What is a Blowout Preventer in Oil Drilling?
A Blowout Preventer (BOP) is a critical safety device used in oil and gas drilling operations to prevent uncontrolled release of formation fluids, such as oil or natural gas, from the wellbore. This essential piece of equipment is installed at the wellhead and acts as a large specialized valve or set of valves designed to seal, control, and monitor oil and gas wells. The BOP system includes various components, with one of the most crucial being the Annular Blowout Preventer. This specific type of BOP uses a donut-shaped rubber seal to close around the drill pipe, preventing the escape of fluids and gases. BOPs are vital for maintaining well control, protecting workers, equipment, and the environment from potentially catastrophic blowouts. They serve as the last line of defense against unexpected pressure surges and are essential for safe drilling operations in both onshore and offshore environments.
Why is a blowout preventer important
Safety Assurance in Drilling Operations
Blowout preventers play a paramount role in ensuring the safety of drilling operations. They act as a crucial barrier against unexpected pressure surges, preventing potentially catastrophic events that could result in loss of life, environmental damage, and significant financial losses. By effectively sealing off the wellbore, BOPs contain high-pressure fluids and gases, mitigating the risk of explosions and fires on the drilling rig.
Environmental Protection
The importance of blowout preventers extends beyond immediate safety concerns to encompass environmental protection. In the event of a well control incident, Annular Blowout Preventers prevent the uncontrolled release of hydrocarbons into the surrounding environment. This function is particularly critical in offshore drilling operations, where oil spills can have devastating consequences on marine ecosystems and coastal communities. By maintaining well integrity, BOPs contribute significantly to the oil and gas industry's efforts to minimize its environmental footprint.
Economic Considerations
From an economic perspective, blowout preventers are indispensable for the viability and sustainability of drilling operations. The financial implications of a blowout can be staggering, including costs associated with lost production, equipment damage, environmental cleanup, and potential legal liabilities. By preventing such incidents, BOPs help safeguard the substantial investments made in drilling projects and ensure the continuity of operations. Moreover, the presence of reliable BOP systems is often a regulatory requirement and a prerequisite for obtaining drilling permits, underscoring their economic significance in the industry.
What are the main types of BOPs
Annular Blowout Preventers
The Annular Blowout Preventer (Annular BOP) is one of the most versatile and widely utilized types of blowout preventers in drilling operations. Its design features a donut-shaped rubber sealing element that can adapt to different wellbore conditions, sealing around various sizes of drill pipes or even an open hole. This flexibility allows the Annular BOP to be used in a wide range of applications, especially in situations where the size of the drill pipe may change frequently. When activated, the rubber element is compressed inward, creating a tight and secure seal that prevents any flow of fluids from the wellbore. The adaptability of the Annular BOP makes it especially effective in operations such as stripping, where the wellbore conditions can change quickly. Furthermore, the Annular BOP is capable of withstanding high pressures, making it an essential component of most blowout preventer stacks. Its ability to form a reliable seal in various conditions, including when there is no pipe present, adds to its importance in ensuring safety during drilling operations.
Ram-type Blowout Preventers
Ram-type Blowout Preventers (Ram BOPs) offer a different approach to sealing the wellbore. Unlike Annular BOPs, Ram BOPs use hydraulically operated steel rams that physically close to seal the wellbore. There are different subtypes of Ram BOPs, each designed for specific tasks. Pipe Rams, for example, are designed to seal around a specific size of drill pipe, creating a tight barrier to prevent any fluid flow. Blind Rams are used when no pipe is present, completely sealing the wellbore and preventing blowouts in such situations. Shear Rams serve a critical role in emergencies, as they are capable of cutting through drill pipe and sealing the wellbore in extreme cases. Lastly, Variable Bore Rams are designed with the ability to seal around different pipe sizes within a given range, offering more versatility than the standard pipe rams. The combination of these different ram types allows for efficient and effective well control, particularly in situations where a quick response is required to prevent blowouts.
Rotating Blowout Preventers
Rotating Blowout Preventers (RCDs) are specialized devices used in managed pressure drilling and underbalanced drilling scenarios. They are designed to maintain a seal around the wellbore while allowing the drill string to rotate. This is an essential feature in operations where the drill pipe must continue to turn for drilling purposes but pressure control must also be maintained. Rotating BOPs use a specially engineered sealing element that is capable of withstanding the high heat and friction generated by the rotating drill pipe. Despite these harsh conditions, the rotating BOP maintains its sealing function, preventing fluid flow and ensuring safe wellbore pressure. The rotating function allows for continuous drilling without compromising safety, making RCDs an important tool in advanced drilling techniques.
