What should be paid attention to during the use of Float Shoe?
The Float Shoe plays a crucial role in cementing operations for the oil and gas industry. It ensures the smooth placement of cement into the wellbore while preventing backflow during the process. To maximize its effectiveness, several factors must be considered during its use. Operators should focus on proper installation, regular inspection, and compatibility with the wellbore conditions. Maintaining the functionality of the float valve within the shoe is also essential to prevent fluid migration and ensure a secure seal. Additionally, attention must be given to high-pressure environments and wear or damage, which can compromise performance. By understanding the critical precautions involved in using a Float Shoe, contractors and engineers can enhance well integrity, reduce operational risks, and extend the life of the equipment. Let’s explore these considerations in detail under the following 6 points to ensure optimal performance and safety.
What Are the Key Considerations When Installing a Float Shoe?
Ensuring Compatibility with the Wellbore
When installing a Float Shoe, one of the key priorities is to ensure it is compatible with the wellbore’s specific conditions. This includes carefully considering the wellbore diameter, the type of casing used, and the alignment of the borehole. Each of these factors plays a crucial role in determining how effectively the Float Shoe will function during the cementing operation. If the Float Shoe is improperly sized or misaligned, it may lead to issues such as difficulty in achieving an adequate cement bond or even complete failure of the equipment. For example, an oversized float shoe may not create a proper seal with the casing, while an undersized one could prevent the flow of cement. To avoid these complications, engineers must ensure that the float shoe matches the exact well design specifications. Additionally, it is essential to tailor the float shoe to the specific requirements of the planned cementing process to ensure that it performs optimally under the expected pressure, temperature, and fluid conditions. A thorough evaluation of these factors will go a long way in preventing unexpected issues during cementing operations.
Preparing the Casing and Cleaning the Wellbore
Another critical aspect of Float Shoe installation is ensuring the wellbore is clean and free of any obstructions that could hinder the performance of the tool. Prior to installation, any remaining mud, debris, or particles within the wellbore should be thoroughly removed. Leftover contaminants can obstruct the float valve, impairing its ability to function as intended and preventing it from achieving a proper seal. To maintain efficient operation, operators should implement a wellbore cleaning procedure that ensures all foreign material is cleared. Moreover, the casing should be inspected for any signs of damage or wear to guarantee its integrity before the float shoe is installed. Any weakness or defect in the casing could lead to issues such as leakage or compromised pressure control. A casing integrity check is an important step to confirm that the casing is sound and capable of supporting the cementing process without complications.
Proper Handling and Installation Techniques
Float Shoes are highly specialized, precision-engineered components, and improper handling during transportation or installation can result in significant damage, which can ultimately affect their performance. It is critical to handle these tools with the utmost care to avoid bending or damaging parts such as the float valve. Operators must ensure that the float shoe is carefully transported, avoiding impacts that could cause harm. During installation, it is vital to secure the float shoe tightly to the casing string, but care should be taken not to over-torque it, as excessive torque can lead to damage to the threads. This can compromise the connection between the float shoe and the casing, potentially leading to leaks or failure during the cementing operation. Specialized tools and trained personnel are essential for a smooth and precise installation. By following best practices in handling and installation, operators can help prevent issues that could delay the cementing process or cause further complications down the line. Taking these steps ensures that the Float Shoe performs as expected and supports a successful and efficient cementing operation.
How Can You Ensure Proper Functioning of a Float Valve in a Float Shoe?
The Role of the Float Valve in Cementing Operations
The float valve, integrated into the float shoe, plays a crucial role in cementing operations by preventing the backflow of fluids. During the cementing phase, it ensures that cement is pushed down the casing and into the annular space without flowing backward into the wellbore. The valve acts as a one-way seal, allowing the cement slurry to flow in one direction only, ensuring proper placement of the cement while maintaining the pressure profile inside the well. If the valve fails to function correctly, the risk of fluid migration into unwanted zones increases, which can negatively affect wellbore integrity and cement bonding. This can lead to issues such as poor zonal isolation, potential contamination, and ultimately, reduced well stability. Therefore, the proper functioning of the float valve is critical in achieving a high-quality cement job and ensuring that the well remains secure throughout its lifecycle.
