What will float shoe do when float collar does not work?
When a float collar malfunctions during drilling operations, it can lead to serious complications, delaying the project and driving up costs. The float collar is designed to prevent cement from backflowing into the casing, ensuring the integrity of the well. However, if it fails to function as expected, it can cause issues like poor cement bonding, non-optimal well control, and operational delays. When facing float collar malfunction, the immediate actions you take can significantly influence the success of the operation.
In some cases, a malfunctioning float collar might be caused by improper installation or damage to the components during previous operations. Before taking any corrective action, ensure that the float collar was installed according to the manufacturer’s guidelines. A float shoe helps control cement placement and prevents backflow, serving as an effective alternative when a float collar does not work as intended.
What Are the Common Reasons a Float Collar May Fail?
A float collar is an essential component in cementing operations, as it provides a one-way valve to prevent cement backflow and allows for proper placement of cement in the casing. However, when a float collar fails, it can lead to a variety of issues, ranging from ineffective cementing to operational delays and increased costs. Understanding the common reasons behind float collar failures is crucial to preventing them and ensuring the integrity of the well.
Improper Installation
Float collar failure often results from improper installation. If not correctly aligned or securely attached, the float collar can malfunction. Installation that is too tight or too loose can damage components like the check valve, affecting its functionality. Always follow manufacturer guidelines and verify all connections during installation.
Wear and Tear from Harsh Conditions
The float collar endures extreme drilling conditions, including high pressure, temperature changes, and abrasive materials. Over time, these factors cause wear on components like rubber seals and valves. Damaged seals can fail to maintain a proper pressure seal, leading to cement backflow. Additionally, exposure to aggressive drilling fluids can degrade the collar's material, increasing the risk of failure.
Check Valve Damage
The check valve prevents cement from flowing back into the casing, but it can fail if blocked, damaged, or corroded. Obstructions such as debris or cement buildup can cause the valve to malfunction, resulting in improper cement placement and poor bonding between the casing and wellbore. Regular check valve inspection is essential for maintaining proper function.
Corrosion
Corrosion is a significant factor in float collar failure, especially in corrosive drilling environments. It weakens metal components, including the check valve, leading to leaks or seal failure. Corrosion can compromise wellbore isolation and cementing operations. To prevent this, regular inspections and the use of corrosion inhibitors in drilling fluids are recommended.
Improper Cementing Practices
Float collar failure can sometimes result from improper cementing practices. If the cement is mixed or pumped incorrectly, it can lead to issues with the float collar’s performance. For instance, if the slurry is too thick or too thin, it can affect the pressure inside the casing and interfere with the float collar’s sealing ability. Furthermore, if the cement is not adequately pumped or there is insufficient displacement, it can cause the collar to malfunction. Proper cementing techniques, including slurry design and pressure control, are critical to ensuring the float collar works effectively.
Excessive Pressure or Temperature
Excessive pressure or temperature can have detrimental effects on the float collar’s components. The seals and valves inside the float collar are designed to operate within specific pressure and temperature ranges. If these limits are exceeded, the materials may deform, resulting in failure. High-pressure conditions can cause leaks, while high temperatures can degrade the rubber seals, leading to malfunction. Ensuring the well is within the recommended pressure and temperature range is crucial for preventing float collar failure.
How to Troubleshoot Float Collar Problems During Drilling?
When a float collar fails during drilling operations, it is crucial to address the issue promptly to minimize delays and costs. Troubleshooting float collar problems can be challenging, as various factors can contribute to malfunction. However, by following a systematic approach, you can identify the root cause and implement the necessary corrective measures to get the operation back on track. Here are some essential troubleshooting steps for dealing with float collar problems during drilling.
Check for Pressure Loss
A sudden pressure loss during cementing operations can indicate a malfunctioning float collar. Float collars are designed to maintain pressure within the casing, and any failure to do so suggests an issue, such as a damaged valve or faulty sealing. Monitor pressure levels during cement pumping, and inspect the collar for visible damage. If necessary, replace or repair any affected components.
Inspect the Check Valve
The check valve is essential for preventing cement from flowing back into the casing. If it malfunctions, improper cement placement can occur, compromising well integrity. Inspect the valve for blockages, corrosion, or wear. If the valve is stuck or damaged, remove any obstructions or replace the valve entirely to ensure smooth operation before continuing the cementing process.
Look for Signs of Seal Failure
Seals in the float collar maintain a pressure-tight connection between the casing and wellbore. Over time, seals can wear out, causing pressure loss or cement backflow. Inspect seals for visible cracks or wear. If damaged, replace the seals and ensure they are compatible with the cement and drilling fluids being used, as certain materials may degrade or react with specific substances.
