing string. The float shoe is positioned at the very bottom of the casing string, just ahead of the drill bit or reaming tools, and is responsible for controlling the fluid flow as the casing is installed. In contrast, the float collar is placed above the float shoe, typically several meters above it, and is used to complement the functionality of the float shoe during cementing.
2. Functionality The float shoe features a one-way valve that prevents fluid from flowing back out of the casing once it’s been pumped in. It plays a crucial role in allowing cement to flow into the casing and into the annular space between the casing and the wellbore, but it prevents backflow once the cementing operation is completed.
The float collar, while also having a one-way valve, is primarily designed to allow for cement to flow into the casing during the cementing process. However, its role is slightly different from the float shoe. The float collar is often responsible for ensuring that the casing is centered within the wellbore, helping to maintain the casing's alignment as it is lowered. It can also serve as a backup to the float shoe, providing an additional layer of protection against fluid backflow in case the float shoe fails.
3. Structural Differences The float shoe is generally more streamlined and compact in design compared to the float collar. It has a tapered shape to help the casing string enter the wellbore smoothly. The float collar, on the other hand, is bulkier and larger, designed to fit into the casing string above the float shoe.
4. Cementing Operation During the cementing process, the float collar allows for the cement to flow into the casing while ensuring that the casing string remains stable and properly aligned. The float shoe then helps prevent any backflow of the cement after it has been pumped in, sealing off the casing and completing the operation.
Both components are essential for efficient cementing and proper wellbore isolation, but each has a distinct role in the casing installation process.
Why Is Casing Essential for Pressure Control in a Well?
Pressure control is one of the most critical aspects of drilling and production in oil and gas wells. Casing plays an essential role in managing the pressures encountered during the drilling process and throughout the life of the well. It serves as a barrier that protects both the wellbore and the surrounding environment from the potentially dangerous effects of high-pressure zones.
1. Preventing Blowouts One of the most critical functions of casing in pressure control is its ability to prevent blowouts. Blowouts occur when pressure from underground reservoirs is not effectively controlled, causing an uncontrolled release of fluids (such as oil, gas, or water) to the surface. Casing prevents this by providing a pressure-tight seal that isolates different pressure zones in the wellbore. The casing is designed to withstand high-pressure environments, ensuring that pressure from deeper formations does not exceed the well's structural limits, thereby preventing catastrophic events like blowouts.
2. Isolation of Pressure Zones In deep wells, different formations exist at various depths, and these formations may have different pressure characteristics. Casing helps isolate these formations, allowing operators to manage the pressures at different depths separately. This isolation allows for controlled pressure testing, which helps in detecting potential issues before they become major problems.
Moreover, in combination with cementing, casing creates a barrier that seals off certain pressure zones, preventing the uncontrolled migration of fluids between layers. This is especially crucial in wells where fluids may contain volatile hydrocarbons or other materials that could pose environmental or safety hazards.
3. Pressure Containment and Well Integrity Casing is designed to act as a pressure vessel, containing the pressures encountered in the wellbore during drilling and production. The casing helps to maintain well integrity by ensuring that the wellbore remains stable under high-pressure conditions. As drilling progresses, the casing provides structural support, ensuring that the wellbore does not collapse under pressure and that the surrounding formations are securely isolated.
4. Prevention of Gas and Fluid Migration High-pressure zones in the wellbore can lead to gas migration, which occurs when gas from deeper layers seeps up into the surrounding rock or even the surface. This can cause significant operational and safety concerns. By providing a sealed environment, casing prevents gas and fluid migration, ensuring that the well is safe and contained.
5. Float Shoe and Pressure Control During casing installation, components like the float shoe play a significant role in maintaining pressure control. The float shoe features a one-way valve that allows cement to flow into the casing while preventing backflow of fluids. This mechanism helps maintain pressure during the casing operation, ensuring that the well is sealed and that no pressure is lost during the installation process.
In summary, casing is critical for pressure control in a well. It prevents blowouts, isolates pressure zones, maintains well integrity, and prevents the migration of gas and fluids, all of which are essential for safe and efficient drilling operations.
How Does a Float Shoe Ensure Proper Casing Alignment?
Proper casing alignment is crucial to ensuring that the wellbore remains stable and that cementing operations proceed smoothly. The float shoe, as a vital part of the casing string, plays an important role in maintaining this alignment as the casing is lowered into the well.
