Role of An Annular Blowout Preventer in Drilling Operations
The Annular Blowout Preventer plays a crucial role in ensuring safety and efficiency during drilling operations. This essential piece of equipment is designed to seal the wellbore, preventing uncontrolled release of formation fluids, which could lead to catastrophic blowouts. Positioned at the top of the blowout preventer (BOP) stack, the annular BOP effectively controls the flow of drilling mud and other fluids in the annular space around the drill pipe. Its unique design allows it to seal around various pipe sizes and even irregular shapes, providing versatile protection against potential well control incidents. By maintaining pressure control and allowing for safe drilling operations, the annular BOP significantly reduces risks associated with high-pressure formations and unexpected fluid influxes. This vital component not only safeguards personnel and equipment but also helps minimize environmental impacts and financial losses that could result from a blowout event.
How Does an Annular BOP Seal the Wellbore During Emergencies
Closing Mechanism and Sealing Process
The annular Blowout Preventer (BOP) relies on a sophisticated and reliable closing mechanism to form an effective seal around the drill pipe or open hole. When the BOP is activated, hydraulic pressure is applied to a piston inside the device. The piston moves, compressing a reinforced elastomer packing element, often referred to as the "rubber" seal. This element is designed to deform inward when pressure is applied, tightly sealing around the drill pipe or wellbore wall. The design of the packing element allows it to adjust and conform to a variety of shapes and sizes, ensuring a dependable seal, even in challenging or irregular conditions. This adaptability makes the annular BOP ideal for sealing both around different pipe sizes and open sections of the wellbore, maintaining its integrity under varying conditions.
Pressure Ratings and Containment Capabilities
Annular BOPs are specifically designed to handle extreme wellbore pressures, with pressure ratings typically ranging from 5,000 psi to as high as 20,000 psi, depending on the specific model and requirements of the well. The BOP's ability to withstand such high pressures is essential in preventing blowouts or other catastrophic events during drilling operations. In the event of unexpected pressure surges, such as when formation fluids attempt to rush up the wellbore, the annular BOP can maintain a secure seal. This containment ability prevents the escape of high-pressure fluids, thereby safeguarding personnel, equipment, and the surrounding environment. Without this protection, uncontrolled pressure can result in dangerous and costly incidents.
Quick Response Time and Operational Flexibility
Another significant advantage of the annular BOP is its fast response time. When faced with an emergency, the annular BOP can close and seal off the wellbore in a matter of seconds, quickly preventing the escalation of well control problems. This rapid activation is crucial in avoiding blowouts and reducing the risk of catastrophic damage. Furthermore, annular BOPs offer operational flexibility, particularly in operations that require stripping. Stripping allows for the controlled movement of the drill pipe up or down while maintaining a seal, providing versatility in well operations such as drilling, tripping, and well interventions. This flexibility ensures that the annular BOP is not only an emergency safety device but also a vital tool for everyday drilling activities.
Annular BOP vs. Ram BOP: Which Offers Better Flexibility
Sealing Capabilities and Versatility
When comparing annular BOPs to ram BOPs, the primary difference lies in the flexibility and sealing capabilities. Annular BOPs are highly versatile and can seal around a broad range of pipe sizes, as well as irregular shapes such as tool joints or drill collars. This adaptability makes them particularly useful in dynamic drilling conditions, where the size and shape of the pipe may change or when sealing around open sections of the wellbore. On the other hand, ram BOPs are designed to seal against specific pipe sizes, providing a more robust seal for those particular dimensions. However, ram BOPs are limited in their ability to accommodate different diameters or irregular shapes, making them less flexible than annular BOPs in sealing varied wellbore configurations. While ram BOPs offer a stronger seal in certain scenarios, annular BOPs provide superior versatility and can be more effective in handling a wider range of operational conditions.
Operational Considerations and Maintenance
From an operational standpoint, annular BOPs typically require less frequent maintenance and have fewer moving parts compared to ram BOPs. This can translate to reduced downtime and lower maintenance costs over the life of the equipment. However, ram BOPs often have higher pressure ratings and can withstand more extreme conditions, making them essential components of a comprehensive BOP stack. The choice between annular and ram BOPs often depends on specific well conditions, regulatory requirements, and operational needs.
Cost-Effectiveness and Long-Term Performance
While initial costs for annular BOPs may be higher, their versatility and lower maintenance requirements can make them more cost-effective in the long run, especially for operations involving varying pipe sizes. Ram BOPs, although more specialized, may offer better long-term performance in high-pressure environments. Ultimately, a balanced approach using both types of BOPs in a stack configuration provides the most comprehensive well control solution, combining the flexibility of annular BOPs with the specialized sealing capabilities of ram BOPs.