How does a BOP system work
Activation Mechanisms
BOP systems are equipped with multiple activation mechanisms to ensure reliable operation in various scenarios. The primary activation method is typically hydraulic, where high-pressure hydraulic fluid is used to operate the BOP's sealing elements. This system allows for quick response times and powerful sealing capabilities. Additionally, most BOP systems include redundant activation methods, such as:
1. Acoustic activation for subsea BOPs, allowing remote operation in deep-water environments.
2. ROV (Remotely Operated Vehicle) intervention panels for manual override in subsea applications.
3. Electrical activation systems as a backup to hydraulic systems.
These multiple activation options ensure that the BOP can be engaged even in the event of primary system failure, enhancing overall safety and reliability.
Control Systems and Monitoring
Modern BOP systems incorporate sophisticated control and monitoring technologies to ensure optimal performance and rapid response to well control events. These systems typically include:
1. Computerized control panels that allow operators to monitor wellbore pressure, BOP status, and fluid levels in real-time.
2. Pressure sensors and flow meters that provide continuous data on well conditions.
3. Automated shut-in protocols that can trigger BOP activation based on predefined pressure thresholds.
4. Data logging and analysis capabilities for post-event investigation and system optimization.
The integration of these advanced control and monitoring systems enhances the overall effectiveness of the BOP, enabling proactive management of well control risks and facilitating quick decision-making in critical situations.
Testing and Maintenance Procedures
Regular testing and maintenance are crucial for ensuring the reliability and effectiveness of BOP systems. Industry standards and regulations require rigorous testing protocols, including:
1. Function tests: Conducted regularly to verify the proper operation of all BOP components.
2. Pressure tests: Performed to ensure the integrity of seals and the system's ability to withstand maximum anticipated wellbore pressures.
3. Stack pull and inspection: Periodic removal and thorough inspection of the entire BOP stack.
4. Preventive maintenance: Scheduled replacement of wear items and critical components.
These comprehensive testing and maintenance procedures help identify potential issues before they escalate into serious problems, ensuring that the BOP system remains in optimal condition throughout drilling operations.
Source: 老白的频道 Lao Bai
FAQ about Annular Blowout Preventers
What is the lifespan of a typical BOP?
The lifespan of a Annular Blowout Preventer can vary significantly depending on factors such as usage frequency, operating conditions, and maintenance practices. Generally, with proper maintenance and regular refurbishment, a BOP can remain in service for 15-20 years. However, critical components such as elastomeric seals and hydraulic systems may require more frequent replacement or overhaul. It's important to note that the operational life of a BOP is not just determined by its age, but also by its performance in regular testing and its compliance with evolving industry standards and regulations.
Can a BOP fail, and what are the consequences?
While rare, BOP failures can occur and the consequences can be severe. Potential causes of failure include:
1. Mechanical failures due to wear or manufacturing defects.
2. Control system malfunctions.
3. Human error in operation or maintenance.
The consequences of a BOP failure can range from minor well control issues to catastrophic blowouts, potentially resulting in loss of life, environmental damage, and significant financial losses. The Deepwater Horizon disaster in 2010 is a stark reminder of the potential consequences of BOP failure. This underscores the critical importance of rigorous maintenance, testing, and operational procedures in BOP management.
How do subsea BOPs differ from surface BOPs?
Subsea BOPs, used in offshore drilling, differ from surface BOPs in several key aspects:
1. Design: Subsea BOPs are typically larger and more complex, designed to withstand high pressures and harsh underwater environments.
2. Activation: They include remote activation systems, such as acoustic controls and ROV intervention capabilities.
3. Redundancy: Subsea BOPs often have more redundant systems due to the challenges of underwater intervention.
4. Maintenance: Maintenance and testing of subsea BOPs are more complex and often require specialized equipment and procedures.
5. Control systems: Subsea BOPs use sophisticated control systems to manage the greater distances and environmental challenges associated with deepwater operations.
In conclusion, Blowout Preventers are critical safety devices in oil and gas drilling operations, serving as the last line of defense against potentially catastrophic well control events. Understanding their types, functions, and importance is crucial for anyone involved in the drilling industry. China Welong is a seasoned global integrated supply chain service provider that was established in 2001. With durable products, we are able to establish a positive reputation through strict quality control. For more information about Annular Blowout Preventers and other oilfield products, please contact us at oiltools15@welongpost.com.
References
- American Petroleum Institute. (2022). "Standard 53: Well Control Equipment Systems for Drilling Wells."
- Transocean Ltd. (2021). "Deepwater Horizon Accident Investigation Report."
- Journal of Petroleum Technology. (2023). "Advances in Blowout Preventer Technology and Testing."
- Offshore Technology Conference. (2022). "Subsea BOP Systems: Challenges and Innovations."
- Society of Petroleum Engineers. (2021). "Well Control for the Rig-Site Drilling Team."