Regular Testing of the Valve
To maintain the effectiveness of the float valve, regular testing is essential. Before the start of any cementing operation, the valve should be thoroughly inspected for its sealing capability. Operators typically perform pressure tests by introducing fluid into the valve to verify that it maintains a consistent seal under varying pressures. This is essential to detect any leaks or mechanical issues early on. If any issues are detected, they can be addressed promptly, preventing any operational setbacks. In addition to pre-operation tests, periodic checks during the operation are important to ensure the valve continues to perform well throughout the cementing process. This ensures that, should any pressure fluctuations occur, the valve will adequately prevent backflow, helping to maintain the integrity of the entire cementing operation.
Maintenance and Cleaning
Another key aspect of float valve performance is proper maintenance and cleaning. Over time, debris such as cement particles or other contaminants can accumulate inside the valve, potentially preventing it from sealing correctly. To avoid this, operators should ensure the valve is cleaned regularly before and after each use. Special cleaning agents may be required to remove any hardened deposits that could impair the valve’s function. In addition to cleaning, it is essential to inspect the valve for any signs of wear or corrosion, which could affect its longevity and reliability. Regular maintenance and inspections can extend the float valve’s lifespan and ensure that it operates efficiently throughout the cementing job. By proactively addressing potential issues, operators can avoid costly delays and ensure the cementing process remains smooth and effective.
What Are the Risks of Using a Float Shoe in High-Pressure Environments?
Increased Stress on Components
High-pressure environments present significant challenges to the float shoe and its components. During cementing operations, the float shoe and its associated parts, especially the float valve, are exposed to extreme pressure conditions. If the float shoe is not designed to handle such stresses, there is a risk of material deformation or even failure. This can result in a compromised cement job, as the float valve may fail to create the necessary seal. To mitigate these risks, engineers must ensure that the selected float shoes are rated for the specific pressure levels expected in the wellbore. Choosing components that are capable of withstanding high pressure is crucial for the integrity of the cementing process and the overall stability of the well.
Risk of Backflow and Cementing Failures
High-pressure scenarios significantly increase the risk of backflow if the float valve fails to maintain a proper seal. The float valve’s primary function is to prevent fluid from flowing back into the wellbore during cementing, ensuring that the cement is placed accurately in the annular space. A failure in the float valve due to inadequate pressure resistance could lead to cement backflow, resulting in incomplete cement placement. This situation can severely jeopardize the well’s structural integrity, making it prone to issues such as gas migration or water contamination. Addressing this risk involves using high-quality, pressure-rated float shoes that are designed to withstand the specific pressure conditions, thereby minimizing the chances of backflow and ensuring a successful cement job.
Material Selection and Design Considerations
The materials used in the construction of float shoes are essential to their performance under high-pressure conditions. Premium float shoes are often crafted from high-strength materials, such as tungsten carbide or specialized alloy steels, which are known for their durability and resistance to pressure. These materials provide the strength necessary to withstand the stress exerted during cementing operations. Furthermore, the design of the float shoe itself plays an important role in ensuring reliability. Features like reinforced valve assemblies can add an additional layer of protection against failure. Engineers must consider both material selection and design features carefully to ensure the float shoe can perform effectively in challenging, high-pressure environments. By addressing these factors proactively, operators can significantly reduce the risks associated with float shoe performance and improve the overall success of the cementing operation.
How Should the Float Shoe Be Checked Before and After Drilling?