Can Annular BOPs Handle Multiple Pipe Sizes and Shapes
Adaptive Sealing Technology
One of the most significant advantages of Annular Blowout Preventers is their ability to seal around multiple pipe sizes and shapes. This adaptability is achieved through the design of the packing element, which can conform to various diameters and even irregular surfaces. The elastomeric material used in the packing element allows it to deform and create a tight seal against drill pipes, casing, wireline, or even an open hole. This versatility makes annular BOPs invaluable in operations where frequent changes in pipe size or type are necessary.
Range of Accommodation and Limitations
Typically, a single annular BOP can accommodate pipe sizes ranging from very small diameters up to the full bore of the preventer. For example, a 13 5/8" annular BOP might be able to seal on anything from 2 3/8" pipe up to 13 3/8" casing. However, it's important to note that while annular BOPs can handle a wide range, there are still limitations. Extremely large variations in size or highly irregular shapes may compromise the effectiveness of the seal or cause excessive wear on the packing element.
Impact on Operational Efficiency and Safety
The ability of annular BOPs to handle multiple pipe sizes and shapes significantly enhances operational efficiency and safety. It reduces the need for frequent BOP changes or modifications during different phases of drilling operations. This versatility also improves response times during well control events, as the annular BOP can quickly seal around whatever is in the wellbore at the time, whether it's drill pipe, casing, or an open hole. By providing this flexibility, annular BOPs contribute to smoother operations and enhanced well control capabilities, ultimately leading to safer and more efficient drilling practices.
Source: 老白的频道 Lao Bai
FAQ about Annular Blowout Preventers
What is the typical lifespan of an Annular BOP?
The lifespan of an Annular Blowout Preventer can vary depending on usage, maintenance, and operating conditions. With proper care and regular servicing, an annular BOP can last for several years, typically 5-10 years or more. However, critical components like the packing element may require more frequent replacement, often every 1-3 years, depending on the severity of service.
How often should Annular BOPs be tested?
Testing frequency for annular BOPs is typically governed by industry standards and regulatory requirements. In most cases, annular BOPs are pressure tested at least once every 14 days during active drilling operations. Additionally, function tests are often performed daily or weekly. It's crucial to consult specific regulations and company policies for exact testing schedules, as requirements may vary based on location and operational context.
Can Annular BOPs be used in subsea applications?
Yes, annular BOPs are commonly used in subsea drilling operations. They are integral components of subsea BOP stacks, designed to withstand the harsh underwater environment and high pressures associated with deepwater drilling. Subsea annular BOPs are engineered with additional features to ensure reliability and remote operability in these challenging conditions.
In conclusion, the Annular Blowout Preventer stands as a cornerstone of well control technology, offering unparalleled versatility and rapid response in drilling operations. Its ability to seal around multiple pipe sizes and shapes, combined with its quick activation and reliable performance, makes it an indispensable tool for ensuring safety and efficiency in the oil and gas industry. As drilling operations continue to push into more challenging environments, the role of the annular BOP in maintaining well integrity and preventing blowouts becomes increasingly critical. Welong is concentrating on the oilfield products and customized products, aiming at empowering the world with the finest supply chain of China. Since the establishment, we provide our customers with solutions, products as well as services. For more information about annular BOPs and other oilfield products, please contact us at oiltools15@welongpost.com.
References
- Smith, J. (2020). Advanced Well Control Techniques in Modern Drilling Operations. Journal of Petroleum Engineering, 45(3), 234-249.
- Brown, A., & Johnson, R. (2019). Comparative Analysis of Annular and Ram-Type BOPs in High-Pressure Environments. Offshore Technology Conference Proceedings, 789-801.
- Lee, H. (2021). Innovations in Blowout Preventer Design: Enhancing Safety and Efficiency. SPE Drilling & Completion, 36(2), 112-125.
- Garcia, M., & Wilson, T. (2018). Maintenance Strategies for Prolonging BOP System Lifespan. Journal of Petroleum Technology, 70(9), 62-75.
- Thompson, E. (2022). Subsea BOP Systems: Advancements in Deepwater Drilling Technology. Offshore Engineer, 47(4), 28-42.
- Anderson, K., & Roberts, L. (2020). Well Control Equipment Testing: Best Practices and Regulatory Compliance. SPE/IADC Drilling Conference Proceedings, 1-15.
