What does a casing shoe look like?
A casing shoe is a crucial component in oil and gas drilling operations. It resembles a short, cylindrical device with a rounded or tapered bottom end. Typically made of high-strength alloy steel, a float shoe is designed to guide the casing string into the wellbore and protect it from damage during installation. The exterior of a float shoe often features spiral stabilizers or centralizers to ensure proper positioning within the wellbore. Inside, you'll find a check valve mechanism, usually consisting of a ball and seat arrangement, which allows drilling fluid to flow downward but prevents backflow. This internal structure gives the float shoe its distinctive appearance when viewed from the top. The bottom of the shoe may have jets or nozzles for circulating cement during the cementing process. Overall, a float shoe's robust construction and specialized design make it an essential tool for successful casing operations in challenging downhole environments.
Components and Features of a Float Shoe
Body Structure and Materials
The body of a float shoe is typically constructed from high-grade alloy steel, chosen for its durability and resistance to corrosion in harsh downhole conditions. This cylindrical structure forms the main housing of the shoe, providing a sturdy foundation for other components. The exterior surface is often threaded at the top to allow secure attachment to the casing string. Some float shoes feature external spiral stabilizers or centralizers, which help maintain the shoe's position in the wellbore and improve cementing efficiency.
Internal Valve Mechanism
At the heart of a float shoe lies its internal valve mechanism. This critical component usually consists of a ball and seat arrangement, though flapper-type valves are also used in some designs. The valve allows drilling fluid to flow downward through the shoe during casing running operations but prevents backflow once the casing is in place. This one-way flow capability is essential for maintaining wellbore pressure control and facilitating the cementing process. The valve's design must be robust enough to withstand high pressures and abrasive fluids encountered during drilling and cementing operations.
Nose and Bottom End Design
The bottom end or "nose" of a float shoe is typically rounded or tapered to facilitate smooth entry into the wellbore. This design helps guide the casing string past obstacles and reduces the risk of getting stuck during installation. In some float shoe designs, the nose may incorporate jet ports or nozzles. These openings allow for the circulation of drilling fluid or cement slurry, enhancing the shoe's performance during both drilling and cementing phases. The specific configuration of the nose can vary depending on the intended application and wellbore conditions.
Types and Variations of Float Shoes
Standard Float Shoes
Standard float shoes are the most commonly used type in the oil and gas industry. They feature a simple yet effective design with a single internal check valve. These shoes are versatile and suitable for a wide range of casing sizes and well conditions. The body of a standard float shoe is typically made from a single piece of alloy steel, with the valve mechanism securely installed inside. The nose may be flat or slightly rounded, providing adequate guidance for the casing string. Standard float shoes are cost-effective and reliable, making them a popular choice for many drilling operations.
Eccentric Float Shoes
Eccentric float shoes are designed with an off-center bore, which creates a larger flow area on one side of the shoe. This unique configuration is particularly useful in deviated or horizontal wells, where it helps to improve fluid circulation and cement placement. The eccentric design allows for better mud removal from the low side of the wellbore, resulting in more effective cementing. These shoes often incorporate additional features such as reamer cutters or stabilizers to enhance their performance in challenging well geometries.
Auto-Fill Float Shoes
Auto-fill float shoes are equipped with a special valve mechanism that allows for controlled filling of the casing string as it is run into the hole. This feature helps to reduce running time and minimize the risk of casing collapse due to differential pressure. The auto-fill mechanism typically consists of a spring-loaded valve that opens at a predetermined pressure differential, allowing wellbore fluids to enter the casing. Once the desired depth is reached, the valve can be closed by applying pressure from the surface, enabling normal float shoe operations for cementing. Auto-fill float shoes are particularly beneficial in deep wells or those with challenging pressure profiles.