Pre-Drilling Inspection Checklist
Before commencing drilling operations, a comprehensive inspection of the float shoe is critical to ensure that it is in optimal condition. Operators should begin by thoroughly checking the float shoe for any visible signs of physical damage, such as cracks, dents, or corrosion. Even minor defects can compromise the structural integrity of the float shoe and its ability to perform under pressure during cementing. Additionally, the float valve, a key component, should be tested for proper functionality. Ensuring that it can effectively seal and prevent backflow is crucial for a successful cement job. It is also important to check that all threads and connections are free from damage. Damaged threads can cause leaks during cementing, which could lead to significant issues, including compromised well integrity and the need for costly repairs. By performing these checks, operators can ensure that the float shoe is fit for the upcoming drilling operations and reduce the risk of failures during cementing.
Monitoring During Operations
Once drilling operations have begun, continuous monitoring of the float shoe's performance is necessary to detect any potential issues early. Operators should be vigilant for any signs of pressure loss, abnormal fluid movement, or a decrease in cementing efficiency. Any irregularities in pressure or fluid flow could indicate problems with the float shoe or valve, potentially leading to backflow or incomplete cement placement. These issues should be investigated immediately to prevent costly downtime or delays. Early detection allows for prompt corrective actions to be taken, which can prevent more severe problems down the line. Monitoring during operations ensures that the float shoe continues to perform as expected and that the cement job proceeds without complications, safeguarding the integrity of the wellbore and minimizing operational disruptions.
Post-Drilling Maintenance
After drilling operations are complete, it is essential to perform post-drilling maintenance on the float shoe. The equipment should be carefully removed and inspected for signs of wear or damage, particularly on the float valve, which may have experienced significant stress during cementing. Thorough cleaning of the float valve and other components will help identify any potential issues and allow operators to assess whether any parts need replacing. Worn or damaged parts should be replaced promptly to avoid reduced performance in future operations. In some cases, upgrading to a newer model or an improved design may be necessary to ensure that the float shoe meets performance standards. Regular post-drilling maintenance ensures that the float shoe remains in good condition and ready for future use, extending its lifespan and ensuring consistent performance throughout its operational life. By adhering to a strong inspection and maintenance routine, contractors can avoid unexpected failures and enhance the reliability of their equipment.
What Are the Precautions to Take During Cementing with a Float Shoe?
Ensuring Proper Cement Slurry Design
The design of the cement slurry plays a crucial role in achieving a successful cement job when using a float shoe. The slurry must be carefully tailored to match the specific wellbore conditions, such as temperature, pressure, and the type of formation being drilled. It is equally important that the slurry is compatible with the materials used in the float shoe, as certain chemical reactions between the slurry and the shoe components could compromise the integrity of the cementing job. A poorly designed slurry may result in issues such as blockages within the float valve, inconsistent or incomplete cement placement, and reduced zonal isolation. To avoid these issues, careful consideration should be given to the type and ratio of the materials in the slurry, ensuring it can flow smoothly and form a strong, durable seal once set. A well-designed cement slurry enhances the overall success of the cementing process and ensures the long-term stability of the wellbore.
Monitoring Cementing Pressure
Maintaining proper pressure during the cementing process is vital to the success of the operation. If the pressure applied to the float shoe is too high, it can damage the float valve or the shoe body, potentially causing leaks or failure to maintain proper seal integrity. On the other hand, insufficient pressure may result in incomplete cement placement, which compromises well integrity and can lead to problems such as gas migration or poor zonal isolation. Operators should rely on advanced pressure monitoring systems to closely track pressure levels throughout the cementing process. These systems can provide real-time data, allowing operators to adjust the pressure as needed to maintain optimal conditions. Proper monitoring ensures that the float shoe performs as intended and helps prevent costly mistakes during cementing.
Preventing Blockages and Overflows
Blockages in the float valve, casing, or other cementing equipment can disrupt the entire operation, leading to delays, increased costs, and potential wellbore instability. To minimize the risk of blockages, operators should make use of centralizers to maintain proper alignment of the casing and promote uniform cement flow. These tools help ensure that the cement slurry flows smoothly through the float shoe and throughout the casing. Regular cleaning and inspection of equipment is also necessary to prevent buildup of debris or hardened cement, which can obstruct the flow path. Additionally, keeping an eye on the potential for overflows is critical, as any uncontrolled cement flow can result in spills, loss of pressure, or contamination of surrounding formations. By taking a proactive approach with regular equipment checks, preventive measures like centralizers, and vigilant monitoring, operators can mitigate the risk of blockages and overflows, ensuring a smooth and efficient cementing operation.