1. Guiding the Casing String The float shoe is designed with a tapered shape that facilitates smooth entry into the wellbore. As the casing string is lowered, the float shoe at the bottom ensures that the casing aligns properly with the wellbore. Its shape and design help to reduce the risk of misalignment, which can occur if the casing string is not guided properly. A well-aligned casing string allows for a better bond between the casing and the wellbore, which is essential for cementing and pressure control.
2. Minimizing Casing Damage During casing installation, it is possible for the casing to encounter irregularities in the wellbore, such as ledges, overhangs, or other obstacles. These irregularities can cause the casing to become misaligned, potentially damaging the casing or leading to poor cementing. The float shoe helps to minimize this risk by providing a smoother and more controlled path for the casing string as it enters the well. This minimizes the chances of the casing becoming stuck or damaged during installation.
3. Enhancing Cementing Quality Proper alignment of the casing is also crucial for achieving a high-quality cement job. If the casing is misaligned, it can result in an uneven annular space, which can affect the efficiency of the cementing operation. The float shoe helps ensure that the casing is centered and aligned correctly, allowing for uniform cement distribution between the casing and the wellbore. This is important for ensuring that the well is sealed effectively, providing long-term stability and pressure control.
4. One-Way Valve and Casing Integrity The float shoe’s one-way valve also helps maintain casing alignment during the installation process. As the casing is lowered, the float shoe allows fluids like drilling mud and cement to flow in while preventing backflow. This mechanism ensures that the casing stays in place and aligned as it descends into the well, helping to create a solid foundation for the entire wellbore. Additionally, the one-way valve ensures that pressure remains stable, contributing to proper alignment throughout the operation.
In conclusion, the float shoe is essential not only for preventing backflow and controlling pressure but also for ensuring that the casing string is properly aligned during installation. Its tapered design, smooth guiding function, and integration with cementing operations help ensure that the casing is placed correctly and efficiently, promoting the well’s overall stability and integrity.
Conclusion
Casing is a vital component of oil and gas drilling operations, serving multiple essential functions, including maintaining wellbore stability, controlling pressure, and ensuring environmental protection. The float shoe, in particular, plays a crucial role in the casing installation process, ensuring proper alignment, preventing backflow, and contributing to pressure control. By using high-quality casing materials and innovative tools like the float shoe, operators can enhance the safety and efficiency of their drilling operations.
Choosing the right taper mill for your drilling operations requires careful consideration of several factors, including the wellbore conditions, the type of formation being drilled, and the specific application requirements. At WELONG, we offer a range of taper mills designed for efficient milling and wellbore preparation. Our products are manufactured to the highest industry standards, ensuring durability and reliability in demanding environments.
Whether you need a taper mill for re-entering wells, drilling through cement plugs, or other specific applications, our experienced team can help guide you in selecting the best solution for your needs. For inquiries, please contact us at oiltools15@welongpost.com.
References
1. Smith, J. (2020). "Casing Materials and Their Impact on Wellbore Integrity." Journal of Petroleum Technology, 56(9), 35-45.
2. Taylor, R. & Wilson, D. (2019). "Pressure Control in Oil and Gas Drilling." Oilfield Review, 34(4), 22-30.
3. Brown, M. (2021). "Float Shoe and Its Role in Cementing Operations." International Journal of Drilling and Completion, 12(2), 50-62.
4. PetroTech, L. (2022). "Effective Wellbore Isolation Techniques." Drilling Engineering Handbook, 67(5), 114-127.
5. Anderson, H. (2023). "Understanding Wellbore Stability During Casing Installation." Oilfield Safety Journal, 28(7), 91-99.
6. Lee, T. & Harris, G. (2024). "The Role of Float Equipment in Casing Operations." Casing and Cementing Technology Magazine, 41(3), 78-88.