Assess the Installation Conditions
Improper installation can cause float collar failure. Ensure the collar is positioned at the correct depth and properly aligned with the casing. Misalignment or incorrect placement can lead to operational issues, so follow manufacturer guidelines for installation. If misinstalled, reinstall or adjust the collar to ensure proper functionality.
Evaluate the Cementing Slurry
Float collars depend on proper cementing for effective performance. If the slurry is too thick, too thin, or not mixed correctly, it can cause pressure imbalances that affect the collar. Check the slurry consistency and ensure it meets required specifications. Too thick may cause pressure buildup, while too thin might fail to activate the collar’s check valve. Work with the cementing team to confirm correct slurry design and pumping pressures.
Monitor Drilling Parameters
Various parameters like pressure, temperature, and flow rates impact float collar performance. Continuously monitor these to ensure they stay within the recommended ranges. Excessive pressure or temperature can lead to malfunction, so adjust parameters to protect the collar. Pay attention to the flow rate during cementing to ensure proper cement placement and avoid issues.
Use of a Float Shoe as Backup
If troubleshooting efforts do not resolve the float collar issue, consider using a float shoe as a backup solution. A float shoe, when installed at the bottom of the casing string, helps to prevent cement backflow and provides pressure control during cementing operations. While the float collar typically handles backflow prevention, a float shoe can offer an additional layer of protection in case the collar malfunctions. Using both the float collar and float shoe together can help maintain wellbore integrity and mitigate the risks associated with float collar failure.
How Does a Float Shoe Help When the Float Collar Malfunctions?
In cementing operations, both the float collar and the float shoe play crucial roles in ensuring proper wellbore pressure control, preventing cement backflow, and securing the casing in place. However, when a float collar malfunctions, the float shoe can act as a backup to maintain the integrity of the well and prevent operational delays. Let’s explore how a float shoe can be helpful when the float collar fails during cementing.
Provides Backflow Prevention
The primary function of both a float collar and a float shoe is to prevent cement from flowing back up the casing after it has been pumped. The float collar typically serves as the first line of defense, sealing off the casing and holding pressure during cement placement. However, if the float collar malfunctions or fails to properly seal, the float shoe can step in to provide backflow prevention. A float shoe, installed at the bottom of the casing string, features a built-in check valve that allows the cement to flow down into the well while preventing any fluid or cement from returning up the casing. This function is crucial for ensuring the cement job remains effective, even in the event of a float collar failure.
Helps Maintain Pressure Integrity
During cementing operations, maintaining pressure integrity is vital to prevent contamination, wellbore instability, and other issues. A float collar failure can lead to pressure loss, which might compromise the entire operation. A float shoe, with its pressure-retaining capabilities, can help maintain wellbore pressure even when the float collar is not functioning properly. The shoe's check valve seals the casing, preserving pressure during the cementing process and ensuring that no fluid or gas migrates into the well. By helping to maintain pressure integrity, the float shoe provides a backup safety measure in case of float collar failure.
Provides an Additional Seal
When a float collar fails, the float shoe’s additional sealing capability provides another layer of protection. The float shoe’s check valve prevents any cement from backflowing into the casing, ensuring that the cement job remains effective and the wellbore remains sealed. This is especially important in deep wells, where pressure management and cement placement are critical. The float shoe acts as an additional fail-safe to prevent any potential issues that may arise due to float collar failure, providing a reliable backup for maintaining wellbore integrity and pressure control.
Cost-Effective Solution
Replacing or repairing a damaged float collar can be expensive, particularly when the malfunction leads to a need for re-entry or additional drilling operations. The float shoe serves as a cost-effective solution to mitigate the impact of float collar failure. By providing a temporary or permanent backup, the float shoe can help avoid the need for costly repairs or re-drilling. This is especially beneficial for drilling contractors who need to control costs while maintaining the integrity of the wellbore and ensuring that cementing operations are completed successfully.
What Steps Can Be Taken if the Float Collar Is Not Sealing Properly?
The proper sealing of a float collar is critical to the success of the cementing operation, as it prevents backflow and ensures the integrity of the casing. However, issues may arise when the float collar does not seal as expected. If the float collar fails to seal properly, it can lead to various operational problems, such as fluid migration, cement contamination, and compromised wellbore pressure. Fortunately, there are several steps that can be taken to address and resolve this issue promptly.