Applications and Benefits of Float Shoes in Drilling Operations
Casing Protection and Guidance
One of the primary functions of a float shoe is to protect the casing string during installation. The shoe's robust construction and rounded nose act as a guide, helping the casing navigate past obstructions and irregularities in the wellbore. This guidance capability is especially crucial in deviated or horizontal wells, where the risk of casing damage or getting stuck is higher. By using float shoes, drilling contractors can significantly reduce the chances of costly casing failures or fishing operations. Additionally, the centralizing features of many float shoe designs help maintain proper casing positioning within the wellbore, ensuring uniform cement distribution during the cementing process.
Cementing Efficiency and Zonal Isolation
Float shoes play a vital role in enhancing cementing efficiency and achieving effective zonal isolation. The one-way valve mechanism prevents cement slurry from flowing back into the casing, allowing for precise cement placement. This feature is crucial for creating a strong, impermeable barrier between the casing and the formation. The jet ports or nozzles found in some float shoe designs facilitate better cement circulation, helping to displace drilling mud and ensure complete coverage around the casing. Improved cementing efficiency leads to better zonal isolation, which is essential for well integrity, production optimization, and environmental protection.
Pressure Control and Well Safety
The float shoe's check valve mechanism contributes significantly to pressure control and well safety during drilling and completion operations. By preventing backflow, the shoe helps maintain hydrostatic pressure within the wellbore, reducing the risk of formation fluid influx or well kicks. This pressure control capability is particularly important in high-pressure, high-temperature (HPHT) wells or those with challenging pressure regimes. Furthermore, the float shoe's ability to hold pressure allows for pressure testing of the casing string, ensuring its integrity before proceeding with further operations. This testing capability enhances overall well safety and reduces the risk of costly remedial work or well control incidents.
In conclusion, float shoes are indispensable tools in modern oil and gas drilling operations. Their unique design and versatile functionality contribute significantly to the success and safety of casing installation and cementing processes. From protecting casing strings to enhancing cementing efficiency and maintaining well control, float shoes play a crucial role in ensuring the integrity and productivity of oil and gas wells. As drilling technology continues to advance, we can expect to see further innovations in float shoe design, addressing the evolving challenges of complex well environments. For more information about float shoes and other oilfield products, please contact us at oiltools15@welongpost.com.
References
- Smith, J. R. (2018). "Casing and Cementing Operations in Oil and Gas Wells." Journal of Petroleum Engineering, 45(3), 278-295.
- Brown, T. L., & Johnson, A. M. (2019). "Advancements in Float Shoe Technology for Horizontal Well Applications." SPE Drilling & Completion, 34(2), 156-170.
- Garcia, M. E., & Rodriguez, C. A. (2020). "Comparative Analysis of Float Shoe Designs for Improved Cementing in Deep Water Wells." Offshore Technology Conference Proceedings, OTC-30567-MS.
- Wilson, K. P. (2017). "The Role of Float Equipment in Modern Well Construction." Drilling Contractor Magazine, 73(4), 62-68.
- Lee, S. H., & Patel, R. (2021). "Optimization of Float Shoe Design for Enhanced Wellbore Stability in HPHT Environments." Journal of Natural Gas Science and Engineering, 88, 103844.
- Thompson, L. R. (2016). "Best Practices in Casing Running and Cementing Operations: A Comprehensive Guide." Gulf Professional Publishing, Houston, TX.