- Bureau of Safety and Environmental Enforcement. (2023). "Blowout Preventer (BOP) Testing Requirements."
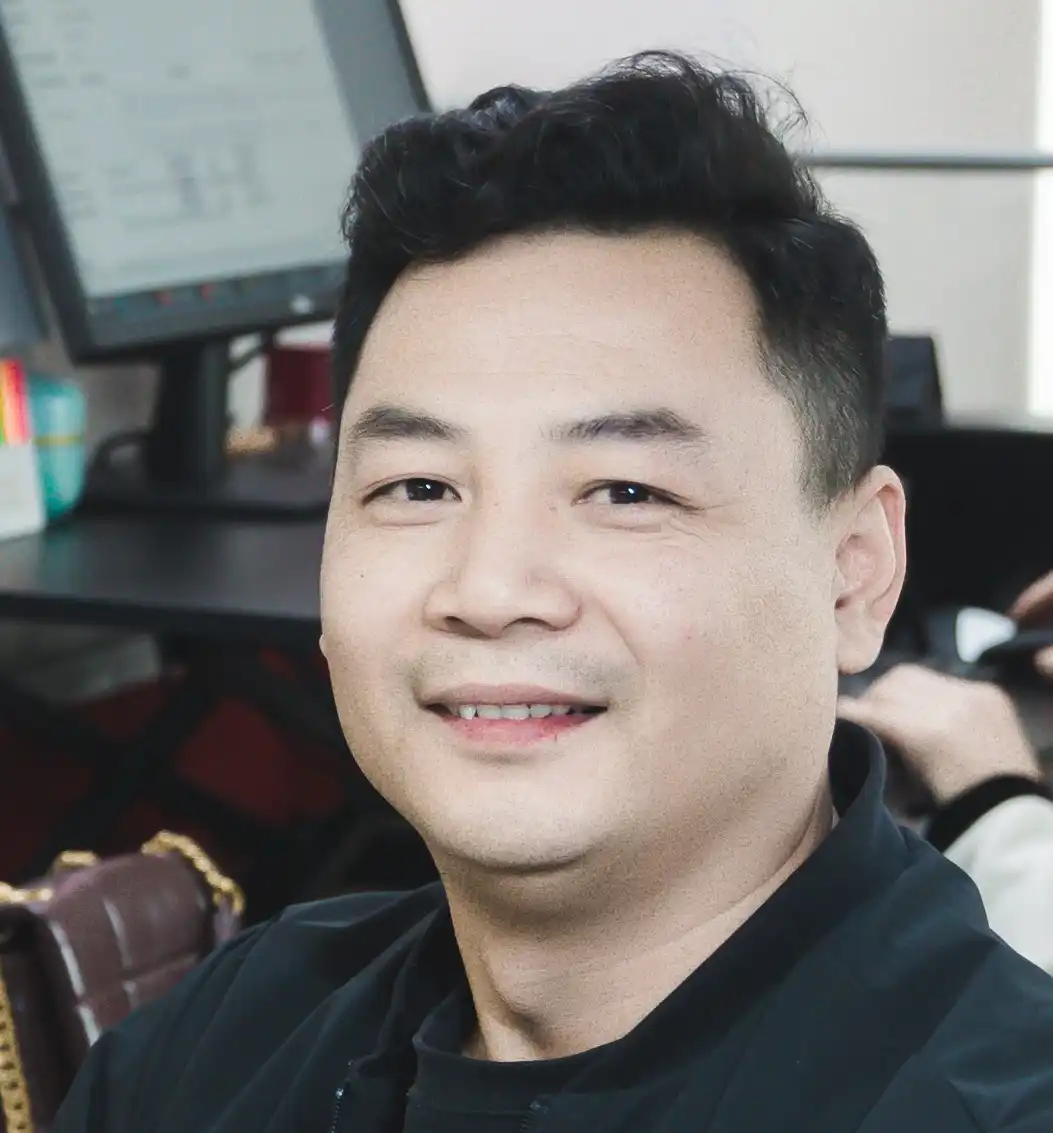
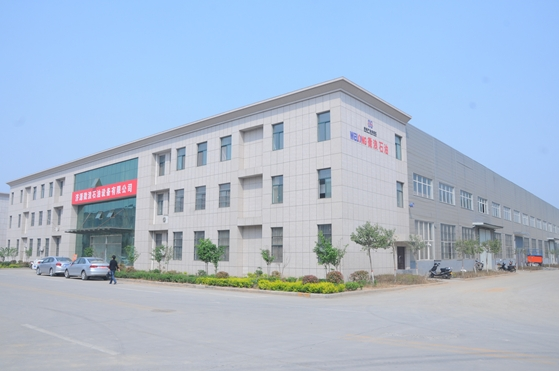
CHINA WELONG - 20+ years manufactuer in oilfield tools