Identify the Cause of the Sealing Failure
The first step in addressing a float collar sealing problem is to identify the root cause of the failure. This could be due to various factors, such as improper installation, damage during the casing run, or manufacturing defects. To pinpoint the issue, it's essential to conduct a thorough inspection of the float collar and the surrounding components. Some common causes of sealing failure include:
1. Debris or contaminants
2. Improper installation
3. Damage during casing run
4. Manufacturing defect
Check the Float Collar’s Orientation
An incorrectly oriented float collar can cause sealing issues. Ensure the float collar is positioned correctly within the casing string, with the check valve properly aligned. If the collar is misoriented, it may fail to form a proper seal, leading to backflow or contamination of cement. Reposition the collar as needed to ensure correct orientation for effective sealing.
Perform a Pressure Test
A pressure test is a reliable method to check if the float collar is sealing properly. By pumping fluid into the casing and monitoring the pressure, you can identify any leaks. If the pressure drops or fluid escapes through the collar, it suggests a compromised seal. In such cases, take corrective action, either repairing or replacing the faulty float collar.
Use a Float Shoe for Backup
If the float collar fails to seal effectively, a float shoe can serve as a backup. Located at the bottom of the casing string, the float shoe helps prevent backflow and maintains pressure integrity. Its check valve can act as a temporary solution, ensuring the cementing process continues smoothly until the float collar is repaired or replaced.
Replace the Float Collar
If the float collar is beyond repair or continues to malfunction, replacing it is the best solution. A faulty collar can compromise the cementing operation, so replacing it ensures proper sealing and wellbore integrity. This may require pulling the casing and re-entering with a new collar, which can be time-consuming and costly but is necessary to maintain the well's structural integrity.
Utilize Pressure-Activated Seals
Some float collars are equipped with pressure-activated seals that require a specific pressure to activate. If the float collar is not sealing due to insufficient pressure, it may be necessary to adjust the pressure in the wellbore to activate the seal. This can be done by adjusting the fluid volume or pressure in the casing. If this approach is not successful, the seal may be damaged or defective, and replacement may be required.
Inspect the Casing and Cementing Equipment
It's also essential to inspect other components of the casing and cementing equipment for issues that could be contributing to the float collar’s sealing failure. This includes checking the casing for deformation or damage, inspecting the cementing equipment for malfunctions, and ensuring that the cement mixture is properly prepared. Any issues with the surrounding equipment can affect the performance of the float collar, so addressing these problems is critical for ensuring a proper seal.
Perform a Leak Detection Test
A leak detection test can help identify the exact location of a sealing failure in the float collar. This test involves introducing a specific gas or dye into the casing to detect leaks. By monitoring the wellbore for any signs of gas or dye escape, the source of the sealing failure can be pinpointed, allowing for targeted repairs. Leak detection tests are especially useful in deep or complex wells where conventional pressure tests may be challenging.
Can a Damaged Float Collar Affect the Performance of a Float Shoe?
The performance of both the float collar and the float shoe is interconnected, as they work in tandem to ensure the success of the cementing operation. While the float collar is designed to seal the casing and prevent backflow, the float shoe serves as a one-way valve at the bottom of the casing string, ensuring that the cement slurry is properly displaced and that no cement leaks out during the operation. Therefore, if a float collar is damaged, it can have a significant impact on the performance of the float shoe, compromising the overall cementing process.
Here’s how a damaged float collar can affect the float shoe:
Compromised Backflow Prevention
A faulty float collar can cause backflow during cementing, allowing fluid to enter the casing and contaminate the cement slurry. This reduces pressure in the wellbore, hindering the float shoe from properly displacing the cement.
Cement Contamination and Poor Displacement
When the float collar fails, contaminated fluid may flow into the casing, leading to improper cement displacement. The float shoe may struggle to guide the cement slurry effectively, resulting in poor cementing, which can compromise well integrity and lead to weak zones in the wellbore.
Inability to Maintain Pressure
A damaged float collar can cause pressure loss in the wellbore, affecting the float shoe's ability to maintain the necessary pressure for proper cement displacement. This can result in premature cement setting, incomplete placement, and failure to isolate zones effectively.
Risk of Fluid Infiltration
A malfunctioning float collar can allow undesirable fluids, like drilling mud, to enter the cement slurry from the annular space. This contamination alters the cement's properties, making it ineffective in sealing the wellbore. Once fluid contamination occurs, the float shoe can't prevent further issues.
Increased Risk of Casing and Formation Damage
Float collar failure can cause pressure imbalance or fluid migration, leading to casing and formation damage. These complications may require corrective actions and can result in expensive downtime, loss of well integrity, and increased operational costs.
