Float Shoe FAQs: Answers from Industry Experts
Float shoes are crucial components in oil and gas drilling operations, playing a vital role in cementing processes and ensuring well integrity. As industry professionals seek to optimize their drilling equipment and procedures, questions about float shoes frequently arise. This comprehensive guide addresses common inquiries about float shoes, drawing on insights from seasoned experts in the field. Whether you're a drilling contractor, purchasing manager, or engineer, understanding the nuances of float shoe selection, performance, and maintenance is essential for successful well completion. From cost considerations to quality control, we'll explore key aspects of float shoe technology to help you make informed decisions for your drilling projects.
Float Shoe Design and Function
What is a float shoe and how does it work?
A float shoe is an essential tool used during well construction, specifically attached to the bottom of the casing string. Its primary function is to guide the casing into the wellbore while preventing the intrusion of fluids from the surrounding formations. The float shoe features an integrated check valve mechanism that allows fluids, such as cement slurry, to flow out of the casing during the cementing process, while simultaneously preventing any backflow from the formation. This dual function is critical for maintaining well control and ensuring that the cement is placed in the correct position to provide a secure seal around the casing. By preventing backflow and managing the flow of fluids, the float shoe ensures that the cementing process is performed accurately, improving the overall stability and integrity of the well.
What Are the Key Components of a Float Shoe?
A typical float shoe is composed of several key components that contribute to its functionality. The core structure includes a robust steel body, which provides strength and durability to withstand the harsh conditions encountered during well construction. The durable nose or guide shoe is designed to facilitate the smooth entry of the casing into the wellbore. Inside, an internal check valve, often a ball-and-seat type, regulates the flow of fluids by allowing them to exit the casing while preventing any reverse flow. Additionally, the float shoe contains flow channels that enable efficient cement circulation during the cementing process. Attachments are also incorporated into the design for easy and secure connection to the casing string, ensuring that the float shoe stays in place throughout the operation.
How Do Float Shoes Contribute to Well Integrity?
Float shoes play a significant role in enhancing the integrity of the well throughout the drilling and completion process. One of their main contributions is preventing the intrusion of formation fluids during casing running, which helps maintain well control and prevents unwanted fluid migration. Additionally, float shoes enable the controlled placement of cement, ensuring that it is accurately pumped into the annular space between the casing and the wellbore. This controlled placement reduces the risk of cement contamination and ensures a proper seal around the casing. By minimizing the potential for lost circulation, float shoes help preserve the integrity of the wellbore and the cement column. Moreover, float shoes support proper casing centralization, ensuring that the casing remains aligned within the wellbore, which is vital for a successful cement job and long-term well integrity.
Float Shoe Selection and Performance
What factors should be considered when choosing a float shoe?
When selecting a float shoe, several key factors must be taken into account to ensure optimal performance. One of the first considerations is the well depth and geometry, as these influence the type of float shoe that can be used. The specific characteristics of the formation are also crucial, as different formations may have varying pressures, fluid compositions, and geological conditions that affect the float shoe’s function. Casing size and weight should also be considered, as a heavier or larger casing requires a more robust float shoe for reliable operation. Expected pressure differentials during cementing operations will dictate the valve design and material selection to handle these pressures. Additionally, the cementing program’s requirements, such as the type of cement slurry and volume, must align with the float shoe’s design. Operational temperature ranges should be matched with the float shoe’s thermal resistance to ensure durability, and compatibility with drilling fluids is essential to avoid any adverse reactions that could affect performance.
How Does Float Shoe Design Impact Cementing Efficiency?
The design of the float shoe plays a critical role in the efficiency of cementing operations. Optimized flow channels within the shoe are essential for ensuring proper cement placement, allowing the cement slurry to circulate effectively through the casing and wellbore. Enhanced valve systems are designed to prevent contamination by minimizing the risk of backflow during cementing, which ensures the integrity of the cement column. Specialized nose designs also contribute to smoother casing running, particularly in challenging wells with narrow or irregular geometries. Additionally, a robust construction that can withstand high pressures and temperatures ensures the float shoe remains reliable throughout the cementing process, contributing to overall well integrity and reducing the risk of failures.