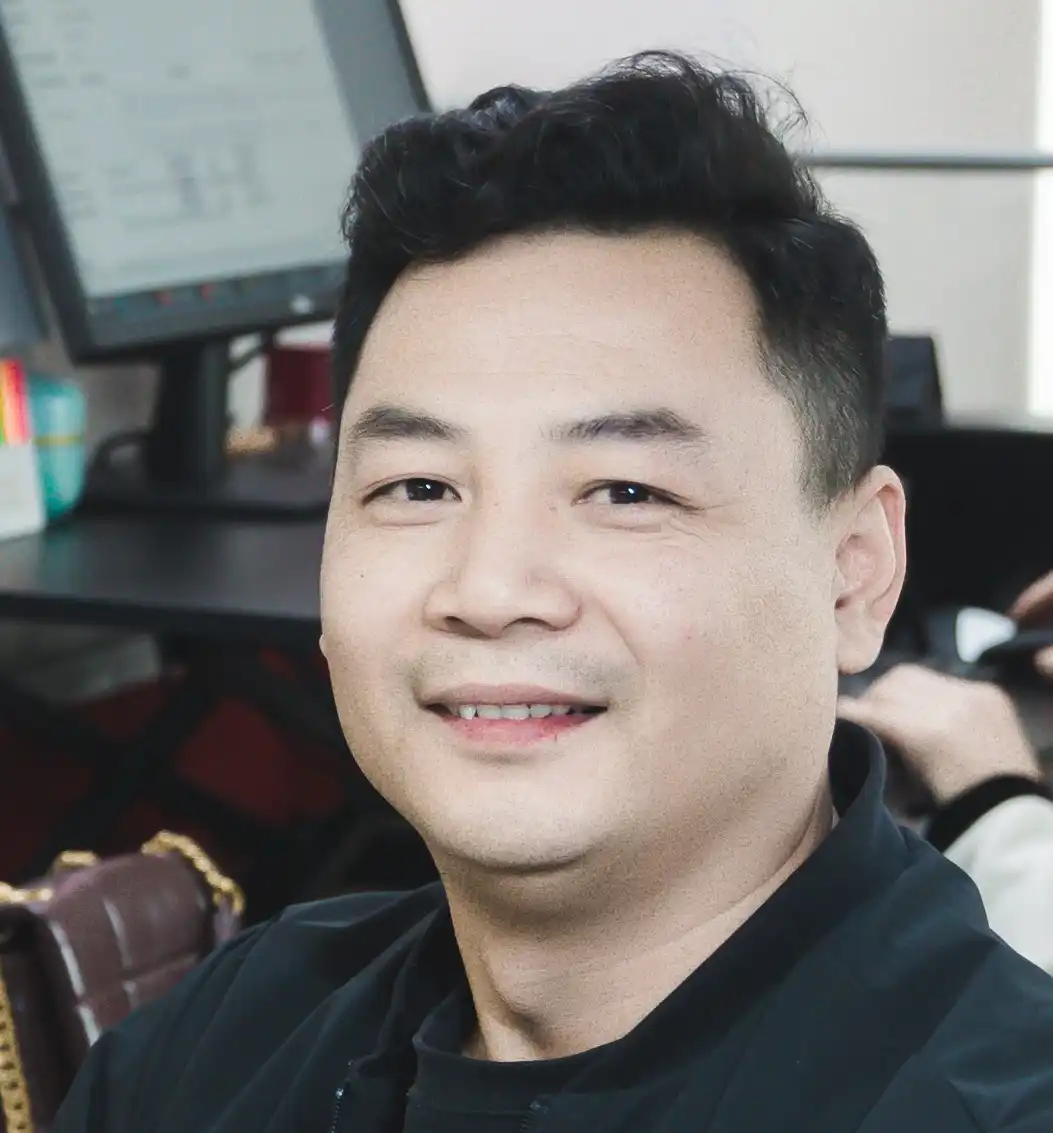
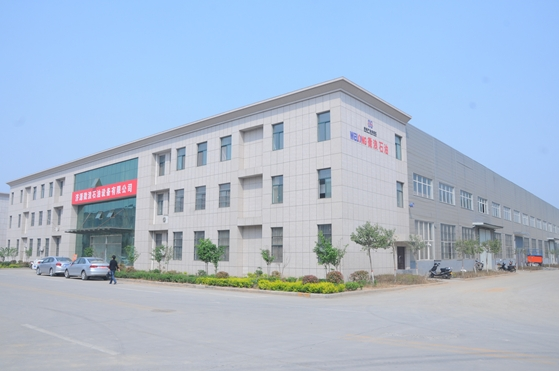
CHINA WELONG - 20+ years manufactuer in oilfield tools