Delayed Cement Setting
Failure of the float collar can cause delays in cement setting, either by premature or slow setting of the cement. This affects wellbore isolation and cement bonding, leading to inefficiencies and potential additional costs in the drilling operation.
Mitigating the Impact of Float Collar Damage on the Float Shoe
To prevent issues with the float collar and float shoe, ensure both are properly installed and inspected, checking for damage, debris, or defects. Correct alignment and proper torque are essential. If the float collar is suspected to be faulty, installing a backup float shoe can maintain pressure and prevent immediate issues with cement displacement. Regular preventive maintenance checks can detect early signs of wear or malfunction, allowing for timely repairs before affecting the cementing process. If the float collar is damaged or malfunctioning, it should be replaced immediately to avoid further damage and ensure the effectiveness of the cementing operation.
How to Prevent Float Collar and Float Shoe Failures in Future Drilling Operations?
Preventing failures in both the float collar and float shoe is crucial to ensuring the success and integrity of drilling operations. These components are essential for proper cementing, and any failure can lead to wellbore contamination, improper cement placement, and costly downtime. Fortunately, there are several strategies that can be implemented to reduce the likelihood of these failures and improve the reliability of these tools in future operations.
Here are key preventative measures:
Choose Quality Components
Select high-quality float collars and float shoes from trusted suppliers to ensure durability and performance. These components should meet industry standards for pressure, temperature, and mechanical integrity, reducing the risk of failure during operations.
Regular Inspections and Maintenance
Implement a proactive maintenance plan with routine visual checks for wear, cracks, and corrosion. Conduct functional tests, such as pressure and sealing tests, to confirm proper performance. Replace any damaged or worn components promptly to avoid failure during cementing operations.
Proper Handling and Storage
Store float collars and float shoes in a clean, dry environment, protecting them from contaminants and physical damage. Ensure they are securely stored or packed to prevent corrosion and deterioration, and handle them carefully during transportation to maintain their integrity.
Proper Installation
Follow the manufacturer’s instructions to ensure correct installation of float collars and float shoes. This includes proper positioning, applying the right torque, and ensuring alignment to avoid operational issues such as misalignment, poor sealing, or blockages.
Select the Right Components
Choose float collars and float shoes suited to the specific well conditions, such as depth, pressure, and temperature. Consult with engineers or suppliers to select components made from durable materials with appropriate pressure ratings to match the environment.
Team Training
Ensure that the team involved in cementing operations is properly trained. Regular training on inspection, maintenance, and installation practices helps prevent failures by enabling early identification of issues and promoting adherence to preventative measures.
Conclusion
Maintaining the integrity of your float collar and float shoe is crucial for the success of your cementing operations. By following best practices for inspection, maintenance, proper handling, and installation, you can significantly reduce the risk of failure. Additionally, choosing high-quality components, selecting the right tools for the job, and training your team will ensure optimal performance throughout the drilling process.
At Welong, we offer a wide range of high-quality taper mills designed to meet the specific requirements of your drilling environment. Our taper mills are built with durable materials to withstand extreme conditions, offering both performance and longevity. Our expert team at Welong is always available to provide guidance on selecting the best taper mill for your needs, ensuring that you get the most out of your drilling operations.
If you have any questions or need further assistance with selecting or maintaining float collars and float shoes, feel free to contact us at oiltools15@welongpost.com.
References
1. Jones, J., & Smith, L. (2019). "Troubleshooting and Repairing Float Collars in Cementing Operations." Journal of Petroleum Technology, 71(4), 58-62.
2. Patel, A., & Williams, S. (2020). "Effective Solutions for Float Collar Failures in Deepwater Wells." Society of Petroleum Engineers, SPE 2009379, 1-8.
3. Johnson, R., & Carter, M. (2018). "Prevention and Mitigation of Float Collar Malfunctions." Oil & Gas Engineering, 42(10), 34-39.
4. Davis, M., & Thompson, G. (2021). "The Impact of Float Collar Performance on Cementing Quality." Journal of Energy Resources Technology, 143(5), 450-457.
5. Lee, K., & Anderson, T. (2017). "Float Collar Failures and Their Effect on Cement Bond Integrity." International Journal of Well Engineering, 35(7), 22-28.
6. Harris, J., & White, D. (2022). "Remediation Techniques for Float Collar Issues During Cementing." Petroleum Engineering Review, 33(3), 50-55.