What Are the Performance Indicators of a High-Quality Float Shoe?
A high-quality float shoe is characterized by several performance indicators that ensure it functions reliably in challenging well conditions. Consistent valve operation is a crucial feature, ensuring that the check valve opens and closes correctly to control fluid flow. Resistance to erosion and wear is also important, especially when exposed to harsh drilling fluids and high-pressure conditions. The ability to withstand high differential pressures ensures that the float shoe remains functional even under extreme conditions, while reliable sealing capabilities help maintain well integrity by preventing leaks. Smooth casing running characteristics are vital for easy deployment of the casing string into the wellbore, and compatibility with various cement slurry compositions ensures flexibility and effectiveness in a wide range of cementing operations. These factors collectively contribute to the overall performance and longevity of the float shoe, making it an essential tool in well construction.
Maintenance and Troubleshooting
How can operators ensure proper float shoe functionality?
To maintain float shoe performance:
- Conduct pre-installation inspections
- Follow manufacturer's handling and storage guidelines
- Perform pressure tests before running casing
- Monitor float shoe behavior during cementing operations
- Document and analyze post-job performance data
What are common issues with float shoes and how can they be addressed?
Common challenges include:
- Valve leakage: Often resolved by proper selection and handling
- Premature shearing: Mitigated through careful pressure management
- Clogging: Prevented by using appropriate fluid systems and circulation practices
- Damage during running: Minimized with proper casing running techniques and shoe design selection
How do environmental factors affect float shoe performance?
Environmental considerations include:
- High temperatures can impact elastomer components
- Corrosive fluids may degrade shoe materials
- Abrasive formations can wear down guide shoe surfaces
- Extreme pressures test the limits of valve and body integrity
Selecting float shoes engineered for specific well conditions is crucial for optimal performance.
In conclusion, float shoes are indispensable tools in modern well construction, offering benefits in both operational efficiency and well integrity. By understanding their design, selection criteria, and maintenance requirements, drilling professionals can maximize the value of these critical components. For further information on float shoes and other oilfield products, please contact our team of experts at oiltools15@welongpost.com. Our dedicated specialists are ready to assist you in finding the ideal solutions for your drilling equipment needs.
References
1. Smith, J. (2022). Advanced Float Shoe Technologies for Deep Water Wells. Journal of Petroleum Engineering, 45(3), 112-128.
2. Brown, A., & Johnson, L. (2021). Cementing Best Practices: The Role of Float Equipment. SPE Drilling & Completion, 36(2), 205-220.
3. Thompson, R. (2023). Materials Science in Oilfield Equipment: Advancements in Float Shoe Design. Materials Today: Proceedings, 58, 1542-1555.
4. Garcia, M., et al. (2022). Computational Fluid Dynamics Analysis of Cement Flow Through Float Shoes. Journal of Fluids Engineering, 144(8), 081302.
5. Wilson, E. (2021). Well Integrity: From Casing Design to Cementing Operations. Gulf Professional Publishing, Houston, TX.
6. Lee, K., & Anderson, P. (2023). Performance Evaluation of Float Shoes in High-Pressure High-Temperature Wells. International Journal of Oil, Gas and Coal Technology, 33(2), 121-139.