What Should Be Done If a Float Shoe Shows Signs of Wear or Damage?
Identifying Signs of Wear or Damage
Common signs of wear or damage in a Float Shoe include cracks, erosion, and reduced valve performance. These issues can compromise the integrity of the cementing process and should be addressed immediately. Regular inspections can help detect early signs of wear.
Repair vs. Replacement
When a float shoe shows signs of damage, operators must decide whether to repair or replace the equipment. Minor issues, such as debris buildup or small cracks, can often be resolved through cleaning and maintenance. However, more severe damage may necessitate replacement to ensure safe and efficient operations.
Upgrading to Advanced Models
If wear and damage are recurring issues, it may be time to upgrade to a more durable or advanced float shoe model. Modern float shoes often feature enhanced materials and design improvements that provide greater resistance to wear and damage. Consulting with a trusted supplier can help identify the best options for your operations.
By addressing wear and damage promptly, operators can maintain the performance and reliability of their float shoes.
Conclusion
The use of a Float Shoe is critical to successful cementing operations in the oil and gas industry. By paying close attention to installation, valve functionality, high-pressure risks, inspection routines, cementing precautions, and handling wear or damage, operators can maximize equipment performance and enhance well integrity. At China Welong, we take pride in offering high-quality tools tailored for the oil and gas industry. Our taper mills are designed to meet the specific needs of drilling contractors, ensuring precision, durability, and cost-effectiveness. With over two decades of expertise, ISO 9001-2015 & API 7-1 certification, and a commitment to excellence, we are your trusted partner for oilfield solutions.
For more information or to discuss your specific needs, contact us at oiltools15@welongpost.com.
References
1. Wood, D. R., & Hu, P. (2013). Casing and Cementing Operations in Oil and Gas Wells. Society of Petroleum Engineers.
2. Smith, A. L., & Hwang, Y. S. (2010). Key Considerations for Float Shoe Performance in Well Cementing Operations. SPE/IADC Drilling Conference.
3. Miller, R. D., & Thompson, T. J. (2015). Float Shoe Installation and Troubleshooting: Best Practices and Common Pitfalls. Journal of Petroleum Technology, 67(8), 72-77.
4. Taylor, S. M., & Jensen, K. B. (2012). Float Shoe Integrity: A Comprehensive Approach to Preventive Maintenance and Risk Mitigation. SPE Drilling and Completion, 27(3), 89-95.
5. Thompson, M., & Richards, G. (2017). Optimizing Float Shoe Design for High-Pressure, High-Temperature Wells. SPE/IADC Drilling Conference and Exhibition.
6. Johnson, C. R., & Hall, P. A. (2014). Operational Challenges with Float Shoes: Ensuring Performance and Safety in Cementing Operations. SPE Drilling and Completion, 29(1), 34-40.