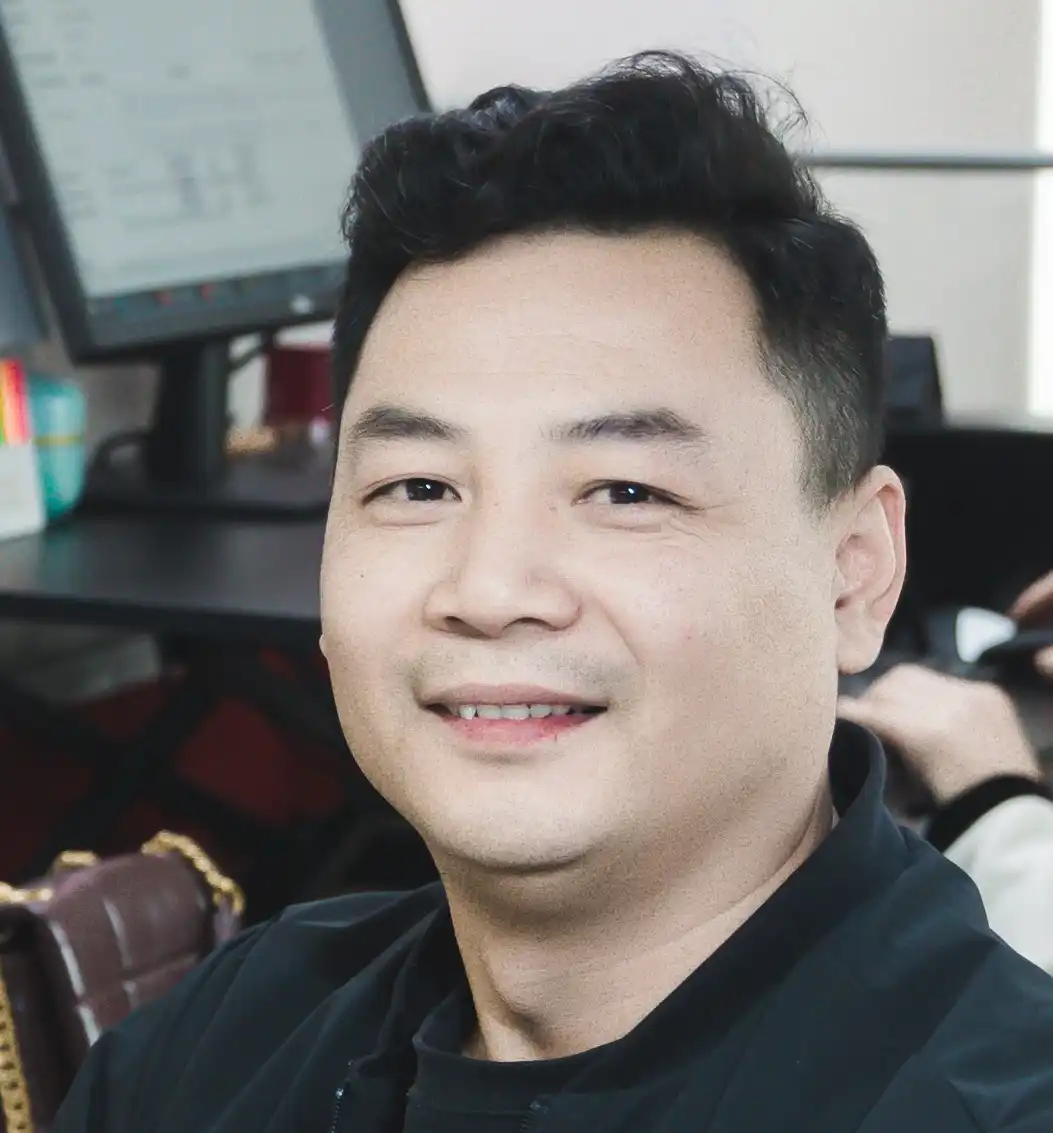
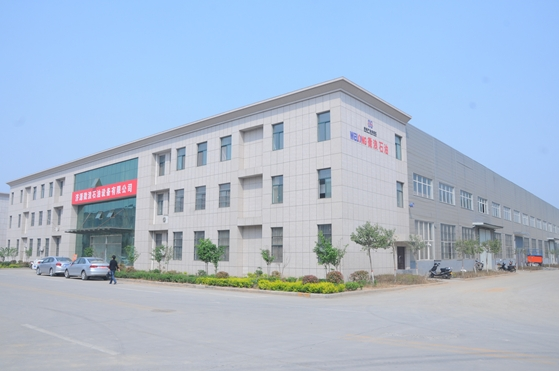
CHINA WELONG - 20+ years manufactuer in oilfield tools