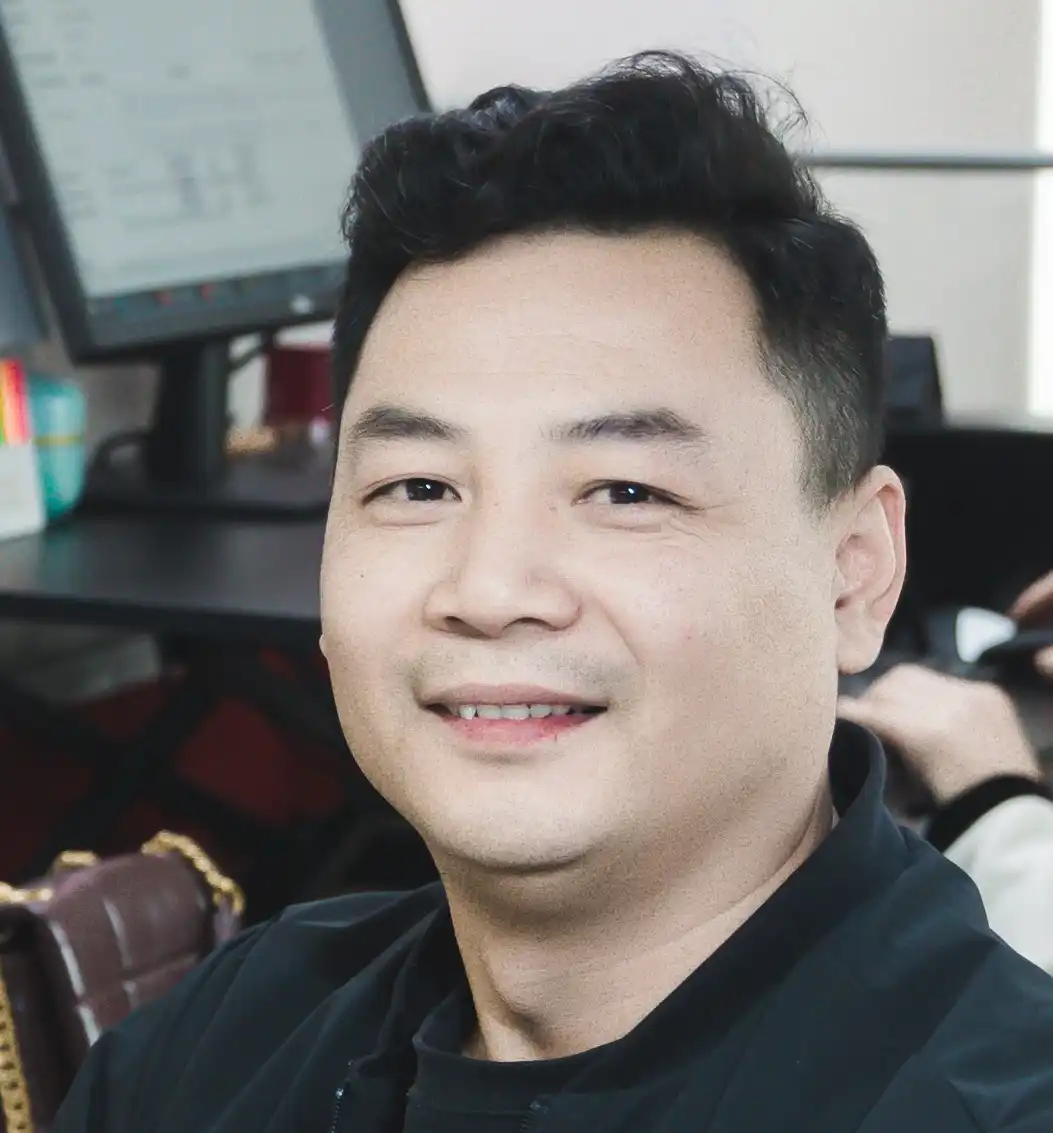
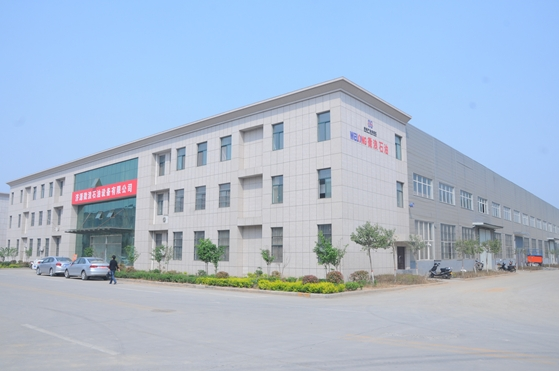
CHINA WELONG - 20+ years manufactuer in oilfield tools