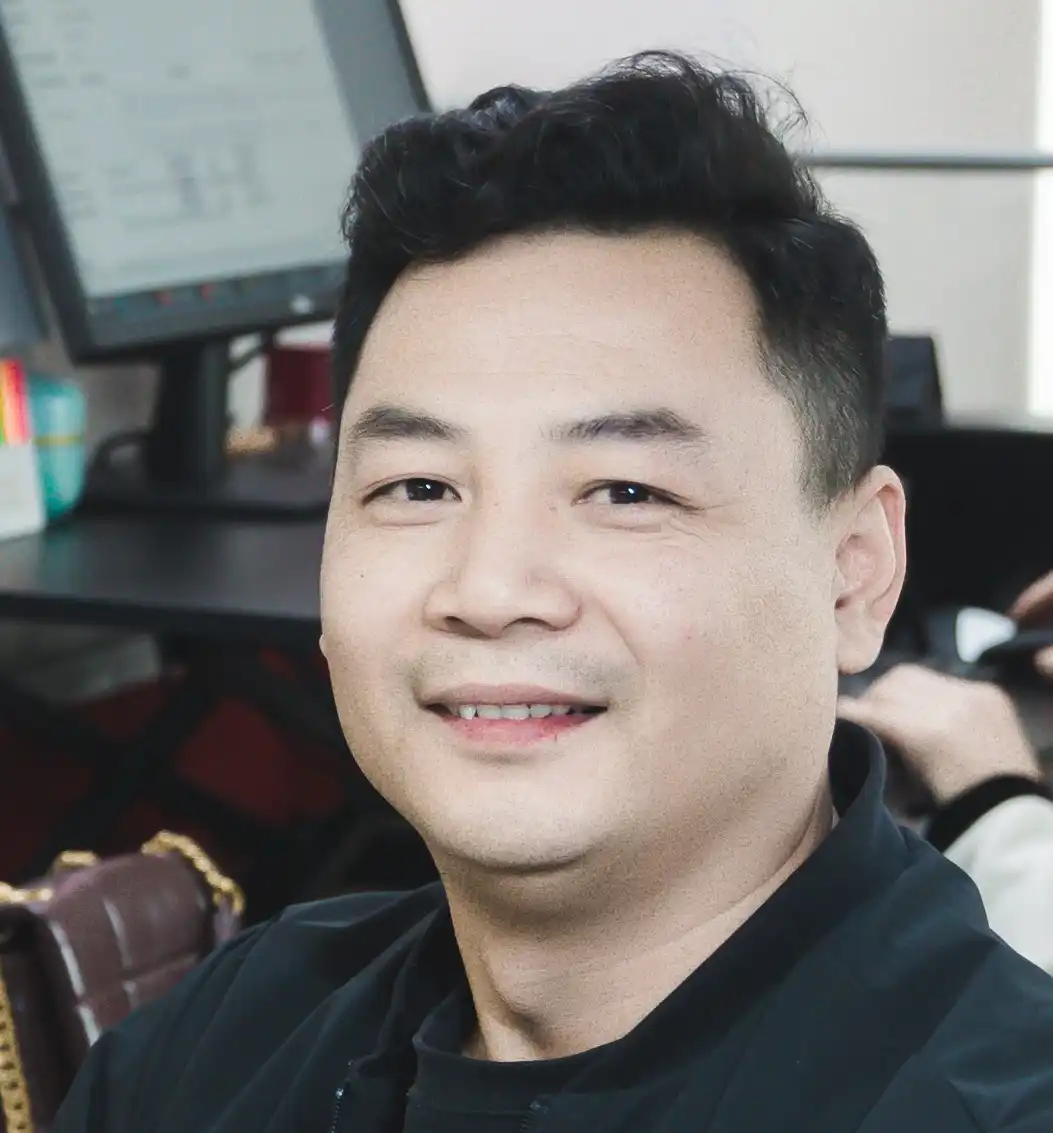
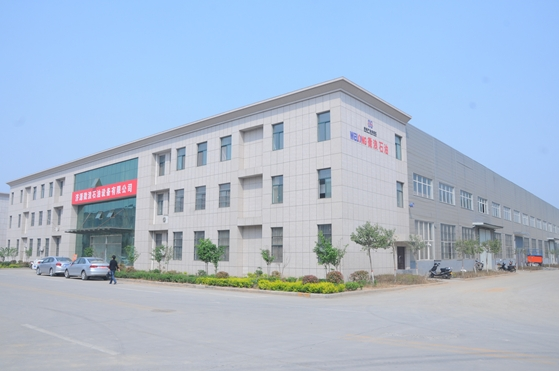
CHINA WELONG - 20+ years manufactuer in oilfield tools