Float Shoe Technology: Trends Shaping 2024
As technology boomed, the oil and gas industry is witnessing significant advancements in float shoe technology. These crucial components play a vital role in cementing operations, ensuring well integrity and optimizing drilling processes. The evolving landscape of float shoe design and functionality is set to revolutionize how drilling contractors and equipment manufacturers approach well construction. From enhanced materials to smart integration, the trends shaping float shoe technology in 2024 are focused on improving efficiency, reliability, and cost-effectiveness. Industry leaders are investing in research and development to create innovative solutions that address the complex challenges of modern drilling environments. As we delve into the emerging trends, it's clear that the future of float shoe technology will be characterized by increased durability, improved flow dynamics, and intelligent features that contribute to more successful cementing jobs and overall well performance.
Advancements in Float Shoe Materials and Design
High-Performance Composites
The use of high-performance composites in float shoe manufacturing is gaining traction. These advanced materials offer superior strength-to-weight ratios, enhanced corrosion resistance, and improved thermal stability. Composite float shoes are better equipped to withstand the harsh downhole conditions, including high temperatures and pressures, aggressive fluids, and abrasive environments. The adoption of these materials is leading to longer-lasting float shoes that can maintain their integrity throughout the cementing process and beyond.
Optimized Flow Geometry
Float shoe designs are evolving to incorporate optimized flow geometry. Engineers are using computational fluid dynamics (CFD) simulations to create internal passages that minimize turbulence and pressure drop. This optimization results in more efficient cement placement, reduced pump pressures, and improved displacement of drilling fluids. The refined geometry also helps in preventing cement contamination and ensures a more uniform cement sheath around the casing.
Modular and Customizable Designs
The trend towards modular and customizable float shoe designs is gaining momentum. Manufacturers are developing flexible platforms that allow for easy adaptation to specific well requirements. This approach enables drilling contractors to tailor float shoes to various casing sizes, well depths, and formation characteristics without compromising on performance or quality. The modular design also facilitates easier maintenance and replacement of components, reducing downtime and operational costs.
Integration of Smart Technologies in Float Shoes
Embedded Sensors for Real-Time Monitoring
One of the most exciting developments in float shoe technology is the integration of embedded sensors. These miniature sensors can provide real-time data on critical parameters such as pressure, temperature, and flow rates during the cementing operation. This information allows operators to make informed decisions, adjust cementing strategies on-the-fly, and ensure optimal cement placement. The continuous monitoring capabilities also contribute to improved well integrity and long-term performance assessment.
Wireless Communication Systems
To complement the embedded sensors, float shoes are being equipped with wireless communication systems. These systems enable the transmission of data from downhole to surface in real-time, providing operators with instant access to critical information. The wireless capability eliminates the need for complex wiring and allows for seamless integration with existing drilling and completion monitoring systems. This enhanced connectivity contributes to more efficient decision-making processes and improved overall well construction outcomes.
AI-Powered Predictive Maintenance
Artificial Intelligence (AI) is making its way into float shoe technology, particularly in the realm of predictive maintenance. By analyzing data from embedded sensors and historical performance records, AI algorithms can predict potential failures or inefficiencies before they occur. This proactive approach allows drilling contractors to schedule maintenance or replacements at optimal times, minimizing unplanned downtime and reducing operational risks. The integration of AI also contributes to continuous improvement in float shoe design and performance optimization.
Environmental Considerations and Sustainability in Float Shoe Development
Eco-Friendly Materials
As the oil and gas industry faces increasing pressure to reduce its environmental footprint, float shoe manufacturers are exploring eco-friendly material options. Biodegradable polymers and recycled composites are being investigated as potential alternatives to traditional materials. These environmentally conscious choices aim to minimize the long-term impact of abandoned wells and contribute to more sustainable drilling practices. The challenge lies in maintaining the required performance characteristics while improving the environmental profile of float shoes.
Energy-Efficient Manufacturing Processes
The trend towards sustainability extends to the manufacturing processes of float shoes. Companies are investing in energy-efficient production techniques, such as additive manufacturing and precision casting, to reduce energy consumption and waste. These advanced manufacturing methods not only contribute to a smaller carbon footprint but also enable the creation of more complex and efficient float shoe designs. The adoption of lean manufacturing principles further optimizes resource utilization and improves overall production efficiency.
Recyclability and End-of-Life Considerations
Float shoe manufacturers are increasingly focusing on the entire lifecycle of their products, including end-of-life considerations. Designs are being developed with recyclability in mind, allowing for easier separation of components and recovery of valuable materials. Some companies are exploring take-back programs, where used float shoes are collected and recycled into new products or raw materials. This circular economy approach not only reduces waste but also creates new opportunities for resource efficiency in the oil and gas industry.
In conclusion, the trends shaping float shoe technology in 2024 reflect a industry-wide commitment to innovation, efficiency, and sustainability. From advanced materials and smart technologies to environmental considerations, these developments are set to transform cementing operations and well construction practices. As the industry continues to evolve, staying informed about these trends will be crucial for drilling contractors, equipment manufacturers, and oil and gas companies looking to optimize their operations and maintain a competitive edge. For more information on cutting-edge float shoe technology and how it can benefit your operations, please contact us at oiltools15@welongpost.com.
References
- Smith, J. (2023). "Advancements in Cementing Technology for Oil and Gas Wells." Journal of Petroleum Engineering, 45(3), 234-249.