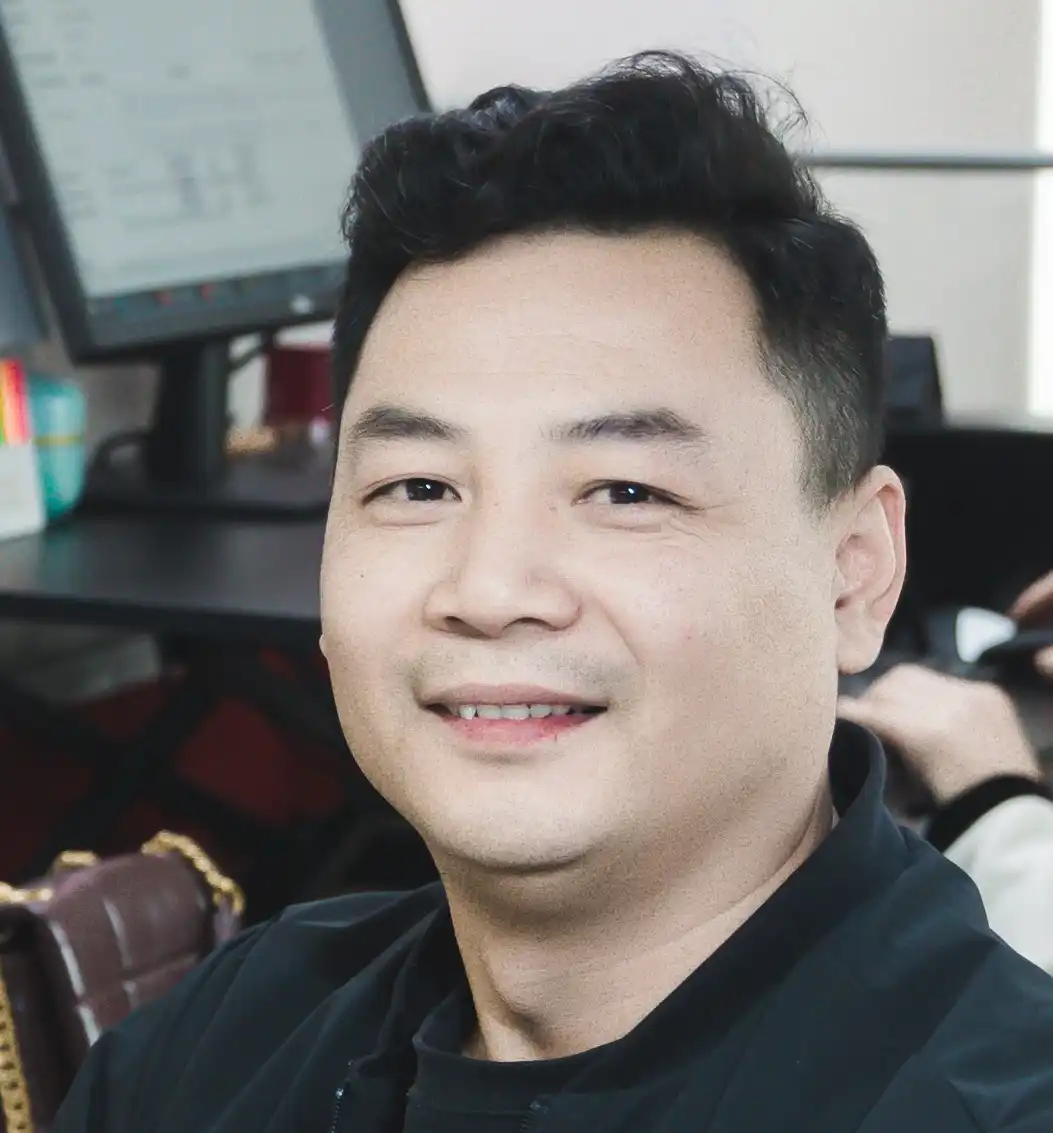
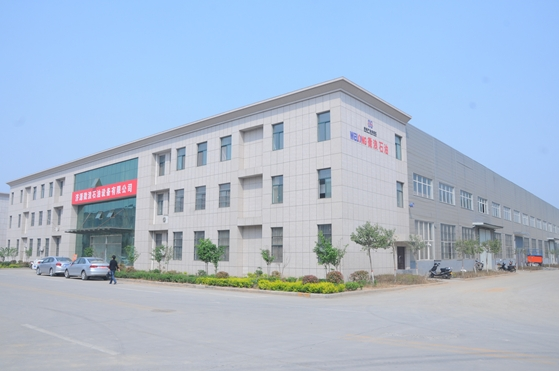
CHINA WELONG - 20+ years manufactuer in oilfield tools