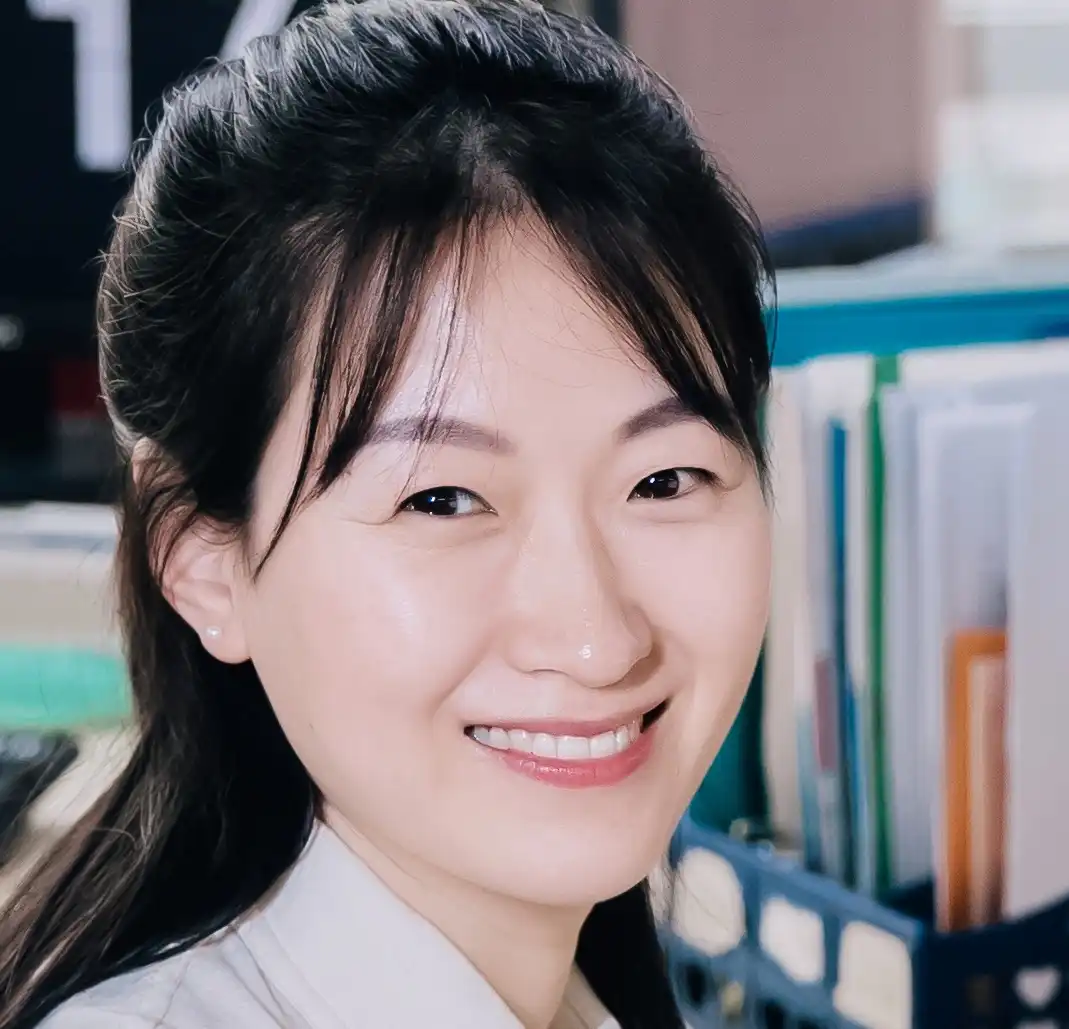
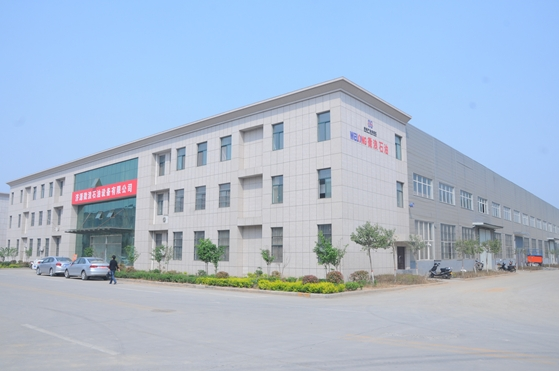
CHINA WELONG - 20+ years manufactuer in oilfield tools