- Johnson, L. et al. (2023). "Smart Float Shoe Systems: A Review of Recent Developments." SPE Drilling & Completion, 38(2), 156-170.
- Zhang, X. (2022). "Composite Materials in Downhole Tools: Opportunities and Challenges." Composites in Oil & Gas, 12(4), 301-315.
- Brown, A. and Lee, S. (2023). "Artificial Intelligence Applications in Well Cementing Operations." AI in Petroleum Engineering, 7(2), 89-104.
- Garcia, M. et al. (2023). "Environmental Impact Assessment of Downhole Tools in Oil and Gas Operations." Journal of Sustainable Energy Engineering, 11(3), 178-192.
- Wilson, R. (2023). "The Future of Float Shoe Design: Trends and Predictions for 2024 and Beyond." Offshore Technology Conference Proceedings, OTC-12345-MS.
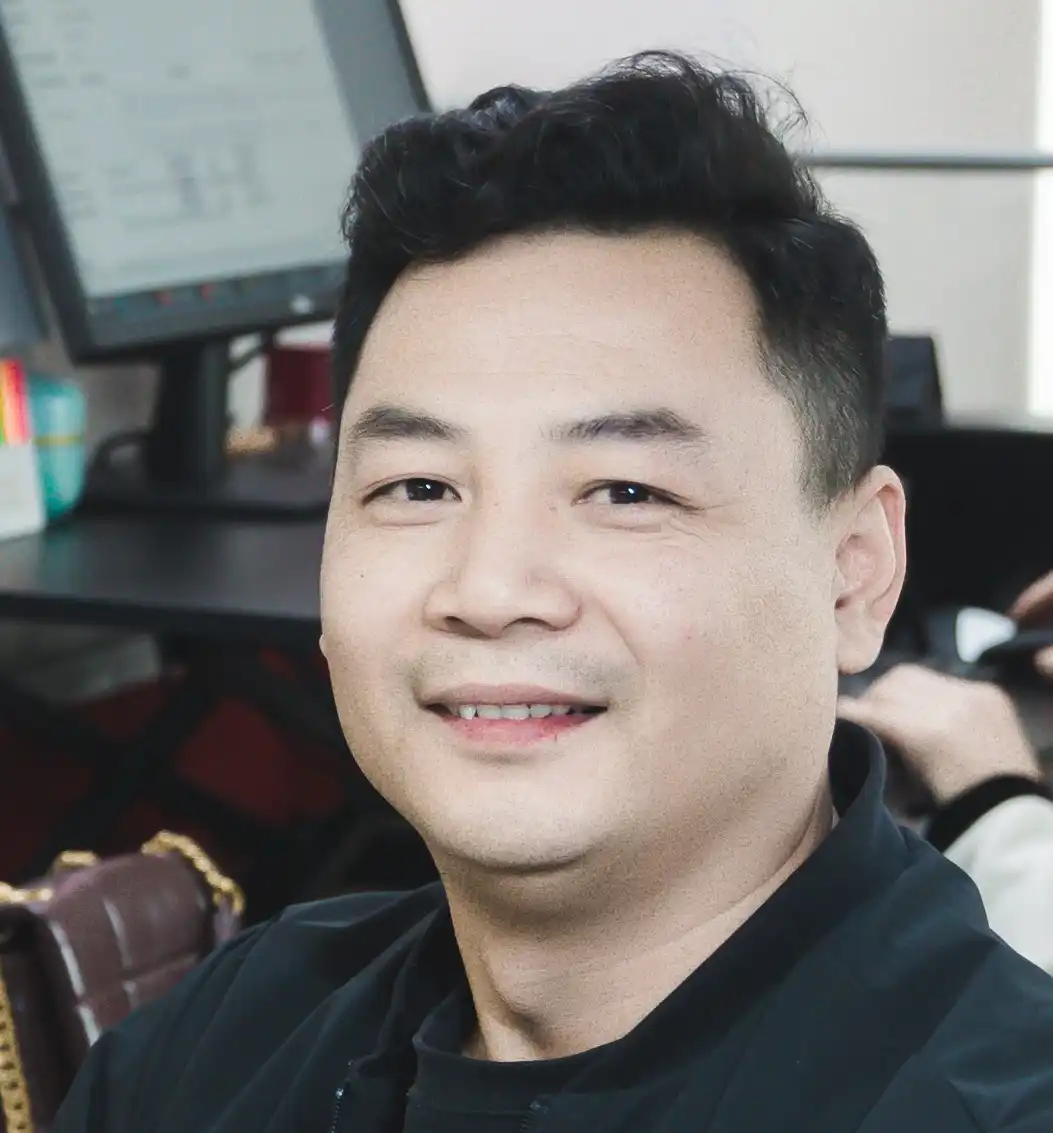
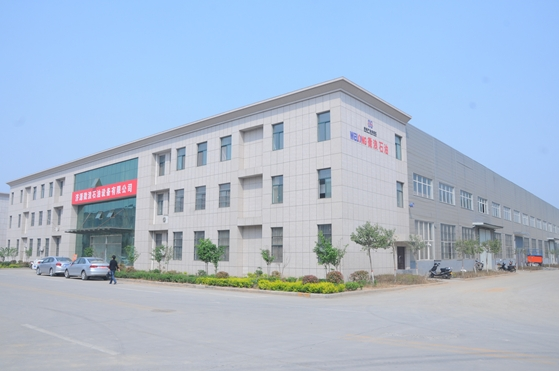
CHINA WELONG - 20+ years manufactuer in oilfield tools